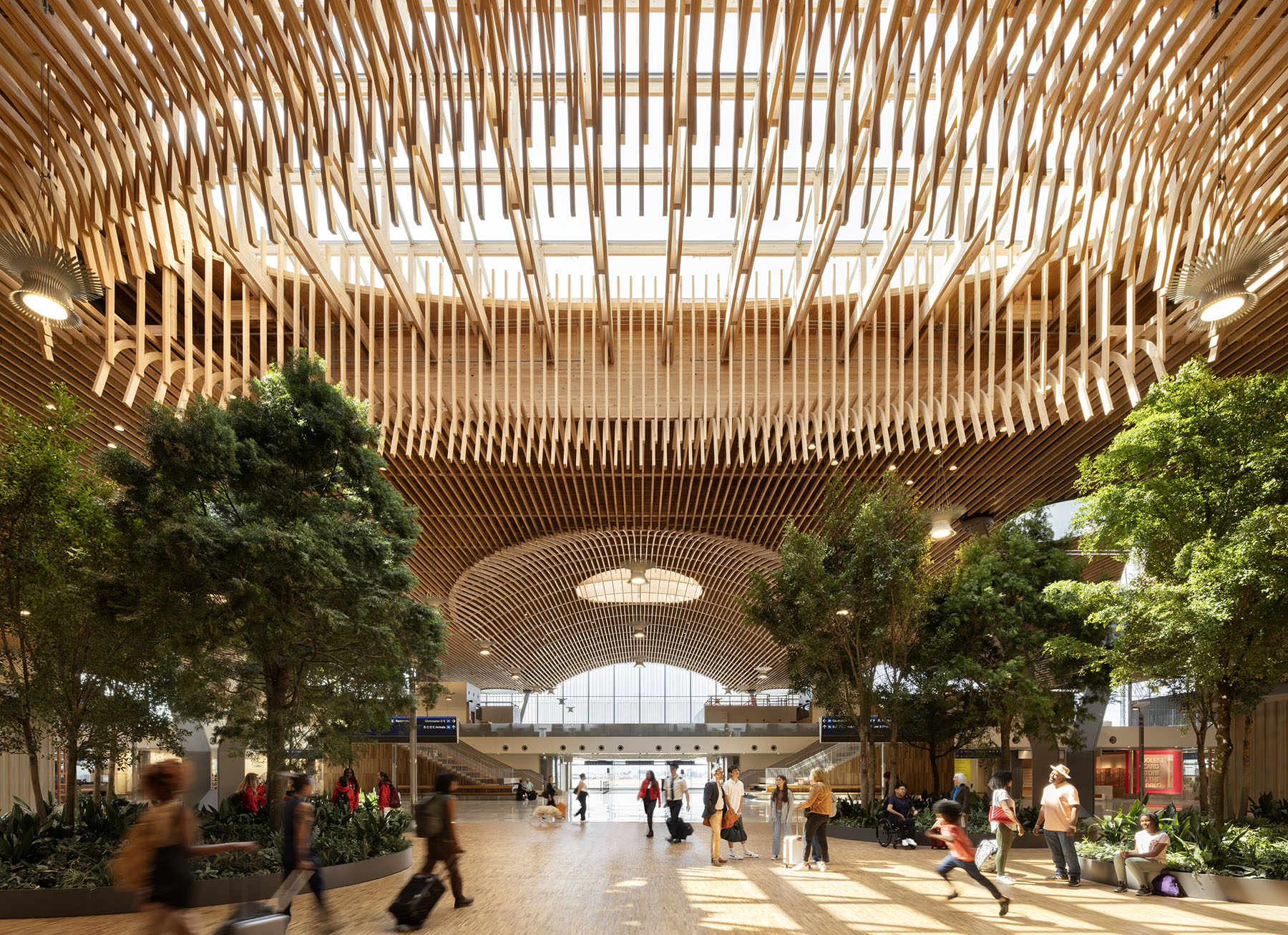
By T.R. Witcher
Oregon’s Portland International Airport consists of about a dozen structures built over the course of more than a half-century. The Port of Portland, which owns and operates PDX, initially asked architecture firm ZGF to remodel the airport’s aging ticket hall, but the minor project quickly grew into a $2.15 billion reimagining of the airport’s main terminal.
The airport needed to double its capacity to 35 million passengers a year by 2045. A new terminal would also have to meet new seismic regulations to ensure it could withstand the impact of a Cascadia-level event – a giant, magnitude 9 earthquake. Further, the new airport had to avoid putting increased power demands on its central utility plant, says Nat Slayton, AIA, a principal at ZGF.
Further reading:
- New Kansas City International Airport terminal opens
- Innovative seismic design shaped new airport terminal
- Timber design chosen for Zurich Airport
And it all had to happen while the airport remained open for business. And one more twist: How would the team do all this without destroying the aesthetic fabric of an airport that Portlanders (and many other travelers) love for its coziness? (Travel + Leisure magazine readers voted PDX the country’s best domestic airport every year between 2013 and 2019 and again in 2021.)
Just ask ‘Y’
The solution was finding the right structure. Working alongside structural engineering firm KPFF, ZGF designed a new 400,000-square-foot terminal around the footprint of the existing building. The firms devised a large modular roof anchored by 34 Y-shaped columns that would be supported on new, seismically resilient foundations. Seismic isolators were placed on top of each prong of these Y columns, which reduced the size and weight of the columns and the foundations.
The new roof is designed to move roughly 2 feet relative to the floor below during a major seismic event, then to come back to its original position without damage when the shaking ends, says Christopher Pitt, P.E., S.E., LEED AP, an associate with KPFF’s Portland office.
Most of the new building straddles the existing structure, so only 10 of the 34 new columns penetrate through the original terminal building. But those 10 columns created challenges – architects and engineers spent almost two years analyzing the space to ensure that the new columns weren’t coming down into critical areas.
“That sounds simple, but we had to locate those in a place where they wouldn’t disrupt the operation of the airport,” said Joe Schneider, senior vice president and account manager for New York City-based development and construction company Skanska.
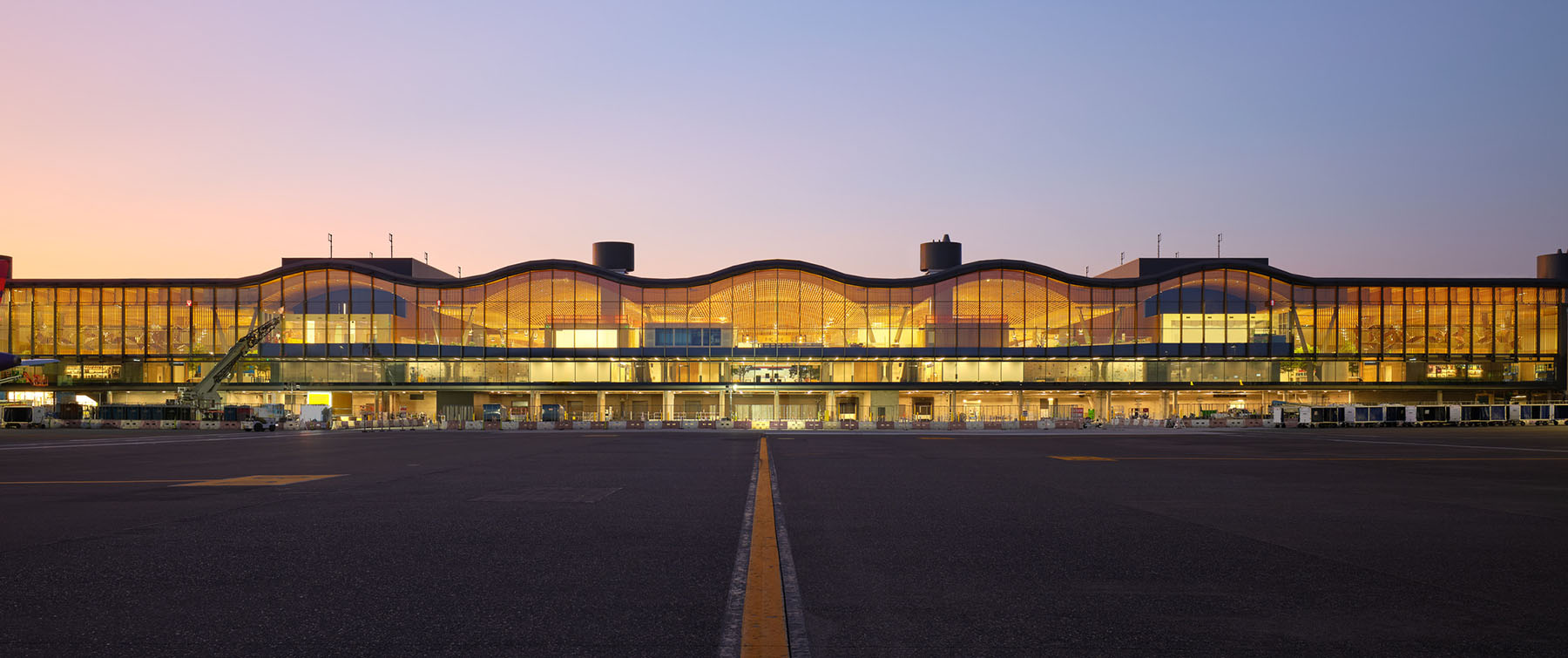
“I remember very distinctly one grid study where we had gone through all of the column locations but one,” Pitt added. “We got to the last column, and we realized it landed right in the main network room, basically the internet connection for the whole airport. We were like, ‘OK, start over.’”
The columns and their foundations were designed in some cases with “eccentric and contorted shapes” to miss critical infrastructure in the deplaning level, Pitt said.
Assemble, disassemble, move, reassemble
Because local regulations prohibited using construction cranes over occupied buildings, the new terminal’s roof was constructed at a fabrication yard on the airport site, says Schneider, then broken down into 18 modules and painstakingly moved into position over the course of four months.
The roof structure was built at an elevation of 13 feet on temporary structures. Then, Dutch heavy-object transport company Mammoet jacked the roof elements up to 55 feet, where the roof modules were positioned onto a temporary transport structure that sat upon Mammoet’s self-propelled modular transporters. The SPMTs then drove the roof module to the construction site at a leisurely 5 mph.
Once the roof elements had been moved to the terminal site, Pitt said, “They’d basically start out over the first Y column support that was right at the edge of the terminal, and it would already be cantilevered a bit, then they’d launch it out to the temporary shoring towers, then they’d launch it out to the next Y column, and then there was another 50 feet (of) cantilever beyond that. So they could do that whole movement, roughly 150 feet or so of launch, over the two nights with just a couple hours of closure each night.”
Connecting the airport to the forest
The 34 new columns, designed on a 100-by-150-foot grid, replace 670 columns in the old terminal. Reaching 36 feet high, these new columns create a large, open, flexible space and support a new mass timber roof comprising an undulating lattice of 35,000 pieces of Douglas fir wood. ZGF wanted to break the space down into smaller, inviting rooms that would evoke a stroll through the forest. The goal, Slayton said, was “to have moments, thresholds, within that space, which really amplified moments of delight, connections to nature, the sky – exactly at the same moments you might otherwise have stress.”
The roof’s 49 skylights not only help define these “room” experiences in the terminal by creating irregular rhythms of light, they also reduce the lighting energy load on the project by 60%.
The roof’s glulam beams feature long cantilevers, which need moment connections at their supported ends, which is rare for wood structures. “We ended up developing a tension-compression couple system where the top ones also need to be able to accommodate quite a bit of shrinkage movement,” Pitt said.
The system uses long rods with spherical washers so they can take the tension load at the top, Pitt continued, “and then as it moves down an inch and a half or so for shrinkage over time, they won’t cause the beams to deflect more and are detailed to ensure there’s no cross-grain tension that could cause splitting.”
But the story of the roof is more than engineering the wood. The Port of Portland challenged ZGF to make a more robust connection between the terminal’s roof and the local communities and businesses that, as Slayton put it, “grow the wood, cut the wood, mill the wood, fabricate the wood, and install the wood.”
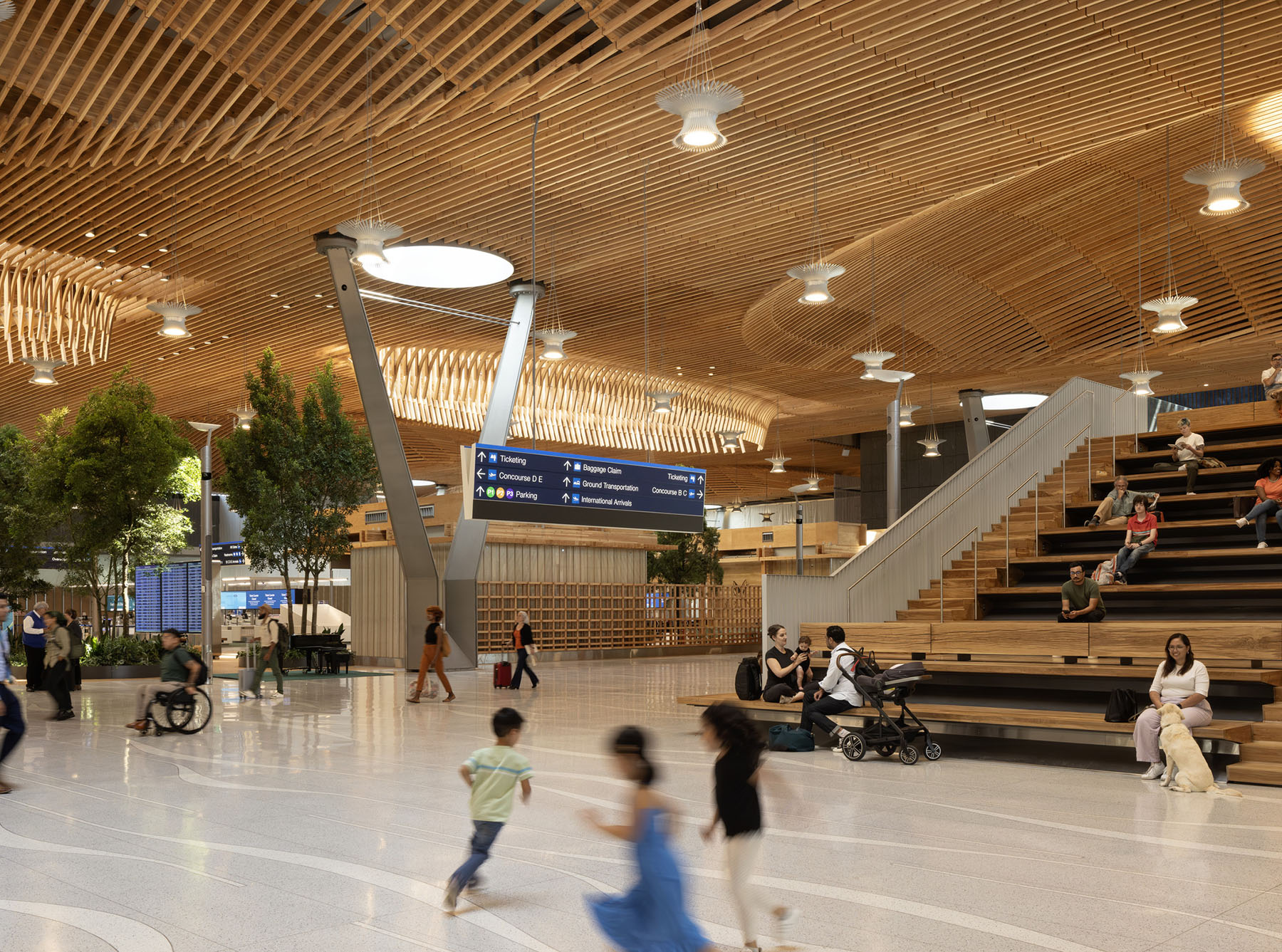
Typically, when wood arrives at a construction site, it has been brought together from various forests and mills and mixed so many times no one really knows where any of it came from – or even if it came from the local region. Devising a scheme to track and tag the wood through its complex supply chain allowed smaller companies, family-owned mills, and fabricators to plug into this giant public works project “to really lift up the full region in a new way,” Slayton said.
In the end, 100% of the wood in PDX’s new roof came from within a 300-mile radius; Slayton says 30% of the timber can be traced to its forest of origin. Further, he added in a follow-up email, 73% of the wood was sustainably harvested.
One more phase to go
The terminal opened to the public on Aug. 14, but some work remains in an ongoing phase 2, which involves replacing the old heat system in the airport’s central utility plant with a new ground source system.
Below the airport, crews are drilling wells into an aquifer. Water will be pulled from the aquifer at around 58 degrees Fahrenheit, then run through a heat exchanger, then put back into the ground at around 40 F. It’s like a heat pump, says Jeff Becksfort, P.E., LEED AP, with PAE, the consulting engineering firm that designed the mechanical, electrical, and plumbing systems on the project. Only instead of exchanging heat with air, “What we’re doing is exchanging heat with water.”
This new system, which will be finished in early 2026, will replace an old, inefficient steam boiler system powered by natural gas – and cut the fossil fuel needed to heat and cool the airport by 90%.
“Everybody loves the project,” Schneider said. “I mean it’s just unanimous praise from everybody. It’s just amazing for the city of Portland. And so people are falling in love with their new airport, and I think the photographs tell the story.”