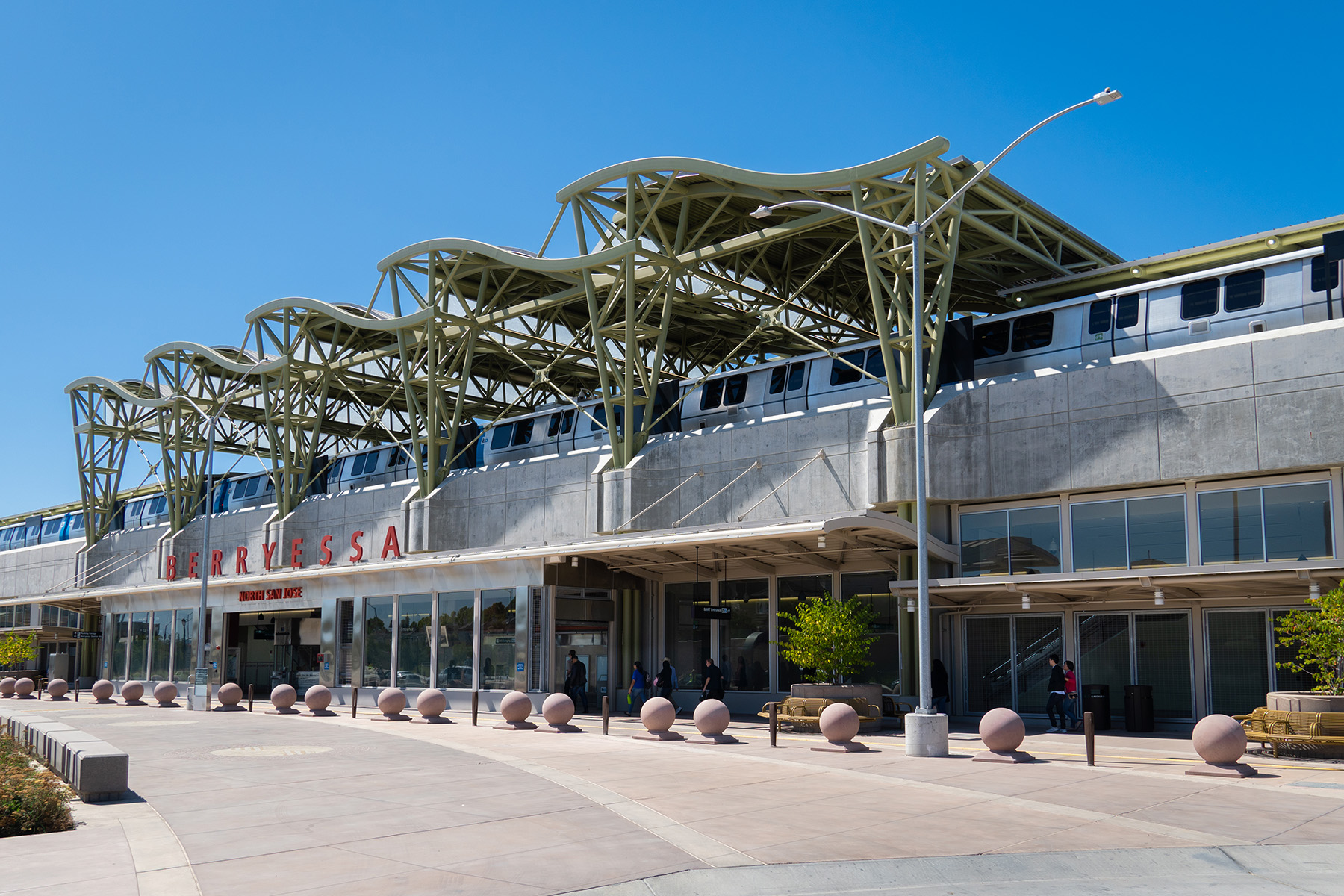
The first phase of the Silicon Valley Extension Program expanded heavy-rail transit service in Northern California from the San Francisco Bay Area southward into the Silicon Valley. The $2.3-billion project encountered challenging site conditions that were resolved by using a lightweight cellular concrete, a tunnel to pass underneath critical utilities, and a system of cameras and sensors to increase safety near an active freight rail line.
Northern California’s Santa Clara County might seem to have everything it needs, from the rolling hills and high-tech industries of Silicon Valley to the swaying palm trees that epitomize the laid-back West Coast lifestyle. But as the region’s population has grown over the years, the county has also experienced that common but undesirable side effect of success: increasing traffic congestion, especially along interstates 880 and 680.
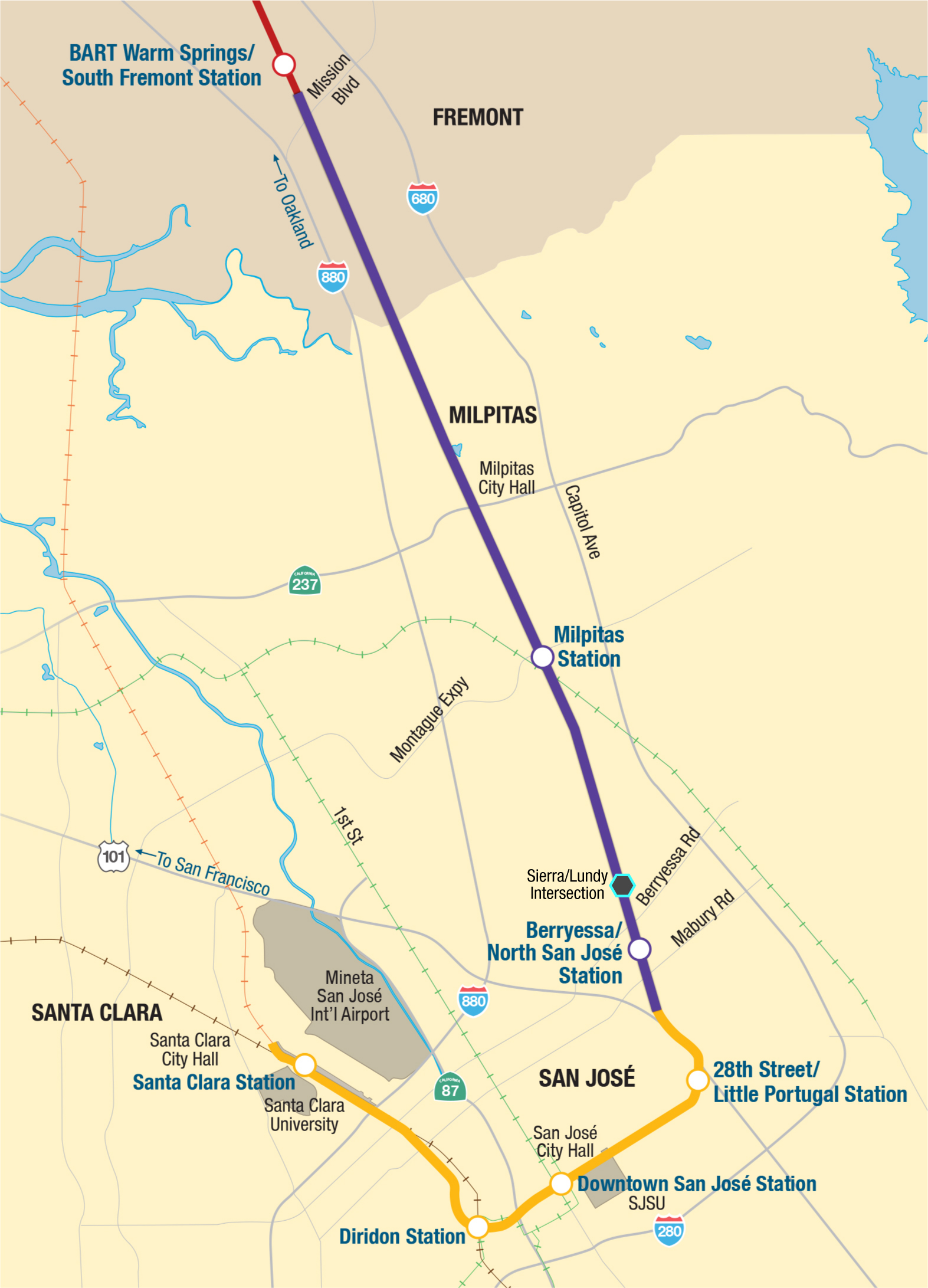
To improve transportation in the greater San Francisco Bay Area, the Santa Clara Valley Transportation Authority and Bay Area Rapid Transit are extending heavy-rail passenger train service southward from Alameda County into Santa Clara County. Called the Silicon Valley Extension Program, the roughly north-south-oriented project will ultimately add 16 mi of new tracks and six new stations to the existing BART network, much of it between I-880 to the west and I-680 to the east. Although Santa Clara County is not part of the BART district, VTA has contracted with BART to operate and maintain the extension within Santa Clara County. VTA is funding and overseeing the construction of the extension’s infrastructure, which it will own. VTA also provides bus and light-rail service within the county.
The first phase of the project, known as the Berryessa extension, was completed during 2020 at a cost of $2.3 billion. It featured the design and construction of two new transit center stations and 10.2 mi of double-tracked rail line starting at BART’s existing Warm Springs station in the city of Fremont and ending in the Berryessa area north of San Jose. Approximately 6 mi of the new line is constructed in trenches, another 3 mi is at grade, and approximately 1 mi is supported on an elevated structure. Roughly half the distance runs parallel to an active Union Pacific Railroad line.
The project’s second phase will include an additional 6 mi of track and add four more stations in the cities of San Jose and Santa Clara. Phase II construction is expected to start in 2022, and the new line will not be completed until at least 2030, according to information on the VTA website.
The design-build Phase I project was constructed by a joint venture of Skanska USA Civil Inc., Shimmick Construction Co. Inc., and Herzog Contracting Corp. The engineering firm Lockwood, Andrews & Newnam Inc., a Leo A. Daly company, served as the lead designer in a joint venture with T.Y. Lin International. LAN’s scope of work included the track systems, stations, mechanical and electrical systems, and certain structures. TYLI’s work focused on the trench and elevated structures, retaining walls, a tunnel, and other structural systems.
Parallel predicament
The new BART line lies within an existing Union Pacific right of way that VTA purchased, with the new tracks paralleling the Union Pacific tracks for the initial 5 mi of the distance south from Warm Springs to a new BART station at Milpitas. That meant some of the first work on the project involved the relocation of Union Pacific tracks slightly westward within the same corridor as well as the removal of grade crossings and other freight-line systems, says Tim Schmidt, LAN’s director of transit for California, who works in the firm’s San Jose office.
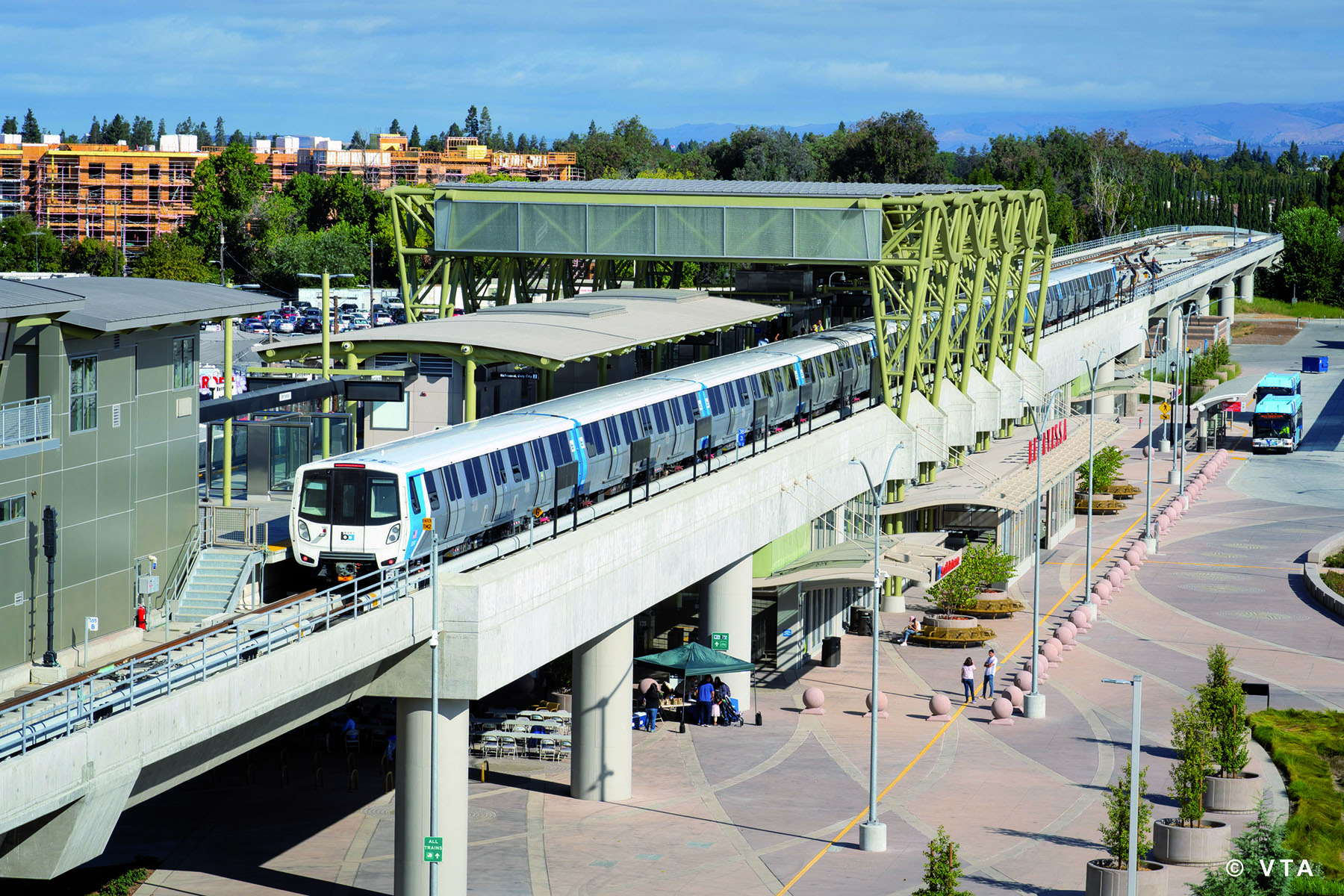
Although most of the track relocation work was completed by VTA before LAN joined the project, the engineers did help develop solutions to the challenges posed by the proximity of the freight traffic, which in places was separated from the BART line by as little as 50 ft, notes Schmidt. (See “Tracking Trouble,” below.)
LAN also helped relocate a Union Pacific spur line to a nearby industrial site. Because the spur line had to cross the trench for the new BART line, a roughly 1,000 ft long track detour known as a shoofly was constructed to maintain access to the industrial site, while the trench work and a new bridge for Union Pacific were completed. That work took about a year, Schmidt adds.
Numerous utilities were also relocated along the route of the Berryessa extension, including underground pipes and buried systems for as many as 13 different utility providers. Among these were roughly 700 linear ft of a 60 in. diameter transmission line for the Santa Clara Valley Water District. The pipeline had to be moved to accommodate the piers for the elevated portion of the rail line, including the elevated Berryessa station.
There was also a major Chevron Corp. gasoline line that supplied fuel throughout the Bay Area and an MCI system that carried all the fiber optic lines from Silicon Valley to the San Francisco/Oakland region — both of which paralleled the BART corridor for the entire 10.2 mi length of the extension, Schmidt notes. Because of the significance and sensitive nature of the Chevron and MCI systems, the project relied on vacuum trucks that used forced air to remove soil and expose the utility lines rather than the more traditional approach of digging potholes, Schmidt says.
Ventilation consideration
In all, the project team spent two years just on utility coordination and relocation. But in certain areas, creative design solutions helped avoid additional relocation work. At the intersection of Sierra Road and Lundy Avenue in San Jose — between the sites for the Milpitas and Berryessa stations — the initial plans called for a shallow trench to house the tracks. But this trench would have disrupted a major sewer line and required the construction of a large siphon system for stormwater and wastewater, says Odeon Li, P.E., a senior bridge engineer in TYLI’s San Ramon, California, office.
To overcome those issues, the Skanska-Shimmick-Herzog contractor team proposed a cut-and-cover tunnel that would pass underneath the sewer line and any other utilities at the site. The utilities would be supported in place, suspended from shoring struts, explains Schmidt. Although this solution would ultimately save time and money, the approach came with its own challenges, Li notes.
For example, the tunnel could not exceed 1,000 ft in length or else it would require mechanical ventilation to dissipate smoke in the event of an underground fire. Rectangular in cross section, the reinforced-concrete tunnel measures 39.5 ft wide and varies in height from 19 ft, 9 in. to 23 ft. A wall in the middle separates the two tracks, with openings at regular intervals to permit access between the sides of the tunnel in case of emergency, Li says.
Instead of ventilation fans, the tunnel relies on three chimneys located within the tunnel roof to convey smoke out of the structure during a fire, Li says. The tunnel roof remains at a constant elevation below grade, Li adds, but the depth of the tunnel varies by several feet along its length, resulting in a maximum soil cover of 17 ft. The varying height within the tunnel provides additional space for smoke to exit the space, Li explains.
AECOM conducted an extensive smoke analysis of the system, Li says. The tunnel structure was analyzed by AMEC Environment & Infrastructure Inc. — now part of Wood Environment & Infrastructure Solutions Inc., based in Aberdeen, Scotland — using FLAC3D modeling software, manufactured by Itasca Consulting Group Inc., of Minneapolis. Because of the region’s high water table, the tunnel was designed using ACI 350 concrete, which is often used for water tanks. This obviated the need for additional waterproofing, although a pumping station was constructed adjacent to the tunnel to collect and remove any stormwater that enters the tunnel through its two portals, Li adds.
Working closely with the city of San Jose, the project team also negotiated a nine-month construction period during which the Sierra-Lundy intersection could be shut down, with traffic diverted to nearby thoroughfares. It resulted in a “win-win situation all around,” says Schmidt. Because the sewer line and other utilities remained operational throughout the project, the city did not have to contend with a maintenance-intensive siphon system, and the contractor enjoyed nine traffic-free months in which to complete the work.
Under and over
Because the Berryessa extension crossed numerous at-grade intersections, more than half the new line was located in trenches up to 30 ft deep. These trenches were also designed using ACI 350 concrete, and in certain locations the soil beneath the trenches was overexcavated and replaced with material that would better support the new loads, Li says.
The project relied on a top-down construction approach, Schmidt adds, in which the new concrete bridges for the roads were first constructed at grade and then the trenches were excavated beneath the bridges. Sacrificial piles supported the bridges until the concrete trench walls were in place to serve as the bridge abutments, Schmidt explains.
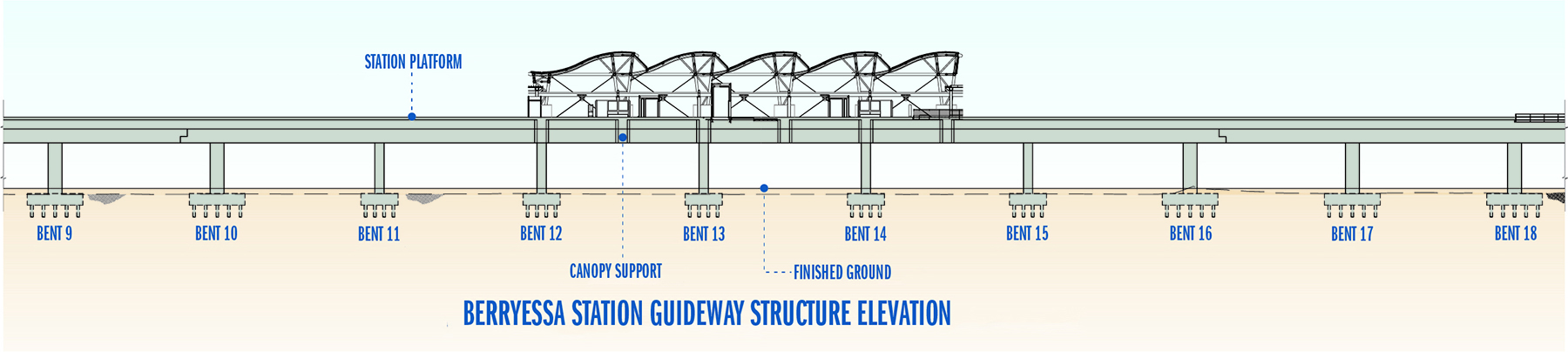
At the approaches to the Berryessa station — elevated as much as 16.5 ft to pass over Berryessa and Mabury roads — the abutments for the raised portions featured backfilled areas behind precast-concrete panels that on a more traditional project would likely have been filled with mechanically stabilized earth, says Li. But geotechnical studies indicated the potential for substantial settlement of MSE at those sites, which might then require additional lifts of MSE and more time.
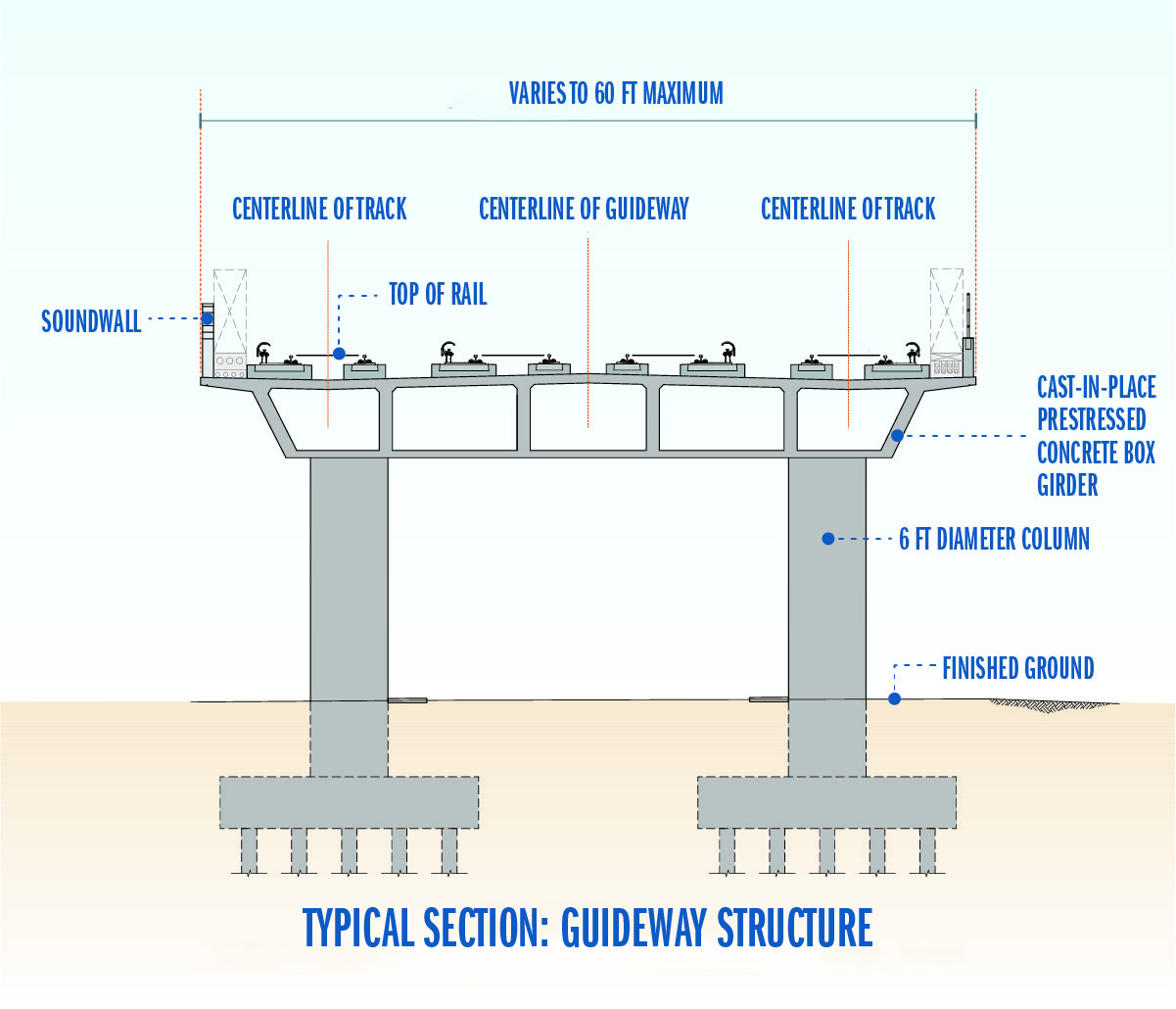
In addition, there were several single-family homes in the area that “abutted right up to the back of our right of way,” notes Schmidt, “so we were concerned about subsidence” potentially damaging those structures.
Instead of an engineered soil backfill, the project turned to a lightweight cellular concrete material that had been used on various freeway and other rail projects in California as well as internationally, says Schmidt. This material, which is infused with air to make it even lighter, reduced the expected settlement to acceptable levels, he adds. Crews first excavated the sites to depths of about 7 ft “and replaced that soil with two lifts of the lightweight cellular concrete to take some of the initial weight off before we started adding our other layers,” Schmidt explains.
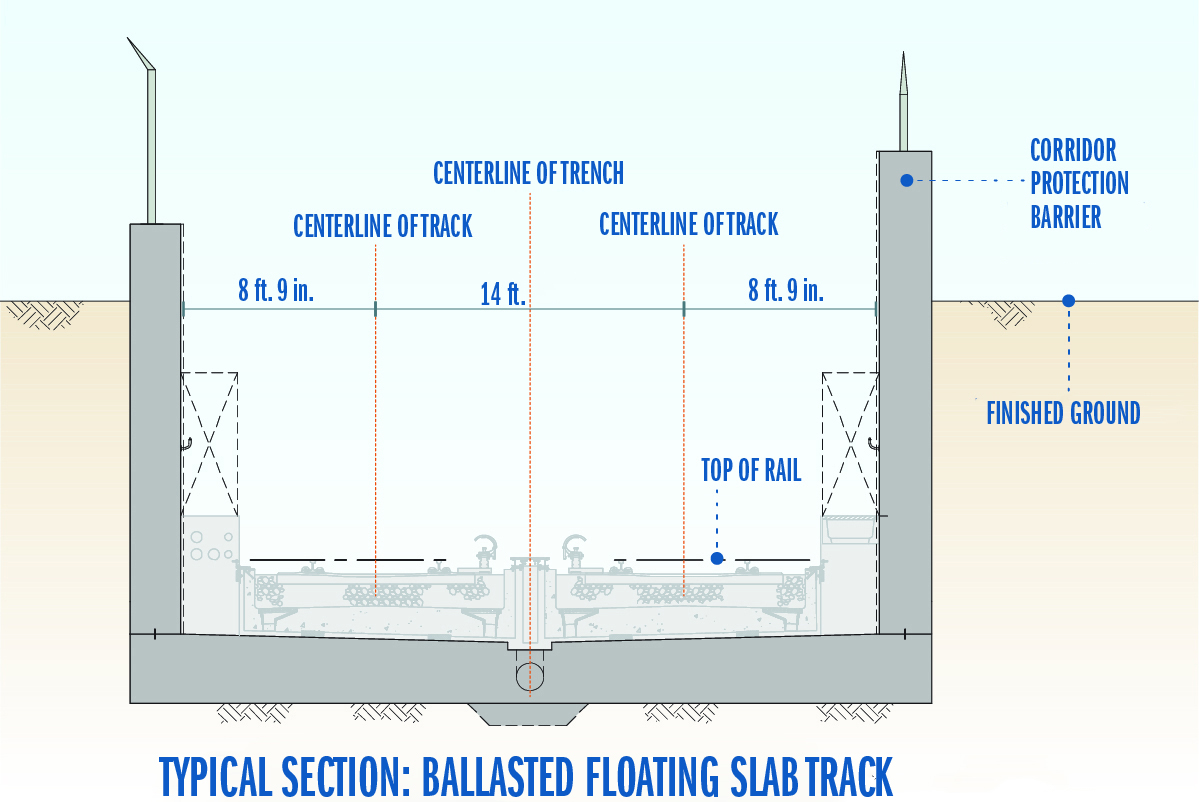
Bay stations
The new multimodal transit centers at Milpitas and Berryessa were initially designed by VBN Architects (now part of STV Architecture) and FMG Architects, respectively, and the designs for both were finalized by Anil Verma Associates. Each station features an adjoining parking garage with more than 1,100 parking spaces, bus facilities, and storage spaces for bicycles.
Located on a 27-acre campus, the Milpitas station is considered BART’s “gateway to Silicon Valley.” It consists of a grade-level concourse with below-grade, split-level boarding platforms, both framed in concrete. The concourse-level station structure is framed in steel and features a series of large skylights in its arched roof to bring natural light into the station and down to the platform level, says Schmidt. A steel-truss pedestrian bridge, roughly 260 ft long and supported on a trio of concrete piers, connects the new BART station to a nearby existing VTA light-rail station. Another steel-framed pedestrian bridge, 229 ft long, connects the BART station’s parking garage to a nearby shopping mall.
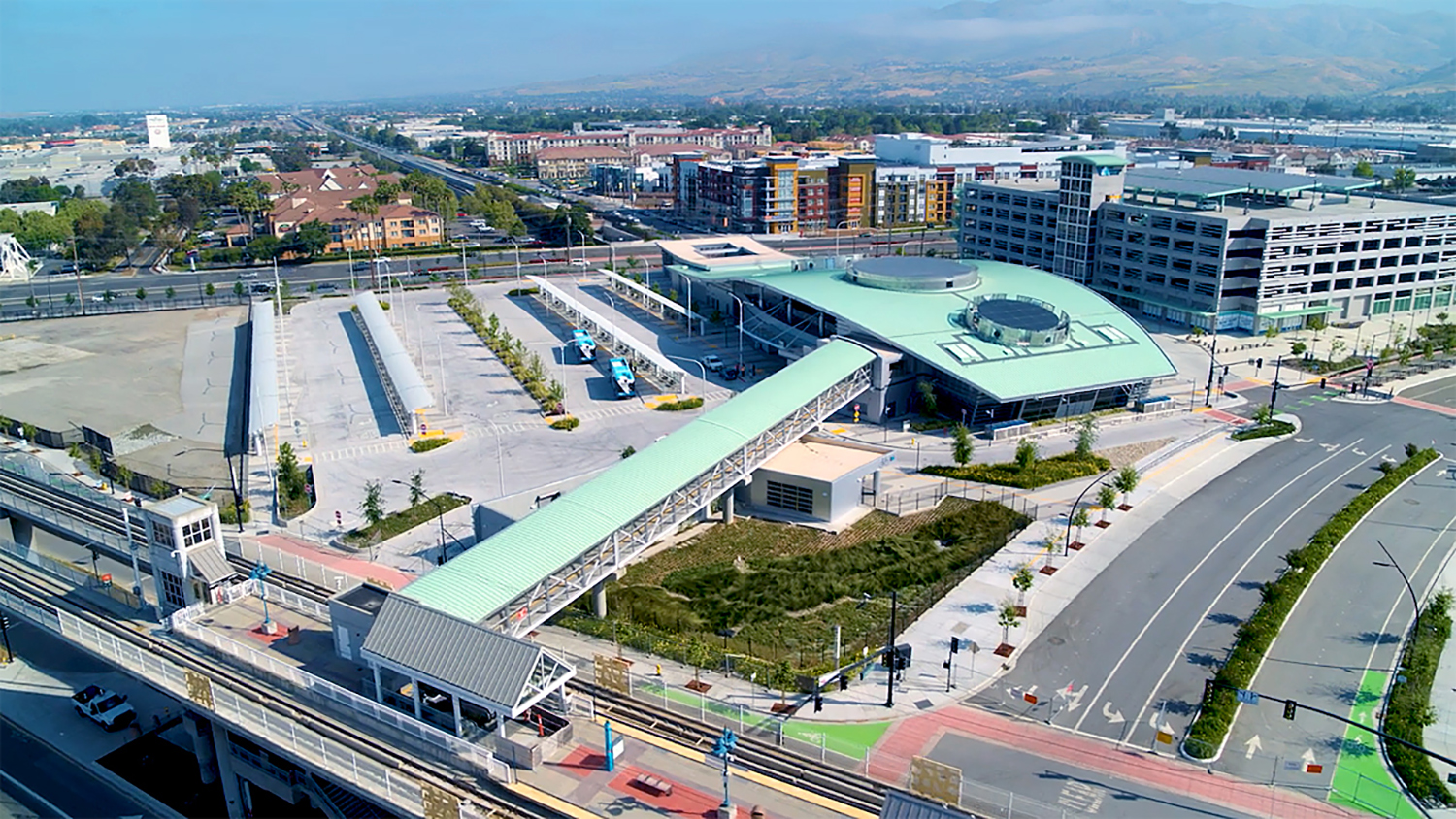
The Berryessa station is located on a 52-acre campus adjacent to a popular flea market in San Jose. The concrete-framed BART facility features an at-grade concourse and an elevated platform. The station is topped by a curvilinear canopy formed from steel tubes in five wavy segments that together measure more than 184 ft long. Designed as an homage to the region’s agricultural heritage, the structure is supported on the concrete columns of the aerial platform.
Both the Milpitas and Berryessa stations feature back-of-house facilities for BART operations personnel. Because the Berryessa station is currently the terminus of the Silicon Valley extension, it also features the facilities to store and monitor trains overnight, notes Schmidt.
A new staircase, gates, and fencing also provide access between the Berryessa station and the adjoining flea market. Transit-oriented development projects are already underway at both new stations, Schmidt adds.
Floodwaters and noise levels
During the Berryessa extension project, the Santa Clara Valley Water District was in the midst of updating the floodplain maps of the area near the new Milpitas station. Because the project was changing what had been an at-grade Union Pacific rail line to the below-grade trenches of the BART system, LAN, VTA, and the contractors worked closely with the water district to ensure that the extension design could accommodate a 100-year flood. This was especially critical in an area south of the Milpitas station at which the trenches could interfere with the flow of stormwater that previously would have just passed over the Union Pacific tracks, notes Schmidt.
To mitigate this concern, the project team installed more than 300 water-balancing pipes beneath and along the sidewalls of an 800 ft long section of the trench. These roughly U-shaped pipes, 12 in. in diameter, are designed to enable stormwater to flow easily from one side of the trench to the other. “We still allow the water to cross the tracks, so to speak,” explains Schmidt. “It just crosses in this series of pipes that goes underneath our trench.”
Noise and vibration issues were additional concerns, especially because of the close proximity of some residences to the new BART tracks. The project team addressed these issues with several measures, including the use of a so-called “floating slab track” in key locations, says Schmidt. This method featured a series of extruded rubber pucks, each roughly 3 in. in diameter, sandwiched between two concrete structures; the upper slab supports the tracks, ties, and ballast. “The extruded rubber squishes as trains go over,” which mitigates the vibration, Schmidt explains.
The project also involved the installation of 12,500 linear ft of sound walls along the track as well as the installation of noise-insulating windows in nearly 250 houses located close to the line.
Other aspects of the project included efforts to maintain vehicular traffic flow in three communities along the route as intersections and grade crossings had to be opened and closed during the construction phase. The complicated design and construction efforts for the project were divided into 31 separate, manageable pieces — called design units — and then subdivided even further into different work packages to better manage the schedule, notes Schmidt.
Phase I of the Silicon Valley Extension Program began revenue service in June 2020. The Phase II work will involve an additional 6 mi long extension, much of it within an approximately 5 mi long tunnel. Four new stations are planned between downtown San Jose and the city of Santa Clara — three underground and a fourth at grade. The plans also include maintenance and storage facilities and the possibility of transit-oriented development projects at each new station.
PROJECT CREDITS
Extension project owner: Santa Clara Valley Transportation Authority, San Jose, California
Extension project operator: Bay Area Rapid Transit, Oakland, California
Design-build contractor: A joint venture of Skanska USA Civil Inc., New York City; Shimmick Construction Co. Inc., Oakland; and Herzog Contracting Corp., St. Joseph, Missouri
Engineering consultants: A joint venture of Lockwood, Andrews & Newnam Inc., a Leo A. Daly company, Houston, and T.Y. Lin International, San Francisco
Preliminary architectural design of stations: VBN Architects, Oakland (now part of STV Architecture) for Milpitas; FMG Architects, Oakland, San Francisco, and Los Angeles, for Berryessa
Final station design: Anil Verma Associates, Los Angeles
Geotechnical engineers: PARIKH Consultants Inc., Milpitas, California; AMEC Environment & Infrastructure Inc. (now part of Wood Environment & Infrastructure Solutions Inc.), Aberdeen, Scotland
Smoke analysis: AECOM, Los Angeles
Structural engineer of record for Milpitas BART station: MFT Consulting Engineers Inc., Pinole, California
SIDEBAR
Tracking Trouble
By Robert L. Reid
Because the commuter rail tracks for the Santa Clara Valley Transportation Authority’s Silicon Valley Extension Program are, in places, located within just 50 ft of active Union Pacific Railroad tracks, the project team for the Berryessa extension portion faced the prospect of having to construct a massive and expensive concrete barrier to keep the two lines safely separated. Instead, VTA and the project team worked with Union Pacific to install a state-of-the-art electronic safety system known as RIDS, for Railroad Intrusion Detection System.
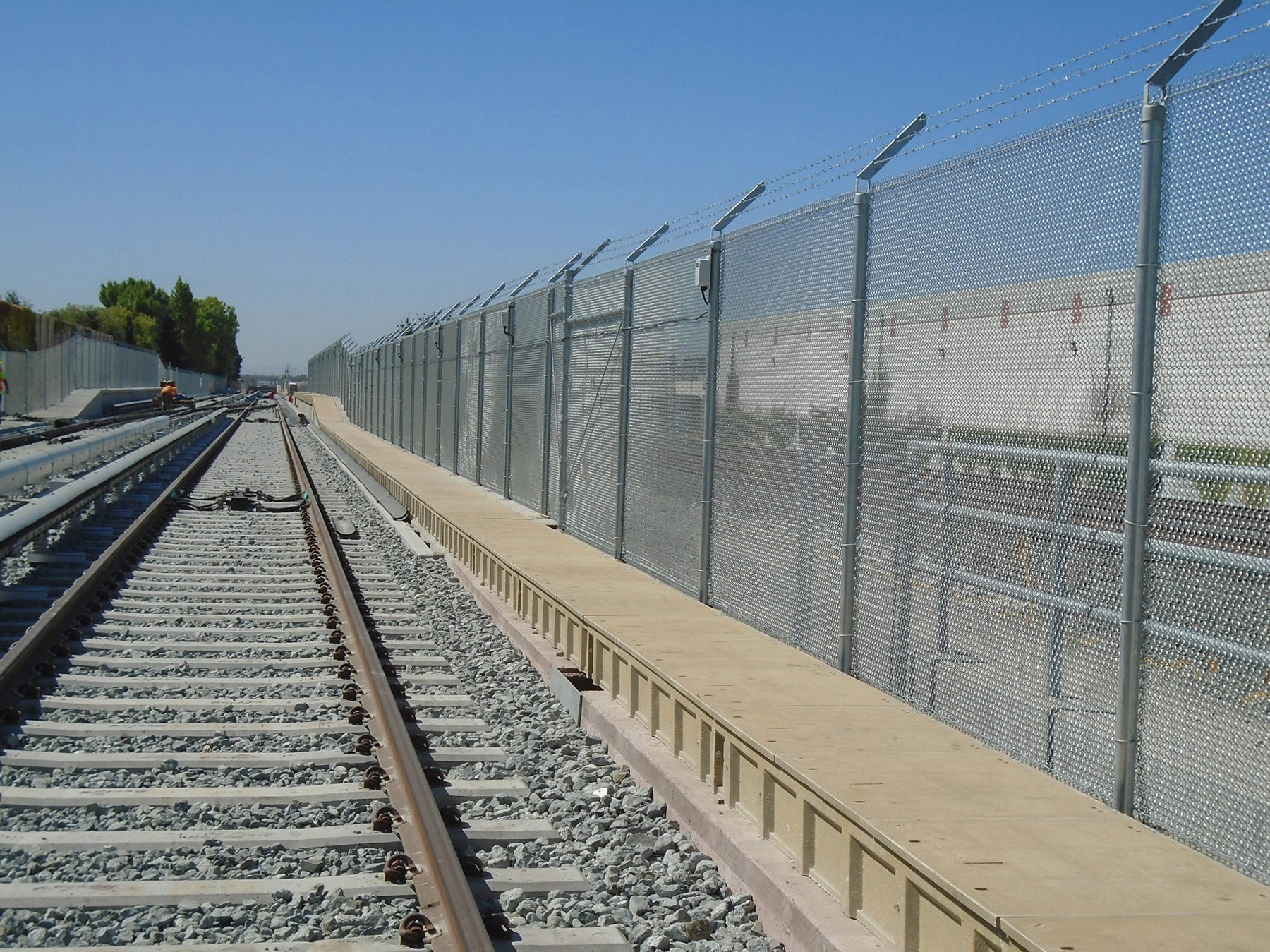
VTA is overseeing the construction of the extension and its new stations; Bay Area Rapid Transit will operate and maintain the line.
Combining sophisticated sensors with video surveillance to detect possible problems and even automatically stop the commuter trains, the Berryessa extension’s RIDS system is the first of its kind to be implemented on a commuter rail transit project in the United States, explains Tim Schmidt, the director of transit for California in the San Jose office of engineering firm Lockwood, Andrews & Newnam Inc., a Leo A. Daly company. LAN served as the lead designer on the project in a joint venture with T.Y. Lin International.
Instead of a large concrete crash wall, a simple chain-link fence separates the BART tracks from the Union Pacific tracks along the entire 5 mi length of the parallel routes. But roughly every 30 ft along that fence is a pole that supports a tilt sensor.
“If there were an intrusion,” Schmidt explains, “if a freight train derailed or some cargo rolled off and hit the fence, and the pole with the sensor went out of plumb by more than 30 degrees, an alarm would be sent to BART’s train operations control center.” The tilt sensors are connected to an automatic train control system, he adds, which could slow down or stop any approaching trains.
The system would keep trains away from the affected area “until the operations control center could determine what caused the fence to tilt and then either release the train to proceed with caution or get somebody out there to clear away the tracks,” Schmidt says.
The system also features infrared closed-circuit television cameras located every 100 ft or so along the route. When a tilt sensor alerts the control center to a possible problem, the cameras are intended to provide visual confirmation as a backup. During a testing phase, high winds sometimes caused false alarms with the tilt sensors, and high temperatures were found to negatively affect the cameras. But the two technologies complemented each other when combined — and saved the project roughly $500,000 by obviating the need for the concrete barrier wall, Schmidt notes.
This article first appeared in the May/June 2021 issue of Civil Engineering as “Tech Core Transit.”