By Robert L. Reid
A $245 million renovation designed to enlarge and modernize much of Tennessee’s Memphis International Airport’s Concourse B also provided the first seismic protection for the facility. Constructed in the early 1960s, the original two-level, concrete-framed concourse had been designed to accommodate wind loads but not seismic loads, says Zachary Treece, P.E., S.E., a senior project engineer in the Los Angeles office of Thornton Tomasetti. Thornton Tomasetti was the primary structural engineer on the renovation project and served as a consultant on the building’s envelope and sustainability features.
Following the introduction of new seismic requirements in the 2000 International Building Code, however, it became clear that the Memphis region, located in the New Madrid Seismic Zone, faced a “high seismic hazard that required a robust structural solution,” Treece explains.
Expanding Concourse B
Concourse B is Y-shaped in plan and extends from the southern end of the Memphis airport’s terminal. The renovation project focused on the stem and the southeast leg of Concourse B, increasing the structure’s width from the original condition’s 60-70 ft to 100 ft in the final condition. The project added roughly 15-20 ft of steel-framed space to either side of the original concourse.
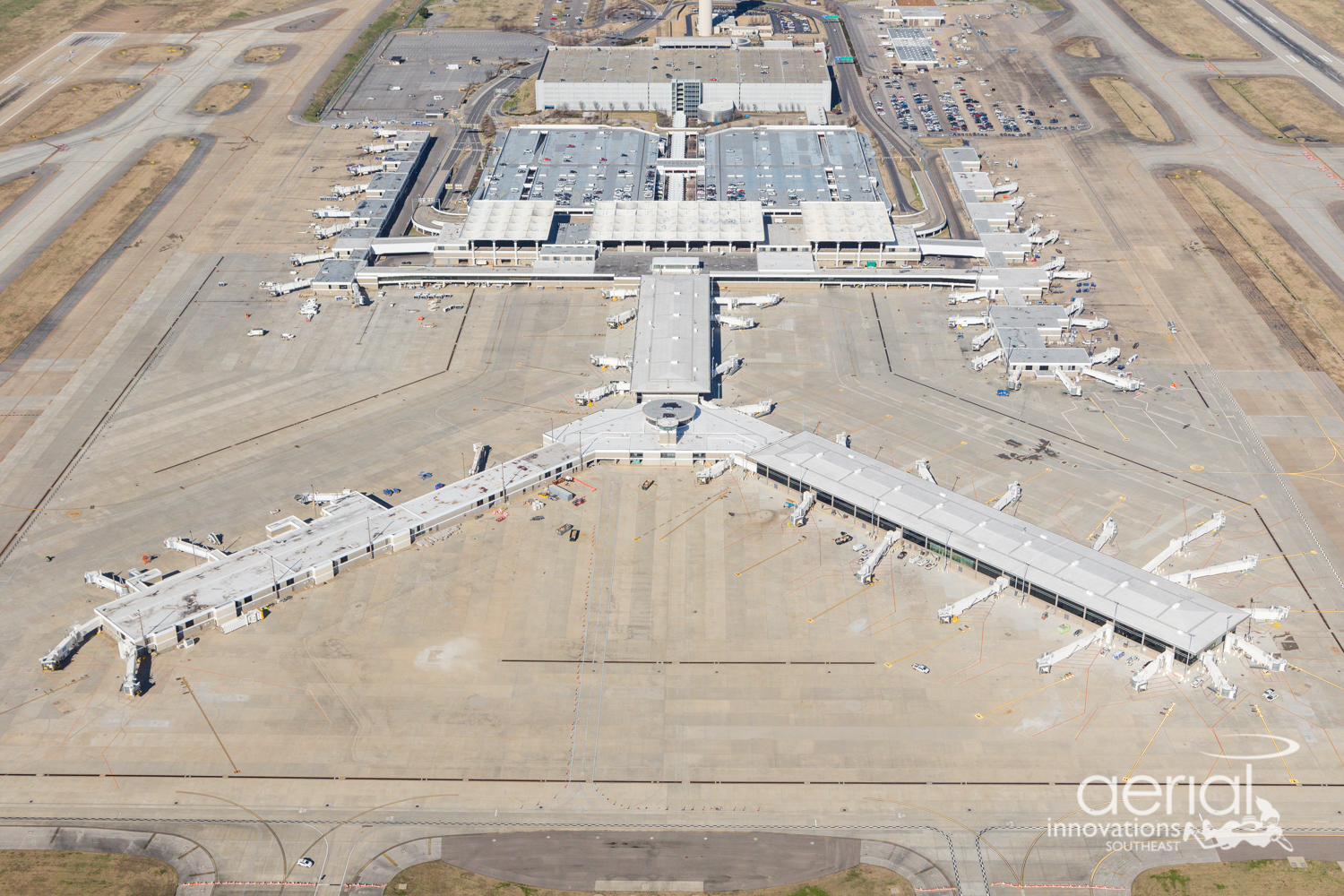
The project also demolished the original roof of the concourse and constructed a new, lighter weight steel-framed roof with higher ceilings that measure approximately 20 ft tall compared with the original 12 ft ceilings, Treece says. The apron level of the concourse, which is not accessible to passengers, was widened with new slab on grade. It houses facilities for maintenance and other airport operations, Treece says.
The southwestern leg of the concourse was not renovated as part of this project but could be modernized in a future project if business at the airport continues to grow, explains the airport’s website.
The project did not add any gates to Concourse B, which has 23 gates. However, Memphis International Airport is considered one of the busiest cargo airports in the United States.
The facility is owned and operated by the Memphis-Shelby County Airport Authority. Memphis-based UrbanARCH Associates served as the prime architect on the modernization project, teamed with Alliiance, the aviation architect, based in Minneapolis. Kimley-Horn, which has an office in Memphis, was the lead civil engineer. Flintco Construction, based in Tulsa, Oklahoma, was the general contractor. Parsons Transportation Group, based in Chula Vista, California, served as the program manager.
Steel framing
To achieve the wider, column-free corridors and higher ceilings of the modernized concourse’s second level, long-span steel trusses were installed that span the full 100 ft width of the new roof level. The existing lower level was buttressed with a system of dual concentrically braced frames and vertically cantilevered perimeter columns to resist seismic forces — a lightweight design that made the new Concourse B as much as 15 times more resilient to seismic forces than it previously was, explains Thomas Poulos, P.E., S.E., a senior principal in Thornton Tomasetti’s Chicago office and the firm’s market sector leader for aviation.
Spaced approximately 40 ft apart along the length of the concourse, the new cantilevered columns consist of W24 x 306 columns used specifically to resist lateral loads at the roof, says Treece. In the longitudinal direction of the concourse, cross bracing consisting of 8 in. to 10 in. diameter round steel tubes, typically, was used to stiffen the lower and upper levels “so that under seismic loads, the building would not move more than what it had been originally designed for under wind loads,” says Poulos. Similar cross bracing was used to stiffen just the lower level in the transverse direction, he adds.
High-strength, 1 in. diameter steel rods were used to connect the new steel-framed portions of the concourse to the existing concrete framing “so we could tie everything together and have it act as one structure,” Poulos says.
The new portions of the concourse are founded on a series of 5 ft thick concrete mats that support the steel bracing and resist overturning. The cantilevered columns are secured via high-strength anchor bolts that can accommodate as much as 220,000 lb each — roughly triple the strength of typical anchor bolts, Poulos notes.
“As the building accelerates in an earthquake,” Treece explains, “one side will want to pick up, while the other side will want to push down. These anchors will hold down the side that wants to lift up.”
Additional efforts
Matching floor elevations within the new concourse spaces was among the project’s challenges, says Poulos, who notes that these elevations varied by as much as 3 in. across the concourse, depending on what finish had been used originally in a given location. To resolve this, a variety of solutions were used, including adjusting the top of the new steel elevation to align with the existing concourse slab, using leveling compounds to adjust elevations, and providing field-adjustable connections where the new steel framing connected to the existing concrete structure. The project also located all mechanical systems to a new space underneath the concourse — in a roughly 2 ft deep excavation — to further reduce weight atop the new structure.
A “dynamic self-tinting glazing” was used within an aluminum-framed curtain wall system in the new concourse to block solar radiation and glare during hours of direct sunlight exposure, explains an architectural narrative from UrbanARCH. The glazing is untinted during hours without direct sunlight and cloudy periods.
The renovation work was completed in February. During the project, Concourse B was temporarily closed, and passenger traffic was shifted to gates in concourses A and C, which are on the east and west sides of the terminal, respectively. With the expanded concourse now available, concourses A and C will be closed but retained for possible future use, according to the airport website.