By Jay Landers
In fall 2021, as supply chain disruptions began reaching crisis proportions, national attention turned to the problem of the increasing numbers of massive container ships waiting off the Southern California shore, unable to enter the ports of Los Angeles and Long Beach in a timely manner. Bedeviled by labor shortages due to COVID and an insufficient number of truck drivers, the two ports, which together handle about 40% of the goods entering the United States, could not keep up with the surge of cargo arriving from Asia.
Undoubtedly, the situation was enormously frustrating for the Port of Long Beach, which by then had been working for nearly 15 years to significantly expand its rail capacity. Fortunately, the Maritime Administration within the U.S. Department of Transportation released, in April, its record of decision certifying the federal environmental impact statement for the port’s planned $1.5 billion program known as the Pier B On-Dock Rail Support Facility. Along with boosting the port’s rail capacity, the project will make the facility more competitive while reducing traffic congestion on local roadways and improving air quality.
The move by MARAD means that the port can now receive $52.3 million in grant funding that the agency had awarded the project in late 2021. The action also enables the port to begin acquiring the nearby properties needed to expand its rail facilities and to seek the two remaining regulatory permits required for the project.
More space for trains
The Port of Long Beach is the second-largest port in the United States by volume of cargo handled, behind only its neighbor, the Port of Los Angeles. In 2021, the Long Beach port handled 9.4 million twenty-foot equivalent units, or TEUs, which are standardized cargo containers having dimensions of 20 ft by 8.5 ft by 8 ft. An all-time high, this level of cargo traffic represented a 15% increase from the previous year.
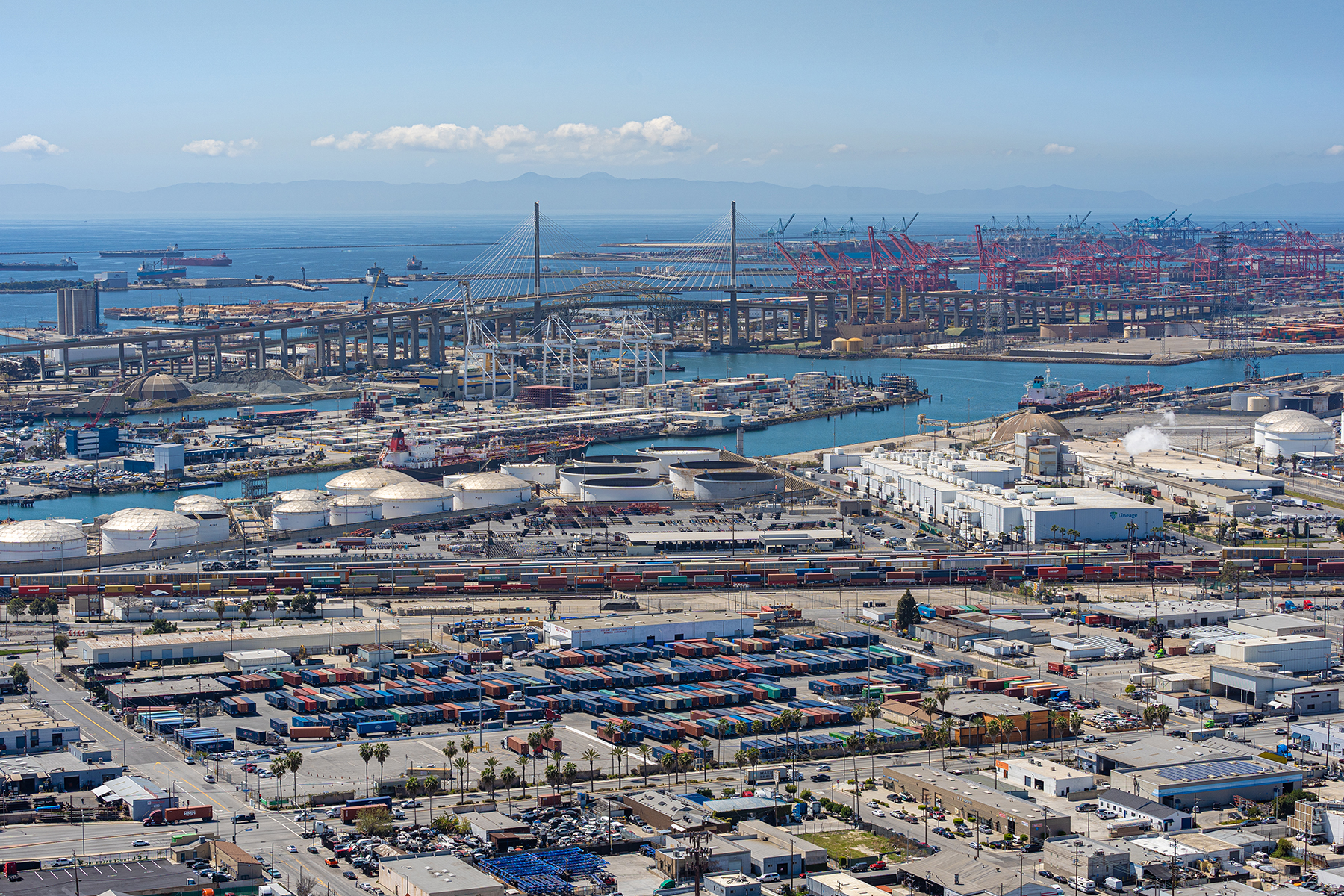
When container ships dock at the Port of Long Beach, their containers are unloaded and transported inland either by rail or truck. Meanwhile, trains and trucks also deliver containers to the port to be shipped overseas.
Five of the six container terminals at the port have on-dock rail yards, where inbound containers can be transferred directly from ships to trains and outbound containers can be transferred directly from trains to ships. Because the arrival of ships and trains cannot always be coordinated precisely, the port needs space in which to stage trains while they wait to be loaded or unloaded, says Mark Erickson, P.E., M.ASCE, the deputy chief harbor engineer for the port.
In essence, the Pier B On-Dock Rail Support Facility involves adding significantly more space at the port for trains, Erickson says. “We’re building a train staging area,” he says. “It’s a big rail yard where we can hold trains for just a short period of time, so that the terminals and railroads can operate more fluidly.” Ultimately, the improved operations will increase the overall competitiveness of the Port of Long Beach, Erickson notes.
Rail to the rescue
Today, approximately 22% of cargo entering and exiting the port is handled by on-dock rail, while the rest is handled by truck. However, the port has set a goal to move at least 35% of cargo by on-dock rail, Erickson says. Greater use of on-dock rail will reduce local traffic congestion and air pollution associated with truck traffic to and from the port. “One train can take 750 trucks off the road,” Erickson says.
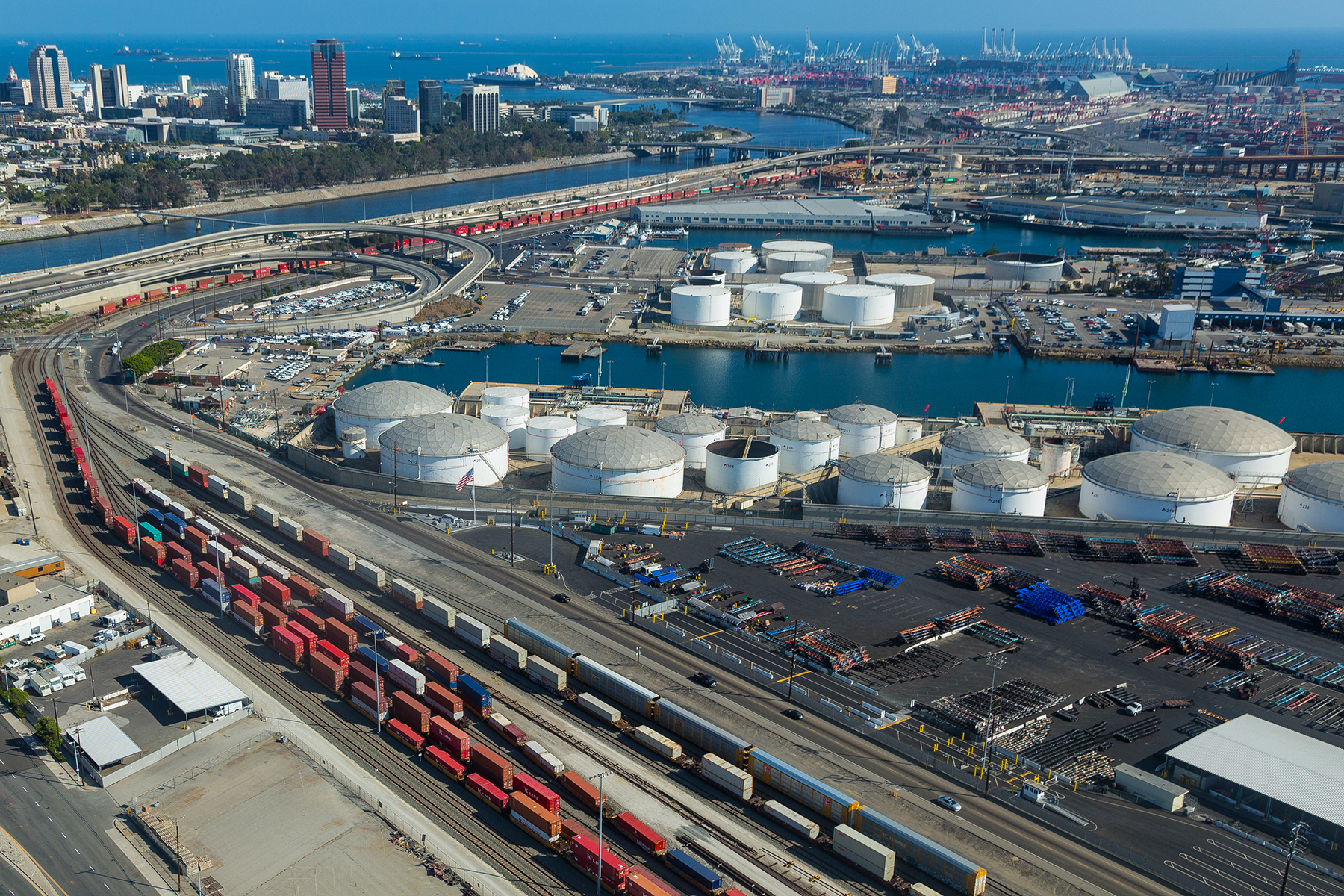
All told, the existing rail yard at Pier B will be expanded from 82 to 171 acres, and the number of tracks will be quadrupled, from 12 to 48. The new tracks will include five arrival/departure tracks, each of which will be 2 mi long and used to stage complete trains. Pier B currently has no arrival/departure tracks. The project also will add 31 yard tracks, which are used to stage and store train cars. Today, Pier B has 10 such tracks. Ultimately, the revamped Pier B will boast 130,000 ft of new track.
Expansion of the rail facilities at Pier B also will enable the Port of Long Beach to conduct on-dock rail operations faster and more efficiently, particularly by accommodating longer trains. Currently, the port lacks the space necessary to handle trains more than 8,000 ft in length. However, container trains increasingly reach lengths of 10,000 ft or more. Trains exceeding 8,000 ft in length must be broken down into smaller units, adding delays and inefficiencies. With the expanded staging area at Pier B, the port will be able to assemble or disassemble larger trains.
By adding to and reworking the existing track network, the port also will enable trains to travel directly to and from Pier B and what is called the Alameda Corridor, a critical 20 mi long freight rail line that connects the ports of Los Angeles and Long Beach with the mainlines of two major railroads.
Improved efficiency
Ultimately, the improvements made as part of the overall project will make every on-dock exchange between the container ships and the port “more efficient,” says Tom Kim, P.E., the project manager for HDR, which is working with the Port of Long Beach to develop the final design for the project.
The improved efficiency will decrease the times that ships must wait offshore for port capacity to be freed up. “They’re going to move these containers quickly to the Pier B rail yard, load the trains, and move the goods out to the Alameda Corridor,” Kim says. “This will decrease the time ships are docked, allowing more ships to come in and out.”
The added on-dock rail capacity provided by the project will help ensure that container ships do not have to wait idly outside the Port of Long Beach in the future, Kim says. For this reason, the project is “very critical for our national economy,” he says.
Many stages
The Pier B On-Dock Rail Support Facility project has been in development since 2007, and HDR has been involved with the effort the entire time, says Try Khou, P.E., the deputy project manager for HDR. Between 2007 and 2018, HDR supported the port by conducting engineering analysis, preliminary engineering, construction costs estimates, and construction phasing for the project.
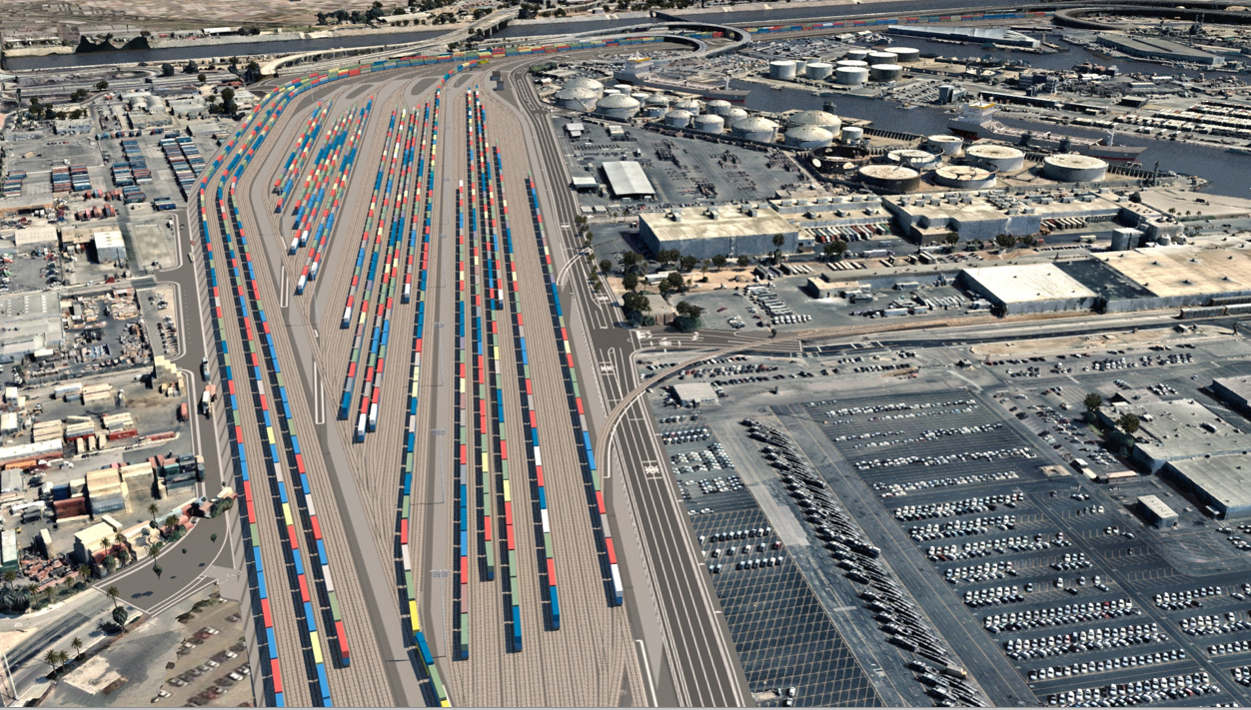
The firm also supported the development of the environmental impact report required by the California Environmental Quality Act. The report was finalized in January 2018. In spring 2019, HDR was awarded the engineering design services contract for the final design for the overall project, with the notice to proceed given that July.
For the final project design, HDR is responsible for the track and rail design and the utility and drainage design, Khou says. Among the main subconsultants on the project, Moffatt & Nichol is designing the structural elements, while Port Design Partners is handling the civil design aspects of the project.
The overall project is being delivered in 12 stages, the first five of which are to be constructed between 2023 and 2026. The remaining seven stages will be completed by 2032. The first stage includes extending two existing tracks by 2,500 ft — essentially doubling the capacity of the existing rail yard at Pier B — and constructing an 800 ft long retaining wall along the adjacent Interstate 710.
The second and third stages include further expansion of the Pier B rail yard, the realignment of a street and two rail spurs within Pier B, the removal of tracks from an area that is to house a future flood control pump station owned and operated by Los Angeles County, and the addition of a locomotive support facility. The new pump station is needed to replace an existing county facility that must be moved to accommodate the Pier B expansion.
The fourth stage of the project involves the demolition of the existing pump station and the construction of its replacement. To reduce train delays, the fifth stage will widen, from two tracks to three, a rail bridge over a nearby waterway known as the Dominguez Channel.
Coordination challenges
Before construction begins, the port must obtain two coastal development permits, first one from the city of Los Angeles and then the other from the California Coastal Commission. Although the time frames for securing the permits are fluid, the port anticipates that the processes will last about nine months, Erickson says.
Besides the port’s own infrastructure, Pier B houses facilities and infrastructure owned and operated by 27 private entities and 15 public utilities. Because much of this infrastructure must be moved to accommodate the expansion of Pier B, overseeing the process of coordinating these utility locations is among the top engineering challenges on the project, Khou says. “They all want to relocate to a certain location,” he says. “But there’s a limited amount of space in the corridor.”
At the same time, construction of the massive project must not interrupt the daily operations of the port, Khou says. “It’s business as usual. That’s the other challenge as well.”