By Robert L. Reid
When the London office of the global infrastructure consultancy AECOM was asked by the United Kingdom’s Houses of Parliament to refurbish the Elizabeth Tower the engineers expected the job would involve a “fairly light touch” to maintain the tower, notes Stephen Baker, CEng, MIStructE, an AECOM associate director. The iconic 96 m tall brick, stone, and ironwork structure at the Parliament complex was completed in 1859 and houses the country’s famous, four-sided Big Ben clock.
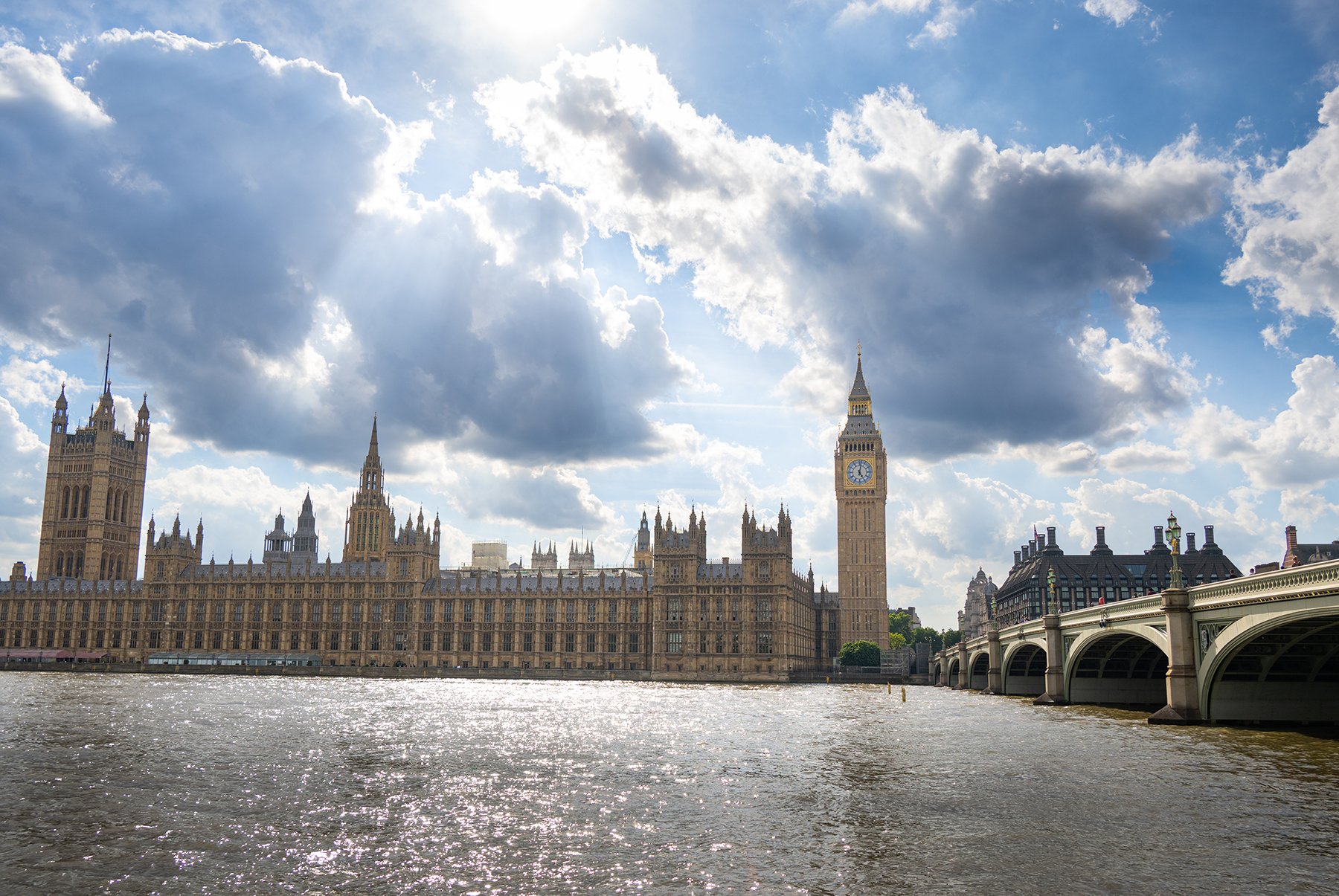
But “as soon as (parts of the tower) started to be uncovered, it became apparent that more and more work was required,” says Baker. This was especially the case for sections of the structure damaged by falling bombs during World War II but never fully repaired.
Ultimately, the refurbishment involved structural work on thousands of individual cast-iron components from the tower’s 30 m tall roof above the clock faces.
These components had to be stripped of lead-based paint and examined for cracks or other damage. Much of the ironwork was then removed and either repaired or replaced by casting new iron elements from an old foundry that was reopened just for the Elizabeth Tower project, explains Baker. The sections of iron in good condition were left in place but — in order to avoid rust — were repainted within four hours of being stripped.
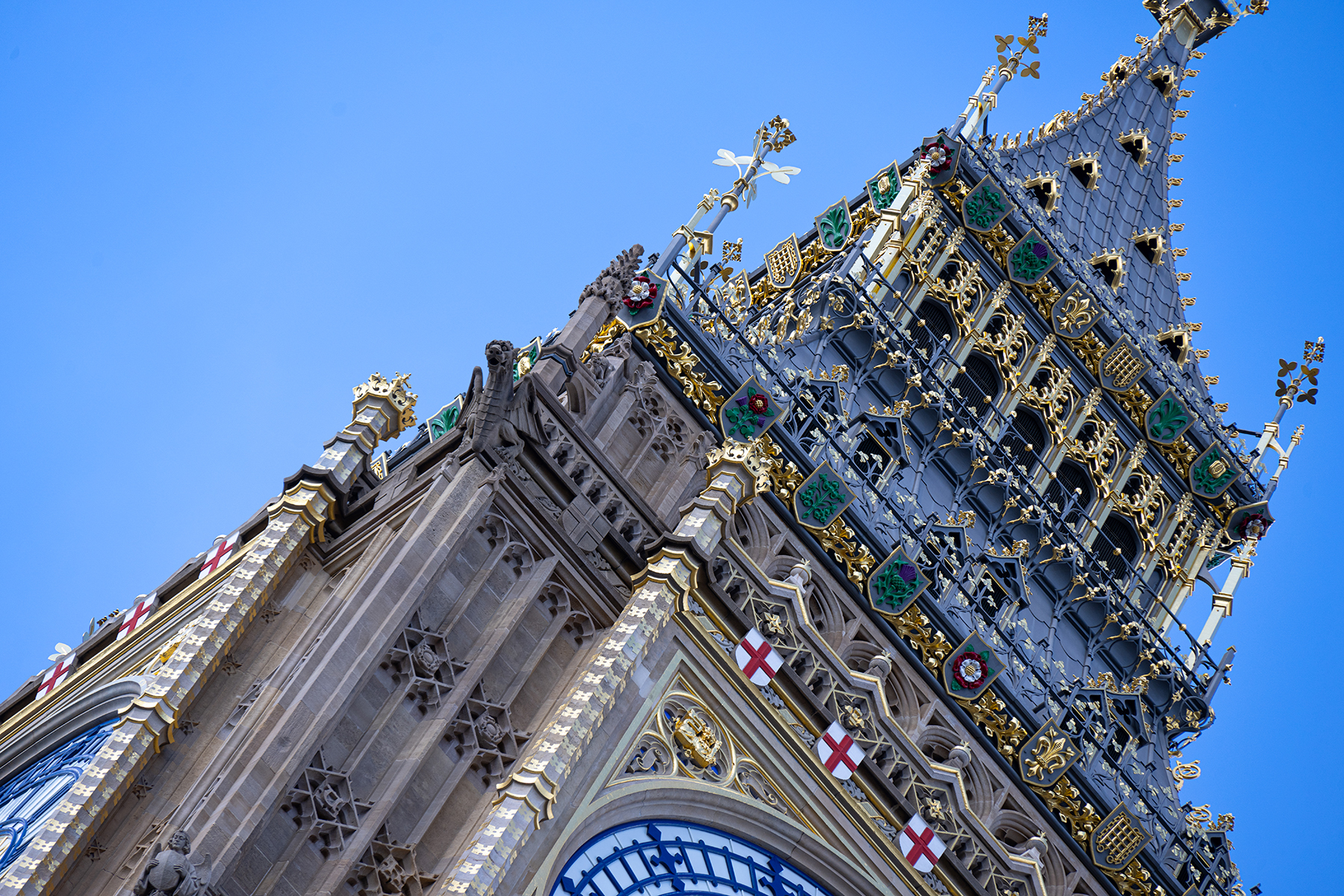
In addition, new stone was needed to replace roughly a thousand pieces of the tower’s limestone cladding that had severely weathered or cracked over the years. This cladding surrounds the tower’s mostly brick-framed structure beneath the clock. But since the Victorian-era quarry that had supplied the original material was no longer in operation, the project team had to find a new quarry that could provide a similar stone, says Matt Penellum, CEng, MIStructE, MICE, a senior structural engineer at AECOM.
The tower also needed a new “crash system” to protect the electrical equipment in an underground level directly beneath the base of the tower in case the heavy cast-iron weights that wind the clock — each weighing a metric ton or more — ever break free and plummet down inside the tower shaft, notes Penellum.
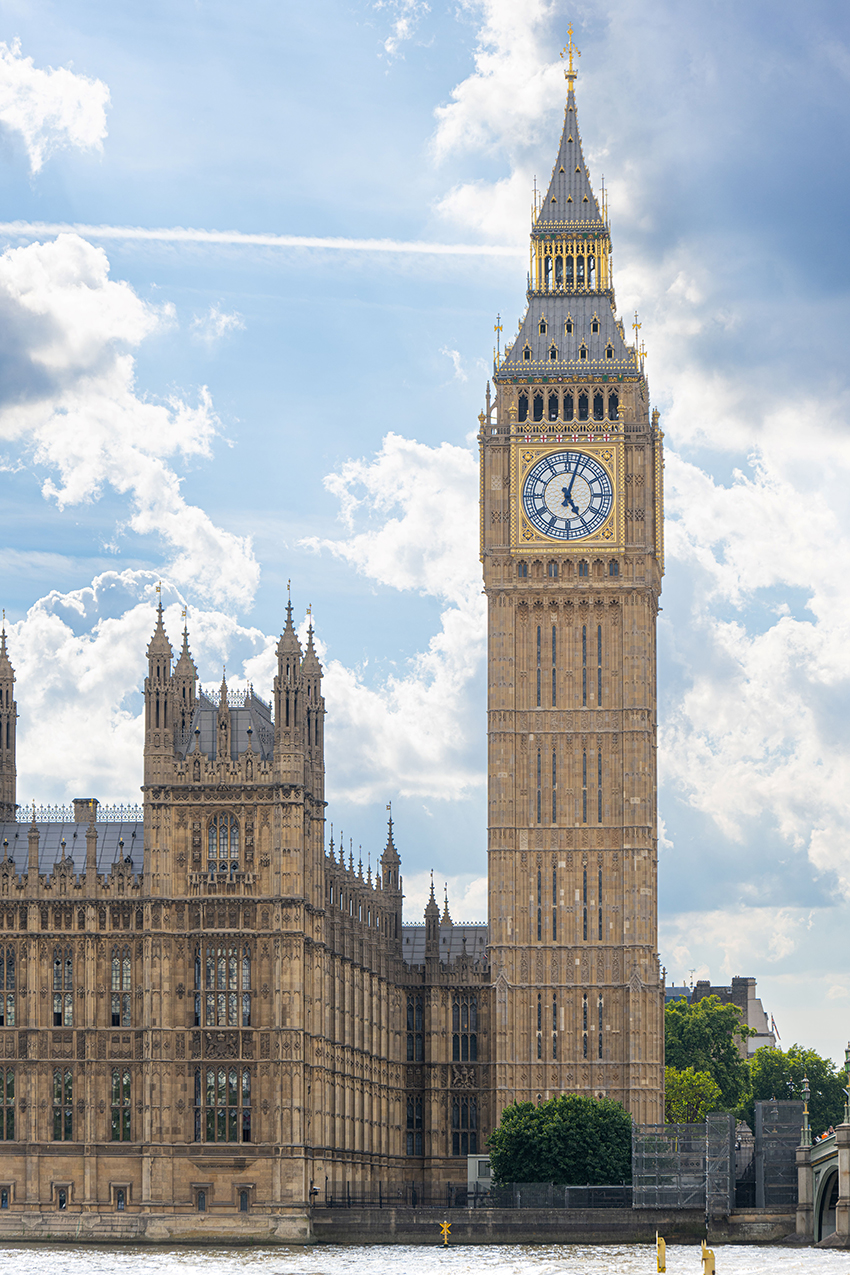
The Victorian-era system of stacking a thick layer of sandbags at the bottom of the shaft to absorb the impact of a potentially falling weight was examined using modern dynamic analysis software and proved inadequate, says Penellum. It was therefore replaced by a system that features two sheets of a plastic polymer designed for impact resistance with a 1 m deep honeycomb of very fine steel between the polymer sheets.
“The idea being that if you hit the top sheet, that will take the initial impact of the weight and then all those honeycombs squash, and in the process of doing that, it absorbs an awful lot of energy and prevents the impact of the weight from getting onto the ground below,” explains Penellum. He adds: “If it’s ever used, it will be totally destroyed in the process, but hopefully it will protect the floor below.”
Undocumented damage and repairs
AECOM provided structural engineering services for the client, Parliament’s In-House Services and Estates team, on the tower project, which cost 80 million pounds (about $99.8 million). London-based Purcell was the architect. Sir Robert McAlpine Ltd., of Hemel Hempstead, England, was the general contractor. S.I. Sealy, of Bredbury, England, was responsible for the mechanical and electrical systems.
The many challenges AECOM faced on the project included a lack of precise documentation regarding earlier repairs conducted during the 1950s and 1980s and limited information about the wartime damage. There were mostly just news accounts from 1941 that the tower had been struck by a falling bomb but few details, says Baker.
As the engineers removed the iron tiles of the roof, however, the extent of the damage became more evident.
Although the news accounts varied, it seemed as if the bomb had struck the tower roof but had not exploded, “which is why the damage to the tower wasn’t worse,” says Penellum. Still, the impact force shattered all the purlins in the southwest corner of the structure and transferred down through the tower into the south clock face, shattering the glass and causing several “significant cracks in the cast-iron metalwork of the clock face,” he explains. The bomb strike also distorted the south clock face, leaving it slightly egg-shaped rather than its original circular form, Penellum adds.
Broken purlins were repaired or recast and replaced, Penellum says, but the engineers decided to leave the damaged clock face as is. They were concerned that if they removed sections of the distorted clock face for repair or replacement, the new parts might not fit back in the existing void.
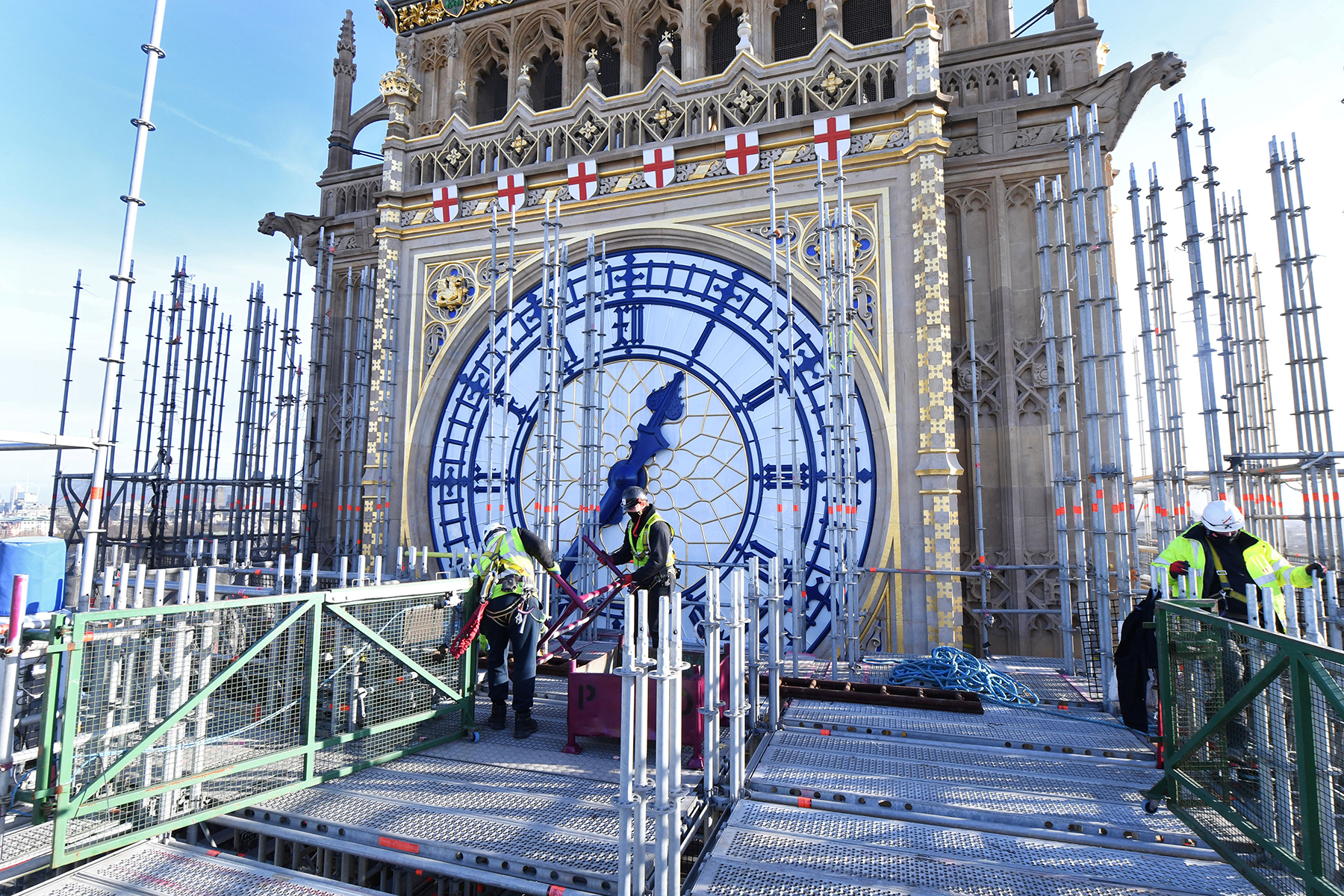
New glazing had been installed in the damaged clock face during the 1950s repairs, Penellum adds, and no further deterioration or other problems had happened since. “So that was a case where our view as conservation engineers was that it was better to keep the original Big Ben clock face rather than to remove some of it and replace it just for the sake of making things look perfect,” Penellum says, adding that “this damage was part of the story of the building.”
Scaffolding and security
The Elizabeth Tower project is just one of a series of refurbishment efforts being undertaken at the Palace of Westminster, the official name for the complex of buildings that houses Parliament and other government offices.
Work on the tower was complicated by its status as a Grade 1 listed building — Historic England’s most highly protected category of structures — and it is surrounded by other equally protected historic buildings, says Penellum. Thus, “when you’re bringing in big construction vans and lifting heavy pieces of steelwork, extreme care was needed so that you didn’t accidentally knock a pinnacle off a nearby tower or something,” he explains.
Moreover, the site’s role as a government complex also involved considerable security concerns. So getting permission to open the gates and drive a van in was not a simple process, nor was getting permission for a massive crane that might lift things over the secure boundary, Penellum says. Likewise, an enormous scaffolding that was erected around the tower during refurbishment work had to be positioned so that it was “not so close to the boundary line that somebody could climb up the fence and get onto the scaffold because that would be an easy route into the palace,” Penellum explains.
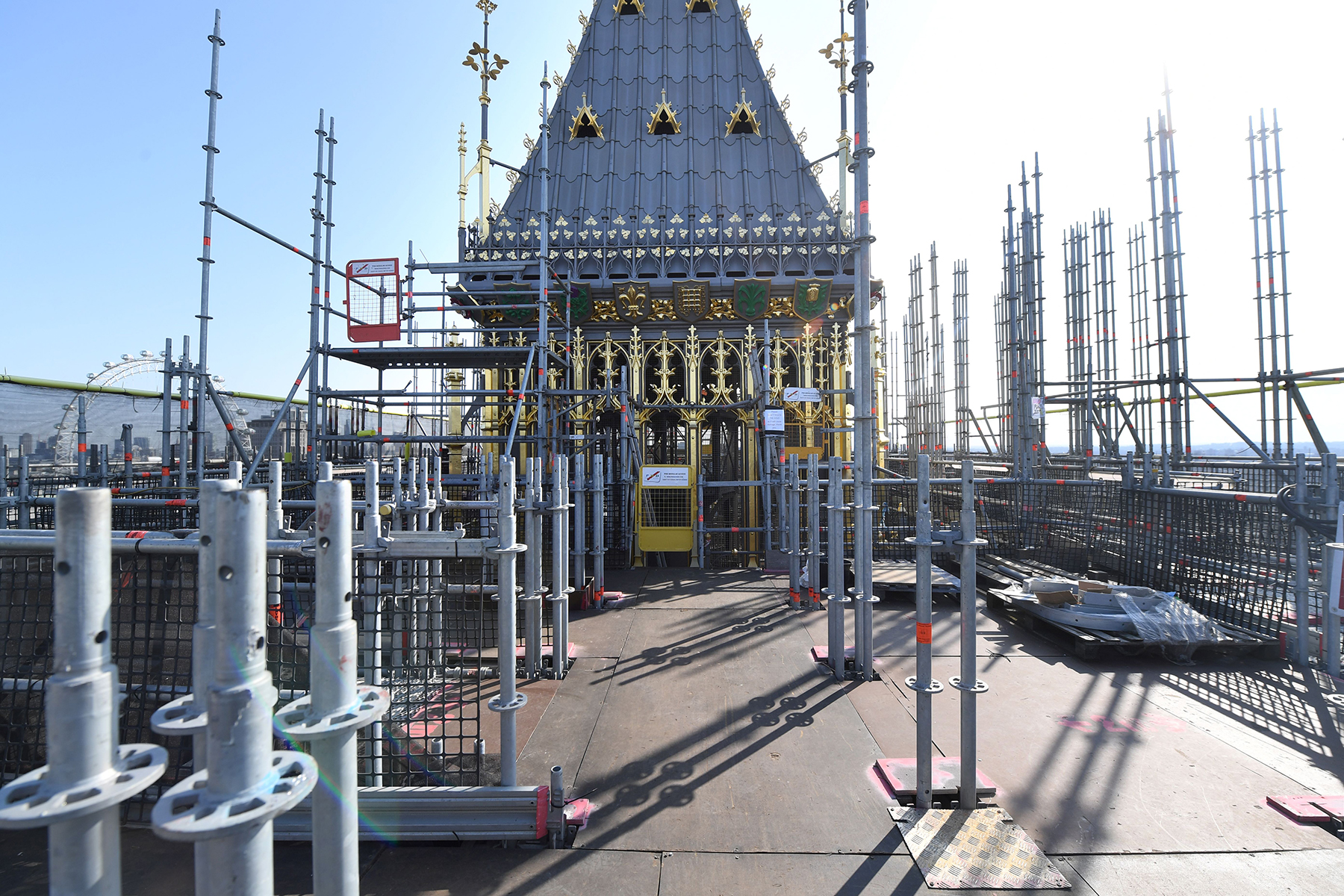
The scaffolding system — for which AECOM prepared the concept design — was one of the most complex aspects of the overall tower project, says David Brown, CEng, FIStructE, MICE, AECOM’s heritage and refurbishment team lead. For one thing, the scaffold could not impose any new load on the tower yet had to follow the tapering form of the tower’s roof. So the system required a complicated series of cantilevering trusses “so you could be directly next to the structure” without fixing any part of the scaffold directly to the tower, Brown says. The scaffold also had to bridge across another building that adjoined the south side of the tower, Brown notes, and the system had to accommodate a series of tunnels and other underground infrastructure beneath the base of the tower.
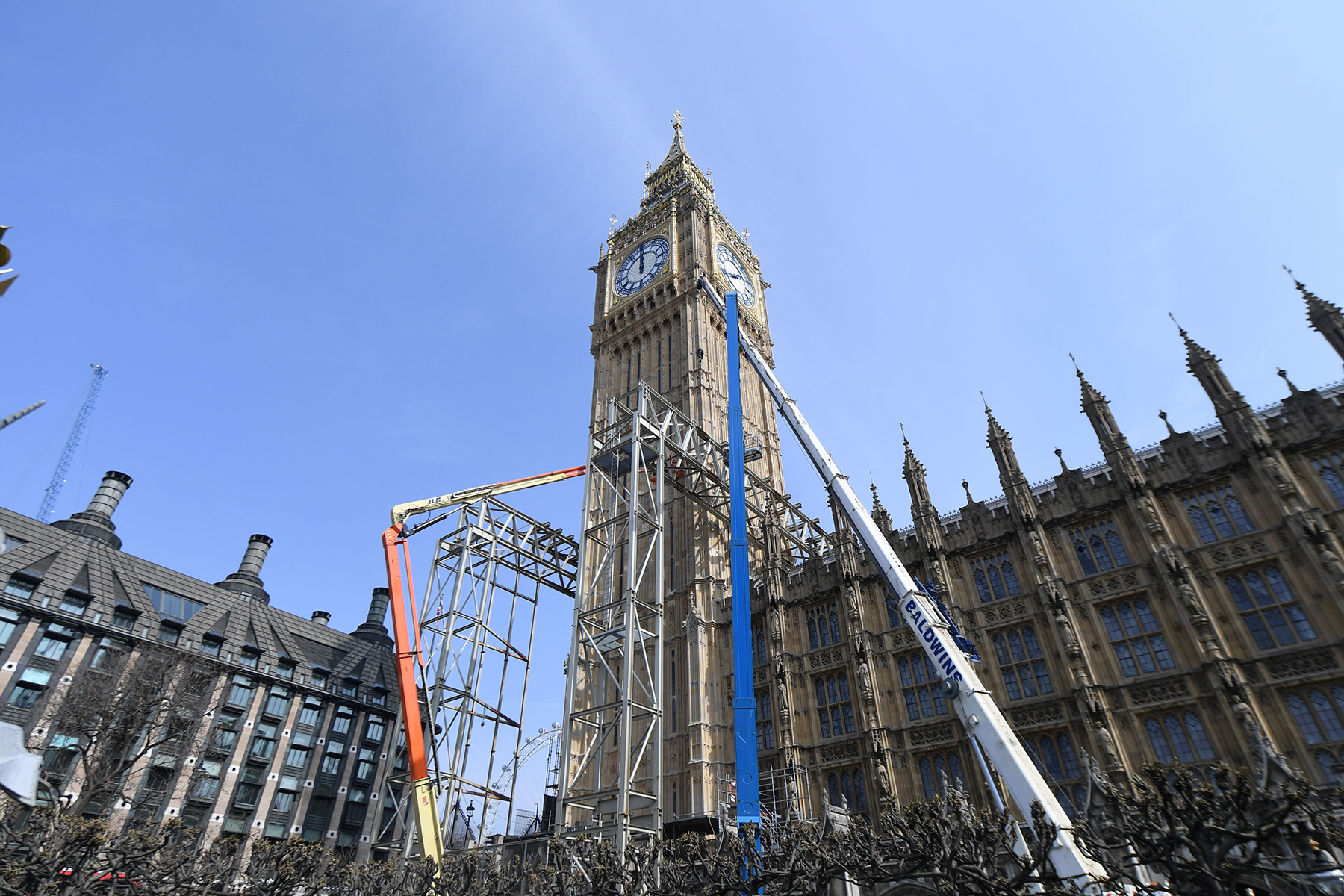
“There were only certain points where we could put in foundation supports” for the scaffold, which consisted of reinforced-concrete piles, Brown explains Then large trusses — roughly 20 m long and several meters deep — were installed to span between the foundation supports. The scaffolding was then erected atop that base of large trusses, Brown says.
Future plans
Because the Elizabeth Tower and Big Ben play such a prominent role in British history, holidays, and other cultural events — from New Year’s to Remembrance Sunday — the engineers involved in the recent refurbishment considered it a once-in-a-career type of project, notes Penellum. And while work on the tower was largely completed late last year, AECOM’s team made sure to keep the future in mind as well.
To that end, the engineers carefully documented “every single repair — via 3D models and scanning and so on and so forth,” says Penellum. The goal was to provide highly detailed information to engineers or other preservationists who might work on the tower 50 or 100 years from now, when the next round of refurbishment might be needed. “We wanted them to be able to see, stone by stone, what we did,” Penellum says.
Work on the refurbishment wrapped up in April.
This article is published by Civil Engineering Online.