By Ian Moran, A.M.ASCE, Justin Rak-Banville, P.Eng, M.ASCE, and Charles Goss, Ph.D.
Most people take for granted waking up in the morning and pouring a glass of clean water. However, for the population of 9,000 people in Iqaluit — the remote northern capital city of the Canadian territory Nunavut — the smell and taste of fuel in the water became an unfortunate reality.
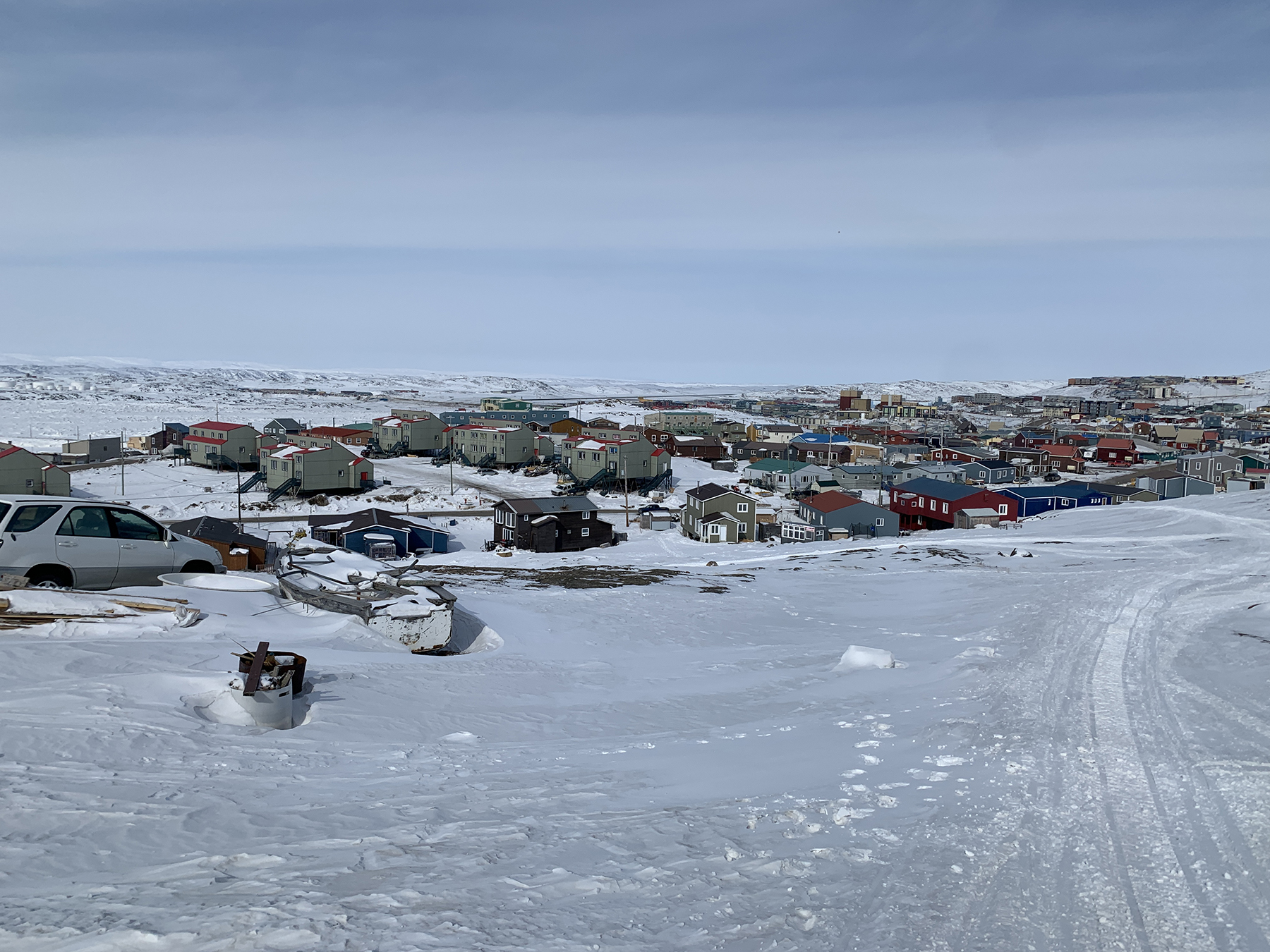
In October 2021, the city of Iqaluit and the Nunavut government declared a state of emergency after visible fuel contamination was discovered in one of the treated water tanks in the city’s 62-year-old water treatment plant. In tandem with hundreds of consumer complaints, the government quickly issued a “do not consume” water advisory.
The city is so remote that it is only accessible by air in the winter months. Area stores sold out of bottled water immediately, citizens began gathering water from a local river, and the Nunavut government began flying in planeloads of bottled water from Ottawa — 1,296 mi away. On top of this, the Canadian Armed Forces were deployed to Iqaluit to set up a temporary water purification system.
Visible contamination was first discovered in the north clearwell, the second of four in-series below-ground treated water tanks. Approximately 52,000 mg/L of petroleum hydrocarbons were measured on the surface of the tank, while the surrounding tanks contained concentrations less than 1 mg/L. Naturally, the first response was to valve off the tank, bypass it, drain it, and inspect it for a contamination entry point. However, the inspection revealed that the tank was in immaculate condition.
How was contamination getting in?
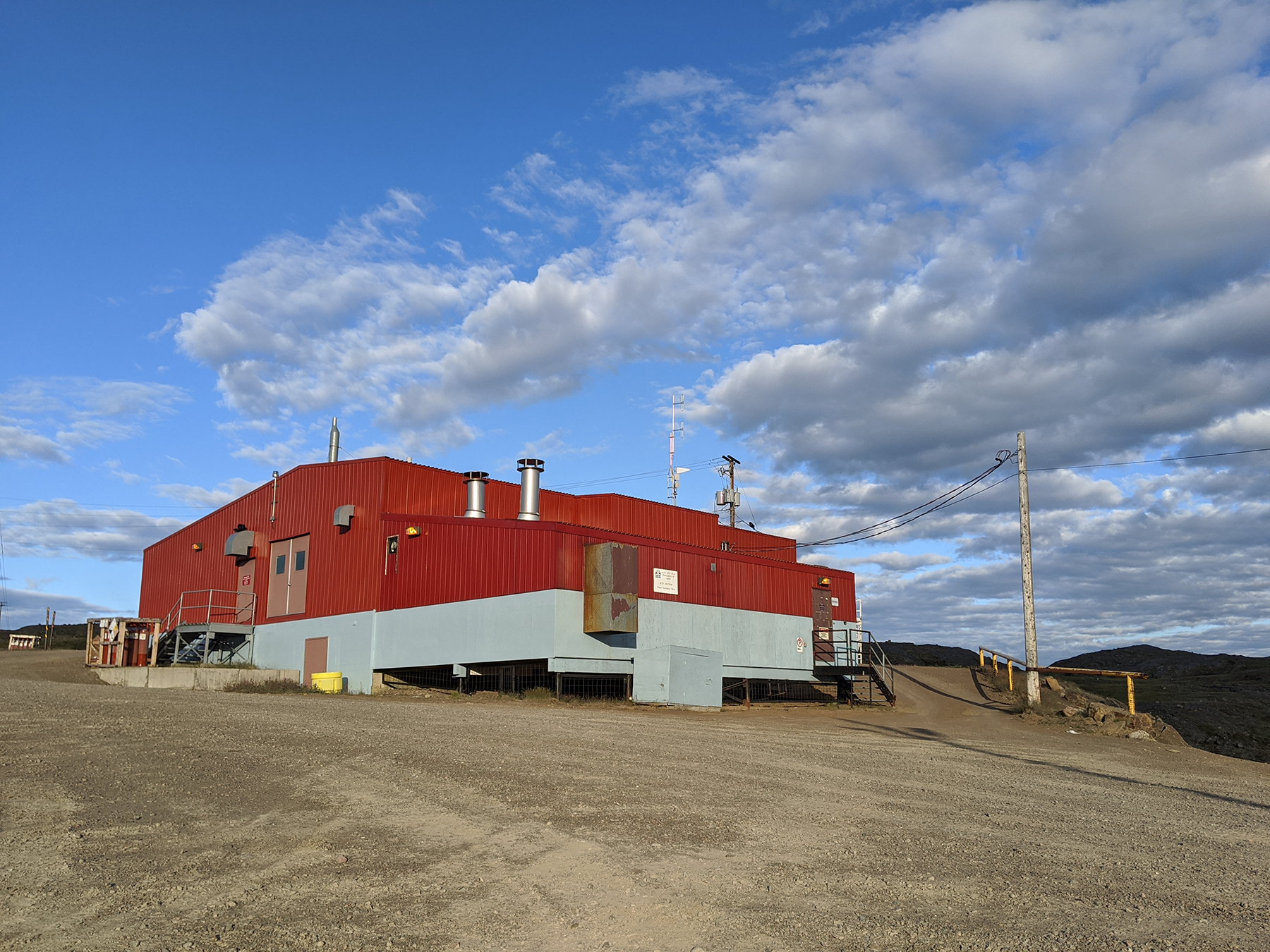
Discovering the ‘void’
The city engaged global engineering firm WSP to identify the source of the contamination, address it, and provide necessary engineering support throughout the water crisis. WSP’s Emergency Ready Team was led by project manager Justin Rak-Banville, P.Eng, who was primarily responsible for managing the complex stakeholder landscape and the many on-site contractor activities. Rak-Banville’s role was crucial in actively restoring consumer confidence in the water utility. Professional chemist Charles Goss, Ph.D., was primarily responsible for installing and calibrating an innovative real-time hydrocarbon monitoring system to actively monitor the water leaving the treatment plant. Engineer-in-training Ian Moran, A.M.ASCE, was primarily responsible for the on-the-ground investigation efforts.
During the investigation, the WSP team discovered an unusual cavelike structure beneath the water treatment plant. This space was very difficult to access, did not appear on any recent engineering drawings, and was unknown to city staff. The space was flooded with contaminated water and featured tight corridors and sections with very limited headroom.
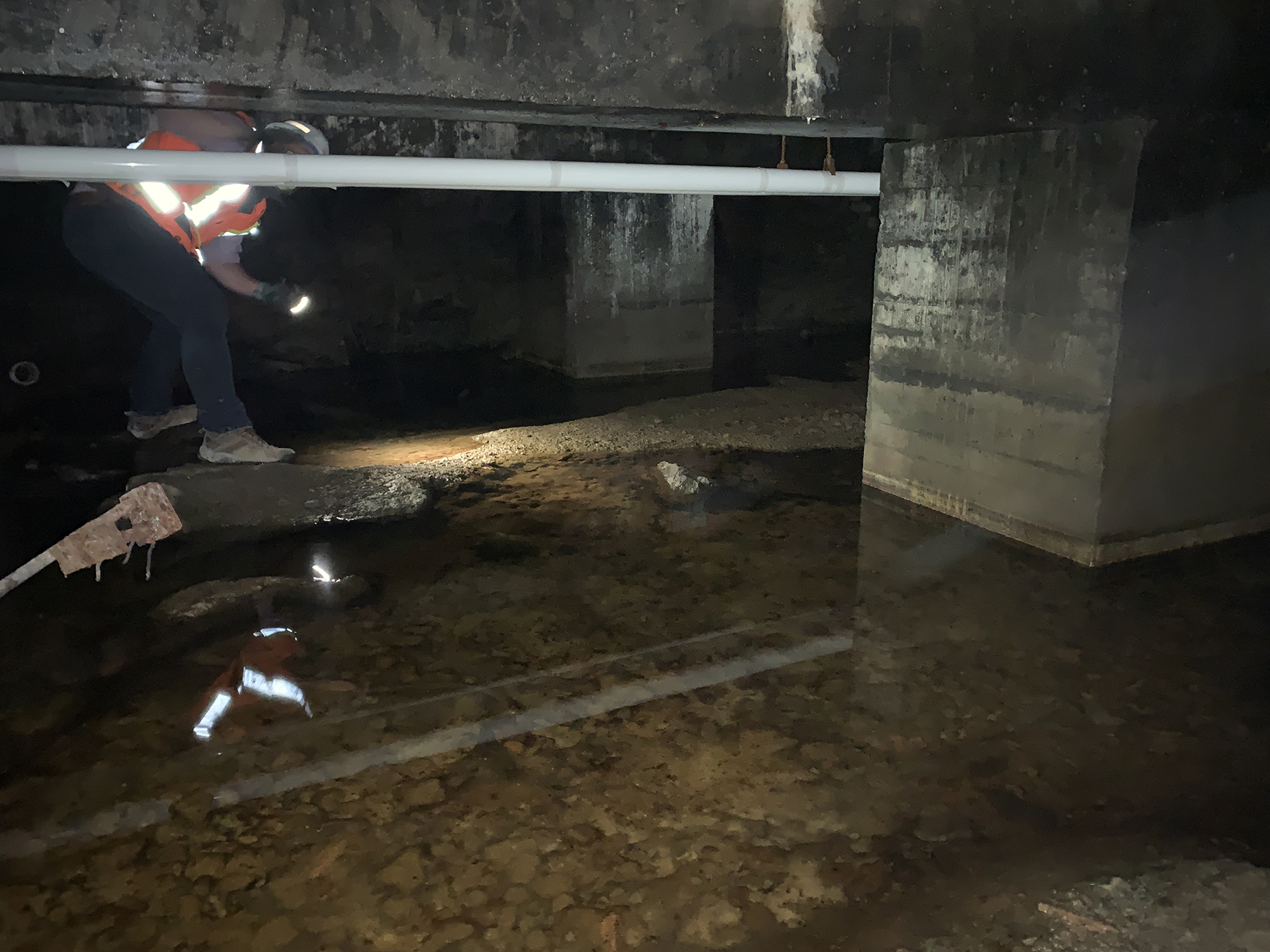
Dubbed the “void,” the space was determined to be essentially the air gap between the water treatment plant and the surrounding bedrock. Picture a cube sitting in a rounded bowl. In the deepest reaches of the void, the team discovered a historical underground fuel storage tank with congealed oil dripping from its underside and contamination pooling across the bottom of the void.
Assessing potential contaminants
Meanwhile, WSP had just completed calibrating the city’s hydrocarbon monitoring system, a spectrophotometer-based instrument known as the s::can that was supplied by Aquatic Life Ltd. The system produced results in real time, which was a vast improvement to the one-week return time on samples that previously had to be sent to southern Canada. Additionally, the system could run field samples and generate unique “fingerprints.” In other words, a sample of the contaminated liquid in the void could be readily compared to on-site fuel products for a potential match.
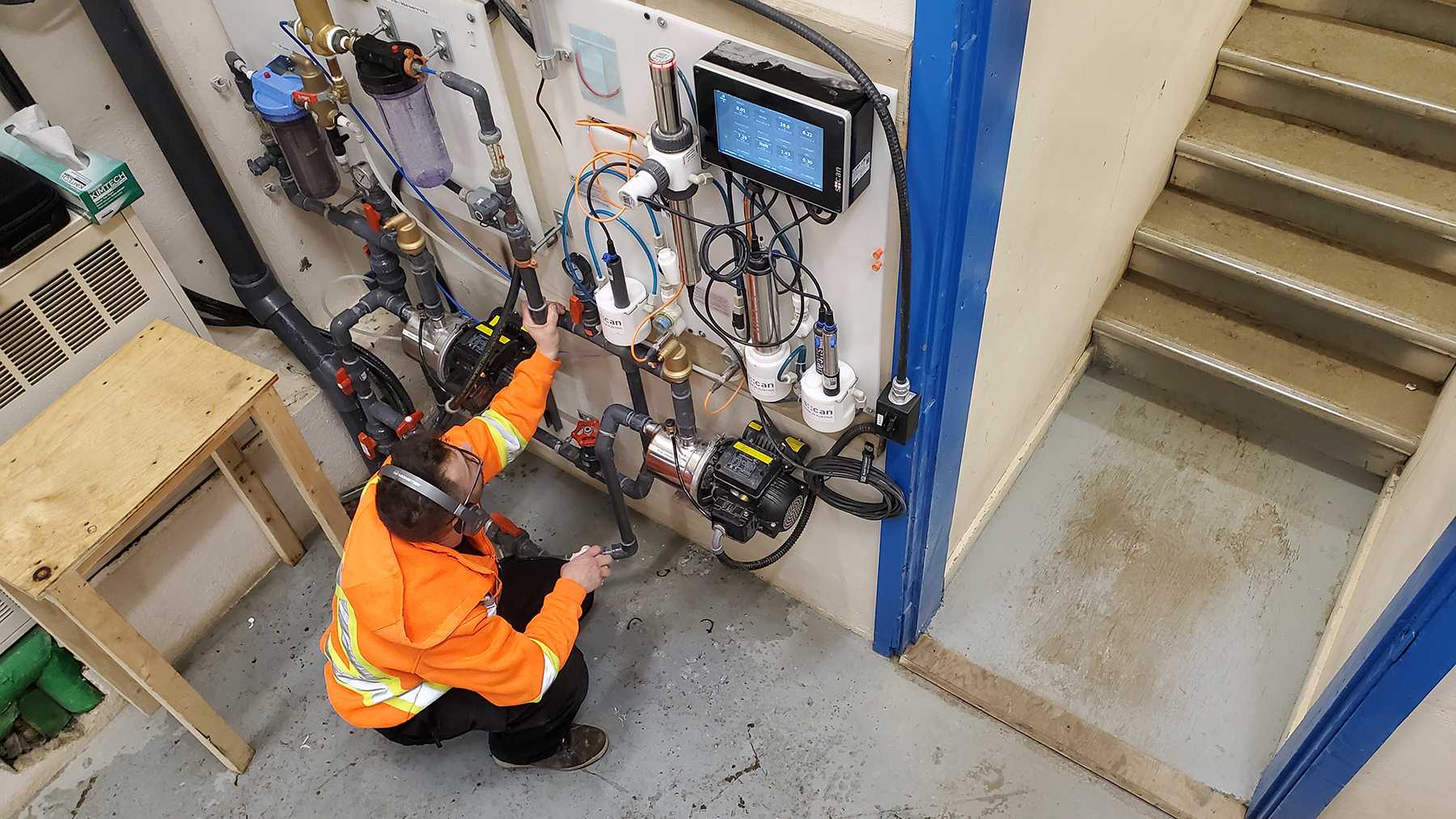
As part of the territorial government’s requirements for lifting the do not consume advisory, the contamination source and contamination pathway needed to be determined. The WSP team exhaustively assessed all known potential sources of contamination and the pathways that each contaminant could take to ultimately accumulate in the system’s north clearwell. This included the oil-saturated underground fuel storage tank and other more common sources, such as pump lubricants and fuel products from the building’s heating system. After all other sources had been reasonably disproved, the underground fuel storage tank remained the most likely, and singular, source.
Proving how the contamination entered the north clearwell was no easy task. The underground fuel storage tank was from the 1960s. No information existed about the tank or what kind of fuel it had stored. Samples directly from the underground tank revealed a wide spectrum of hydrocarbons, including light fractions and heavy fractions. Samples taken from the liquid at the bottom of the void were exclusively heavy fractions. But what happened to the lighter fractions?
Solving the mystery
The water treatment plant was, effectively, a full-scale distillation column.
The lighter hydrocarbon fractions entered the treatment facility by wicking through the porous concrete of a raw water storage tank used in the early stages of the treatment process. After traveling through several rapid-mix tanks, the light hydrocarbons finally settled in the very slow-moving north clearwell. Because lighter hydrocarbons float on water and the interconnecting pipes are at the bottom of the tanks, the hydrocarbons got caught on the surface of the north clearwell and did not readily pass into the downstream tanks or distribution system.
The WSP team combined the fingerprints of the lighter hydrocarbons on the surface of the north clearwell with the heavy hydrocarbons at the bottom of the void. The combined fingerprint was a strong match for the raw contents of the underground tank.
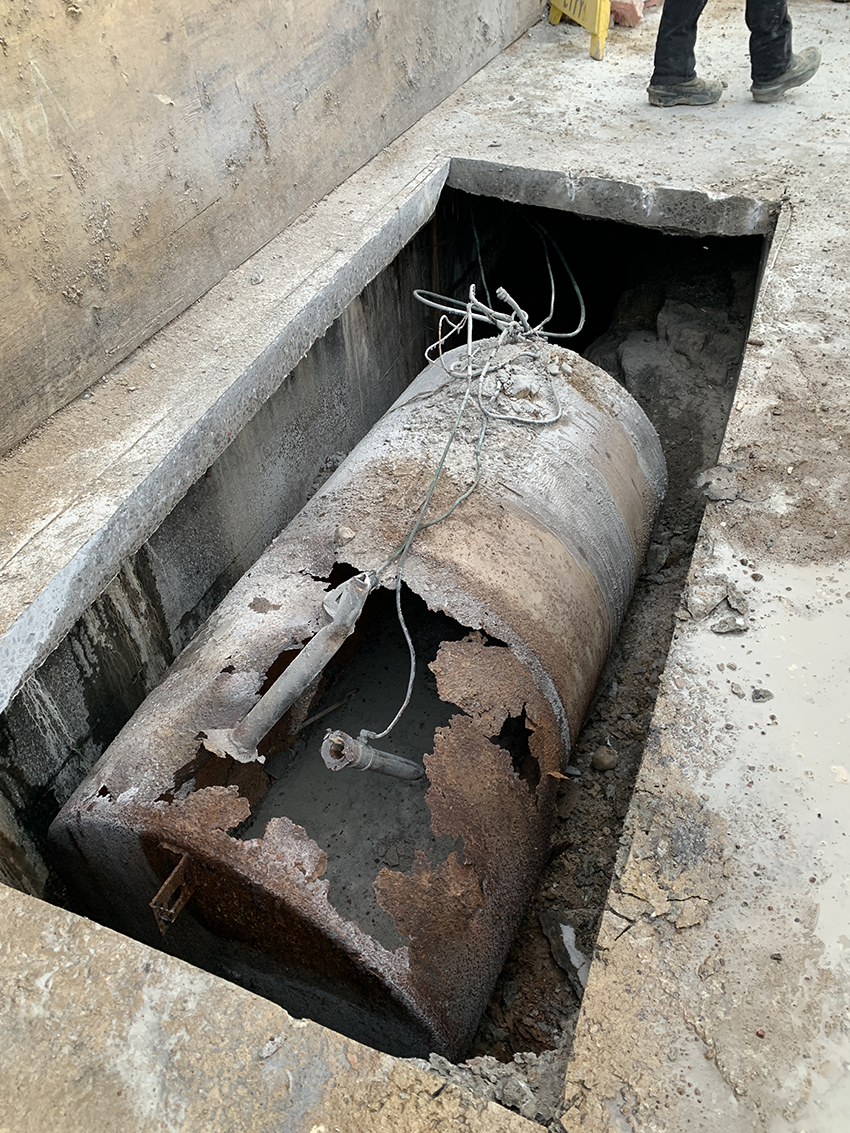
The water treatment plant underwent multiple critical upgrades, including installation of a bypass system, removal of the underground fuel storage tank, and intensive cleaning of the void. After rigorous water quality testing, the do not consume advisory was lifted. The Canadian Armed Forces were reassigned to fight forest fires in British Columbia, and the city reopened its recreational facilities.
Unexpectedly, the system remained hydrocarbon-free for just three months. Once again, the smell and taste of fuel in the water became an unfortunate reality.
A second investigation
The second event was significantly different from the first incident. This time, the city was equipped with a hydrocarbon monitoring system, an updated emergency response plan, and the resources to address the matter quickly and efficiently. Another major difference was the exclusive presence of heavier hydrocarbons in this round of contamination, rather than the lighter hydrocarbons found months earlier.
Until this new source of contamination was identified and addressed, the water treatment plant bypass system was initiated. The bypass system conveyed disinfected and screened water directly to the distribution system.
The WSP Emergency Ready Team was on the first flight to Iqaluit and included subject matter experts from all corners of the country. The system was reassessed from start to finish, and every inch of the below-ground tanks was investigated for new or notable concerns.
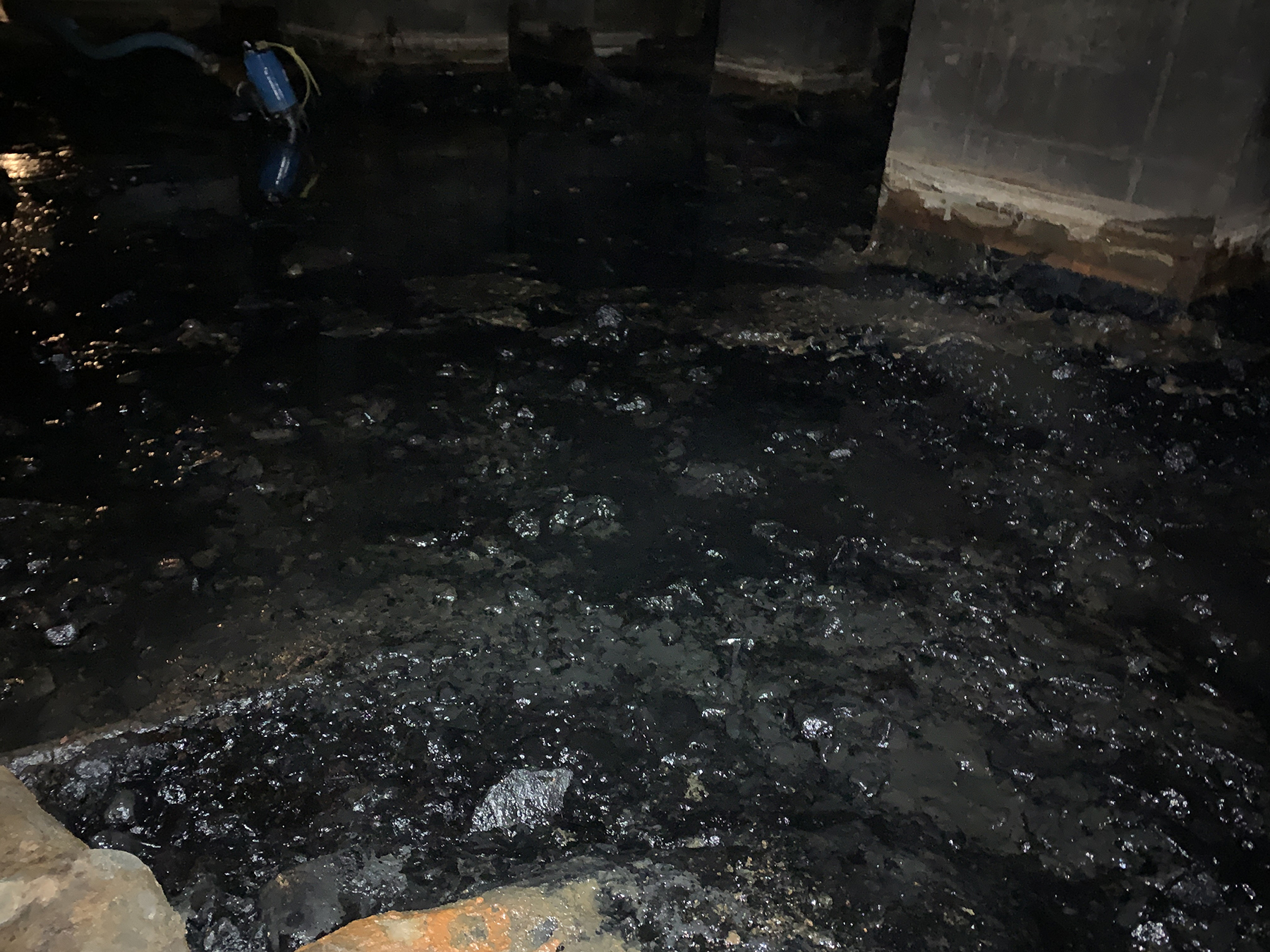

Another source of contamination
During the investigation, a black tarlike substance was found protruding from some of the treated water tank walls. A sample of the substance, which had not been observed during the previous tank inspection, was run through the s::can and found to have a nearly identical fingerprint to the contaminated water. With this new contamination source confirmed, attention turned to what this product was and why it was there.
The answers were found in historical construction records and grainy, age-worn photographs. The tarlike substance was a water stop product with heavy hydrocarbons as a compositional ingredient. Commonly installed in construction joints, these products expand when wet to prevent the movement of water. When embedded deep enough in concrete, this expansion presents no problems. However, if the concrete cover is insufficient to retain the expansion, the water stop can burst out of the wall.
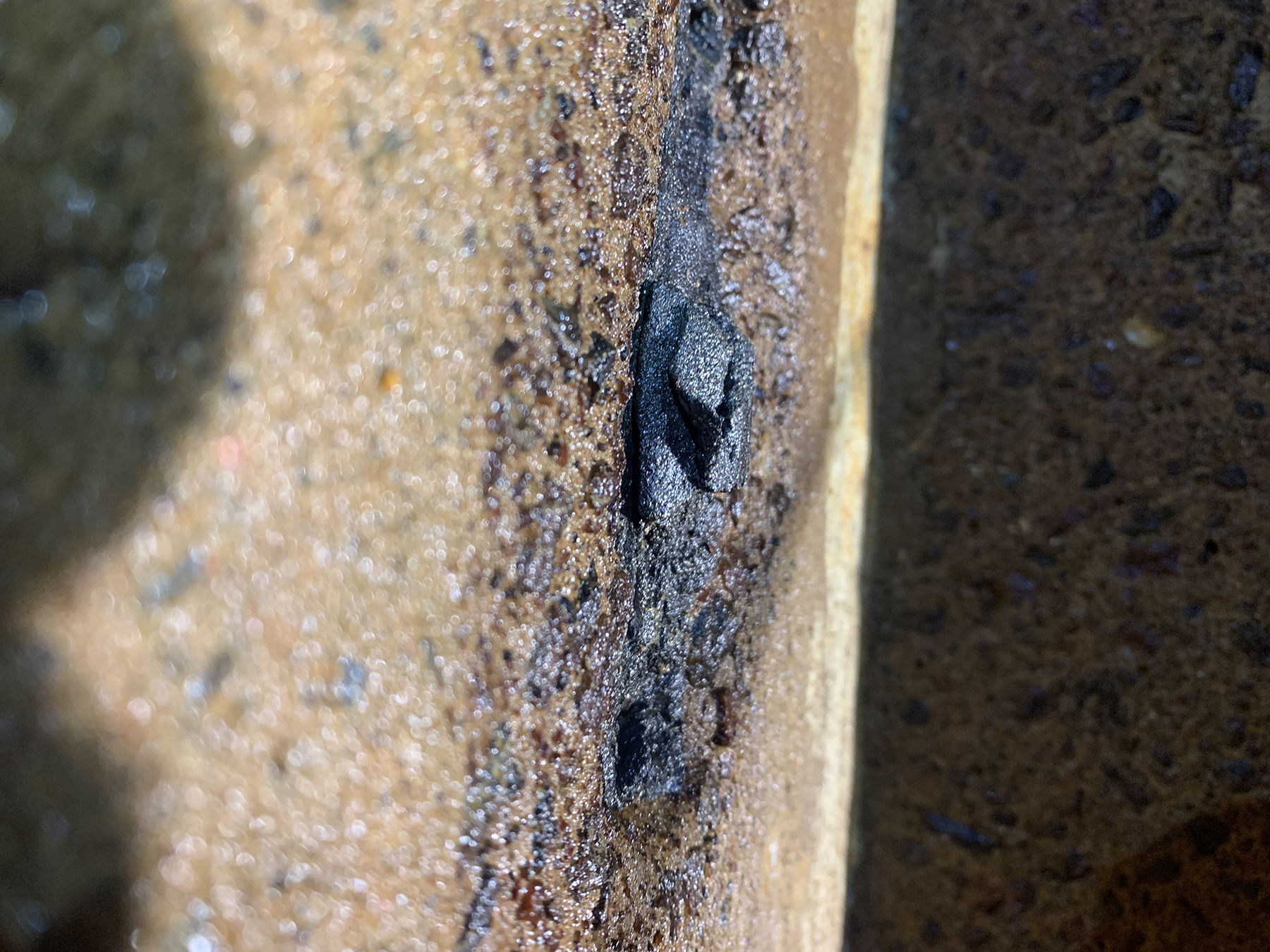
As it turns out, only a thin layer of grout had been used to embed the water stop product in the tank. The frequent modifications made to keep the system online during the October event, including tank bypassing, draining, and flow rerouting, increased tank turbulence. In turn, this turbulence is believed to have caused one portion of the water stop to expand. This expansion likely triggered a chain reaction along the same joint, causing several sections to burst out of the tank wall.
WSP worked with the city to return the tanks to service. All remaining water stop product was chiseled out, the concrete was patched as needed, and a chemical waterproofing mortar was applied to all floors and walls to keep future contaminants from entering the tank. After the repairs were complete, WSP’s subject matter experts confirmed that the venerable water treatment plant should remain fit for service for years to come, and the facility was successfully returned to full operation.
Restoring consumer confidence
A critical component of the project involved restoring severely eroded consumer confidence. Consumers were informed not only of one fuel contamination incident but also of a second separate contamination event only a few months later. On top of that, consumers had to endure almost two full months under the do not consume advisory.
WSP worked with the city to draft public service announcements and deliver several simplified technical presentations to the mayor, city council, and national news media outlets. The city posted water quality information on its website on a regular basis and provided residents with access to a water quality hotline and an abundance of additional resources on health risks and the public water system. Successes in restoring consumer confidence were realized through frequent engagement with local public health officials and Health Canada. This project has been recognized by engineering and water sector associations for its forward-thinking approach to public engagement.
Although fuel contamination of a water system is a substantial event, it is important to note that the petroleum hydrocarbons that passed into the Iqaluit distribution system did not reach any concentration that would be concerning to any consumer, whether that consumer was an adult or a child. The efforts of the city and the WSP team likely prevented a much more serious situation.
Ian Moran, A.M.ASCE, is an engineer-in-training, Justin Rak-Banville, P.Eng, is the director of water and wastewater for western Canada, and Charles Goss, Ph.D., is the water team lead for global engineering firm WSP.
Project Credits
Owner: City of Iqaluit, Nunavut, Canada
Engineer: WSP
This article is published by Civil Engineering Online.