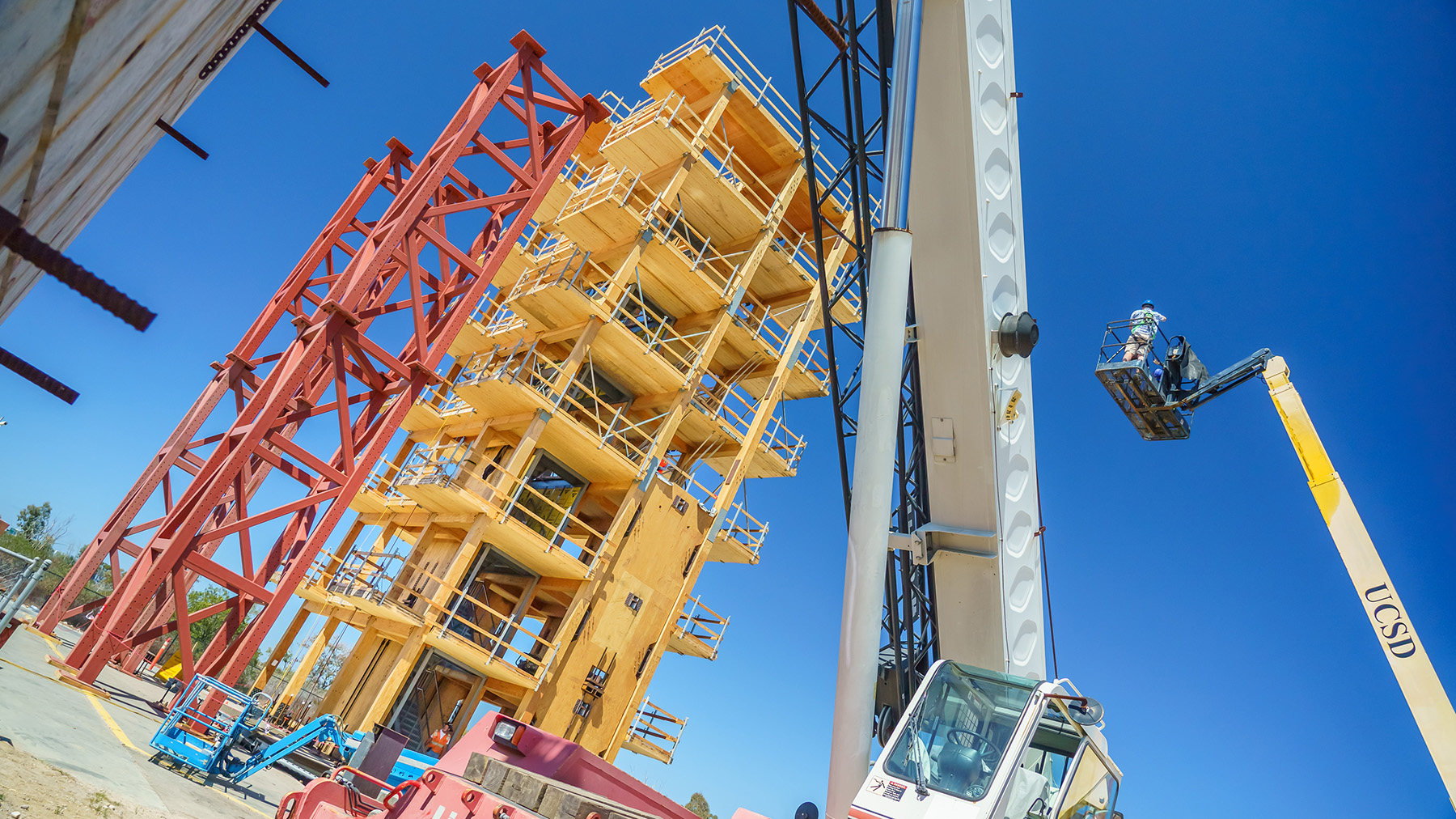
By Kayt Sukel
It is often said: “The bigger they are, the harder they fall.” But the largest full-scale building ever tested on the University of California San Diego’s newly upgraded outdoor shake table remained upright through dozens of earthquake simulations run over several weeks.
The Natural Hazards Engineering Research Infrastructure’s TallWood project is a 10-story building made of cross-laminated mass timber, a load-bearing material composed of thick, compressed layers of wood. Shiling Pei, Ph.D., P.E., F.SEI, M.ASCE, an associate professor of civil and environmental engineering at the Colorado School of Mines and a principal investigator on the project, says the building uses a combination of innovative design elements to resist seismic forces.
“We used a lateral system called a posttension mass timber rocking wall. This design mimics what a concrete or steel rocking wall/frame does, except we are using mass timber panel material,” Pei explains in an interview with Civil Engineering. “If you design the structure correctly, this timber material doesn’t crack or deteriorate. It’s very flexible and can absorb energy fairly elastically, and it’s only one-fifth the weight of concrete.”
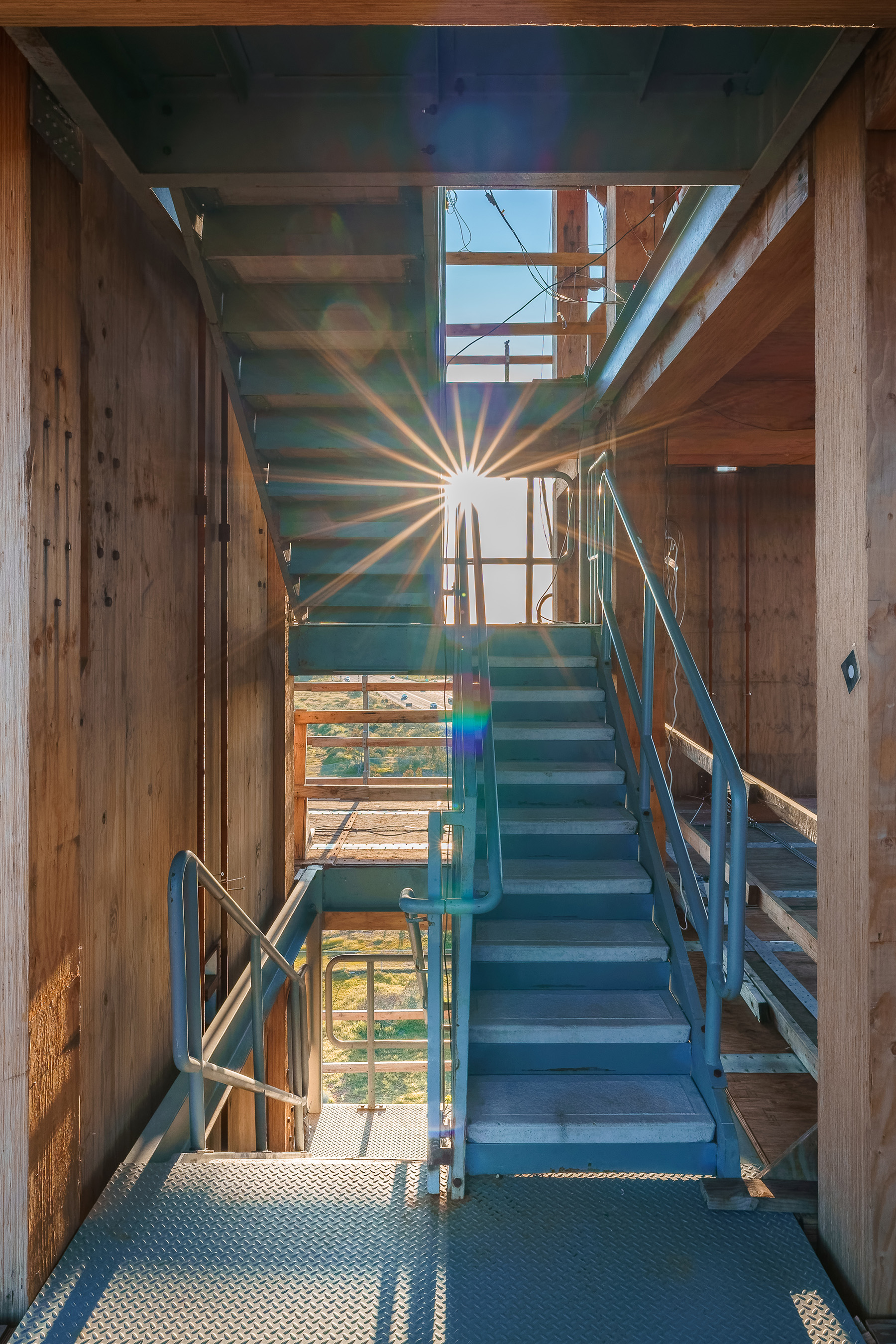
Traditional, code-conforming concrete building frames typically crack in the face of strong seismic forces. However, the NHERI TallWood tower also leverages a so-called low-damage timber-framing system in which the joints can rotate without causing excess stress.
“We designed the gravity framing so the joints could rotate up to 3% drift without causing damage. Well-designed concrete or steel joints can likely tolerate 3% drift without collapse but not without damage,” says Pei.
“In addition, the nonstructural system, which is the face of the building, was specially detailed to allow a certain level of isolation from the main structure. When you put all these things together, the entire building design was targeted for low-damage performance in response to an earthquake,” explains Pei.
“I’ve been conducting wood and seismic research for over two decades,” says Pei. “The interesting thing about wood is that it is very hard to scale it down for testing. You almost always have to do a full-scale test. It’s also more convincing if you can do a full-scale test. And the only place we can do a 10-story, full-scale test of our design is NHERI’s outdoor shake table at UCSD.”
The TallWood project was the first building to be tested on the NHERI Large High-Performance Outdoor Shake Table, known as LHPOST6, since UC San Diego announced in 2019 that the facility would undergo a significant upgrade. The upgrade allows the table to finally move with a full six degrees of freedom.
Joel Conte, Ph.D., P.E., F.EMI, M.ASCE, a professor of structural engineering at UC San Diego and principal investigator for the LHPOST6, says while the shared-use facility was originally designed two decades ago to have multiple actuators to facilitate back and forth, up and down, left to right, yaw, pitch, and roll movements, the original build only allowed back and forth horizontal movement due to costs.
“From the very beginning, we had the idea to have four horizontal actuators in a V-shaped configuration to allow multiple degrees of freedom to reproduce the kind of movement we see on the ground surface in real earthquakes,” Conte notes in an interview with Civil Engineering. “But it was too expensive to build the facility with six degrees of freedom right off the bat. We’ve tried for years to get the funding to do an upgrade, and (we) were finally awarded $16.9 million from the National Science Foundation in 2018.”
The LHPOST6 team includes Conte, other faculty from UC San Diego’s Department of Structural Engineering, and staff from MTS Systems Corp. in Eden Prairie, Minnesota. It took the team approximately a year to design the upgrade and another 2.5 years to construct it. Initially, the team thought it would only need to double the facility’s accumulator bank — the part of the shake table system that pressurizes oil to power the actuators — to reach its design objectives for the facility. The team quickly learned a bit more would be required.
“Once we started to focus on the redesign, we realized we would have to quadruple the size of the accumulator bank. So instead of 2,500 gal. of nitrogen at 3,000 psi to accumulate the necessary amount of pressurized oil to power the table’s actuators, we’d need 10,000 gal. of nitrogen at 3,000 psi,” Conte states. “We also added two new, large pumps and doubled the lines to get the pressurized oil to the horizontal and vertical actuators so we could get the degrees of freedom we wanted.”
Now, according to Conte, “We can test different civil infrastructure systems under more realistic conditions.”
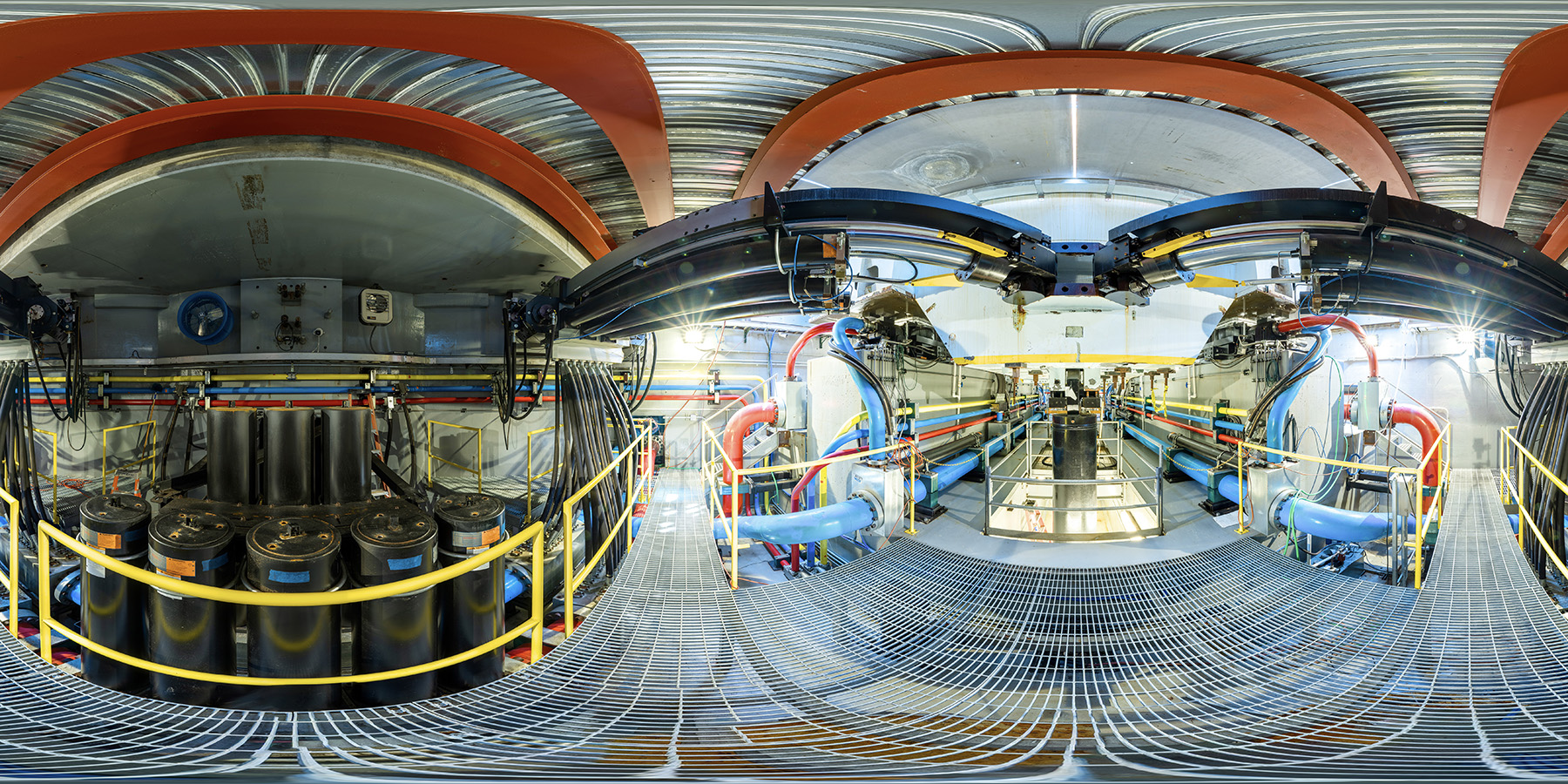
University of California San Diego)
Once the upgrades to LHPOST6 were complete, Pei and his colleagues built the TallWood structure on the facility’s platen. Pei says he was excited to begin full-scale testing. The TallWood team had previously done a test on a two-story tower in 2017 but could only glean so much about how an earthquake might affect the building elements since the platen could only move horizontally.
Finally, on May 9, Pei was able to see the potential movement interactions when the 10-story version of the mass timber tower was tested with not one but two earthquake simulations: a re-creation of the 1994, magnitude 6.7 Northridge earthquake and then a reproduction of the 1999, magnitude 7.7 Taiwan Chi-Chi earthquake. It was the first-ever full-scale test of such a tall structure. The tower remained standing through both tests.
Pei said he was not surprised by the structural performance of the building. “We had numerical models predict the performance before we did this test — and, ballpark, we thought we’d reach about 2% drift. That was about what we saw. So, structurally, it performed well within our expectations,” he says.
“But what surprised us was the nonstructural system. The facade of the building, including the windows, performed very well, and it wasn’t because they didn’t move. We had GoPro cameras looking at the corners of the windows and saw the glass leave the frames. But the (frames) never broke,” according to Pei.
In the weeks since the initial shake tests, the researchers have continued to assess the tower’s performance in response to different types of earthquakes.
“We’ve now run more than 100 earthquakes on TallWood,” says Conte, speaking at the end of May. “It’s still standing.”
Pei, for his part, is looking forward to diving into the data provided by the shake table testing, and he hopes that the results will convince others that a mass timber building can be a “viable and high-performance” option for high-seismic regions.
Beyond the TallWood project, Conte said he is looking forward to collaborating with other researchers and industry partners to run more tests, and he is hopeful that shake table tests, in concert with computer modeling and simulation, will help improve the design of vital civil infrastructure to withstand the earthquakes of the future.
This article was first published by Civil Engineering Online as “Behind the scenes of the TallWood shake table test at UC San Diego.” It appeared in the September/October 2023 print issue of Civil Engineering as “Shake It Up.”