By Jay Landers
The manufacturing of building materials and the construction of buildings are key sources of carbon emissions globally. Looking to offset these emissions domestically, the U.S. Department of Energy recently awarded $39 million in funding to 18 research teams seeking to devise methods for designing and building structures that ultimately store more carbon than is released during their construction.
“This is a unique opportunity for researchers to advance clean energy materials to tackle one of the hardest-to-decarbonize sectors that is responsible for roughly 10% of total annual emissions in the United States,” DOE Secretary Jennifer Granholm said in a June 13 news release.
Net-carbon-negative buildings
In June, the DOE’s Advanced Research Projects Agency-Energy announced the recipients of funding from its program known as Harnessing Emissions into Structures Taking Inputs from the Atmosphere. Launched in November 2021, HESTIA seeks “to demonstrate the ability to achieve net-carbon negativity in our buildings,” says Marina Sofos, Ph.D., the program director for HESTIA.
To this end, the HESTIA program promotes the development of “building materials that store more carbon than is emitted during their production process” as well as materials that “make more efficient building designs that can similarly store as much carbon as possible and extend the overall lifetime of the building,” Sofos says.
Ultimately, the goal is to produce buildings that are “net-carbon negative on a full life-cycle basis,” Sofos says. As a result, research projects also were evaluated on the basis to which each considered “minimizing the end-of-life emissions and extending the service lifetime of the building,” she notes.
That said, carbon emissions were not the only factor considered by the HESTIA program. To receive funding, projects had to offer “some type of a market advantage or improvement over the incumbent” material or process, Sofos says. “We also included metrics around the actual performance of the material or building element in question.”
Projects selected for funding included alternative concrete mixes, woodlike products and lumber alternatives, insulation materials, structural systems and panels, adhesives, and timber products.
The three projects highlighted below will attempt to develop low-carbon approaches to two of the most common materials used in construction: concrete and lumber. Two of the projects also feature 3D printing, a method that has the potential to significantly reduce waste generated during construction.
Alternative to dimensional lumber
Researchers from Oregon State University received $2.5 million from the HESTIA program to develop a cellulose cement composite, or C3, to be used in residential and light commercial construction. “We’re coupling together cement and other additives with cellulose to try to make a material that could be an alternative to dimensional lumber,” says Jason Weiss, Ph.D., the Edwards Distinguished Chair in Engineering at Oregon State and the principal investigator on the project.
The project builds on previous work done by the researchers to improve cement performance by incorporating cellulose nanocrystals into the material. “This allows us to move into a new class of materials,” Weiss says. “It’s very exciting.”
“There’s really several components that we’re working on to make the C3 as carbon negative and carbon sequestering as possible,” Weiss says. For starters, including cellulose as part of the mixture decreases the amount of cement clinker that must be used to make C3. This matters because significant amounts of carbon dioxide are released during the kilning process that is used to create clinker, which is the active part that essentially acts as the “glue” in cement. In this way, the presence of the cellulose reduces the carbon emissions associated with the production of the C3, Weiss says.
In addition to the carbon embodied in the cellulose, the C3 itself will carbonate, meaning it will absorb atmospheric carbon dioxide. “We’re able to carbonate a lot of the cement” that is used to bind the cellulose, Weiss says. Because the surface of the C3 will be covered with an extremely thin film of cement, nearly all the material will be capable of absorbing carbon dioxide readily. “We’re anticipating that we’re going to be able to get 80% or 90% carbonation,” he says.
Finally, use of C3 could help reduce wildfires, another major source of carbon emissions. This happy outcome would result from the researchers’ plan to use small-diameter logs that are unsuitable for lumber production but provide a source of fuel for wildfires.
As a blend of cellulose and cement, C3 materials “resist rot and fungal growth, fire, and heat transfer,” according to the DOE’s summary. “They can be deployed quickly due to compatibility with current construction processes and lend themselves to large-scale commercial adoption.”
3D printing with ‘hempcrete’
Of the 18 projects receiving funding from the HESTIA program, the largest award — at $3.7 million — went to an effort by researchers at Texas A&M University to develop designs for low-rise residential and commercial buildings that would be constructed using large-scale 3D printing and an alternative to concrete known as “hempcrete.” Consisting of the woody core of hemp plants mixed with a lime-based binder, hempcrete is a lightweight, net-carbon-negative material.
Given its rapid growth cycle, hemp is “really, really good at absorbing carbon dioxide from the atmosphere to build itself,” says Petros Sideris, Ph.D., M.ASCE, an assistant professor in the Zachry Department of Civil and Environmental Engineering at Texas A&M and the principal investigator on the research project. Hemp’s ability to sequester carbon dioxide rapidly makes it “very attractive as a material to use” in projects intended to have low or no associated carbon emissions, Sideris says.
In terms of performance, hempcrete is not nearly as strong as conventional concrete. Therefore, the researchers will examine methods for incorporating other materials to improve hempcrete’s strength. “One idea would be essentially to include some vertical elements within walls made out of hemp,” Sideris says. “Our intention is to select the materials of those elements in such a way that the entire building is net-carbon negative.”
In its current forms, hempcrete, which is not a new material, does not work with 3D printing. “Conventional hempcrete is made for molding,” Sideris says. As a result, the material’s flow properties, consistency, and stability are not compatible with those required for 3D printing. “What we will be trying to do is to make a printable hempcrete mix design,” he says.
An automated process that obviates the need for formwork, 3D printing offers certain advantages compared with conventional construction methods. “Construction 3D printing can significantly lower production costs, construction times, and environmental impacts from reduced construction waste,” according to the DOE’s description of the projects receiving funding from the HESTIA program.
To this end, the Texas A&M research team will seek to “combine a sustainable material with a sustainable construction process,” Sideris says.
At the same time, the project will aim to design long-lasting buildings that are more resilient than conventional structures. “Hempcrete can provide structures that are more resilient to natural hazards compared with commonly used, lightweight, wood-framing construction,” according to the DOE’s summary.
Funicular forms
Development of a new form of concrete that can be used as part of a 3D-printing process also is the focus of a research team, led by the University of Pennsylvania, that received $2.4 million in funding from the HESTIA program. Additional project participants hail from Texas A&M, The City College of New York, architecture firm KieranTimberlake, and specialty chemicals company Sika, which is the industrial collaborator on the project.
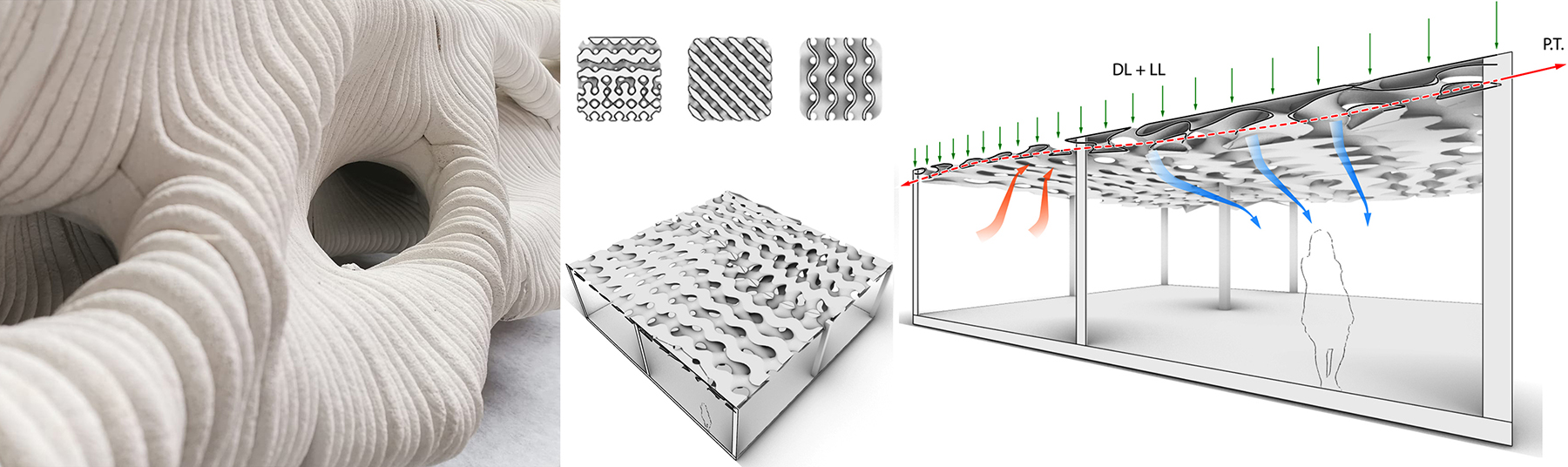
Along with making their concrete compatible with 3D printing, the researchers aim to create a high-performance material that absorbs atmospheric carbon, says Masoud Akbarzadeh, Ph.D., the director of the Polyhedral Structures Laboratory and assistant professor of architecture at Penn’s Weitzman School of Design and the principal investigator on the project. “If you had a material that could absorb carbon, you could contribute to the carbon negativity of the building (constructed with the material),” Akbarzadeh says.
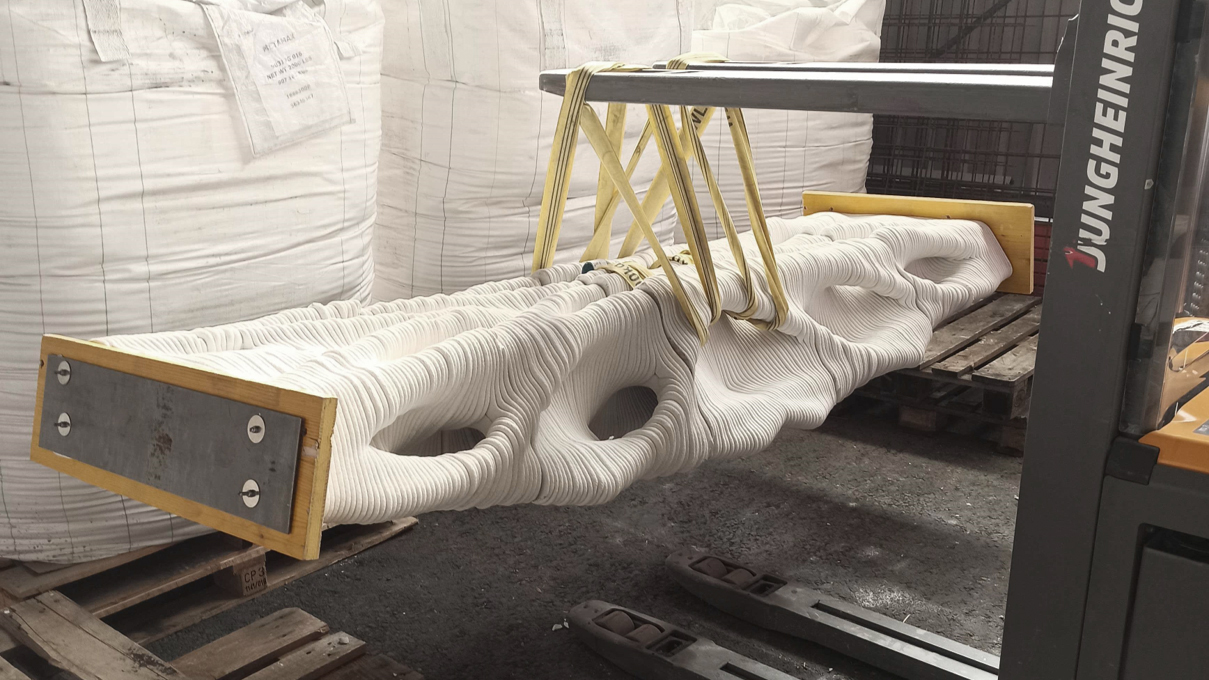
As noted earlier, 3D printing helps minimize production costs and construction waste, improving project performance. Taking this approach a step further, the researchers plan to deploy prefabricated 3D-printed concrete forms as part of a structural floor system that is specially designed to require the minimum mass.
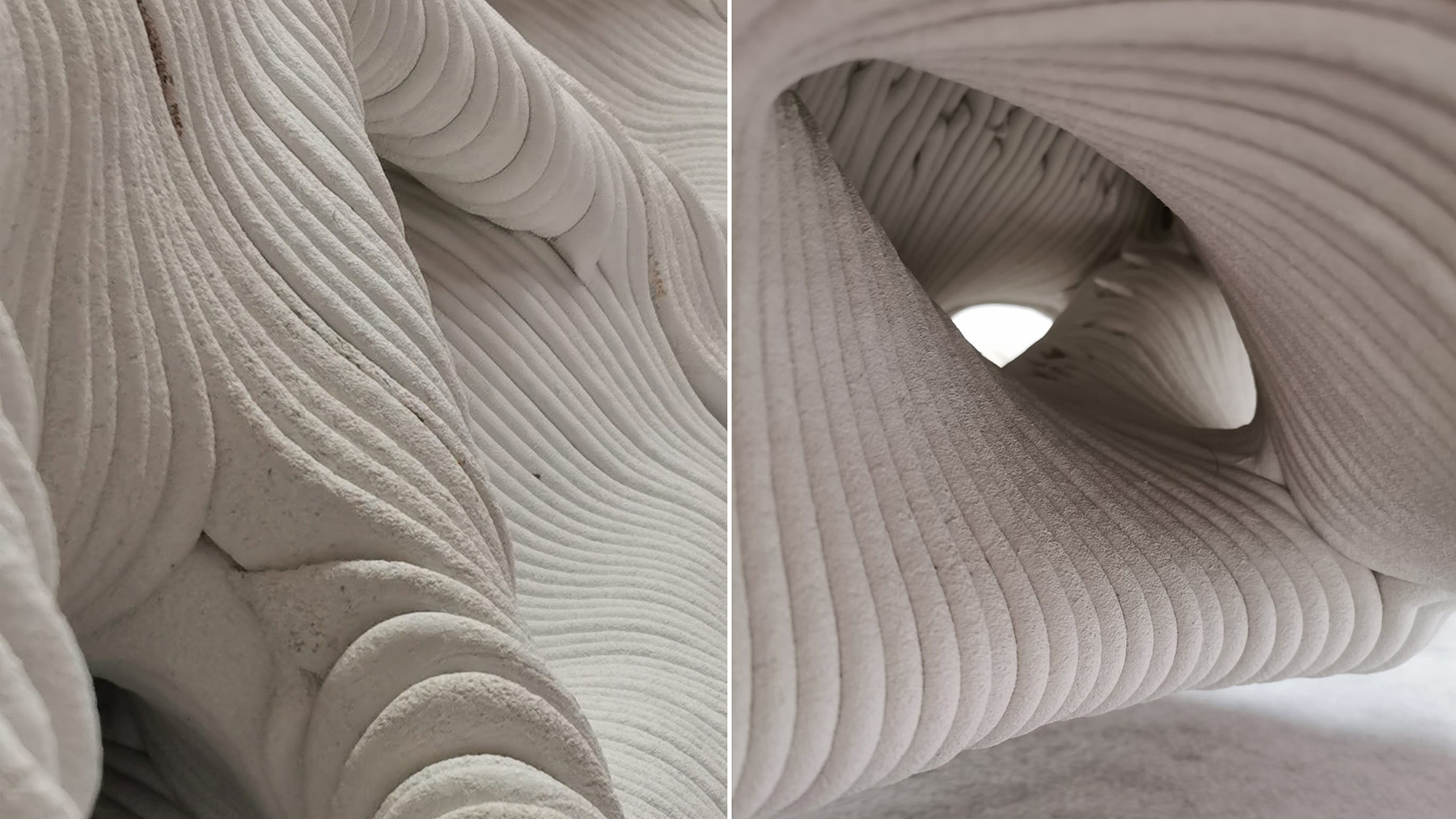
This goal is achieved using what are known as funicular systems, or forms in which the “material precisely aligns with the direction of the flow of force within your structure and there’s a minimum bending moment in the system,” Akbarzadeh says. “These are efficient structural forms that carry the forces in the form of pure tension or pure compression.”
Because of their highly efficient design, such structures require significantly less material as compared with conventional structures. They also “have a large surface area that can be exploited for carbon absorption and radiative heating and cooling purposes,” Akbarzadeh says.
In addition to creating highly streamlined structures made of carbon-absorbing concrete, the researchers also intend to ensure that such structures can be readily recycled and repurposed at the end of their design lives, Akbarzadeh says. To this end, the various parts of a structure will be reinforced by means of post-tensioned cables that can be removed much more easily than traditional steel reinforcement.
Getting started
For its part, the DOE is in the process of negotiating cooperative agreements with the winning research teams and developing technical performance-based milestones for each project. Performance periods for the various projects range from one to three years.
“Now the fun actually begins,” Sofos says.