By Kurt Chirbas, P.E., Paul Mallory, and Marc Gravel
The San Diego County Water Authority recently rehabilitated sections of three large-diameter concrete tunnels within its aging First Aqueduct water conveyance system. Because the critical aqueduct could only be shut down for repairs for a limited time, traditional rehabilitation methods were not possible.
Instead, the design-build team hired by the Water Authority used an innovative combination of two methods — sprayed-in-place geopolymer mortar to reline the pipes and sliplining using fiberglass-reinforced polymer mortar pipe — to rehabilitate sections of the tunnels within the available 240-hour time frame.
Infiltration identified
Established in 1944, the Water Authority provides water to six cities, 17 special districts, and the Marine Corps Base Camp Pendleton.
The First Aqueduct water conveyance system extends from just south of the border between Riverside County and San Diego County to San Vicente Reservoir near the census-designated area known as Lakeside. This system of trenched pipes and tunnels currently conveys treated water to 11 entities that serve roughly 727,000 of the 3.3 million residents served by the Water Authority. (The First Aqueduct is also part of the Water Authority’s integrated water delivery system and in an emergency can be configured to serve the authority’s entire service area.)
During inspections in 2019 and 2020, the Water Authority identified groundwater infiltration in three 72 in. diameter sections of the tunnels in the First Aqueduct system built in 1947. A 500 ft long section of Lilac Tunnel had minor infiltration and no structural concerns. A 3,100 ft long section of Red Mountain Tunnel had moderate infiltration with no signs of structural degradation. Finally, a 3,600 ft long section of Oat Hills Tunnel had significantly more infiltration and moderate signs of structural degradation.
Addressing infiltration is crucial as it can adversely affect water quality and structural integrity. The traditional method of rehabilitation for tunnels of this size involves sliplining with split-casing steel pipe. The approach involves carrying, expanding, and positioning individual sections of steel into the existing tunnel and then completing a full circumferential and longitudinal weld on each section. Following the lengthy welding process, the interior surface of the steel pipe is prepared and coated with epoxy.
Absent viable alternatives for providing treated water to customers, the Water Authority determined the aqueduct could only be shut down for repairs during three periods of 10 days (240 hours) in the cooler winter months, based on downstream reservoir capacity and minimum fire reserve quantities.
The constraints provided were far too restrictive for traditional rehabilitation methods.
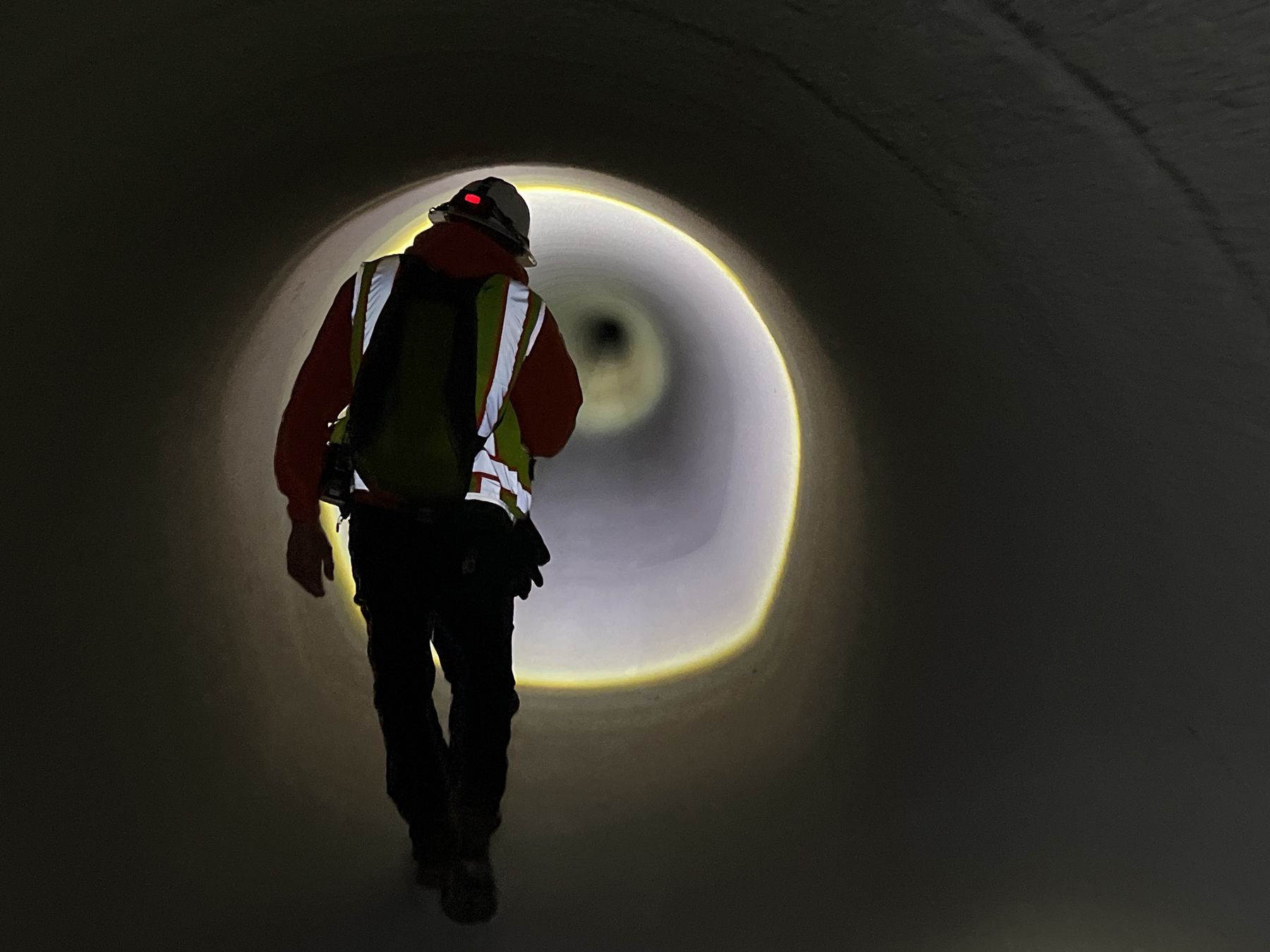
Winning proposal
The Water Authority used the design-build project delivery model to engage the water rehabilitation industry for viable solutions for adding 75 years of design life to the rehabilitated tunnel sections.
Two teams were prequalified to submit proposals. The winning proposal was submitted by Michels Trenchless Inc. in partnership with the design consulting firm Stantec. Trenchless construction and rehabilitation of challenging projects is one of the services for which Michels Trenchless, a member of the Michels Family of Companies, is most accomplished in the water and wastewater, energy, and renewable energy markets.
The team developed a solution using a sprayed-in-place geopolymer lining on the sections of the Lilac and Red Mountain tunnels. Use of a sprayed-in-place geopolymer material that complies with the NSF/ANSI/CAN-61 standard for potable water, titled Drinking Water System Components - Health Effects and developed by NSF (formerly the National Sanitation Foundation) and the American National Standards Institute, are starting to be more commonly used for rehabilitation of large-diameter potable waterlines. This is based on improved performance parameters compared with the traditional sliplining approach of the past.
The contractor leveraged its experience with sprayed-in-place materials, specifically with the GeoSpray 61 geopolymer mortar product from GeoTree Solutions, a subsidiary of Critica Infrastructure. GeoSpray 61 met the strict NSF-61 standards for rehabilitating potable water pipes and would enable the application of a thinner thickness than other products based on flexure strength.
For the section of the Oat Hills Tunnel, the team opted to install FRPM pipe by means of sliplining and annulus grouting, providing the structural integrity to withstand the rock load should the original tunnel fail. Additionally, the selected product has a design life of approximately 100 years, exceeding project goals.
Good candidates for geopolymer lining
Because their locations within the mountain range limited access to their pipes, the 500 ft long Lilac Tunnel section and the 3,100 ft long Red Mountain Tunnel section made good candidates for centrifugally applied geopolymer lining.
Geopolymer lining offers significant technical advantages, including expanding the life span of each tunnel by more than 75 years, creating a watertight seal without needing to bond to the substrate, and improving structural integrity by withstanding external pressures from groundwater of up to 90 ft of head.
The project team chose GeoSpray 61 for a range of reasons, such as the need to comply with the requirements of NSF/ANSI/CAN-61 for drinking water contact. Other reasons included the physical properties of the material, including its 1,500 psi flexural strength, its fast-setting and curing ability, and its ability to self-bond without cold joints when multiple layers are applied.
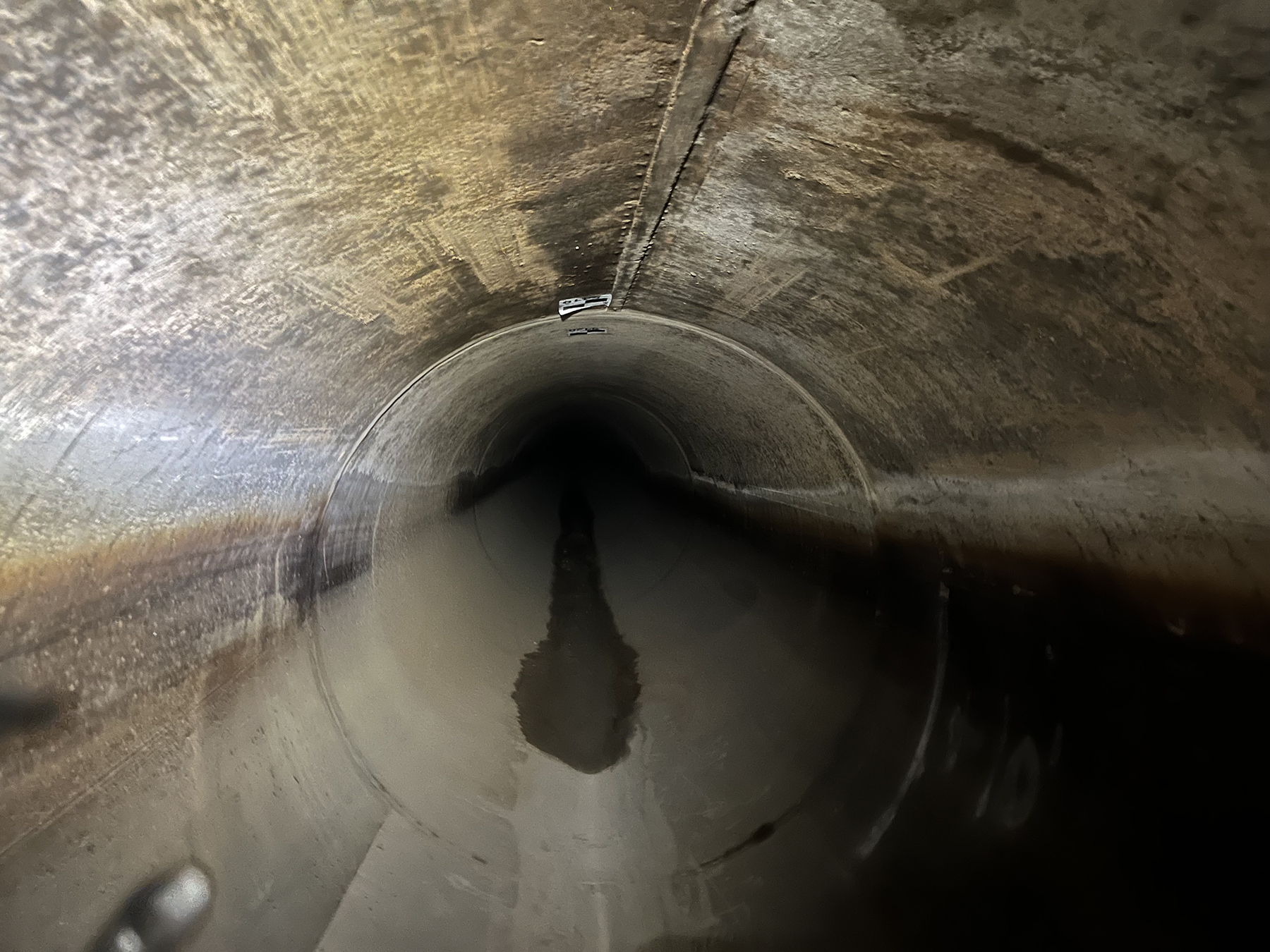
Installing the lining
An installation process specifically designed to apply geopolymer lining as part of the First Aqueduct project minimized the amount of downtime needed for installation. The GeoSpray 61 was applied using Michels Trenchless’ proprietary centrifugal application devices that were specifically designed for the 72 in. diameter Lilac and Red Mountain tunnels.
For the Lilac Tunnel alignment, the material was pumped approximately 750 ft to the application device. The material was applied as the application device was retracted at the calculated speed. The total thickness of 1.5 in. was applied in two passes, each 0.75 in. For the Red Mountain Tunnel, the material was mixed topside, loaded into specially designed diesel conveyance carts, and delivered to the application device for installation.
During the first shutdown, the Lilac Tunnel rehabilitation was completed along with full grouting of the leaks in the Red Mountain Tunnel. All work on the Red Mountain Tunnel was performed from two temporary access portal locations. The first half of the geopolymer application on the Red Mountain Tunnel was completed during the second shutdown and the second half was completed in the early portions of the third shutdown.
Following the geopolymer applications, the Lilac and Red Mountain tunnel sections were completed and released back to the Water Authority on schedule. In total, more than 1 million lb of geopolymer liner was installed in approximately 3,600 ft of tunnel during the three shutdown periods.
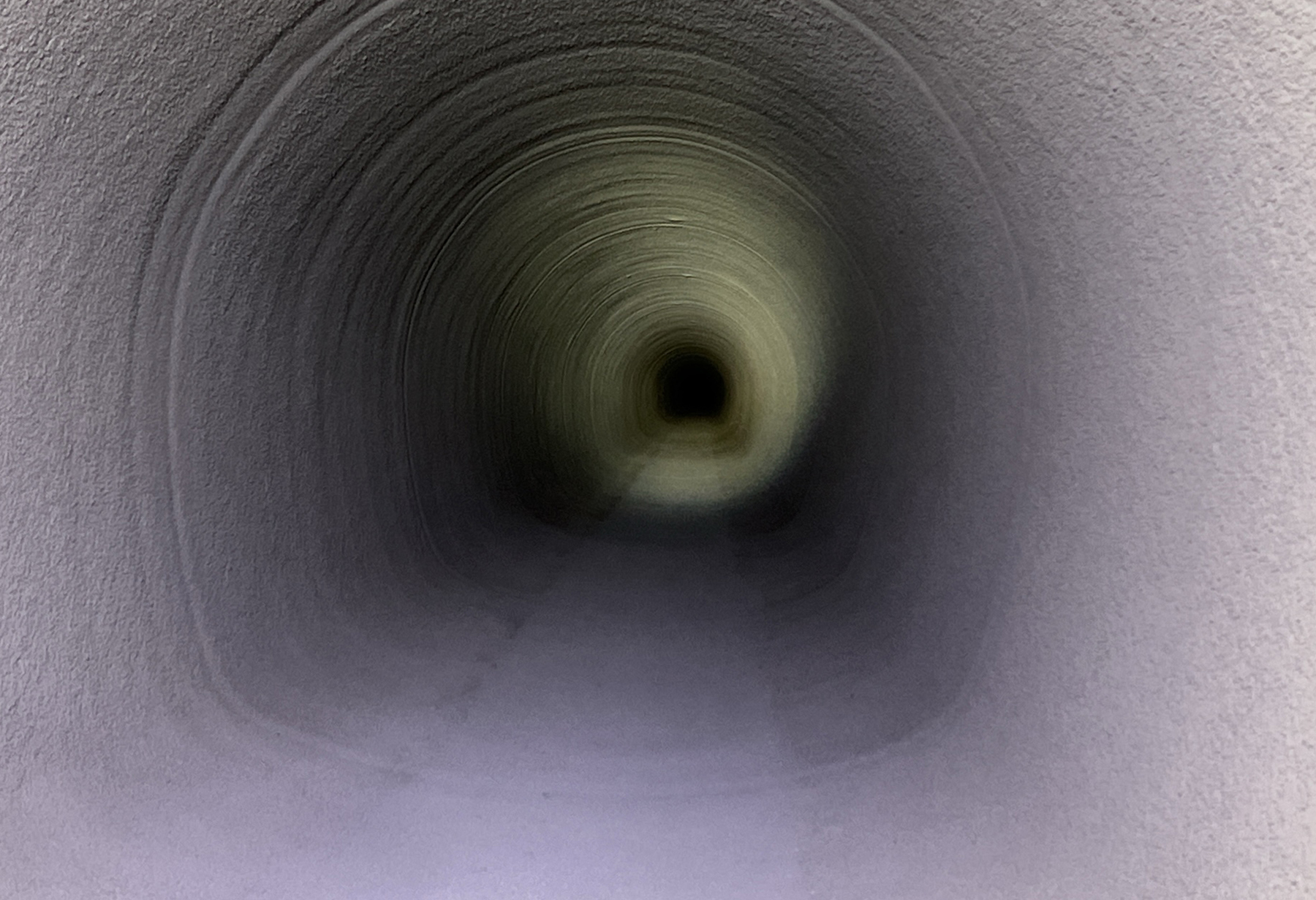
New milestones
For the Oat Hills Tunnel, rehabilitation took the form of sliplining 63 in. diameter FRPM pipe from Hobas Pipe USA Inc. This approach provided significant technical advantages due to FRPM’s inherent corrosion resistance, lower material costs, faster installation, and ability to meet performance standards without the need for concrete repair.
The FRPM pipe design pushed the boundaries of innovation, as it was specifically designed and tested to withstand a full hydrostatic head of 154 psi, or 350 ft, from external groundwater load. The original design called for the use of wheeled casing spacers to support the FRPM pipe during installation for the entire run. However, after further study, the project team determined that, based on the high-jacking capacity of the Hobas pipe, much simpler spacers with polypropylene shoes would also work. Therefore, the design was revised to use shoes instead of wheeled spacers.
The section of the Oat Hills Tunnel requiring rehabilitation was 3,600 ft long, 72 in. high, and horseshoe shaped. The horseshoe shape required a tailored approach. Lidar data for the entire length of the tunnel was collected and used in conjunction with a digital replica of the proposed FRPM pipe and its runners to identify any potential obstructions between the existing tunnel and FRPM pipe.
With thorough planning and first-class execution, the Michels team set new industry milestones for the longest and fastest large-diameter FRPM pipe sliplining operation, installing 3,600 linear ft of 63 in. diameter pipe on time and in just more than two calendar days. On average, each 20 ft long section of FRPM pipe was installed in approximately eight minutes.
As projects become increasingly complex, project success often relies on the experience and creativity of the entire project team. For the San Diego County Water Authority’s First Aqueduct system, the partnership, open communication, and shared goals of the contractor, engineering firm, two product suppliers, and the customer resulted in the installation of two distinct products to complete a complex project on a tight timeline.
Kurt Chirbas, P.E., is western region manager for GeoTree Solutions. Paul Mallory is a senior construction manager and Marc Gravel is a special projects manager for Michels Trenchless Inc.
Project credits
Owner: San Diego County Water Authority
Design-build team: Michels Trenchless Inc. and Stantec
Geopolymer mortar supplier: GeoTree Solutions
Fiberglass-reinforced polymer mortar pipe supplier: Hobas Pipe USA Inc.
This article is published by Civil Engineering Online.