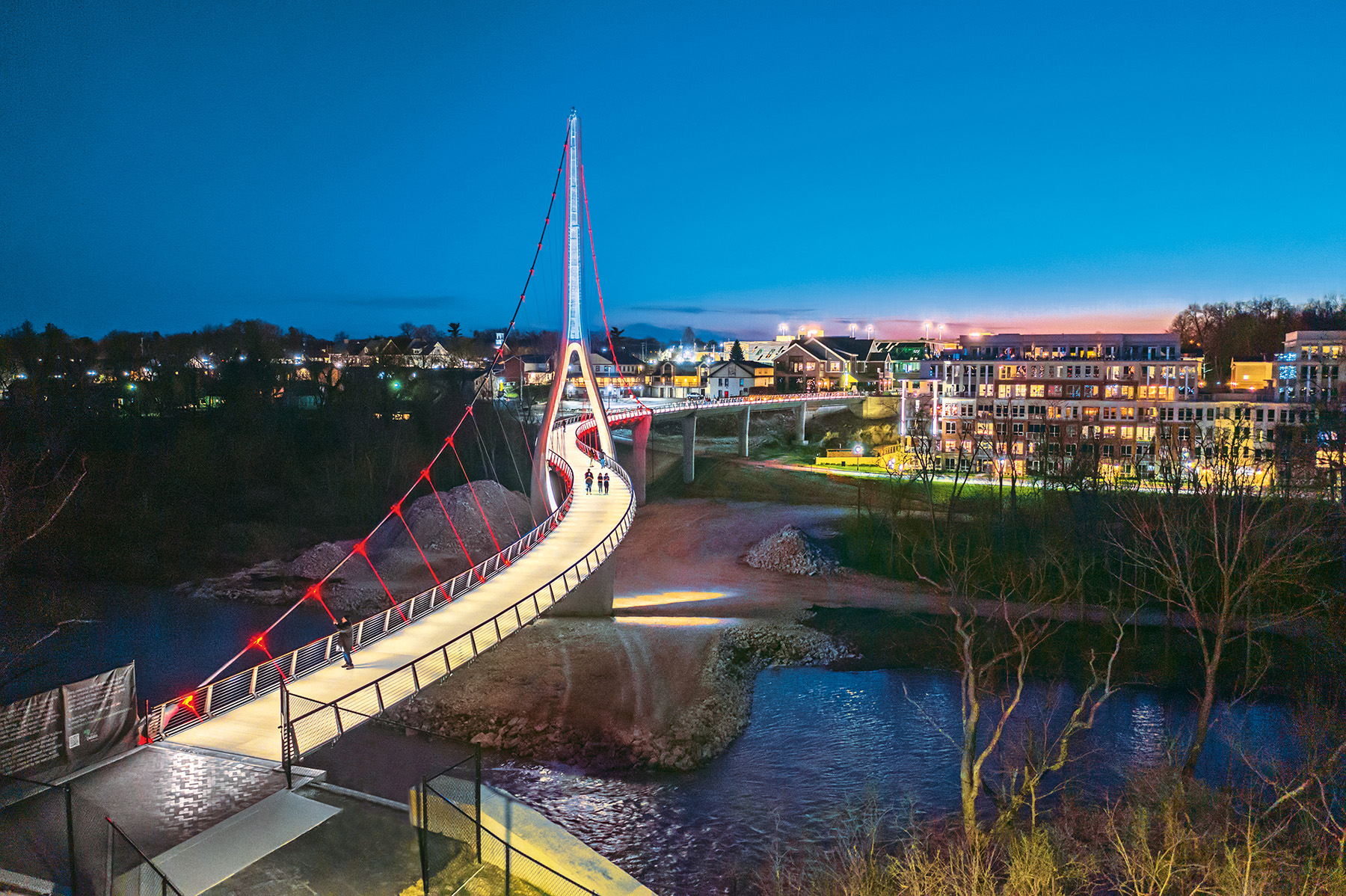
A new pedestrian bridge, S-shaped in plan, now spans the Scioto River in downtown Dublin, Ohio, a suburb of Columbus. The 760 ft long, cable-stayed crossing features a 500 ft long main span and a 169 ft tall single tower. The slender, curving deck is 14 ft wide. Aligned roughly east to west, the bridge crosses the Scioto between the historical downtown of Dublin on the western bank and a planned public park and other new development on the eastern bank, explains Dan Fitzwilliam, P.E., M.ASCE, a senior bridge engineer in T.Y. Lin International’s San Diego office.
TYLI was the project’s structural engineer. The bridge was designed by the architecture firm Endrestudio and constructed by Kokosing Construction Co. Dubbed the Dublin Link, the bridge opened in mid-March, although it closed briefly in May for planned painting and sealing work that had been delayed until warmer weather, according to a city of Dublin press release.
Located north of Dublin’s Bridge Street, which features a vehicular crossing with relatively narrow sidewalks, the Dublin Link bridge was intended to provide a safer method for pedestrians and cyclists to cross the river and to create “a landmark in the middle of town,” says Fitzwilliam.
The new bridge features a cast-in-place concrete tower and a concrete deck supported by a steel box girder system that is triangular in cross section. There are concrete-framed abutments at each end and a series of four, 65 ft long concrete approach spans on just the west side of the structure. Each approach span is supported on a concrete column. The S-shaped design accommodates the east and west side landing points of the bridge, which do not align, Fitzwilliam says.
Although a straight, diagonal alignment was possible, the curving solution “adds a lot of interest, “Fitzwilliam explains, “and dramatizes the experience as you come across — you’re looking in different directions as you cross the bridge.”
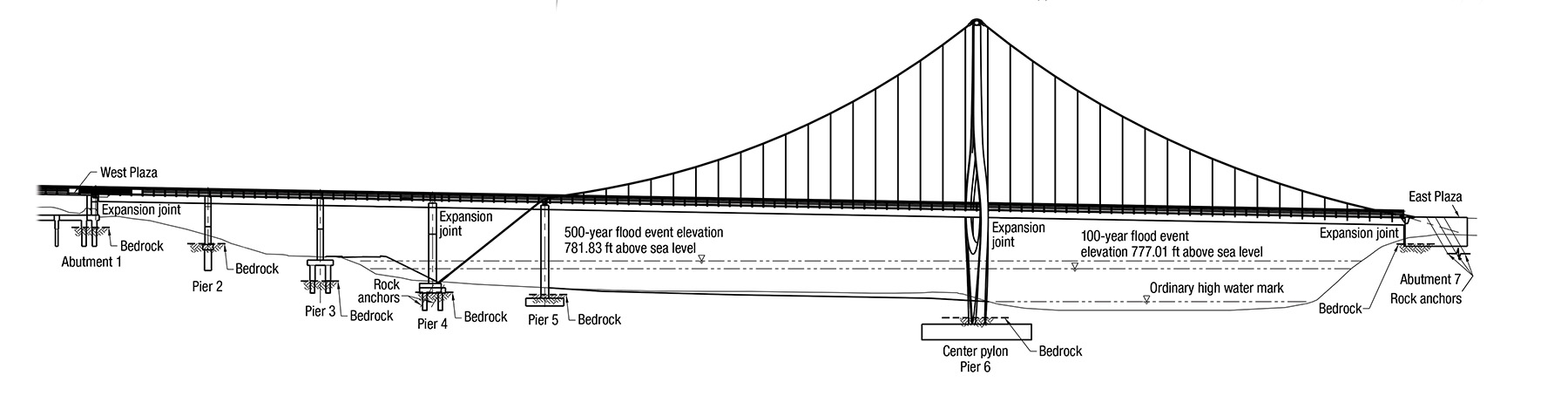
Because the bridge’s single tower, located at the midpoint of the main span, is founded on the western bank of the river, only the eastern half of the main span crosses the river in its normal flow. But most of the area beneath the bridge is part of a wider flood zone — a fact that the project team experienced repeatedly as the entire flood zone was indeed flooded multiple times during the construction phase, Fitzwilliam notes.
The structure features a somewhat unique, single-plane arrangement of cables that connects to just one side of the deck on each half of the main span, switching from the south edge of the deck on the eastern half to the north edge on the western half, Fitzwilliam says.
This configuration means that the cables pull toward the inside of each curve, creating an arching action in plan. Swapping the cables from one side of the deck to the other helps balance the torsion that builds up on one side of the main span with an equal and opposite torsion on the other, Fitzwilliam explains.
Also somewhat uniquely, the deck passes through an opening in the tower without actually being supported by that structure. This arrangement — which resembles a relatively wide thread passing through the eye of a needle — required larger sizes for the stays closest to the tower: roughly 32 mm in diameter compared with 21 mm for the typical stays, Fitzwilliam notes.
There is roughly 1 ft of clearance on either side of the deck as it passes through the tower opening, and the system is designed to accommodate at least 2 in. of vertical movement because of temperature changes or activity on the bridge as well as approximately 1.5 in. of longitudinal movement.
The main cables are 120 mm in diameter. On the east end, the main cable is anchored into the abutment, but on the west end it required a tie-down cable that is secured with rock anchors at the base of the second column westward from the tower. Because this backstay is located within the floodplain, its lower portion is surrounded by a steel pipe to protect against debris impacts during a flood event, Fitzwilliam says.
The cables were fatigue-tested at two labs in Germany for long-term exposure to wind and vibrations, which involved 1 million cycles for the main cables and 2 million cycles each for the stays.
To provide the necessary torsional stiffness for the bridge, the triangular box girder that supports the deck features a closed cross-sectional design rather than the more conventional approach of separate I girders, Fitzwilliam says. In addition, the box girder system is asymmetrical, swapping sides to accommodate the way the cable stays shift from one edge of the deck to the other.
Moving east to west along the 14 ft wide deck, the box girder is initially a 10 ft wide structure located beneath the south side of the deck, beneath the stays that attach to the south edge. Morphing in size as it moves westward, the box girder increases to 14 ft wide as it passes through the opening in the tower, before returning to a 10 ft width on the western side of the main span.
But on the western side, the box girder shifts its mass to the northern edge of the deck, beneath the stays that are now attached to the north side of the span, Fitzwilliam explains.
To help minimize the tendency for lateral vibration from wind and dynamic live loads, the box girder system also features pendulum-style tuned mass dampers — one on each side of the main span at the midpoint of each section, which is the place of maximum potential displacement, Fitzwilliam says. It is the first time that TYLI has used this type of damper on a bridge; normally such dampers are used in buildings.
Although the abutment on the west side of the bridge is a conventional support, the east side abutment required a novel design to accommodate the negative moment generated at a column on the west end of the main span. “We have a fairly unique situation (at the east abutment) where we need to generate negative moment but also allow for movement” to avoid fixity, Fitzwilliam says.
The solution was to create a concrete vault at the east abutment and extend the deck’s steel girder another 30 ft into that space, adding supports at both the apparent end of the girder and also at the actual end of this support 30 ft farther in. Together with a slide bearing system, the approach generates the necessary negative moment on the east side to match the conditions on the west end of the span and provides the desired stiffness but still allows movement for thermal changes, Fitzwilliam explains.
The tower is supported on a 6 ft thick spread footing. The approach span column closest to the tower is also founded on a spread footing, albeit smaller than the tower’s system. The other three columns are supported on cast-in-drilled hole piles, ranging from 10 to 16 ft in depth and 2.5 to 4 ft in diameter.
Designed to be a city icon, the bridge features multiple lighting systems to create different color-changing effects, with some of the lights illuminating the stays and others focusing on the upper portion of the tower.
This article first appeared in the November 2020 issue of Civil Engineering.