By Alejandro Fernandez, LEED Green Associate, Jordan Komp, P.E., S.E., and John Peronto, P.E., S.E., CEng, FIStructE, FICE, F.ASCE, LEED AP
Precedent-setting design, testing, and construction processes culminated in Ascent, currently the world’s tallest mass timber hybrid structure.
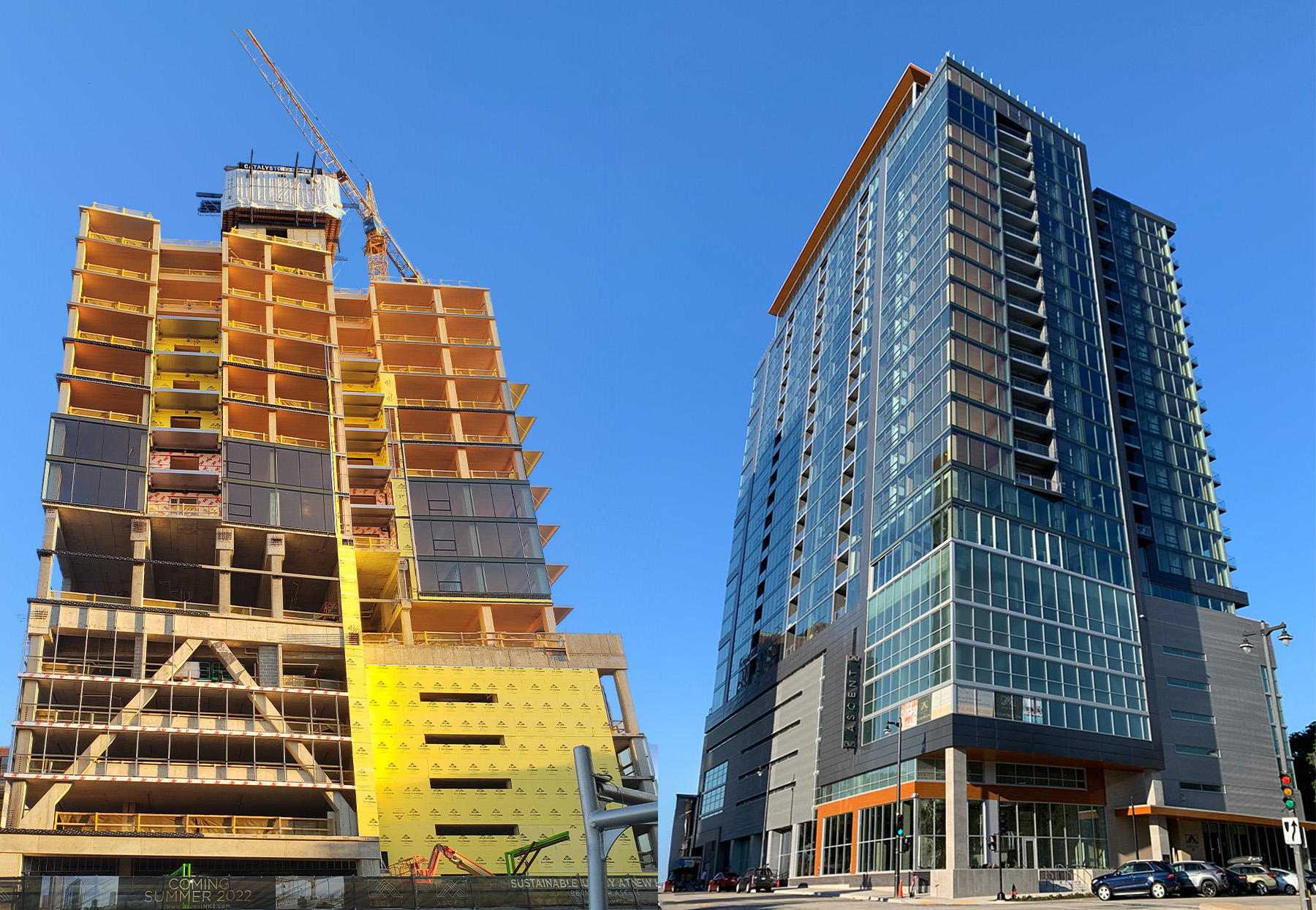
In 1895, the world’s tallest habitable building was in an unlikely place — Milwaukee — a small Midwestern city known then for its rapidly expanding immigrant population. At just over 350 ft tall, Milwaukee City Hall is still a symbol of the city’s German heritage, with four beer stein turrets flanking its clock tower. While it lost its title in 1897 to the Hamburg City Hall in Germany, more than a century later, a building in the city has garnered another world record for its height: Ascent — a 25-story, 284 ft tall mass timber hybrid structure with six levels of parking at its base and 19 residential and amenity levels above.
Ascent, designed by Korb + Associates Architects, is in Milwaukee’s East Town neighborhood, just a few blocks from Lake Michigan and the city’s Historic Third Ward. New Land Enterprises, a real estate development and property management company, had owned the plot of land Ascent sits on for more than 30 years and at one time was considering traditional concrete developments on the site.
While New Land was weighing its options, in 2016 structural engineers at Thornton Tomasetti — in collaboration with designers at Perkins&Will and researchers at the University of Cambridge — were exploring the limits of tall mass timber construction for River Beech Tower, a conceptual design for an 800 ft tall, 80-story building in Chicago. Thanks in part to projects like River Beech Tower, New Land seized the opportunity to build a mass timber product that would offer an unparalleled experience for residents.
Two years later, New Land began assembling a team to bring Ascent to life. Throughout the design process, Thornton Tomasetti focused on three critical areas: permitting, structural efficiency, and procurement.
Permission granted
Typically, building codes in the United States are prescriptive in nature and are developed to identify code-compliant systems and parameters for designers. For Ascent, even at the originally conceptualized 18 stories, it would stand well above the code-prescribed maximum-allowable five stories and 85 ft height for timber structures. It would therefore require a variance — several, in fact.
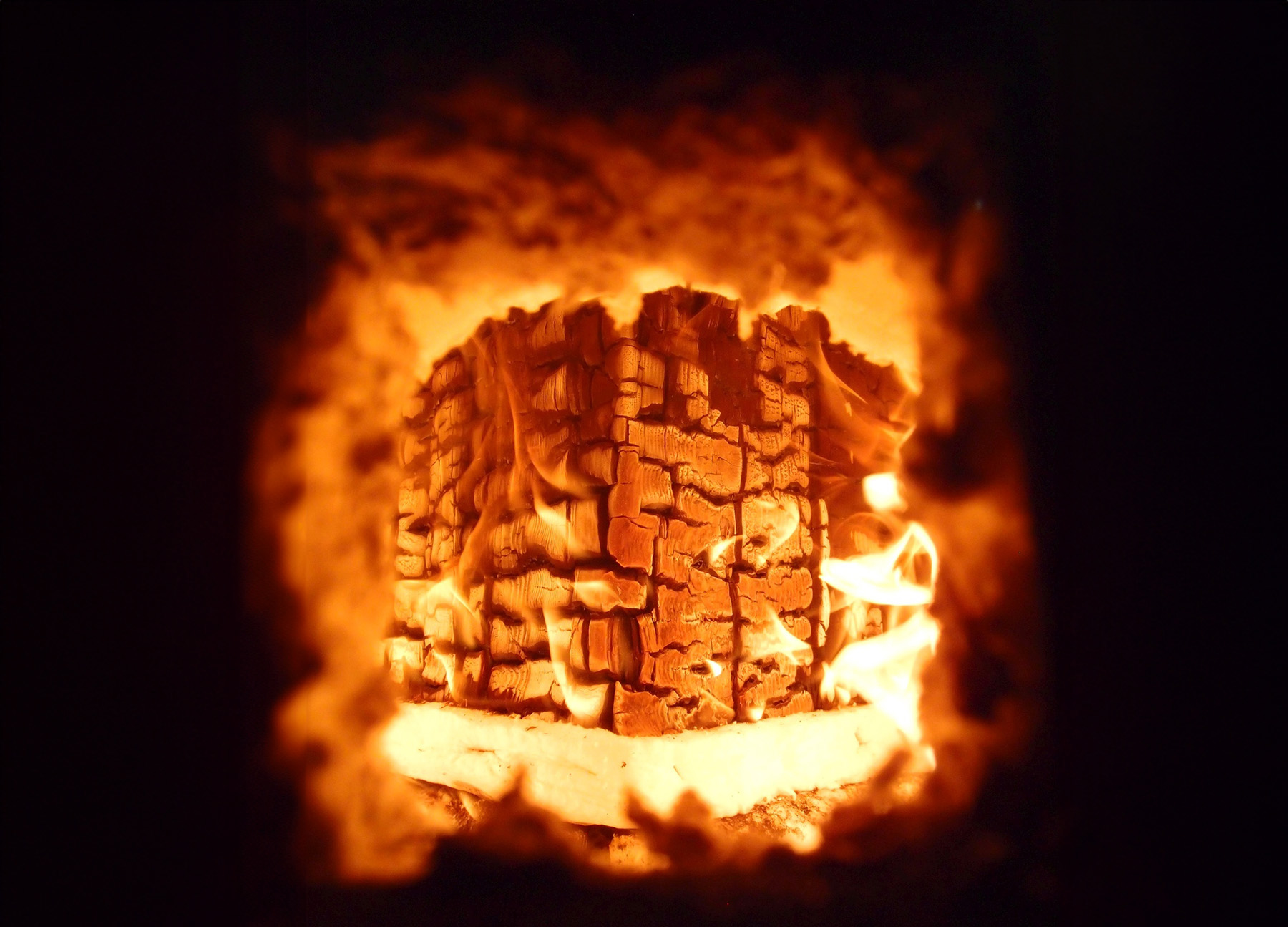
Aware of this critical fact, the Ascent team began discussions with the authority having jurisdiction early in the design process. As a result of the initial meetings, the AHJ was open to the idea of Ascent but did not formally agree to a variance. The city’s fire department was also brought in for preliminary discussions. While not typically part of the approval process, all stakeholders realized the critical role of the fire department for this project.
After months of meetings, research, and design, the stakeholders agreed on a path forward: employing a performance-based design approach based in part on the International Building Code’s Section 104.11: Alternative materials, design and methods of construction and equipment. This provision allows designers to propose unconventional or unusual systems for approval.
While this may be an uncommon path to many designers, it was not the first time the IBC’s alternative materials provision was used in relation to mass timber. In 2017, the Framework project in Portland, Oregon, obtained a building permit for a 12-story mass timber structure. Though the project was never built due to financial constraints, it did create a precedent for the Ascent team.
As part of the final approval, the team was granted multiple variances in relation to the Wisconsin Commercial Building Code. For height and number of stories, the team received a variance to exceed the standard Type IV height (85 ft/five stories), contingent on the building being fully sprinklered and meeting the requirements of Type IA construction, with permitted reductions to type IB.
To obtain this variance, the team had to prove a three-hour fire rating for the typical building columns and a two-hour fire rating for the beams and floor slabs. The team determined that this fire rating would be attained either by drywall encapsulation of the timber elements and connections or a sacrificial char layer around the beams, columns, and timber slabs, in accordance with the National Design Specifications char method.
However, due to existing Type IV code restrictions on height, char method calculations and associated research for timber elements were available only for a two-hour fire rating. To verify the applicability of current char calculations for the three-hour rating required for the columns, the Ascent team partnered with the U.S. Department of Agriculture Forest Products Laboratory in Madison, Wisconsin, and tested European and American wood column samples. The results* have been made public and are now an important resource for teams pursuing tall mass timber construction.
The permit approval process also included achieving a two-hour fire rating for all beam-column connections. At the time of design/construction, there were no commercially available wood connectors with a tested two-hour fire rating. Fortunately, the earlier referenced Framework project had received USDA grants to load and fire-test a mass timber beam-column connection capable of achieving a two-hour fire rating. The design team used this assembly throughout the Ascent project at exposed conditions to achieve the required two-hour fire rating.
2015 IBC did not allow concealed spaces for Type IV structures. However, from a design perspective, it was desirable to conceal several mechanical, electrical, and plumbing components inside drop ceilings. (It should be noted that the 2021 IBC includes provisions for concealed spaces for mass timber structures.)
Additionally, the design team was committed to using a number of code-compliant, fire-suppression elements (many of these are also now required by 2021 IBC for type IV-A, IV-B, and IV-C construction). While typically not required by the state at the time, it was agreed that Thornton Tomasetti would act as a licensed mass timber special inspector for the superstructure as well as the engineer of record. These dual services added additional checks and balances, ensuring that the design intent was accomplished in the field.
The final design of the structure’s lateral system, comprising the reinforced-concrete stair and elevator cores, incorporated core walls that could be fully erected prior to construction. These walls were equipped with operational standpipes, prepared during construction, which alleviated fire department concerns related to fighting any fires during construction. The nonstructural fire protection system items included a fully sprinklered building, dual water supply to the fire pump, smoke detection, fire department access on two roads, electronically supervised valves, fire command center, fire department communications support, and stair pressurization.
Structural design and philosophy
The building needed to have a highly efficient structural design to make the project a reality and economically viable for the developer. To this end, the team optimized every element of the structure.
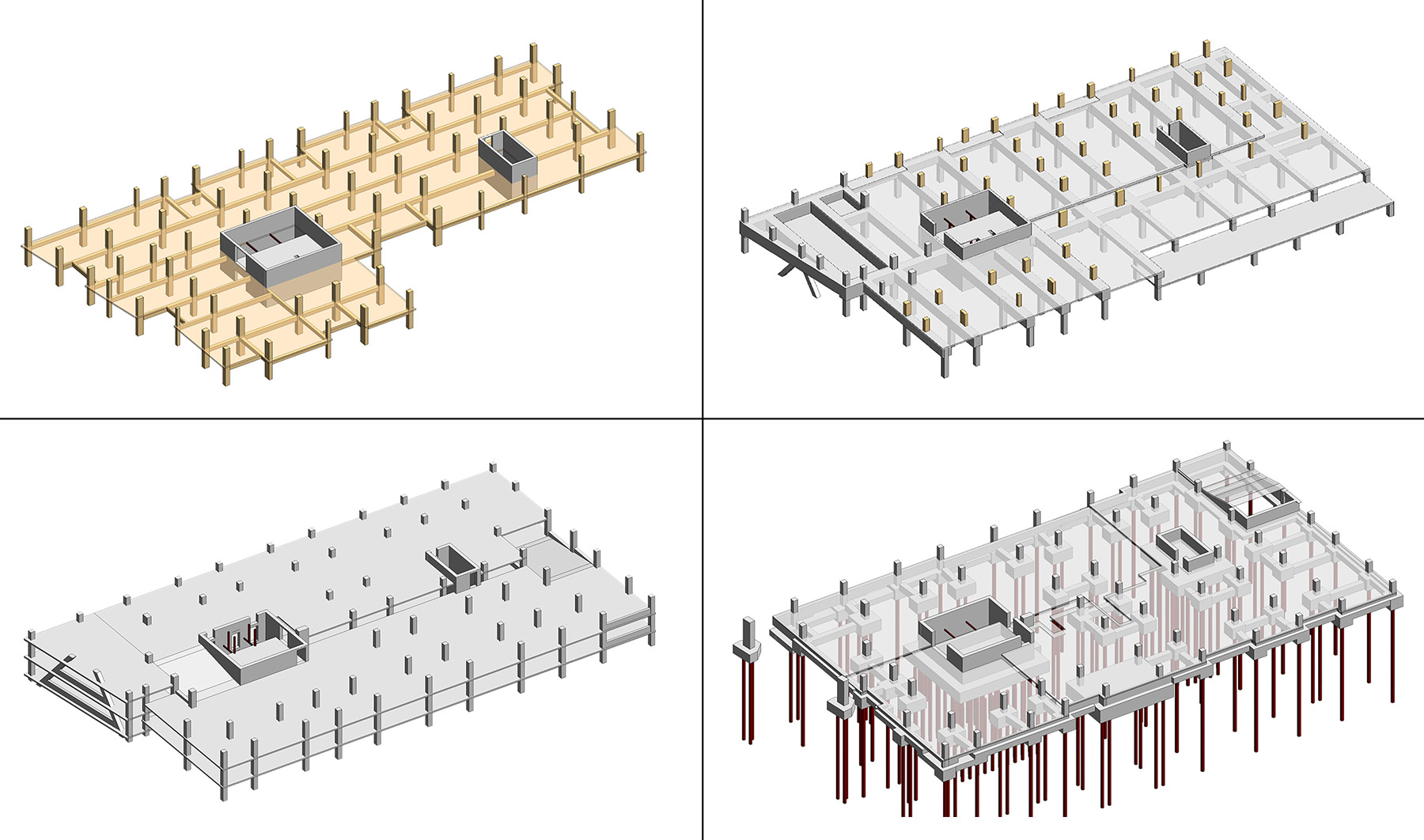
Taking advantage of the relative light weight of the mass timber superstructure — mass timber having a density of 35 pcf compared with standard concrete construction of 150 pcf — the team conducted static and dynamic load testing to achieve the highest-capacity piles in the state. At 450 tons, load testing improved the typical geotechnical capacity of the 16 in. diameter concrete-filled steel pipe piles by nearly a factor of two, significantly reducing the number of piles required and minimizing the construction time required to install the piles.
To maintain efficient flat plate, posttensioned slabs (typically measuring 7.5 in. thick) in the parking structure, the team opted for additional columns throughout it, which eliminated the need for long-span beams and formwork and minimized the number of spans and demands in the transfer elements above.
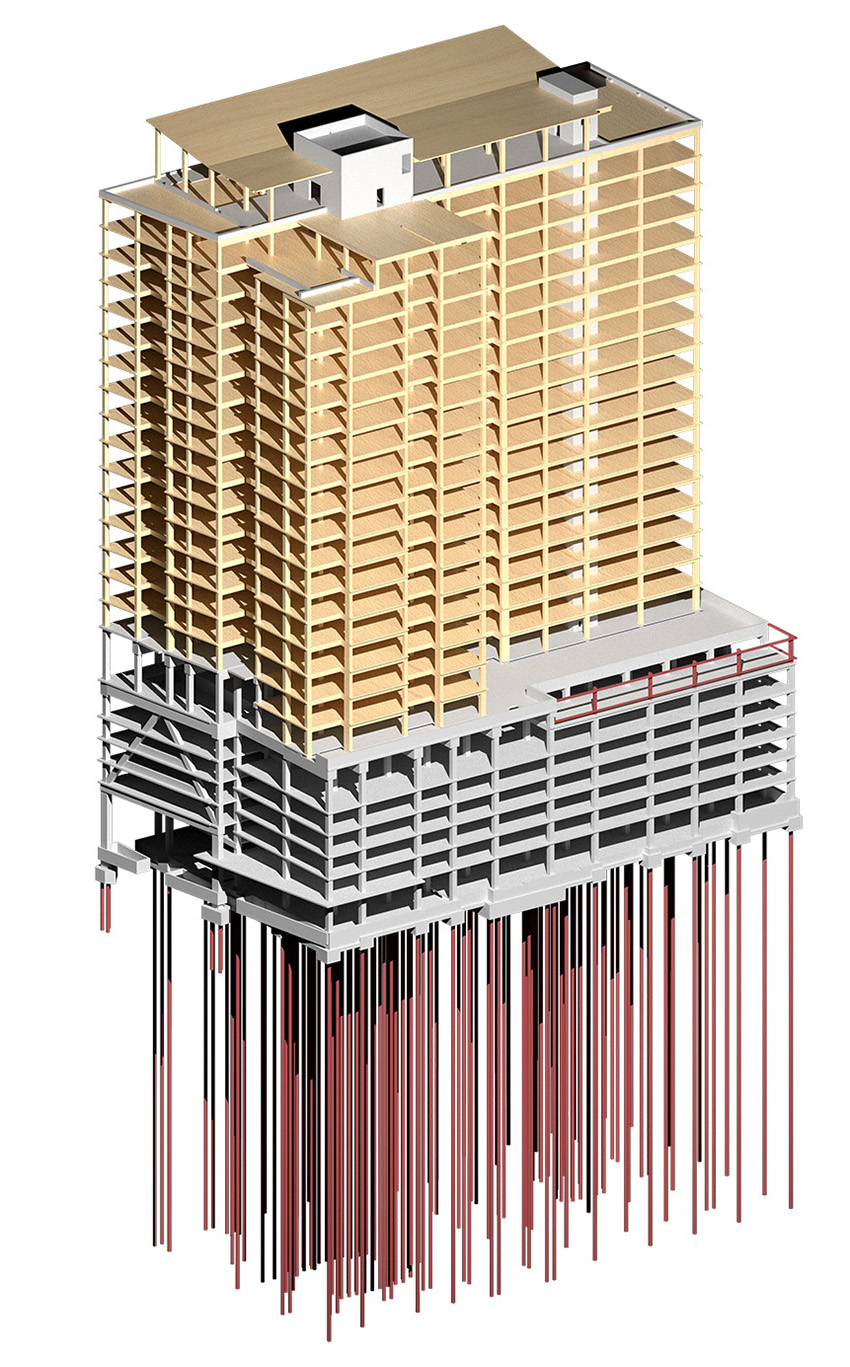
The design team incorporated a “transfer level” at the top of the podium, merging the typical mass timber residential column grid above with the parking grid and drive aisle requirements below. The team sized 4-5 ft deep posttensioned transfer beams to work within the allotted ceiling height required by the swimming pool and mechanical equipment.
While the transfer elements benefited from the light weight of the mass timber superstructure above, thus minimizing overall depth, this reduced weight also required stressing the beams in stages to prevent the tops of the beams from cracking. Half the posttensioning force was incorporated after the initial concrete pour, with the remaining stressing occurring after 50% of the building’s mass timber was constructed.
To optimize the floor framing, the team explored multiple floor-panel systems, including nail-laminated, dowel-laminated, and cross-laminated timber, eventually selecting the latter system. The mass timber superstructure comprises 8 ft wide, 7 in. thick, five-ply cross-laminated timber panels and incorporated a 2.5 in. noncomposite gypcrete topping slab.
The CLT panels are supported on glulam beams spaced 16-20 ft apart, spanning 20-25 ft between glulam columns. The team studied the grid and framing layout at length, including the impact of rotating the framing 90 degrees to minimize the amount of wood fiber required in the glulam beams. Glulam columns, ranging in width from 16 in. to 42 in., were typically transferred at level 7 to support the parking aisles below.
Exposed glulam members incorporate a sacrificial char layer, which provides a three-hour fire rating for columns and two hours for beams. This sacrificial layer increased the overall wood fiber required, and therefore at locations where members were intended to be concealed, such as in bathrooms and corridors, the member fire rating was achieved by encapsulating the members in the drywall. This minimized the size and cost of the structural elements.
In exposed conditions, the glulam beam-column connections used the previously tested Framework connectors. However, at concealed locations, the team designed a bearing-type connection to minimize the cost. In lieu of standard mass timber column-column connections, which typically use steel members, the team developed a series of connectors incorporating epoxied dowels, screws, and steel bearing plates to provide material savings while allowing for field flexibility.
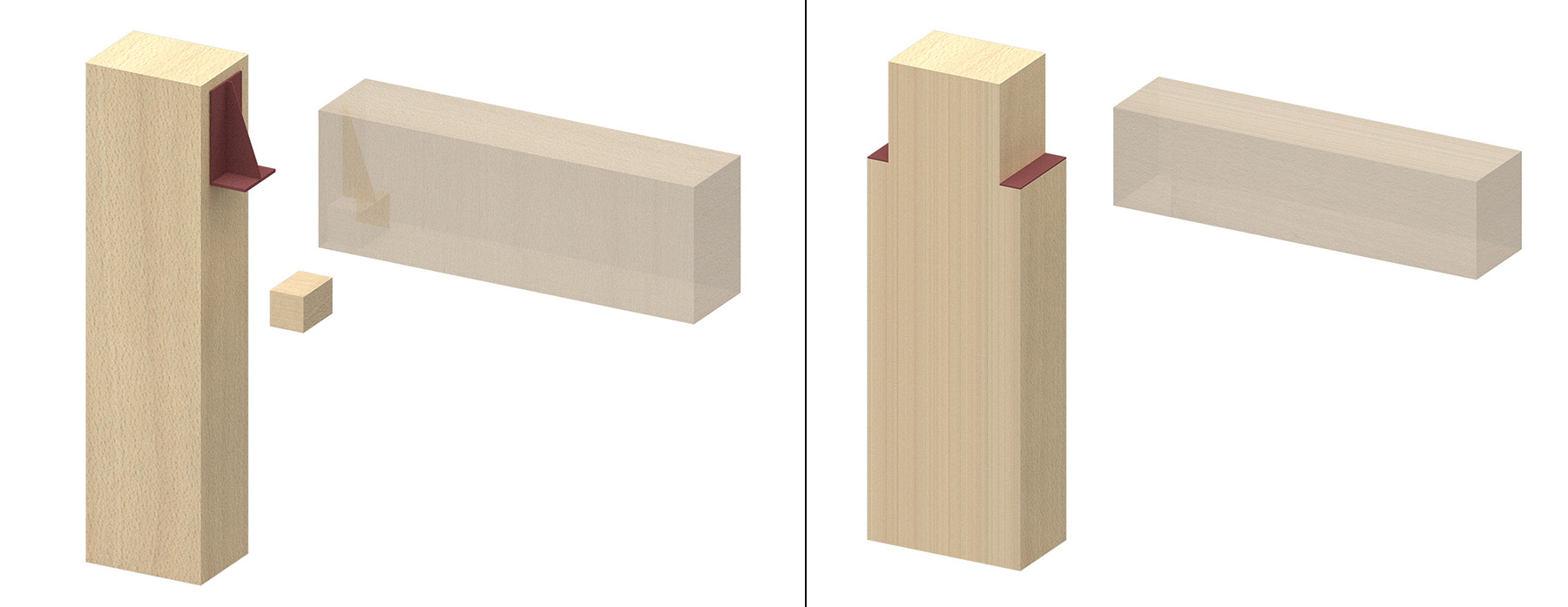
As part of the variance process, the team determined that the lateral system would incorporate reinforced-concrete core walls centered on the structure’s vertical transportation elements. Wind loading controlled the lateral system design due to the proximity to Lake Michigan and Wisconsin’s relatively low seismicity. The CLT panels, wood splines, and steel strapping served as diaphragms to transfer lateral loading to the core walls at each level.
Procurement and construction
With the permit path secured and the structural concept in place, the Ascent design team turned to procurement, and Timberlab was brought on to assist with this aspect of construction. Original concepts for the tower explored locally sourcing the material and taking advantage of Wisconsin’s vast forestry resources; however, the team quickly realized that the volume of wood required would make this approach impractical from the procurement and fabrication points of view.
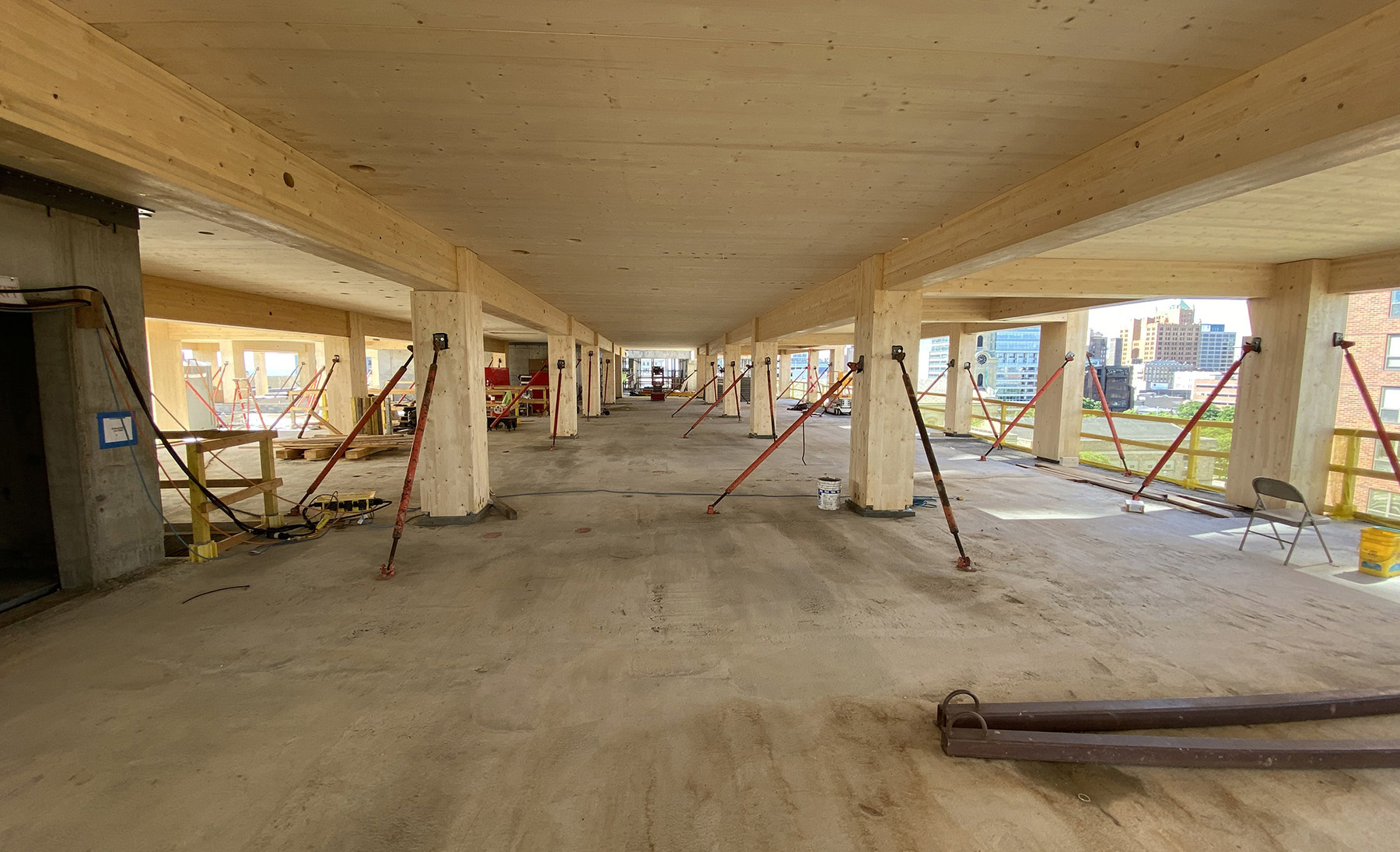
Sourcing the wood from other domestic suppliers was not feasible either because of the limited number of suppliers and economic pressures at the time. As a result, the design team’s focus shifted toward European suppliers. Europe’s rich history of designing and building with wood and its proven production capacity were strategic advantages, which meant the project could be competitively bid in North America despite additional transportation costs. In the end, the team chose Austrian spruce.
From a design perspective, using European-sourced timber required the team to study several factors. While the CLT panels typically meet U.S. standards (ANSI/APA PRG 320 2018: Standard for Performance-Rated Cross-Laminated Timber), the European glulam elements have, generally speaking, reduced bearing capacities compared with their North American counterparts and require unique consideration when determining the material grading process, as standards and testing procedures between Europe and the U.S. are not identical. Therefore, the capacities for Ascent could not be directly translated, which required the design team to evaluate multiple U.S., European, and hybrid designs based on existing test data and research.
To facilitate procurement and prefabrication, there were more than 80 calls between the architect, MEP trades, general contractor, and structural engineer to locate all the mechanical systems and required penetrations through the timber structural elements. The procurement and structural teams held weekly calls to finalize detailing requirements during material procurement. These additional coordination efforts resulted in a highly detailed fabrication model that included every piece, connection, and penetration.
Once fabricated in Austria, the mass timber elements were delivered via truck to ports in northern Germany, loaded into containers, and barged to the U.S. East Coast. The timber elements were transported in containers via train to Chicago and then trucked to the Port of Milwaukee for storage. Timberlab’s work during this procurement operation was crucial due to additional market challenges caused by COVID-19 and the Suez Canal blockage in March 2021, which entangled the entire shipping container freight market. With embodied carbon being of special concern for our industry, it should be noted that boat transport offers relatively low EC emissions compared with trucking.
While the mass timber components were detailed, C.D. Smith, the general contractor, began tower construction at the end of summer 2020. By the end of April of 2021, the concrete podium was nearing completion, and the first timber pieces began arriving on-site. These pieces would end up being erected by C.D. Smith’s composite team, consisting of just five ironworkers, five carpenters, and two laborers.
Prior to construction, C.D. Smith and Timberlab created a mass timber mock-up to ensure the workers could understand and plan for the construction tolerances and sequencing required on-site. While the crew had limited mass timber construction experience, within a short while, it was erecting a floor per week — two to three days for columns, one to two days for beams, and one day for CLT panels.
As mentioned earlier, as part of the agreement with the city, Thornton Tomasetti performed special inspections for the project. These were instrumental not only in ensuring that the structure was fabricated and erected in accordance with the design intent but also crucial to expediting responses to unforeseen construction conditions common on projects of this magnitude. It was also particularly critical due to Ascent being cutting-edge construction, especially within the U.S.
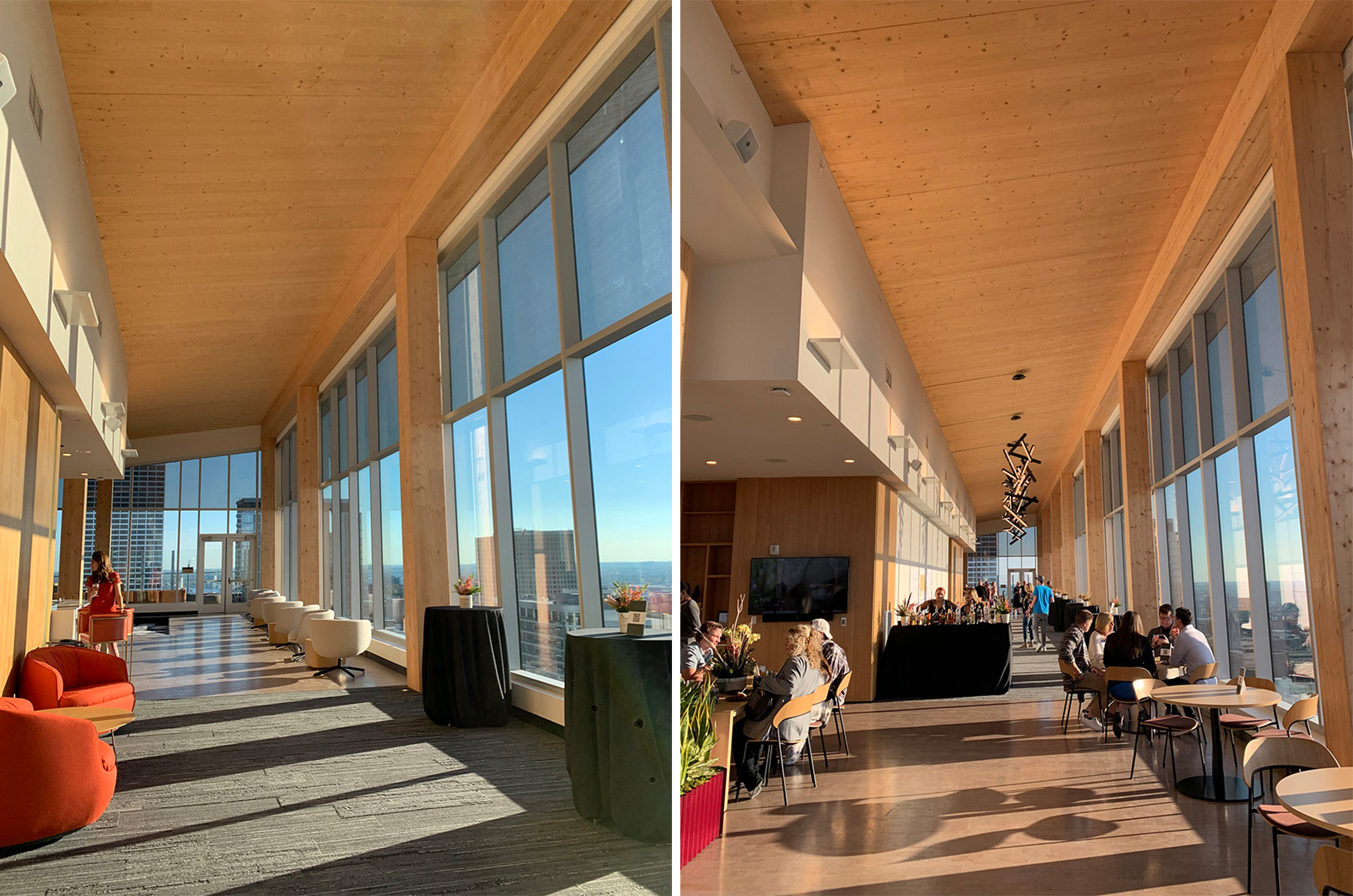
Thornton Tomasetti also worked closely with the construction team to monitor the vertical movement of the structure during construction. A robust monitoring and compensation program was put in place to survey the elevation of every column and core wall intersection at each floor. Research is currently limited on vertical shortening and the associated compensation of mass timber structures, requiring engineering judgment with respect to elastic shortening, creep, shrinkage, joint settlement, and construction tolerances and their impacts on structures over time.
Based on initial analysis and research, it was anticipated that Ascent would require vertical compensation comparable to that of a 60-story concrete structure. As a result, the design team created an anticipated compensation schedule based on the real-time construction schedule, which allowed the contractor to add or remove shims as required to achieve the target design elevations at each floor and column. These predicted elevations were then reviewed and verified throughout the construction of the superstructure. In many conditions, the target elevations were slightly higher than the theoretical floor elevations to account for the eventual shrinkage of the structure.
Through completion of the structure and building occupancy, it was estimated that using mass timber reduced the overall construction schedule by nearly five months. The design team understood early on that mass timber would be more expensive than a traditional concrete building, therefore those five months of advance income were crucial to the financial success of the project.
While the 2021 IBC has opened a path for taller mass timber buildings, albeit with additional limitations on exposure of the mass timber elements, Ascent sets a precedent for the future of tall mass timber construction in the U.S. New Land’s foresight and the design team’s innovative detailing, material testing, and collaboration with city officials showed that through a project-specific, performance-based design approach, mass timber can be used to develop a commercially viable high-rise building.
As with Milwaukee City Hall, it is unlikely that Ascent will keep its position as the tallest in the world for very long — especially because new mass timber buildings of greater heights have already been announced. Nevertheless, Ascent will endure as a testament to what is possible with forward thinking, dedication, and a willingness to collaborate.
Alejandro Fernandez, LEED Green Associate, is a senior associate, Jordan Komp, P.E., S.E., is an associate principal, and John Peronto, P.E., S.E., CEng, FIStructE, FICE, F.ASCE, LEED AP, is a senior principal at Thornton Tomasetti.
*To find out more about the testing of the wood column samples, read “Determination of Char Rates for Glulam Columns Exposed to a Standard Fire for Three Hours.”
Owner
New Land Enterprises, Milwaukee
Architect
Korb + Associates Architects, Milwaukee
Structural engineer/mass timber inspector
Thornton Tomasetti, Milwaukee
General contractor
C.D. Smith, Milwaukee
Timber procurement
Timberlab, Portland, Oregon
This article first appeared in the January/February 2024 print issue of Civil Engineering as “Timber Rises.”