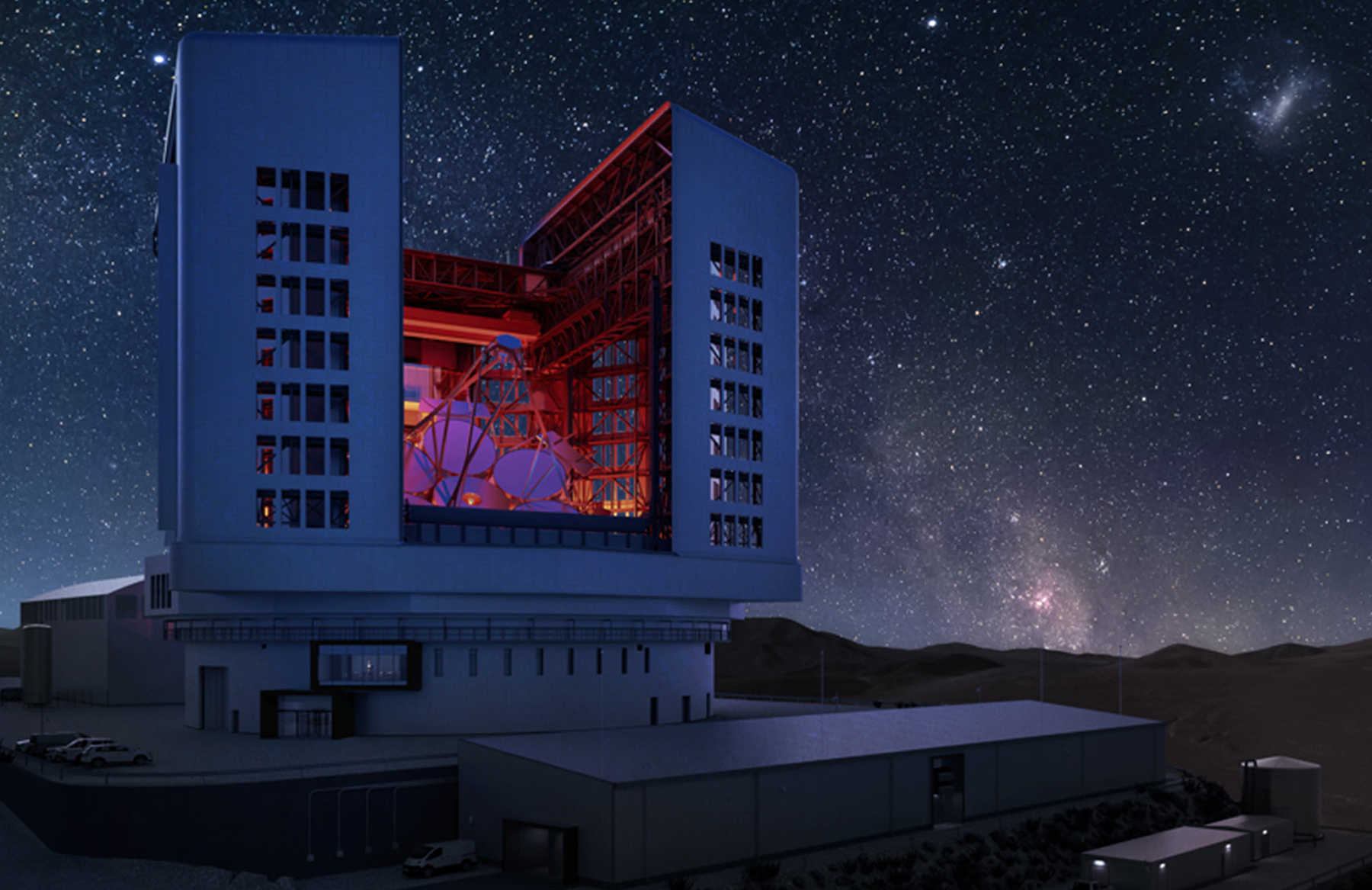
By T.R. Witcher
Rebecca Bernstein, Ph.D., chief scientist for the Giant Magellan Telescope, describes the universe as the ultimate physics laboratory. “The universe can create things at extreme scales – extreme densities, extreme energies – that we can’t create on Earth,” she said.
Nevertheless, what scientists and engineers can create on Earth to study the cosmos is remarkable. Few of these creations are more impressive than the under-construction Giant Magellan Telescope. Conceived in the early 2000s, the telescope, part of a new generation of extremely large telescopes, will be the world’s most powerful when it goes online in the early 2030s.
Further reading:
- Telescope inspectors reach for the stars in West Virginia
- Underground telescope will help scientists detect gravitational waves
- New bridges will help keep NASA’s rocket parts rolling in Florida
The $2.54 billion telescope project is a partnership among 14 institutions around the world, including the University of Arizona, Carnegie Science, the University of Texas, the University of Chicago, Texas A&M University, Harvard University, the Smithsonian Institution, and Arizona State University. Global partners hail from Australia, Brazil, Chile, Israel, South Korea, and Taiwan.
Giant Magellan will be in Chile’s Atacama Desert, at the base of the Andes Mountains, on the grounds of Las Campanas Observatory, which is owned by Carnegie Science. The telescope will stand about 115 feet tall and be protected by a 213-foot-tall enclosure – basically a 22-story building that can rotate in under four minutes. The enclosure was designed by Bilbao, Spain-based architecture and engineering firm IDOM and recently passed final design review.
A light-gathering powerhouse
At the heart of Giant Magellan is a petal-shaped arrangement of seven giant mirrors, each 8.4 meters in diameter. For perspective, the James Webb Space Telescope measures 6.5 meters in total across its mirror segments. Collectively the mirrors of the Giant Magellan will function as one 25-meter-diameter imaging surface. The new telescope will be able to reach four times better spatial resolution than the Webb telescope. It will enable scientists to study exoplanets with 15 times greater resolution than with the Webb telescope.
Large mirrors have distinct advantages. “When you have smaller mirrors, you have miles and miles of edges in the middle of the mirror,” Bernstein said. “All those edges scatter a little bit of light, and that just adds background to your image.”
“So you collect almost 100 times more light,” she added. “You make a 100 times more accurate measurement of the location of the mirror. And the speed with which you can do that is how well you can keep it aligned while you’re working at night.”
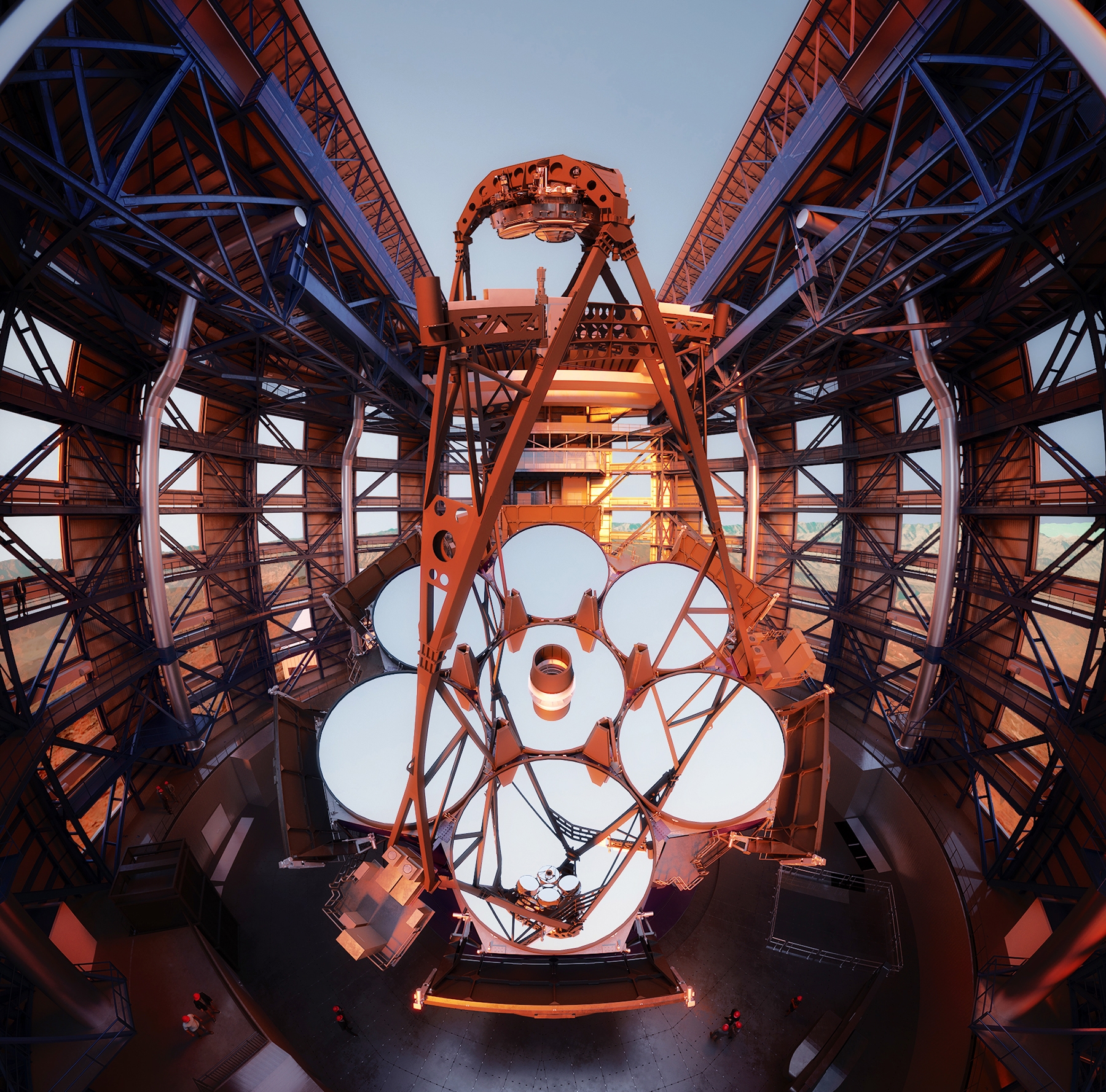
Giant Magellan is, like all telescopes, essentially a bucket that gathers light. The seven primary mirrors collect light and – because they’re reflective surfaces – reflect it up to a set of seven, smaller, lightweight, highly agile mirrors that are mounted above the primary mirrors. These secondary mirrors, each 1 meter in diameter, allow the telescope to perform a correction called adaptive optics.
“They deform 2,000 times a second,” Bernstein said. “We measure the turbulence in the atmosphere 2,000 times a second, and we change the curvature of the mirrors 2,000 times a second to take out the turbulence in the atmosphere.”
The result? Unprecedented resolution and accurate images.
Light then reflects off the secondary mirrors down through an opening at the center of the array of large primary mirrors – and into a series of large scientific instruments. This minimal reflection pathway ensures that more than 75% of light from astronomical sources reaches Giant Magellan’s science instruments.
The key to bringing this telescope to fruition lies at the University of Arizona’s Richard F. Caris Mirror Laboratory, where the world’s largest mirrors are manufactured. The seven mirrors for Giant Magellan, each nearly 28 inches thick at their deepest point, are made of Ohara E-6 borosilicate glass.
The curved mirrors are 80% hollow; according to the lab’s website, their structure is “molded by melting it into a honeycomb interior while spin casting in a custom-designed rotating oven.” Buell T. Jannuzi, Ph.D., director of Steward Observatory and head of the University of Arizona’s department of astronomy, noted that the mirrors “being hollow but still with significant structure, allows (them) to be strong and stiff where we want them to be stiff (supporting the surface) – while still being easy to control in terms of temperature.”
The front surface has to be polished to an almost unimaginably precise level – the variance cannot exceed a fifth of the thickness of a human hair “if you want the light to go where it’s intended to go,” Jannuzi said. If you expanded the mirrors to the size of North America, he adds, the biggest acceptable hill or valley you could have would be about 2 inches.
Not surprisingly, the polishing work is extremely rigorous. The lab carefully studies the way light interacts with the surface as it’s being polished.
“It is a wonderful mix between really accurate engineering and artistic work like a glassblower or woodworker in the sense that you can’t polish too long and remove too much glass,” Jannuzi said. “If you take away too much glass in one part of the surface, you’re going to have to bring the rest of the surface down to the same level. So if we suddenly get a low spot, we can’t add glass back.”
The last stage of mirror fabrication is to apply a thin layer of reflective aluminum. Each mirror takes about four years to complete and costs roughly $20 million.
State-of-the-art enclosure
The telescope must be protected from the elements, including sunlight, dirt, dust, and inclement weather. Enter Giant Magellan’s equally impressive enclosure, equipped with 151-foot-tall, 500-ton shutter doors and advanced airflow and seismic protection systems.
How air moves around a telescope and around and through its enclosure has a huge impact on the quality of the images the telescope can produce. The site in Chile boasts dark skies, a dry climate, a stable atmosphere, and sufficient altitude. It also receives air blown across the Pacific Ocean over 3,000 miles; when it arrives at the Giant Magellan site, that air is very homogeneous in temperature.
“But then the air is getting heated by the ground. It can be heated partially by the telescope and the enclosure themselves,” said Bruce Bigelow, Ph.D., element manager for site infrastructure, enclosure, and facilities for Giant Magellan. Temperature gradients degrade the image quality of the telescope, like shaking a camera while taking a picture. “So what we want to do,” he continued, “is move as much air past the telescope as possible to keep everything at the same temperature.”
To help, the enclosure will use 400 computer-controlled openings – they look like narrow windows – that can carefully modulate airflow around the telescope, depending upon which direction the telescope is pointing, how high up it’s pointed, and wind conditions.
The enclosure utilizes a sophisticated hydrostatic bearing system that allows the telescope to float on an oil film just 50 microns thick, move smoothly, and point anywhere in the sky.
The foundation and the pier that the telescope sits on are very rigid to react to the motions of the telescope as it’s studying objects in the sky. That, in turn, puts “real vertical and lateral stiffness requirements on the seismic isolation system that are typically not present for a building,” Bigelow said. “But then in a big earthquake, we need to be able to transition from that stiff vertical and lateral condition to a much more flexible lateral condition so that the ground can move under the telescope. By providing bearings between the telescope foundations and the ground, we allow that motion to happen, and by preventing all the motion that’s happening in the ground, we’re avoiding transmitting it up into the telescope, where it would cause a hazard for the telescope optics.”
The enclosure uses several seismic isolation components. One, a friction pendulum bearing, is “basically a big dish that’s about 7 feet in diameter with a puck that slides in the middle of that dish,” Bigelow said. “So as the ground moves, the telescope is actually going to go up and down a little bit in a ring of 24 of these dishes.”
The fact that it’s a dish, he adds, means that as an earthquake winds down, the telescope can slowly return to its nominal position at the bottom of those dishes so research can resume.
Those bearings decouple most of the motion of the ground from the telescope. To mitigate the rest, the isolation system uses a set of four hydraulic dampers, basically giant shock absorbers that use the motion energy to heat the oil in the dampers.
“And so that’s over the course of a four- or five-minute earthquake,” Bigelow said. “That’s how we release the energy without damaging the telescope.”
Finally, a set of large hydraulic cylinders “allow us to bring the telescope back exactly to its home position after an earthquake,” Bigelow added. Figuring out how all these components work together has taken engineers and designers several years.
To help clean and recoat the mirrors every 4-5 years, a 75-ton crane will be placed at the top of the enclosure. It will be able to reach and remove any of the mirrors, so that they can be lowered to grade level and transported to another building to be recoated. (The crane will also be used to help assemble the telescope.)
Approaching the finish line
The support site for the telescope – essentially a small village to house staff and construction crew – has operated since 2017. Excavation for the telescope and enclosure foundations was completed in 2019. And the underground infrastructure systems for water, fire protection, electricity, and networking were completed in 2021.
The site uses water from nearby Las Campanas Observatory. “But we are in the desert, so we have to be extremely careful with the use of that water,” Bigelow said. “We only use it for human purposes. We don’t use the local water for construction. That water must be brought in by truck.”
Wastewater will be recycled and treated at the site, so it can be discharged back into the country’s natural environment.
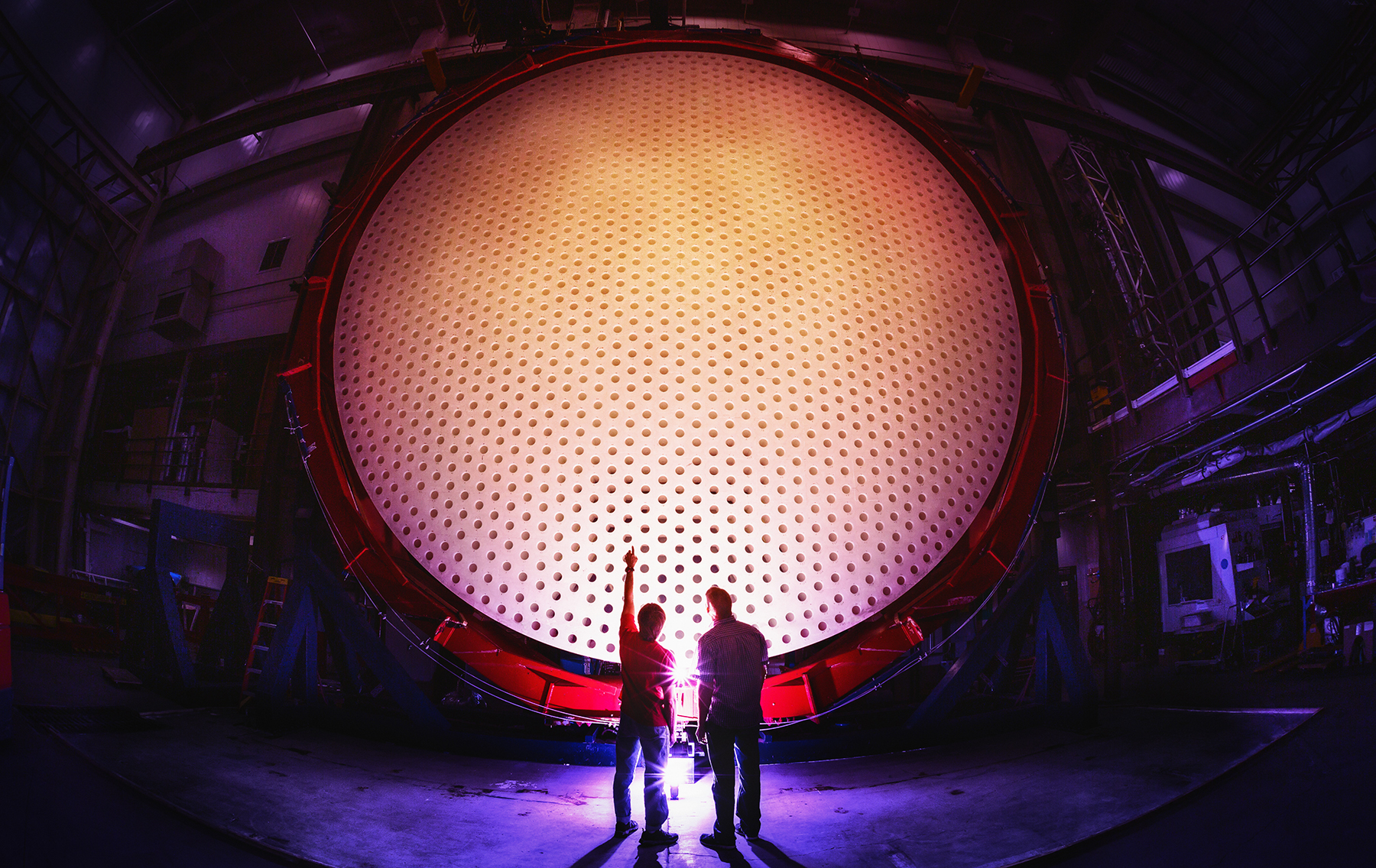
The seven primary mirrors have been cast. Three have been polished and are sitting in storage waiting for assembly. The other four are in various stages of fabrication. The smaller adaptive mirrors will be completed in 2026. Bigelow says that more than 40% of the telescope is under construction, most of it being done across 36 states.
The telescope will sit atop a 1,300-ton, 128-foot-tall support mount that will be assembled in a new manufacturing plant in Rockford, Illinois.
The telescope and its enclosure are expected to be complete in the early 2030s.
Its high-resolution imaging will enable scientists to study the complex interactions between the universe and the stars and planets within it – including our own. But the real achievements of Giant Magellan may prove to be the ones we can’t yet imagine.
“People like to say that telescopes are discovery machines,” Bigelow said. “So you build it partly because there’s things you’re looking for, but the most amazing things that the telescopes usually do are surprises. They discover things that were unanticipated.”
This article is published by Civil Engineering Source.