By Robert L. Reid
Commissioned in 1914, the battleship Texas is the last surviving Dreadnought-type warship in the world and the only battleship still in existence that fought in both World War I and World War II. A floating museum ship since 1948, the Texas recently completed one of its most important missions during this current phase of its service as a tourist attraction and historical artifact: being moved 35 nautical mi. This is the distance from where it had been berthed in La Porte, Texas, to a shipyard in Galveston, Texas, where it is undergoing repairs designed to preserve the ship for another 50 or even 100 years.
Surrounded by a small flotilla of tugboats and other escorting vessels, the Texas was towed through the Houston Ship Channel in late August and is scheduled to remain in Gulf Copper & Manufacturing’s Galveston dry dock until June. At that point the current funding for the project is expected to run out, says Brad Currin, P.E., a senior project manager and the head engineer of the Texas project at Valkor Energy Services, of Katy, Texas.
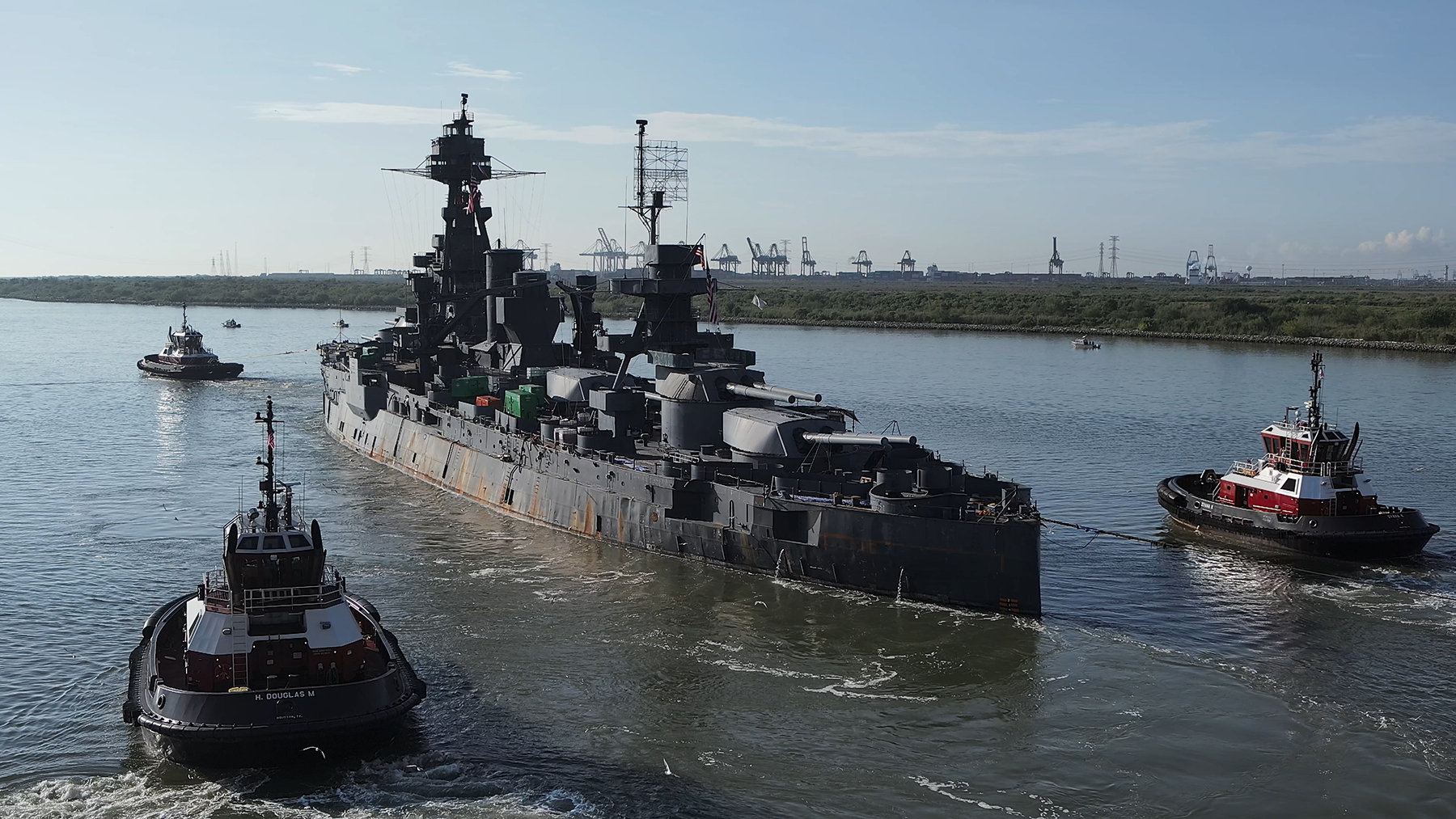
A marine engineering and transport firm that also services the oil and gas industry, Valkor Energy Services is the project manager and lead engineering consultant on the battleship Texas rehabilitation project.
The battleship is owned by the state of Texas, administered by the Texas Parks and Wildlife Department, and operated by the Battleship Texas Foundation, a nonprofit organization that works “to help develop the historic ship into a premier hands-on museum and visitor attraction,” according to the foundation’s website. The foundation is leading the current restoration efforts.
Prove it to move it
The recent trip to Galveston was only the second time the battleship Texas has been moved since becoming a museum ship — it was sent to the same shipyard, albeit then under different ownership, for dry docking and repairs in 1988, says Currin. But after sitting stationary for the 31 years in a slip at the San Jacinto Battleground State Historic Site, off the Houston Ship Channel, the ship was considered by many people to be too deteriorated and unseaworthy to move again.
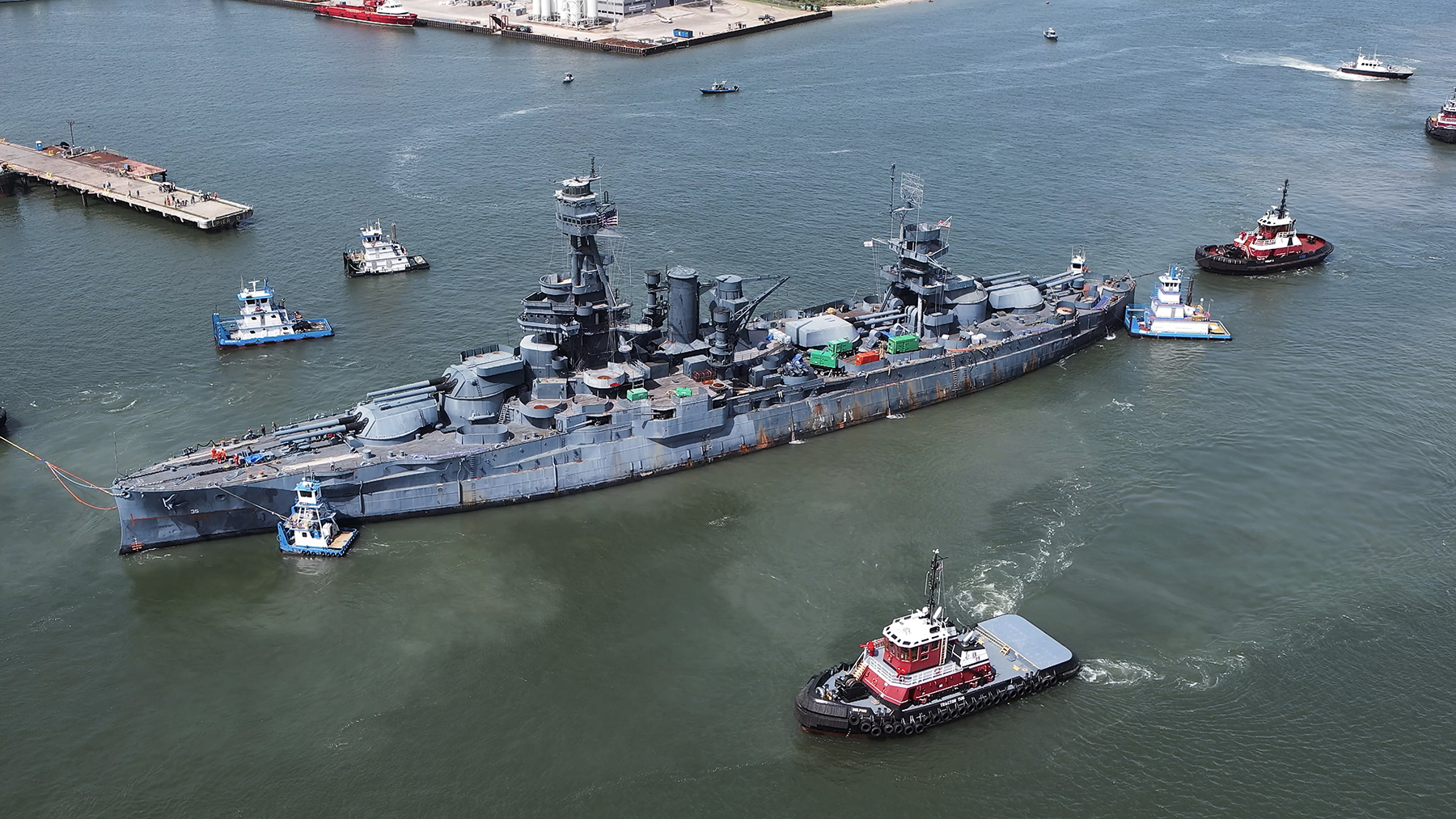
“The longstanding narrative was that the battleship was in such bad shape that there was a huge probability it would sink in the middle of the channel,” says Aldo Benavides, Valkor Energy Services’ project director and chief operating officer. “The first thing we had to do, just to get funding from the state, was to prove that the condition of the ship would allow it to be moved.”
The state had been considering options that ranged from spending $100 million to stabilize the ship in place, with no actual repairs, to $35 million to simply scrap the old vessel. Instead, Valkor Energy Services proposed the current scheme to spend $35 million to tow the Texas to the Galveston dry dock for restoration. “I thought surely for $35 million we can keep it floating for another several years,” Benavides explains.
Assessing the ship
Starting in 2019, Valkor Energy Services worked with a number of firms to gather data and create structural models to demonstrate the feasibility of the plan to move the Texas. For example, Ardent, a global marine and offshore services company based in the Netherlands, used a naval architecture software known as General HydroStatics, from Creative Systems Inc., of Port Townsend, Washington, to survey the Texas’s structural condition, including the thickness of the hull steel and internal steel supports.
The survey also indicated the potential for hogging moments, which could lead to possible buckling from the imposed compression forces in the midship portions of the vessel during the tow, says Currin.
Other firms involved in the project included United Kingdom-based Offshore Consulting Group, which helped perform structural and construction design basis calculations, and Fort Lauderdale, Florida-based Resolve Marine, which helped plan the actual towing operation.
Although the various tests and surveys indicated that the Texas “was in much better shape than anyone expected,” Benavides says, the ship did have problems. For one thing, it was actively taking on water, especially in the two so-called blister tanks that had been added to either side of the hull between the wars as a defense against torpedoes.
A series of some 40 bilge pumps had been installed to continually drain the tanks, which at times during the project were pumping out water at rates of 2,000 gal./minute. Moreover, various watertight compartments within the ship were no longer watertight — they had been compromised over time by corrosion and earlier efforts that involved cutting into these constrained spaces to create larger areas for easier maintenance and pumping access, says Currin. The end result was that water could potentially move around within the ship in ways that no one could easily predict, follow, or control.
“There was no real telling where the watertight integrity remained,” Currin says.
In addition, a ship like the Texas was never meant to be moored in one place, unmoving for decades at a time, with no oil, fuel, or ballast in its various holds and with major parts of the ship removed, including the propellers and shafts and various smaller guns (though the iconic large turrets remained in place).
Such changes made the ship’s center of gravity uncertain, notes Benavides, and raised concerns over how the vessel would perform as it was towed, including whether it would be in danger of rolling over.
Pumping water in and out
Ultimately, though, the team developed a plan to move the ship that satisfied the various stakeholders, from the state legislature to the insurance companies and even the U.S Coast Guard, which is in charge of the Houston Ship Channel.
New steel supports were installed at critical locations within the ship to stiffen the vessel, temporary salvage patches were added to leaking areas on the blister tanks, and a two-part, polyurethane closed-cell foam material was pumped into the blister tanks to prevent any large volumes of water ingress, says Currin. The foam worked “like a very large bandage to buy us time to get to the shipyard,” he explains, adding that once the foam was installed the level of pumping dropped from 2,000 gal./minute to less than 25 gal./minute.
But one problem “with corroding vessels is that they do not get better with time; they only get worse,” Currin adds.
So for the move itself, additional pumps were installed at critical locations throughout the ship until the Texas had approximately 20,000 gal./minute of pumping capacity onboard. Water ingress increased as the battleship was towed through the ship channel, so the pumping rose again as well to about 150 gal./minute — a sustainable level “that we could stay ahead of and keep under control,” Currin notes.
Ironically, given how hard the project team worked to keep water out of the battleship, it also pumped water into key sections of the vessel to help during the move. “One of the unique aspects of the tow was that we actually pumped in 1,600 long tons of water into the midship section to basically ballast it down and reduce that hogging, to relieve the compression stresses on the shell plating at the bottom of the midship portion,” explains Currin.
To ensure an easy tow, about 33,000 cu yd of silt and other material was dredged from the area around the Texas’s slip “to make sure we had a free and clear access to pull the vessel out into the main ship channel,” Currin says. Likewise, the remnants of an old sheet pile wall were removed to eliminate potential obstructions.
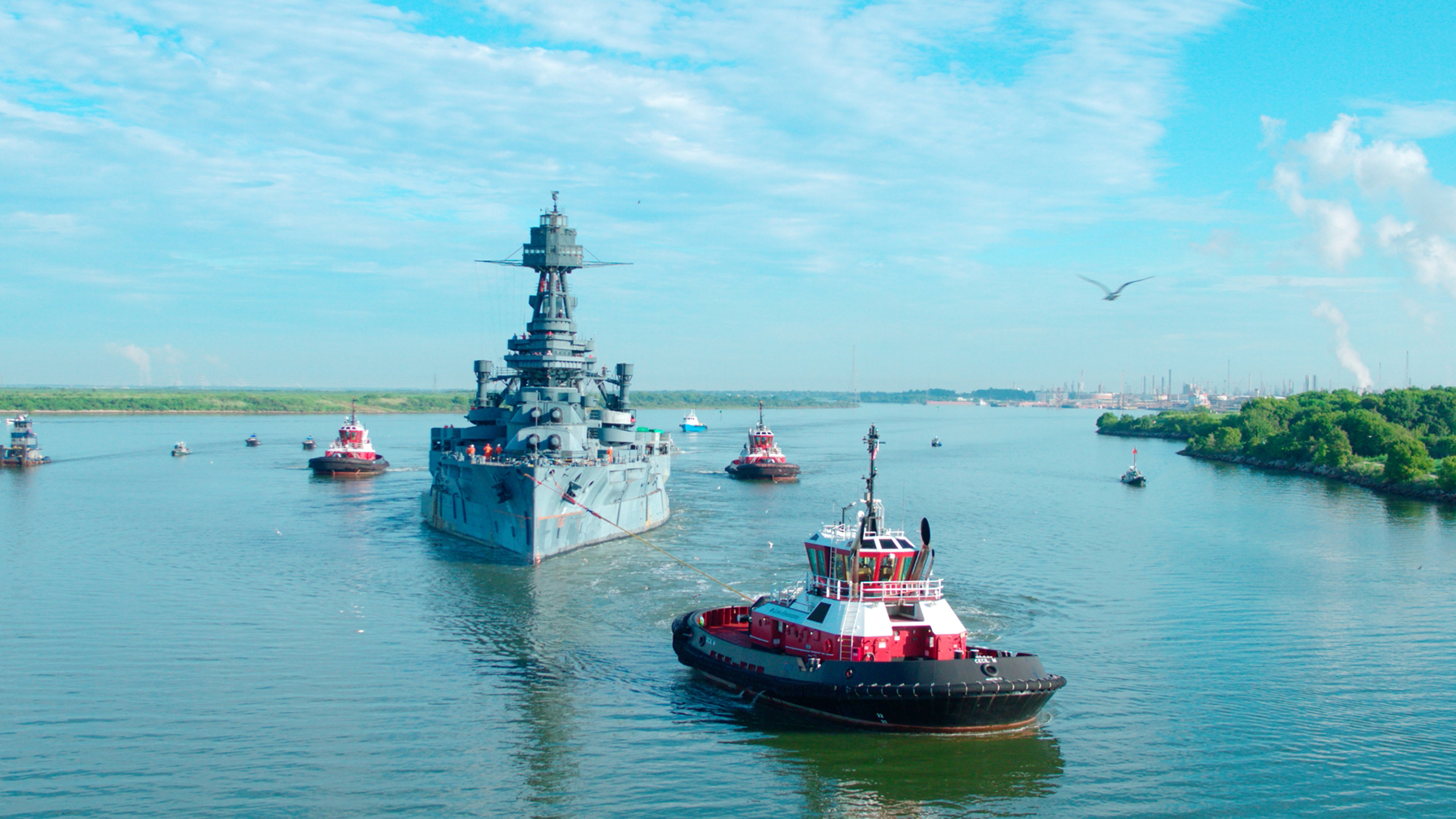
With one tug at the bow, another at the stern, several escort vessels nearby, a Coast Guard Cutter in the lead, and a roughly 1,000 ft radius safety zone established around the battleship, the Texas began its roughly 10-hour journey early on the morning of Aug. 31. The stern tug helped steer the battleship during the move because the big ship’s rudder was locked in place at a 14-degree angle that made the vessel continually turn to starboard, Currin adds.
A future up in the air
Once at the Gulf Copper shipyard, the 26,000-ton battleship was positioned within a floating dry dock and lifted out of the water for repairs. Somewhat appropriately, the dry dock itself had been recently restored after suffering severe damage and sinking near the Bahamas, says Currin. He and Benavides examined the structure, which had been cut in half and refloated, and determined that the 50-year-old system remained in good working condition and would meet the needs of the Texas project.
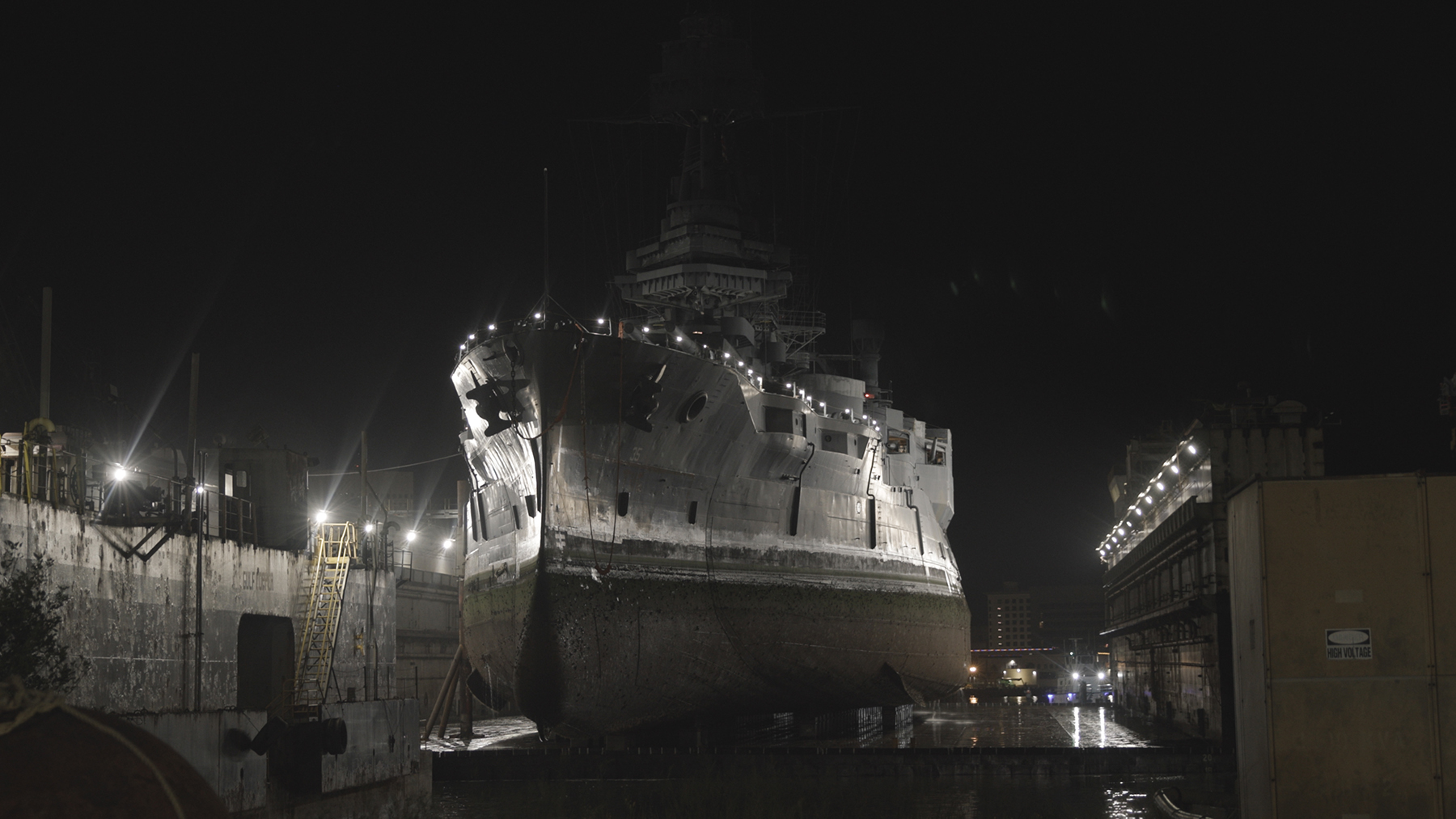
At publication time, repairs to the battleship were underway, including the removal of the foam material from inside the blister tanks via a high-pressure water nozzle. The blister tanks themselves will then be removed so that original sections of the hull can be accessed for additional repairs.
Because the amount of work needed far exceeds the current budget, the project team is actively seeking more funding Currin says. “What we’re doing is figuring out how far we can stretch that money,” he explains.
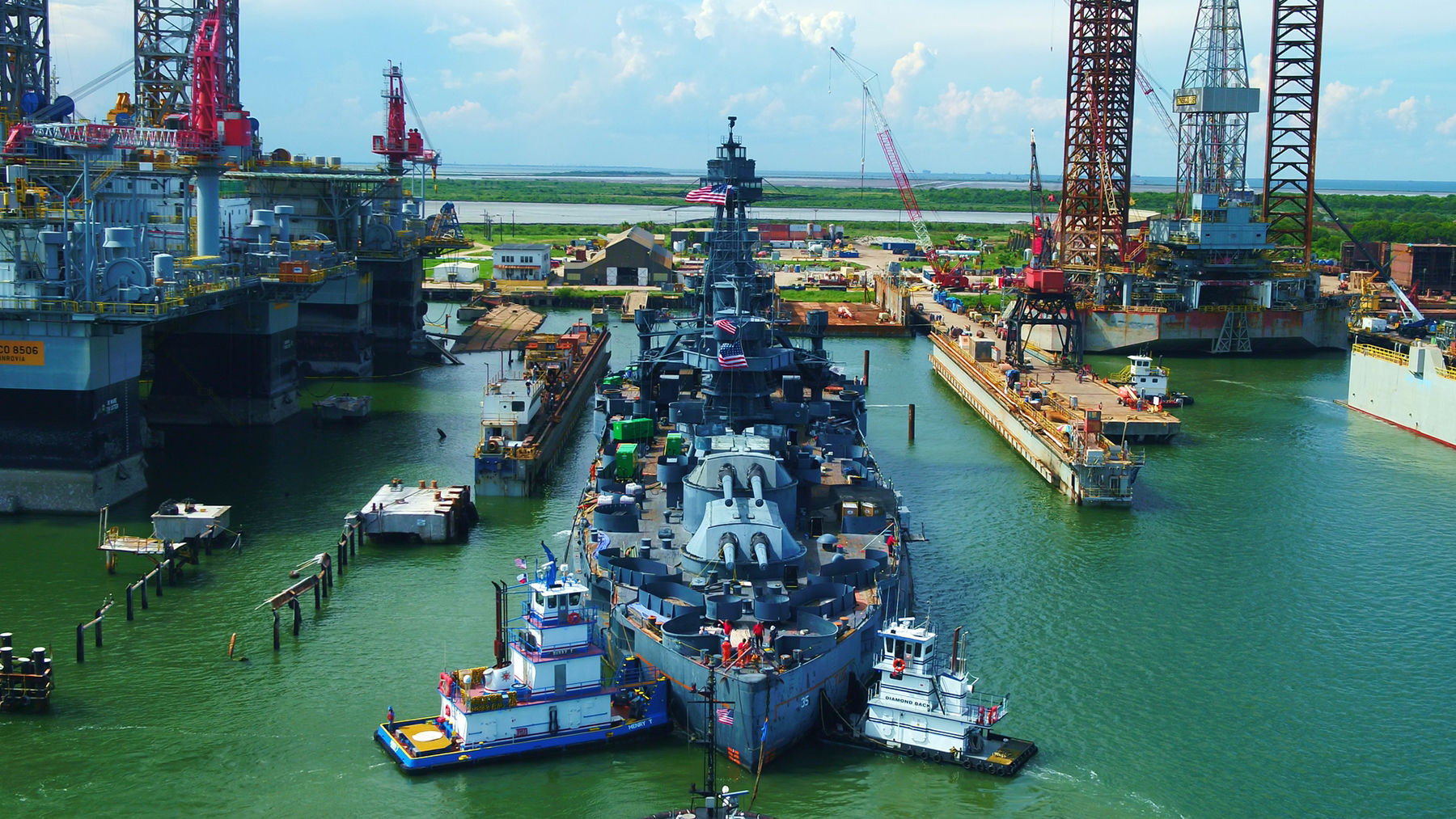
This article first appeared in Civil Engineering Online.