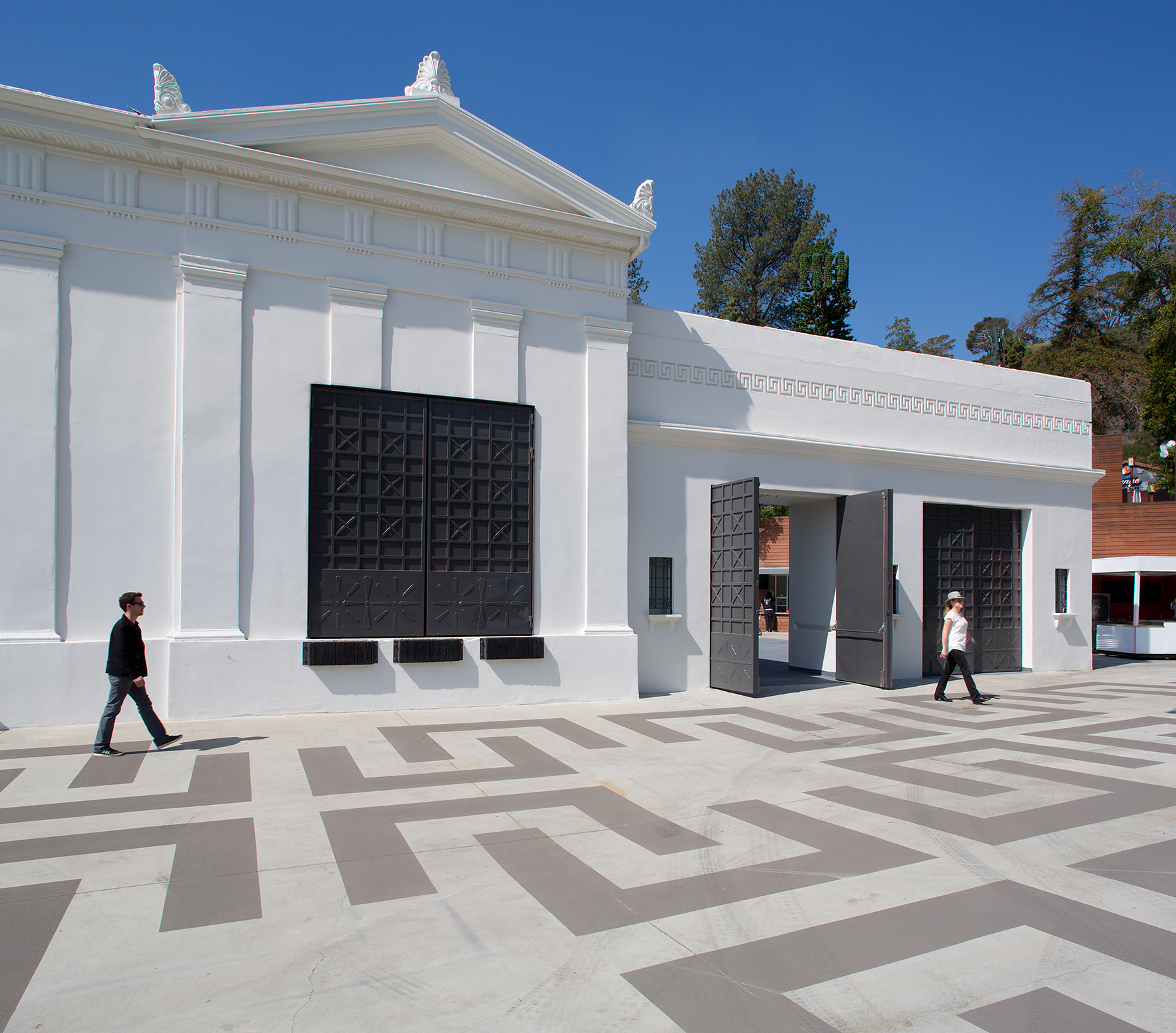
By Robert L. Reid
The Greek Theatre in Los Angeles recently underwent two seismic retrofit projects, one involving the roof over its backstage areas and the other improving two elevated seating terraces. Other work at the open-air entertainment venue included a historical rehabilitation and upgrade to the facilities.
The Greek Theatre, an outdoor concert, performance, and events venue in Los Angeles’ Griffith Park, turned 90 last year. Although the COVID-19 pandemic had temporarily closed the city-owned amphitheater for the 2020 season, which prevented an in-person celebration, the historical site was commemorated in what might ultimately be a more important way: by using the shutdown period to complete a needed seismic retrofit to the theater’s elevated seating terraces.
It was another act in an ongoing improvement project that also featured a separate seismic retrofit to the roof and skylights above the venue’s backstage areas, a historical rehabilitation, and other upgrades that helped prepare the Greek Theatre for when it reopened in August as a safer and more modern facility.
Completed in 1930 — and designed through “an extensive survey of Greek theatres throughout the world,” according to the venue’s website — the Los Angeles Greek Theatre welcomed an audience of nearly 4,000 to its first event in June 1931. Constructed into the base of a steeply sloping hill, the facility originally featured an open-air stage at the eastern end of the site. This stage was surrounded on three sides by concrete-framed backstage areas that were covered by a steel-framed roof structure topped by a thin concrete slab and Greek-style green-glazed terra-cotta tiles. A basement level was located beneath the stage, the surrounding plazas, and the original seating area, which sloped up the hill to the west on a concrete deck. The basement included a parking garage, offices, restrooms, and other amenities.
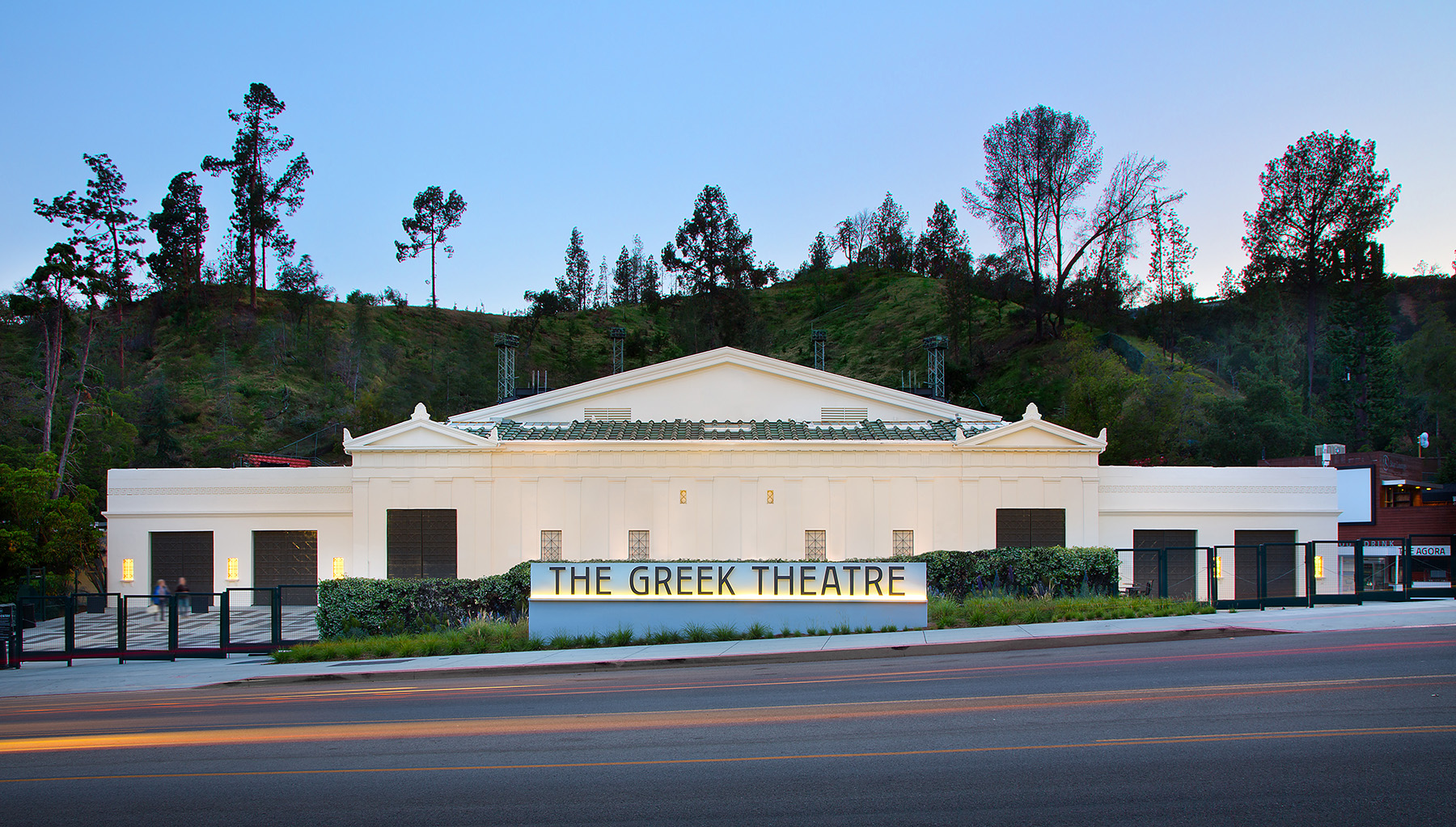
The overall rehabilitation project was led by the Los Angeles-based architecture firm RIOS, which was also responsible for the landscape architecture, interior design work, and other aspects of the project. The client was the Los Angeles Department of Recreation and Parks, which acted as its own general contractor. Miyamoto International, based in Sacramento, California, was responsible for both recent seismic retrofit projects. The Los Angeles office of Page & Turnbull served as the project’s historic architect.
Maintaining the historical fabric
By the 1950s, the Greek Theatre’s originally open stage had been covered by a peaked, steel-framed roof, and during the 1980s, the seating area was expanded with the addition of two sloping steel-framed terraces, one on the north side and another on the south side of the original seating slab, says Ken Wong, P.E., S.E., M.ASCE, a principal at Miyamoto. The venue can now accommodate an audience of approximately 5,900. The parking garage beneath the original seating is not large enough to accommodate modern vehicles and so is now used for storage and other back-of-house functions, Wong adds.
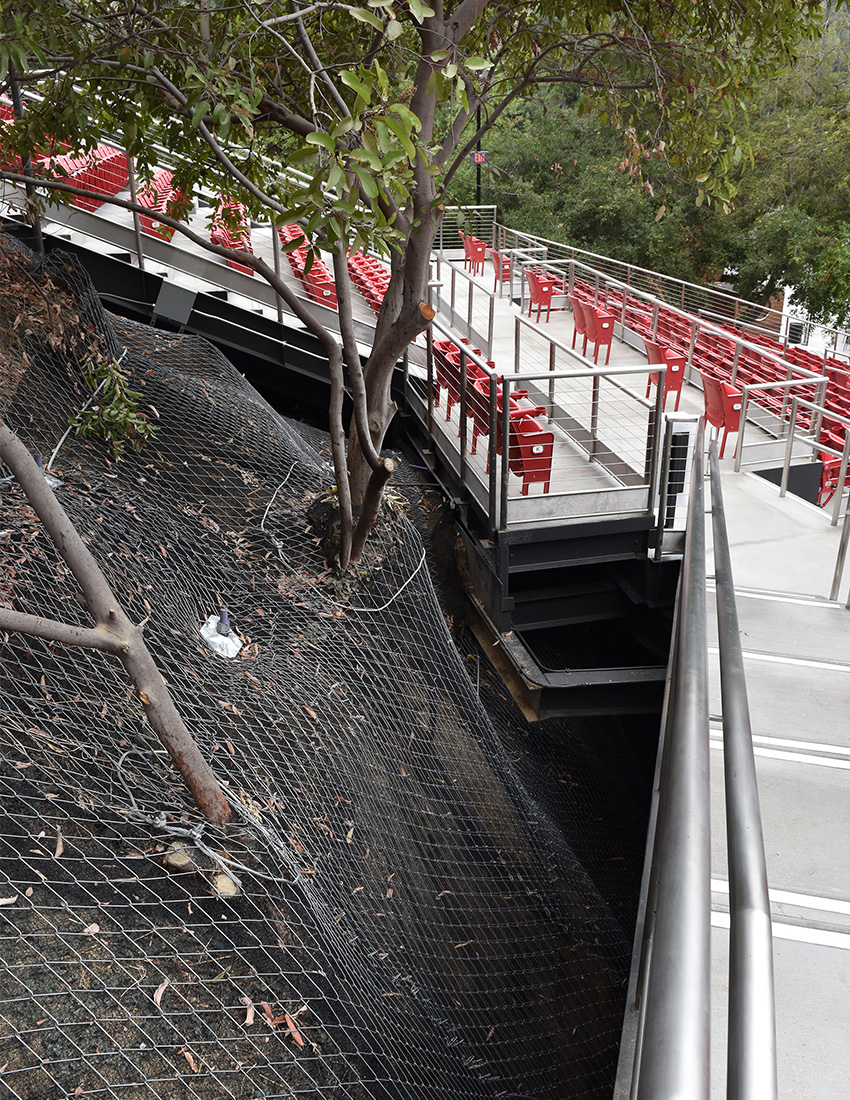
The historical rehabilitation work involving Page & Turnbull began around 2015, and the seismic retrofits involving Miyamoto began in 2017. These projects took multiple years to complete in part because of the complexity of the work but also because the city wanted to keep the Greek Theatre operating throughout these various efforts. “So there was a very short construction window,” says John Lesak, AIA, LEED AP, FAPT, a principal and architect at Page & Turnbull.
Crews could work on improving the theater only from November to April because the theater’s performance season ran from May through October. “So the project was broken up into lots of phases executed over several off-seasons,” Lesak explains.
The initial phases involved a general cleanup of the facility’s exterior spaces. This work comprised extensive repainting — including the addition of a repeating “Greek key” pattern to the site’s concrete entrance plaza to “give the plaza a Hellenic look,” explains the RIOS website. Some large digital signs that “took away from the character” of the neoclassical setting were removed, says Lesak, and the iconic steel doors at the entrance that had become heavily corroded were removed, repaired, repainted, and reinstalled.
The doors swung open and closed on large steel pivot hinges, Lesak notes, which were replaced with stainless steel hinges and bearings to prevent future corrosion. The door surfaces were likewise treated with high-performance paint to protect against rust.
The restrooms, dressing rooms, and other spaces for performers, as well as various amenities for the audience, were also upgraded during the first phases of the project.
Strengthening for seismicity
The seismic retrofit of the original terra-cotta tile-clad roof above the backstage areas was triggered by Los Angeles’ nonductile concrete building ordinance, which applies to buildings constructed prior to 1977 that use a concrete structure as their lateral load-resistance system, says Wong. Such buildings were “constructed to building code standards earlier than the code improvements in 1976,” and thus “are at particular risk for collapse and could pose significant life safety hazards,” according to the website of the Los Angeles Department of Building and Safety.
Although buildings subject to the ordinance have as much as 25 years to complete their retrofits, the ongoing changes to the Greek Theatre made this an opportune time to initiate the backstage roof seismic work as well, Lesak says.
That roof leaked badly, especially around the existing skylights, says Wong. Although portions of the roof system had been repaired several times in the past, the original tiles — now nearly a century old — remained in place but were in poor condition. Made from heavy glazed terra cotta, these tiles measured roughly 2 ft long and weighed as much as 60 lb or more each. The roof featured a combination of overlapping flat-pan tiles and peaked-cap tiles that had originally been anchored to the roof slab by copper wires.
Many of the original tiles were broken, though, and held in place by just their own weight, says Wong. So continuing to use those tiles was no longer possible. Because of the site’s historical nature, however, and the need to obtain approvals from the Los Angeles Office of Historic Resources and the city’s Cultural Heritage Commission, the project had to maintain the theater’s historical fabric as much as possible. But the exact types of tiles from the original construction were no longer commercially available, Wong notes, which meant they had to be replaced with roof tiles that essentially duplicated the original system made with modern fabrication methods.
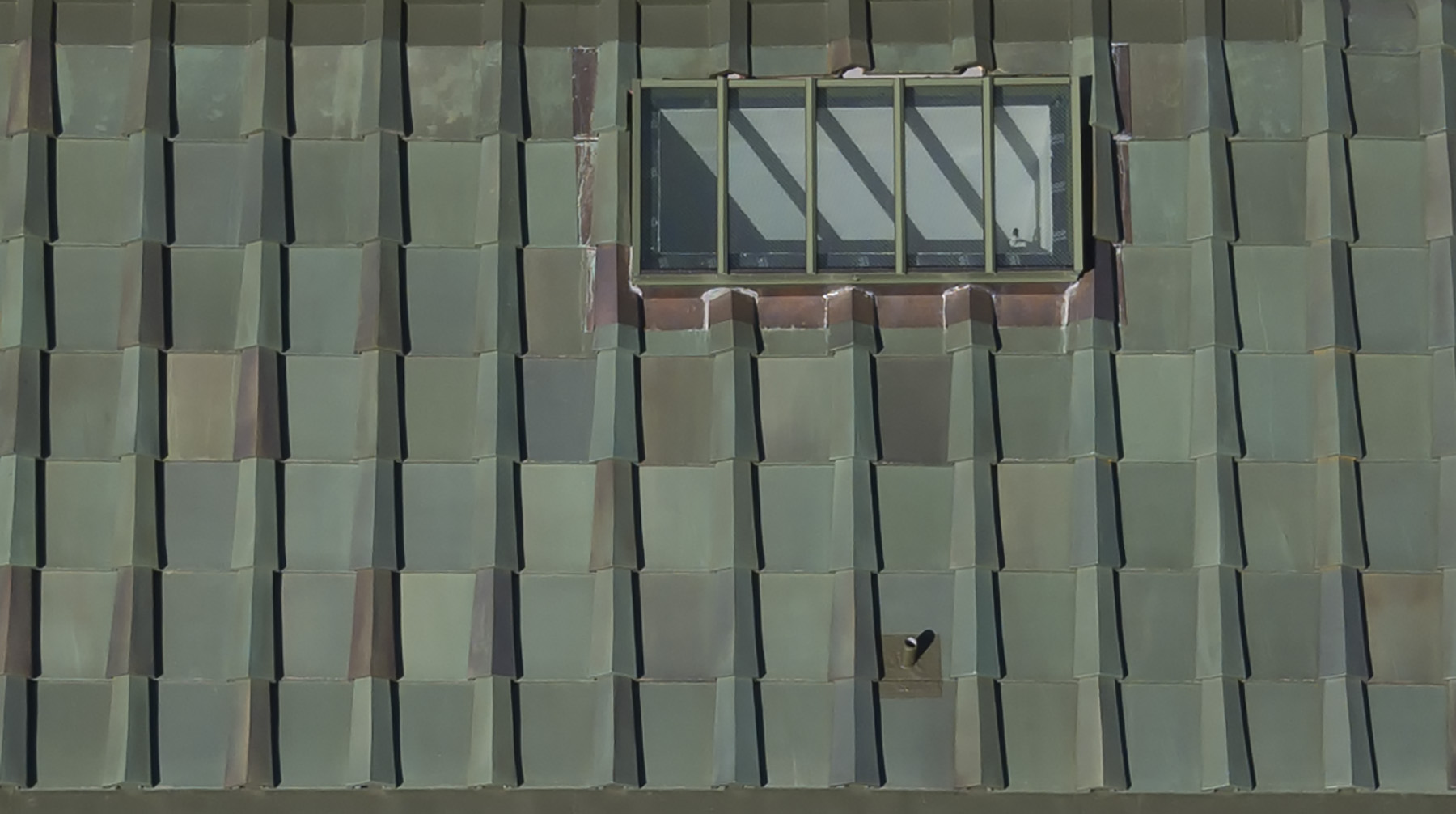
To that end, Page & Turnbull worked closely with MCA Clay Roof Tile, of Corona, California, to create several full-scale mock-ups of the tile layout and sample the possible tile textures and colors. Although the original tiles were produced by hand-packing the clay material into forms, the new tiles were fabricated by a method called slip-casting in which the liquid clay material is poured into a form similar to the way concrete is placed, Lesak says. The process involves a longer drying time than for traditional terra cotta, but the tiles are glazed the same way and the method works well to create the large pieces needed for the Greek Theatre, Lesak explains. The new tiles were also manufactured in advance “so they’d be ready to go once construction started,” he says, which was a vital part of completing the work within the project’s constrained schedule.
Layering reinforcement
Although there are various ways to seismically upgrade a roof, some of the most common methods — such as the use of a horizontal truss — would have been visually intrusive and disruptive to the existing historical fabric of the theater, notes Wong. Instead, crews installed layers of carbon fiber-reinforced polymer across the roughly 6,000 sq ft roof, which was U-shaped in plan and featured several skylights and other openings that required special attention.
The FRP was manufactured and installed by HJ3 of Tucson, Arizona. It arrived in rolls on spindles and was first unrolled and run through a bath of an epoxy adhesive — like wallpaper glue — so that it would adhere to the sloped roof all along its length rather than just in select points, Wong says. The material was applied in strips roughly 3 ft wide and as much as 100 ft long, with multiple layers used where additional strength was required, such as where the side wings of the U met the main portion of the roof, Wong says.
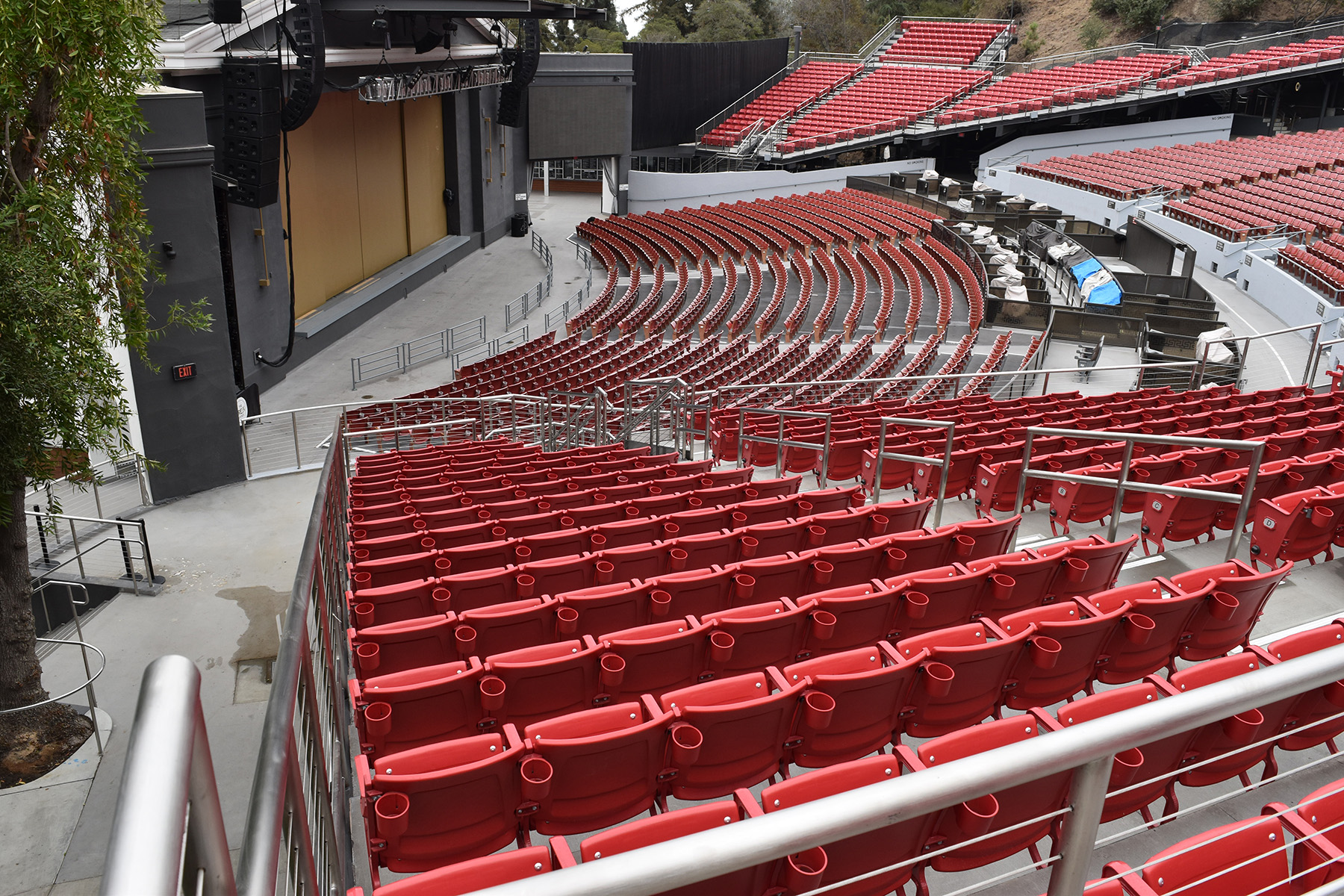
When FRP was first considered, an initial concern was whether the thin concrete deck of the backstage area roof — just 2 in. thick — would be strong enough during a seismic event to transfer loads into the extremely strong layers of FRP. “A lot of the lateral load in a roof system like (the Greek Theatre’s) comes from the walls, which are monolithic with the roof,” Wong explains. “So the loading has to go through the roof slab to get to the FRP.”
If that slab was not strong enough, the FRP might literally tear the roof apart during a seismic event, Wong explains.
Fortunately, laboratory tests determined that the strength of the roof slab concrete was more than sufficient, with a capacity of about 6,000 psi. That was unusually strong concrete for the period when the Greek Theatre was constructed, Wong says, and he speculates that perhaps the original concrete was hand-applied to create an especially stiff mix. Regardless, the existing slab strength made it feasible to use the FRP material.
The skylights as well as two large, louvered openings in the roof — to accommodate a pipe organ that had long since been removed — provided additional challenges, especially with leaking and drainage. But concentrated applications of FRP around the skylights as well as new framing and the installation of high-performance glass resolved any issues with those openings, Lesak says. Likewise, the use of a cricket drainage system atop the louvers — also known as a saddle system — helps divert water to the new roof drains that replaced earlier drains.
The new skylights consist of integrated assemblies attached to the roof by a shallow embedment and post-installed anchors, Wong adds.
Although the thin concrete roof slab could accommodate the layers of FRP, it was not sufficiently thick to anchor the new terra-cotta tiles, Lesak says. The original copper wires could not be reused, and a modern mechanical fastener system would not work well with the FRP. Instead, various solutions were initially considered — “all of which involved either punching lots of holes in the concrete or adding a lot of steel below” the roof, Wong says.
Ultimately, the design team secured the tiles with an adhesive foam that “is primarily used in hurricane areas to keep tiles from blowing off in the wind,” Lesak says. Page & Turnbull had used the adhesive system elsewhere with good results. So it was incorporated into the overall new roof assembly, which consists of the original concrete deck, the new FRP layers, a bituminous layer for waterproofing, and then the adhesive foam and new tiles, Lesak explains.
Tackling the terraces
Because the north and south seating terraces were added during the 1980s, they were not part of the Greek Theatre’s historical fabric, and thus Page & Turnbull was not involved in their seismic retrofit. Instead, Miyamoto worked with the city’s Bureau of Engineering and Department of Public Works on what was a separate contract from the rest of the Greek Theatre rehabilitation and improvements. It was also the most challenging part of the project in terms of engineering, Wong says.
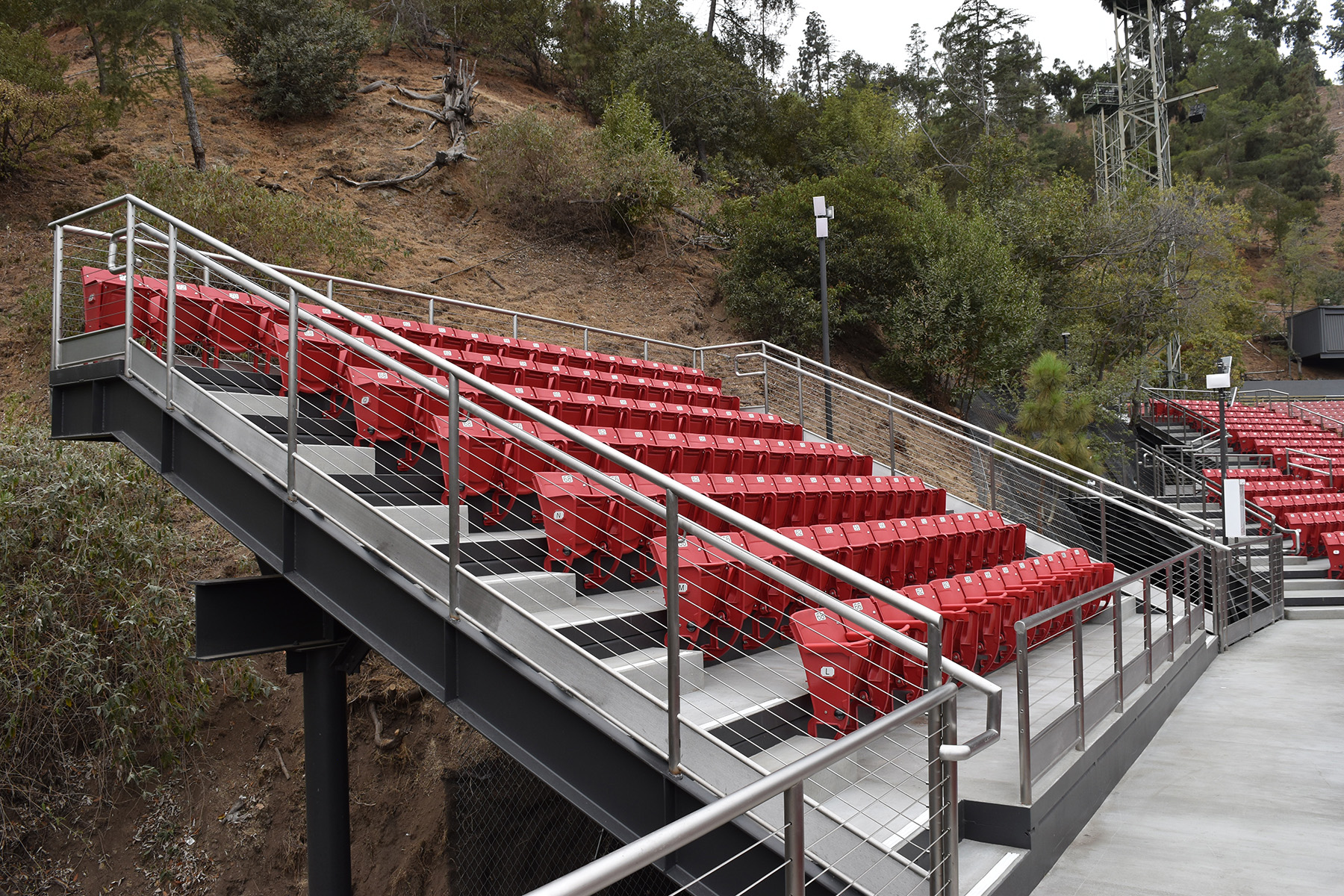
The terraces consisted of two grandstand structures that featured a series of narrow concrete slabs on corrugated metal decks that spanned only a few feet between steel channel risers, which were supported on sloping steel beams and girders, Wong says. Each terrace was supported on about two dozen vertically cantilevered steel columns that — because of the site’s irregularly sloping ground — varied considerably in length. The shorter columns — generally about 4 ft in length — were located close to the stage while the longer columns — approximately 15 ft long — were installed farther back, Wong says. But there were also some shorter columns located farther up the slope, and essentially every column was somewhat different in length from every other column.
Because the terrace decks were heavily corroded at the start of the retrofit — in some places, the metal portions had completely disappeared, Wong notes — Miyamoto’s first work involved emergency repairs to the undersides of those decks. The firm worked with United Riggers and Erectors Inc., of Walnut, California — the terraces’ project contractor — to support the undersides of the aisles and exit ways with angled iron pieces to make sure the system could accommodate the live loads, Wong says.
To establish the baseline conditions at the site, Wood Environment & Infrastructure Solutions — part of John Wood Group PLC, based in Aberdeen, Scotland — conducted geotechnical studies to determine the location of bedrock beneath the terraces as well as the allowable foundation pressures and pile loads, says Wong. These analyses revealed that the extreme variations in column lengths and other factors meant that the terraces “suffer from highly irregular distribution of seismic forces between columns, with nearly all seismic loading resisted by a small number of columns located at one end of the structure,” according to a June 4, 2020, report from the Los Angeles Board of Recreation and Park Commissioners.
Only about four of the 24 columns beneath each terrace — the shortest ones — were handling nearly all the lateral loads, Wong stresses, while the longer columns were experiencing considerable torsional movement. These conditions could have led to “potential failure of the most heavily loaded columns” in the event of an earthquake, the commissioners’ report concluded. Thus the “structures do not meet the life-safety standards of ASCE 41 (Seismic Rehabilitation of Existing Buildings).”
The soil conditions beneath the terraces consisted of an “unknown layer of fill you couldn’t rely on” to depths of 15 to 20 ft below grade, Wong notes. Moreover, the geometry of the terraces was not well documented, and many of the existing connections within the structures appeared to have been improvised in the field, he adds.
The seismic solutions involved the installation of a series of buckling-restrained braced frames to “restrain the areas that are most susceptible to movement,” Wong says. The idea is to make the whole structure move uniformly along its axis in an earthquake instead of twisting, he explains. Concrete grade beams were also used at the ground level to tie the columns together and better distribute the lateral loads — a feature the original system had lacked. In addition, sliding connections were installed at the tops of some of the shortest columns, Wong says.
The original steel risers and concrete decks were also replaced, and much of the work was performed beneath plastic tarps because of the presence of lead paint on the old structures.
Reopening and recognition
Although the ongoing pandemic pushed back the planned reopening date for the Greek Theatre from spring to summer 2021, the venue was operating again at press time, providing a more attractive — and seismically safer — space for Angelenos to gather for entertainment and events.
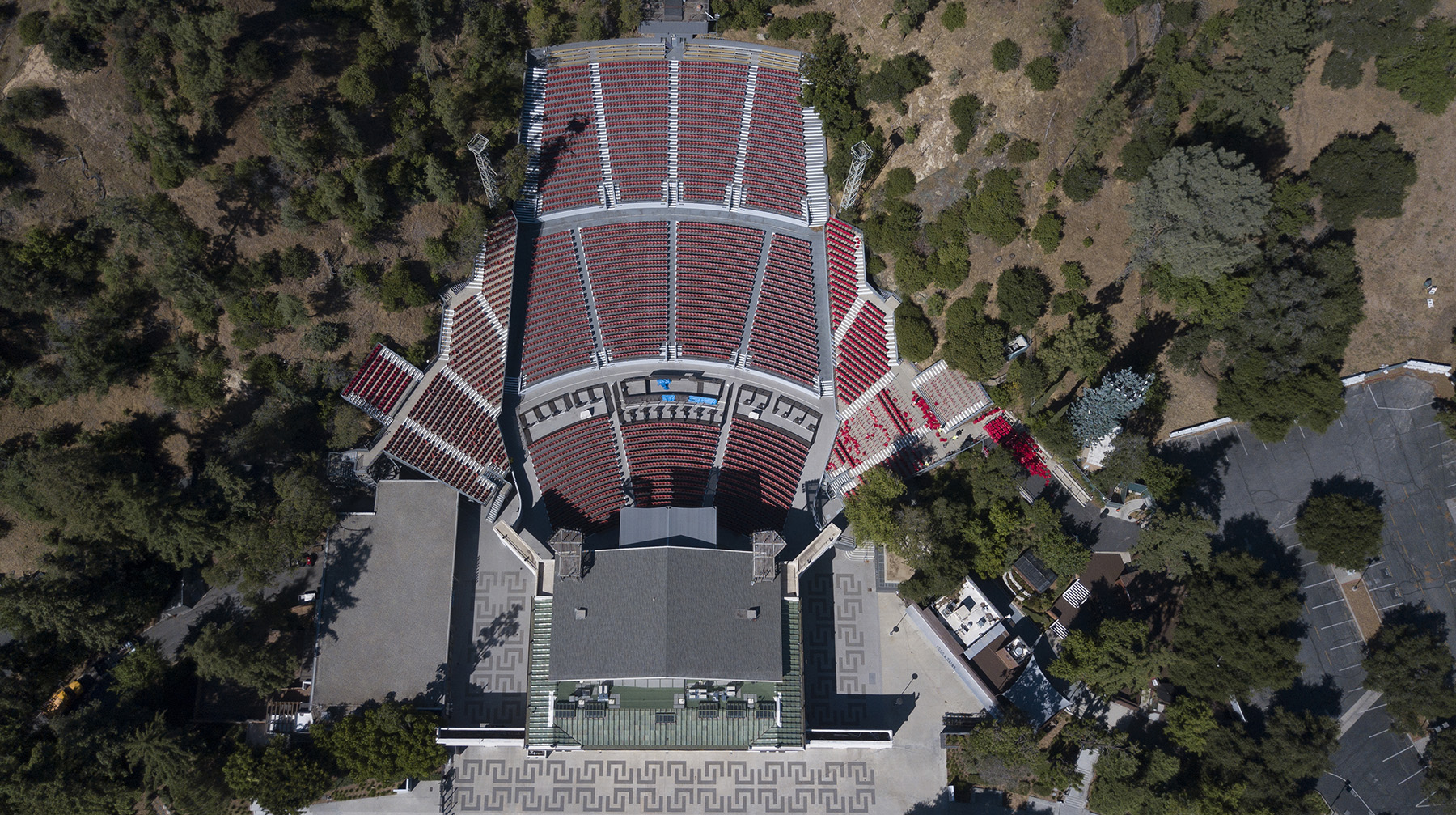
For Wong, the project helped demonstrate that the FRP material is “a great tool to use for strengthening existing buildings without being too intrusive and without doing too much damage to historic fabrics.” Clearly, a panel of his peers agreed: The Greek Theatre rehabilitation project was honored with a 2020 Preservation Design Award for Rehabilitation from the California Preservation Foundation, as determined by a jury of top professionals in the fields of architecture, engineering, planning, and history.
Robert L. Reid is the senior editor and features manager of Civil Engineering.
PROJECT CREDITS
Owner and general contractor: Los Angeles Department of Recreation and Parks
Rehabilitation project director: RIOS, Los Angeles
Historic architect: Page & Turnbull, Los Angeles office
Seismic retrofit consultant: Miyamoto International, Sacramento, California
Geotechnical engineer: Wood Environment & Infrastructure Solutions, part of John Wood Group PLC, Aberdeen, Scotland
Tile manufacturer: MCA Clay Roof Tile, Corona, California
Roofing contractor: Best Contracting Services Inc., Gardena, California
Door restoration contractor: K.C. Restoration Co. Inc., Gardena, California
Fiber-reinforced polymer manufacturer: HJ3, Tucson, Arizona
Terraces contractor: United Riggers and Erectors Inc., Walnut, California
This article first appeared in the November/December 2021 issue of Civil Engineering as “A Seismic Double Bill.”