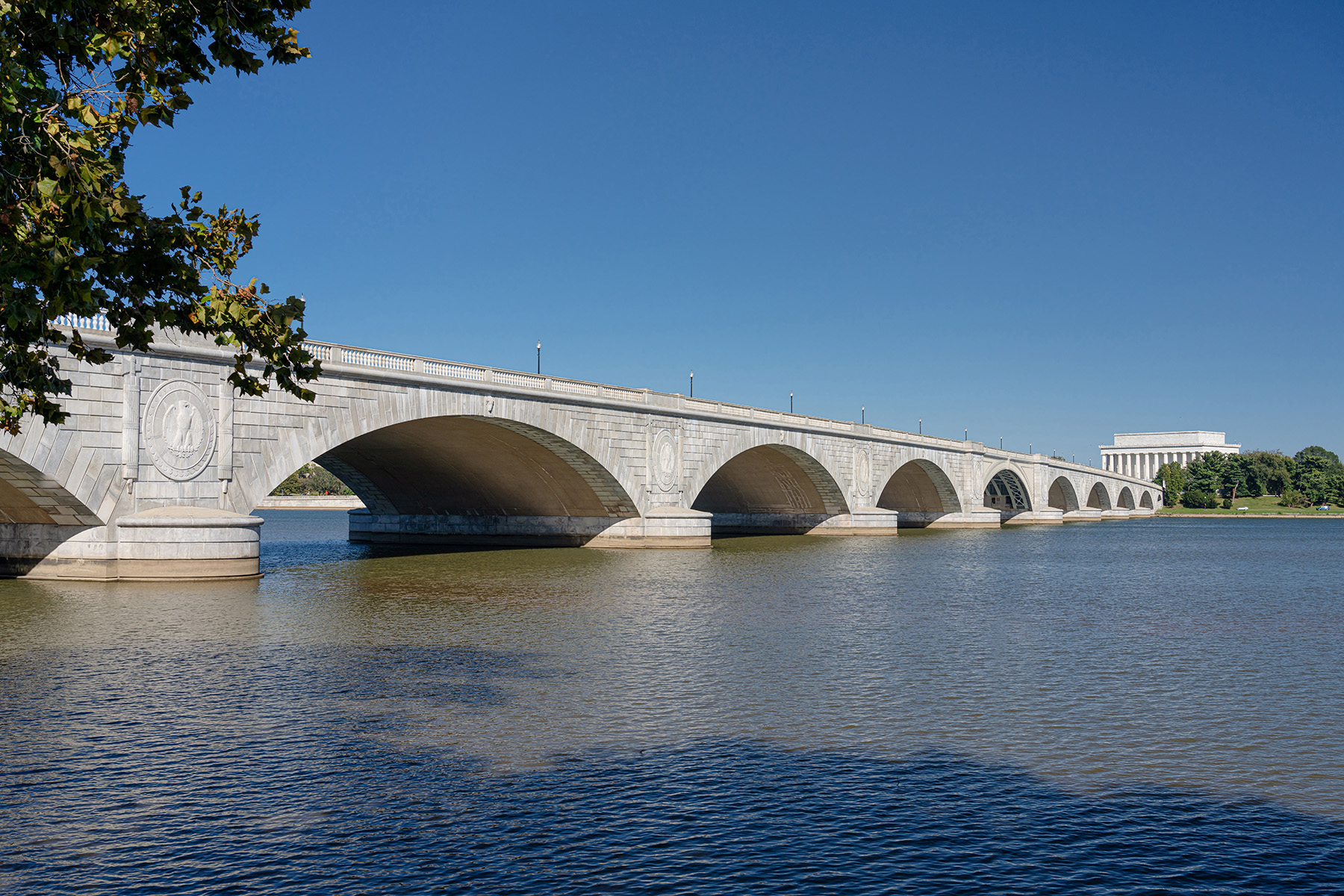
By Donald Arant and Vicki Kramer
Threatened with closure because of corrosion and other deterioration, the Arlington Memorial Bridge in Washington, D.C., was renovated and rehabilitated with innovative design and construction practices. The iconic crossing will continue to serve as both a major commuter route and a ceremonial entrance to the nation’s capital for years to come.
The Arlington Memorial Bridge is an iconic piece of the nation’s infrastructure. Serving as a key connector across the Potomac River between the Lincoln Memorial in Washington, D.C., and Arlington National Cemetery in Virginia, this historic 89-year-old structure was recently rehabilitated using creative design and construction practices that will preserve the bridge for future generations. The National Park Service owns the structure, and the Federal Highway Administration’s Eastern Federal Lands Highway Division — which inspects the NPS’ bridges — administered the rehabilitation project.
Kiewit Infrastructure Co., part of Omaha, Nebraska-based Kiewit Corp., was the design-build contractor on the $227 million effort. AECOM, now based in Dallas, served as the lead designer, with assistance from New York City-based Hardesty and Hanover.
Iconic structure
Designed by the New York City architecture firm McKim, Mead and White, the Arlington Memorial Bridge opened in 1932 as “a memorial to the sacrifices of our nation’s veterans and as a symbol of the reconciliation between north and south following the American Civil War,” explains an NPS website about the rehabilitation project. The iconic, neoclassical structure connects the District of Columbia on the east side of the Potomac River, with Virginia on the west side, carrying more than 68,000 vehicles daily on six lanes, each 10 ft wide.
Measuring 2,162 ft long and 94 ft wide, the bridge is a structural masterpiece that features 10 reinforced-concrete arch approach spans. When first built, the bridge also featured a 216 ft long double-leaf bascule span at the crossing’s center, designed by Strauss Engineering Co., of Chicago. At the time of its completion, it was the longest, heaviest, and fastest-opening drawbridge in the world.
Eight of the bridge’s approach spans are cast-in-place deck arches located over the Potomac. The other two approach spans are smaller concrete arches that cross roadways on either side of the river — one on the west end spanning a portion of the George Washington Memorial Parkway and the other on the east end crossing Ohio Drive.
Although it was originally designed as a drawbridge, the double-leaf bascule span has not been opened since 1961, because other bridges constructed across the Potomac over the years — upstream and downstream of the Arlington Memorial Bridge — have reduced the clearances for boat traffic on the river.
Discovering deterioration
The project was the first major rehabilitation of the Arlington Memorial Bridge since its opening, but the need for such work had been anticipated for some time. Moderate deterioration of some steel members and spalling concrete were detected in 2003 during what was then a biennial inspection by the FHWA. By 2009, however, the problems had become severe enough for the highway administration to start inspecting the structure annually, with some portions of the bridge inspected even more frequently because of corrosion.
Underwater inspections in 2012 and 2014 — conducted by Clark Nexsen, of Virginia Beach, Virginia — revealed evidence of scouring of the bridge’s concrete piers as well as undermining issues on two piers.
In 2015, severe corrosion was detected in the bridge’s structural and reinforcing steel, with the loss of steel exceeding 80% in some areas and even reaching 100% in certain locations. A closer look revealed that secondary load-bearing support beams, located at the bascule span, were corroding at a faster rate than anticipated and no longer met load-bearing standards, according to FHWA inspection officials. As a result, two curbside lanes of traffic, as well as parts of the adjoining sidewalks, were temporarily closed.
A $4 million, yearlong effort addressed the corrosion in the bascule span, enabling the curbside lanes to reopen. But weight limits were imposed to safeguard the overall structure, and the need for a more comprehensive rehabilitation of the bridge was evident. Without such an effort, “the bridge would have been required to close to all traffic in 2021 due to continued deck deterioration,” according to the NPS website.
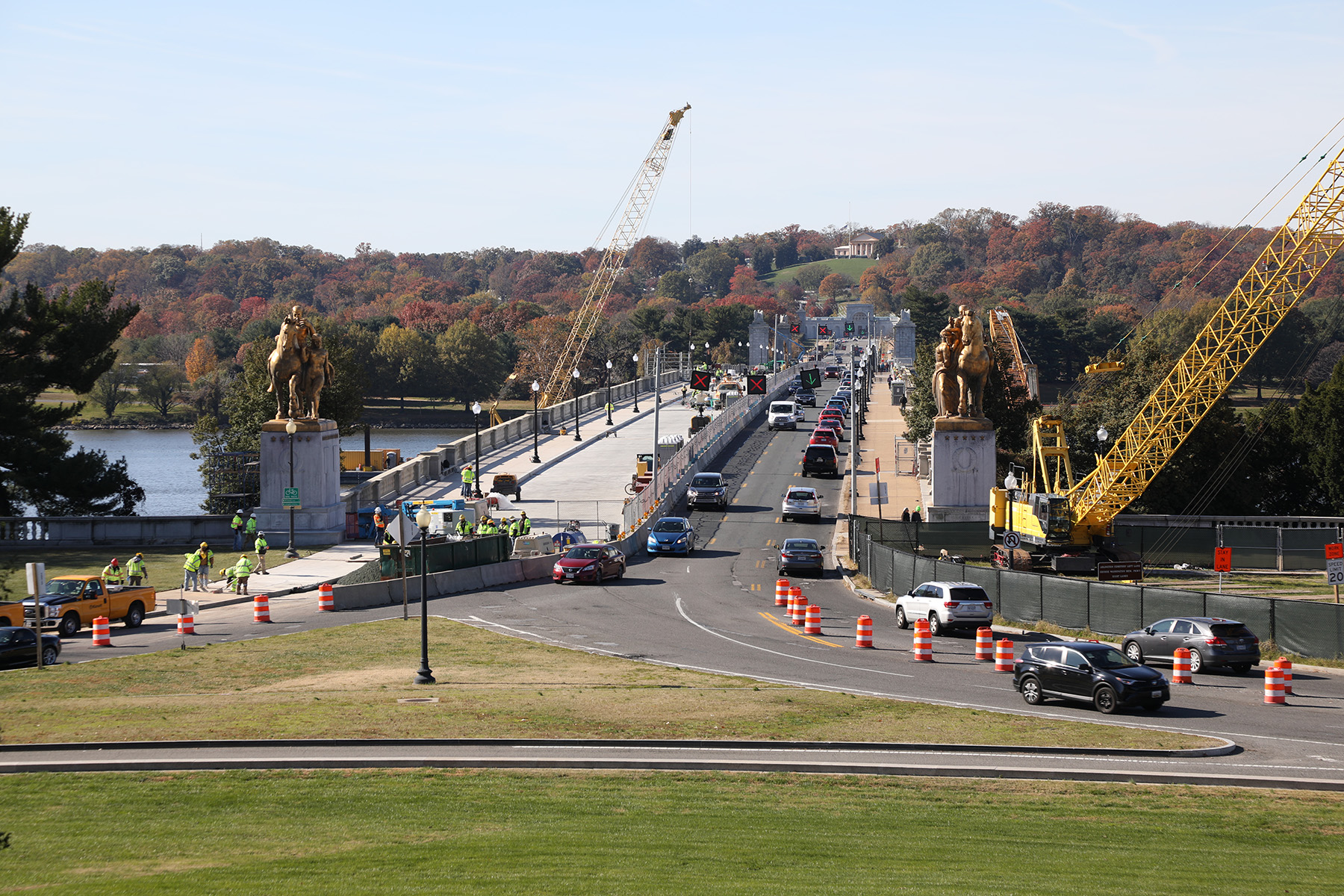
A thousand-day effort
The Arlington Memorial Bridge rehabilitation project is one of the largest infrastructure projects in NPS history, focusing on a combination of replacement and restoration to preserve the structure’s original character. Most significantly, the now unnecessary bascule span was replaced with a new span composed of variable-depth steel girders. The method used was cost-effective and did not require a long-term full closure of the bridge. Instead, half the bridge (lengthwise) was worked on at a time, keeping at least three lanes of traffic open at all times.
Two schedules were ultimately considered for the project: a 1,550-day calendar, which would divide the project into multiple phases based on the levels of funding that could be secured at different times, and a 1,000-day calendar that was the best-case scenario, in which the entire project would be fully funded from the start. Fortunately, the 1,000-day schedule prevailed, which saved taxpayers millions of dollars and cut 1.5 years off the projected construction time.
One of the initial challenges for the project team was that potential contractors had only been allowed to examine the interior of the bridge once, which meant that the design-build team first had to validate the preliminary engineering, conceptual designs, and constructability proposals. Those initial proposals also involved separating the bascule portion of the work from the rest of the bridge rehabilitation. But the fully funded, 1,000-day schedule meant that work on the drawbridge and the approach spans could take place concurrently.
Repairs and rehabilitation
Key aspects of the rehabilitation project included:
- Repairing the concrete arch spans, concrete bridge piers, and bridge railings and other nonstructural components. Crews also repaired or replaced the existing access hatches, ladders, and personnel platforms for inspection and maintenance access throughout the bridge as needed.
- Cleaning and repairing sections of the stone facade that adorns each side of the concrete arch spans as well as the existing bridge drainage system.
- Replacing expansion joints and bearings, the bridge deck and sidewalks, and the existing exposed aggregate sidewalks; the sidewalks were replaced with similar materials.
- Removing the granite curbs along the roadside edge of the sidewalks and resetting them as the new bridge deck and sidewalks were installed.
- Removing light poles prior to the removal of the existing bridge deck and sidewalks and then painting and resetting them with new sidewalk construction.
- Installing an upgraded lighting system with conduits inside each arch span to conform to current electrical standards.
(For a more detailed look at the structural aspects of the project, see “An almost invisible engineering effort,” in the sidebar below.)
New deck design
The work on the bridge deck and sidewalks was critical to the project, involving the replacement of the existing concrete bridge deck with a concrete deck designed to minimize water intrusion. The new deck features a latex-modified concrete overlay that the NPS and the FHWA specified because it was a long-lasting material that provided a good wearing surface for the bridge, matched the look of the existing deck surface, and was lower in cost than other options.
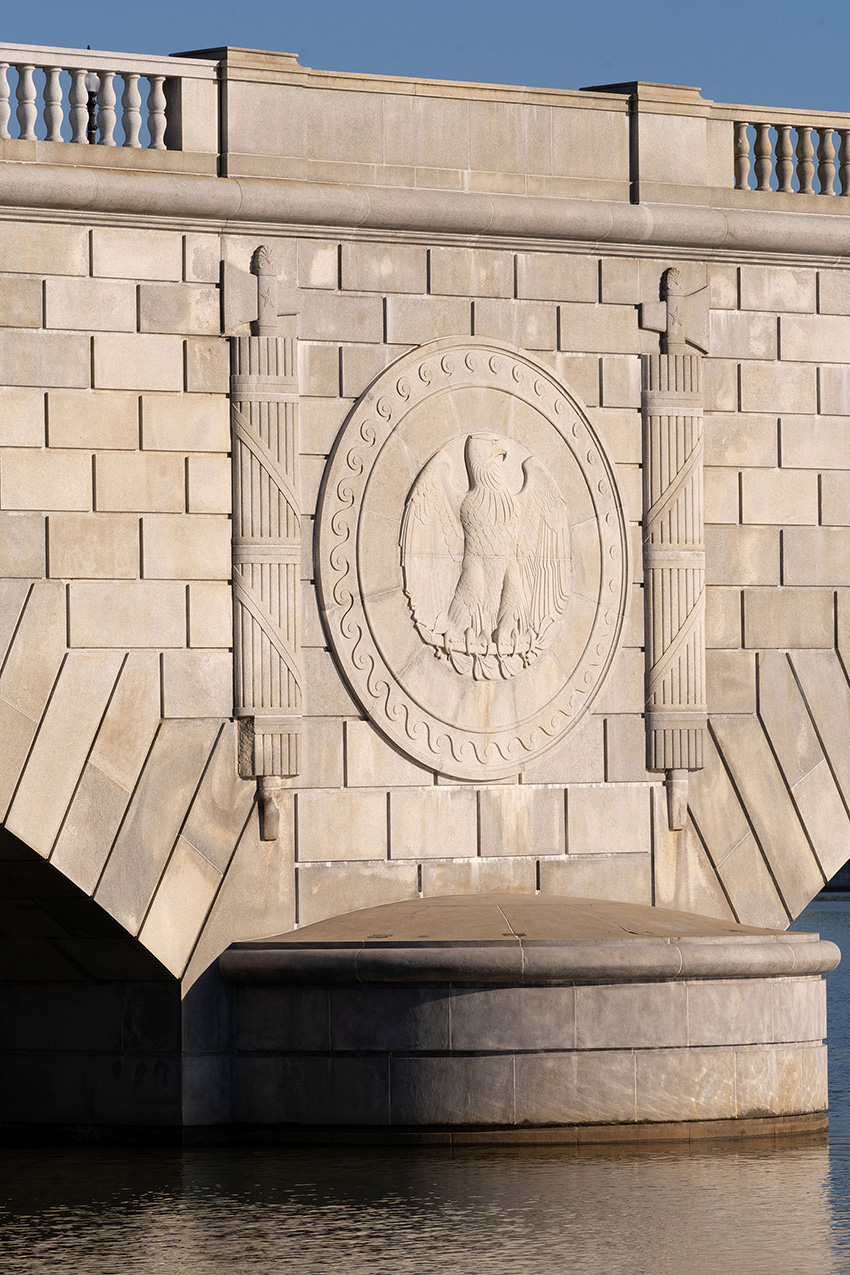
The original deck and sidewalk were made from cast-in-place concrete. The new sidewalks were again made from CIP concrete, but the new deck was made from 450 high-performance precast-concrete panels, each measuring 44 ft by 10 ft and featuring stainless-steel reinforcement.
Setting the new deck panels in place while maintaining traffic on the bridge could have been a challenge. But Kiewit’s in-house engineering group — Kiewit Infrastructure Engineers — designed a temporary trestle system that operated a 200-ton crane. This crane picked up the precast panels from the active roadway during the night shift and maneuvered them into place.
Another major component in the deck rehabilitation involved the replacement of the badly deteriorated concrete pier frames with new columns and pier caps. The new frames were installed on the exterior of the original frames, which allowed access to the interior of the drawbridge throughout the duration of the project. Small portions of the deck were removed so that the new columns and caps could be placed. Then the old frames were removed, and the new beams and deck were installed.
Preservation efforts
Kiewit and its partners were dedicated to the balance of preserving as much of the bridge’s original structure as possible while incorporating engineering and construction materials and methods that would extend the life of the crossing. To that end, local architecture firm Quinn Evans was brought on to guide the historic design of the rehabilitation.
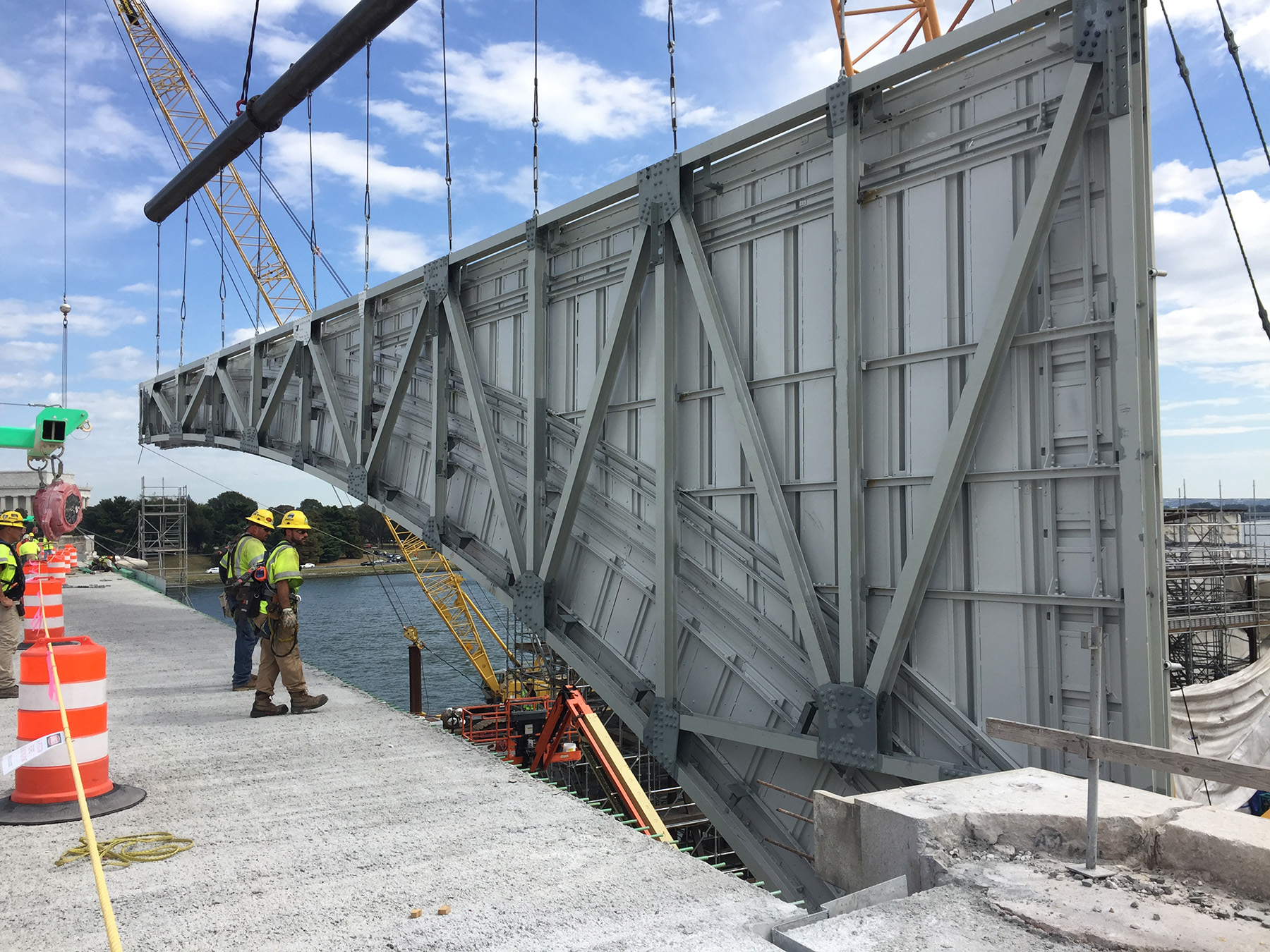
Prior to the rehabilitation, the bascule section consisted of riveted steel trusses supported on riveted steel trunnion posts with counterweights below the deck. The original design also featured exterior fascia girders with floor beams to hold up the structure.
To preserve the original appearance of the drawbridge, the bascule section was replaced with a new fixed-span section that features 216 ft long steel girders, each weighing 170,000 lb. Once these girders were installed, a system of steel trusses was added beneath the new girders to mimic the original design.
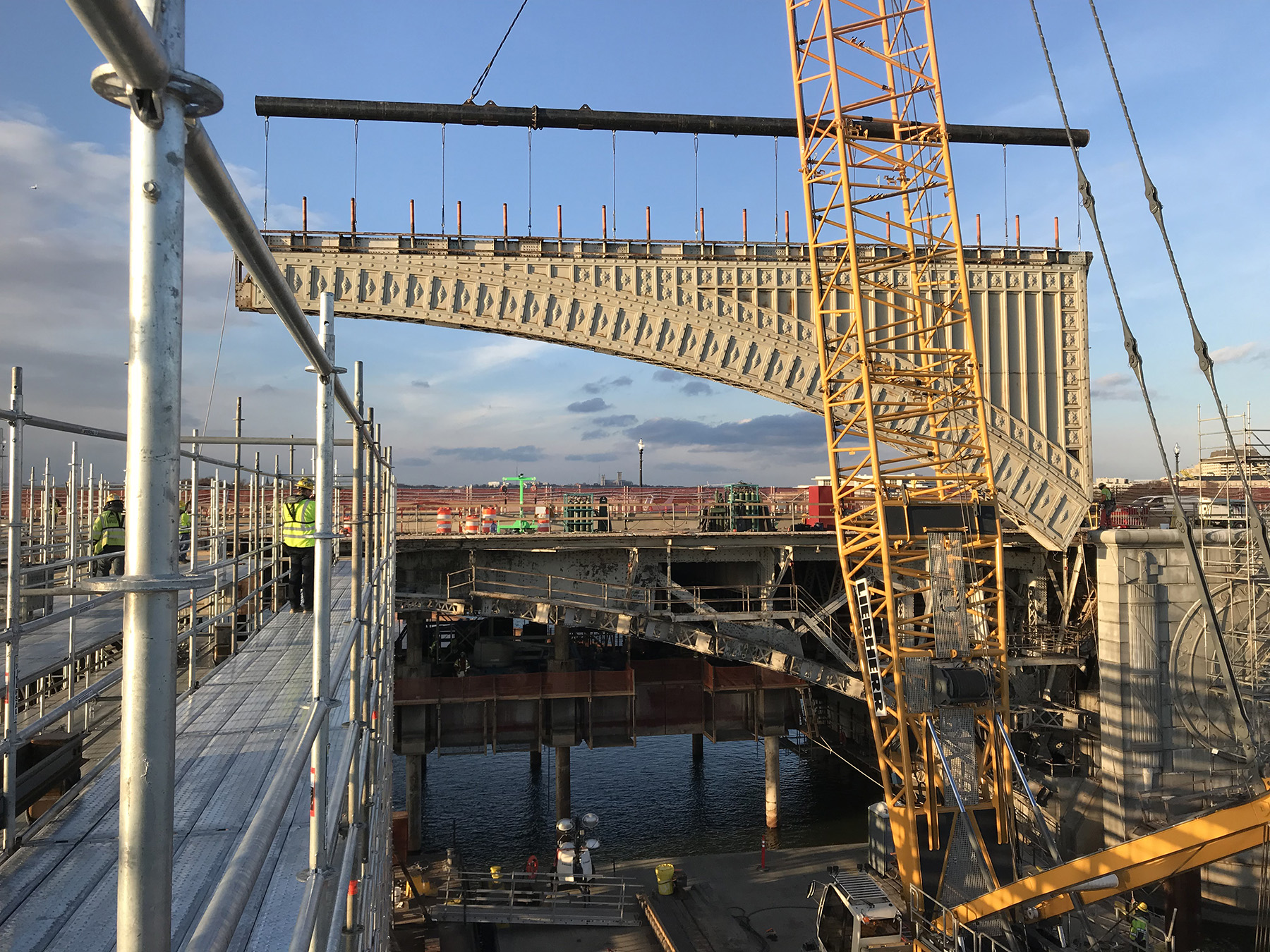
Additionally, the NPS considered the original bollard pop-up protective posts — used to stop traffic when the drawbridge was open — to be a historic element. The design-build team worked with NPS historic preservation specialists to keep the bollards in the rehabilitated bridge structure. The original bascule machinery and machinery rooms were also preserved.
Supporting structure
Because traffic had to be maintained on the bridge during the replacement of the bascule section, the drawbridge portion was cut in half lengthwise while an in-water shoring system held up the halves of the structure. Traffic continued to move across three lanes, first on one side of the bridge, then on the other.
To support the bifurcated structure, Kiewit Infrastructure Engineers designed a jack-up barge using 22 barges with shoring towers supported on a pipe-pile system to create a working platform atop the water. The barge supported the drawbridge’s floor beams, allowing the bascule portion to be cut in half lengthwise while live traffic drove overhead. The concept required significant engineering reviews at multiple levels to ensure the safety of the traveling public and construction staff. This unique solution facilitated schedule and operational efficiencies that supported an aggressive completion deadline and minimized impacts to motorists and pedestrians.
Facade features
Though most of the detail of the arch bridge is in the granite facade, the face of the drawbridge has a detailed metal facade that was covered in corrosion and rust. The team built a custom cradle on the barge to allow the facade to be repaired and restored as a complete unit, maintaining the integrity of the original pieces and making reassembly much easier. Pieces were sandblasted, and the entire structure was repainted.
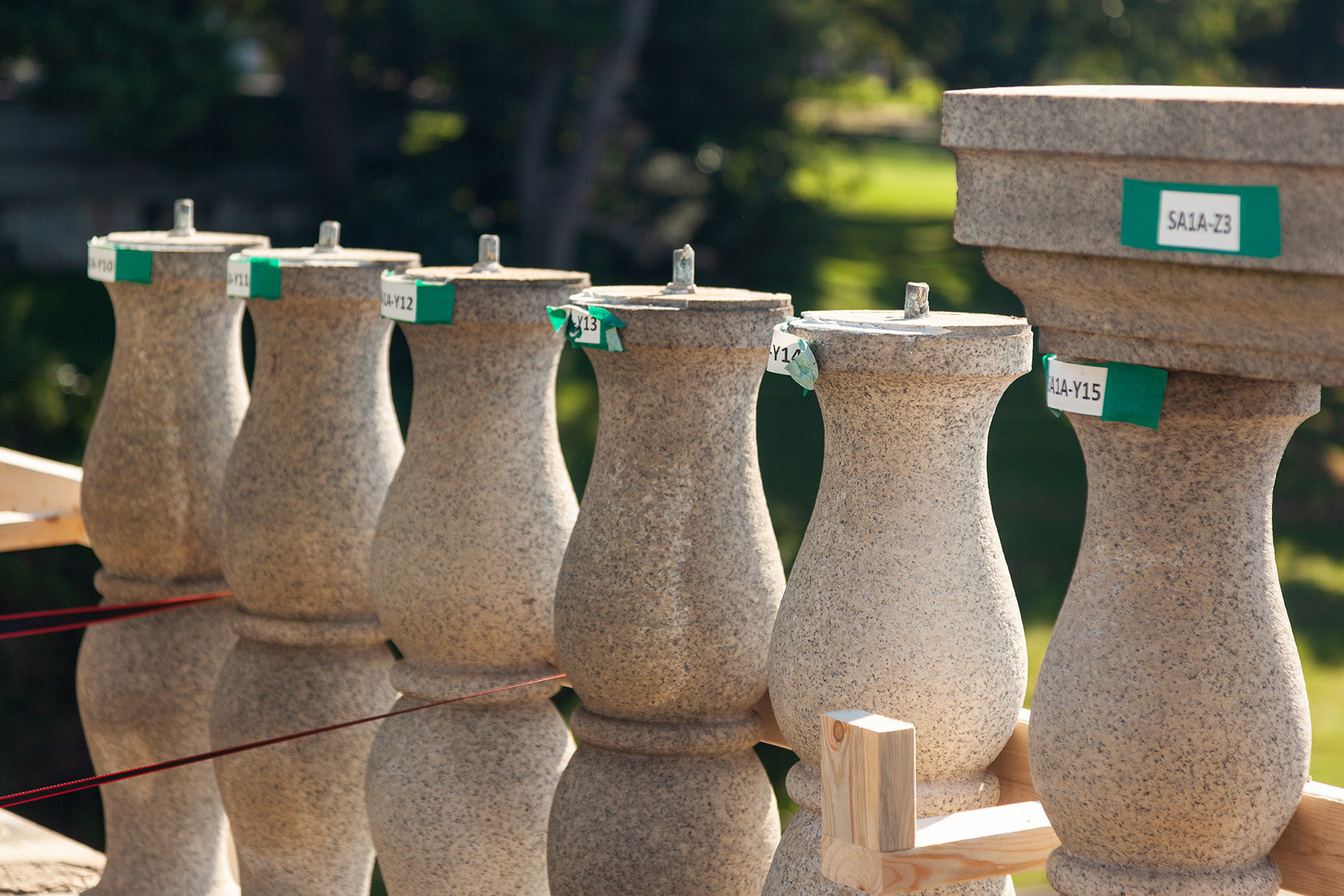
Kiewit enlisted the expertise of Lorton Stone LLC, of Newington, Virginia, to assist with the inventory and cleaning of thousands of granite balustrades before carefully restoring them to their home on the face of the drawbridge. More than 5,000 pieces of stonework were removed and cleaned at an off-site facility. Every piece was cataloged, refurbished, and replaced in its original position. Throughout the process, Kiewit worked closely with the NPS and the FHWA on every detail of the project to ensure that the integrity of the bridge was maintained and history preserved.
Reopening for the future
The rehabilitated Arlington Memorial Bridge was fully reopened to the public on Dec. 4, 2020. Because the design-build team’s innovative solutions obviated the need for a long-term closure of the bridge, the plan prevented an adverse economic impact on the region that the Metropolitan Washington Council of Governments estimated could have cost more than $74 million a year in traffic delays alone.
Because of the support of the FHWA and the NPS, the design-build team was able to adopt novel engineering strategies that delivered the project under budget and ahead of schedule. Officially, the bridge should now enjoy at least another 75 years of useful life. But even more, the project “will give new life to our capital’s ceremonial entrance while respecting its character, history, and national significance,” the NPS concludes.
Donald Arant is a project manager and Vicki Kramer is the business development and government affairs liaison for Kiewit Corp., of Omaha, Nebraska.
PROJECT CREDITS
Owner: National Park Service
Rehabilitation project administrator: Federal Highway Administration, Eastern Federal Lands Highway Division
Design-build team lead: Kiewit Infrastructure Co., Omaha, Nebraska
Lead designer: AECOM, Dallas
Design consultant: Hardesty and Hanover, New York City
Historical architect: Quinn Evans, Washington, D.C., office
Precast deck panels: PennStress, Roaring Spring, Pennsylvania
Granite restoration: Lorton Stone LLC, Newington, Virginia
Metal restoration: Allen Architectural Metals, Talladega, Alabama
Latex modified concrete overlay: Wagman Inc., York, Pennsylvania
Underwater inspections: Clark Nexsen, Virginia Beach, Virginia
SIDEBAR
An almost invisible engineering effort
The structural repairs to the Arlington Memorial Bridge were designed to restore the crossing without calling attention to any changes.
By Robert L. Reid
The restoration of the Arlington Memorial Bridge had to be completed within a tight, 1,000-day schedule, with traffic continuing to drive across the structure throughout the project. But the design-build team did get some initial assistance from a somewhat unexpected source.
The National Park Service and the Federal Highway Administration’s Eastern Federal Lands Highway Division — the bridge’s owner and the administrator of the rehabilitation project, respectively — developed the design documents to roughly 60% completion before the design-build contract was awarded. For Ken Butler, P.E., the chief bridge engineer for AECOM’s North American Complex Bridge Practice, this was only the second time in more than 20 years of working on alternative delivery projects that he had seen clients initiate that level of design development.
Dallas-based AECOM was the lead designer on the bridge rehabilitation project, which was led by design-build contractor Kiewit Infrastructure Co., of Omaha, Nebraska.
Butler says that the NPS and FHWA had “obviously put a lot of thought into the project.” Both agencies were “excited to have the project underway” on one of the “crown jewels” of the NPS’ bridge program, which maintains more than 1,450 structures across the nation, he notes. Of course, such a high level of client interest and involvement also meant that the project faced a high level of complexity. “We were supposed to reconstruct (the bridge) and make it structurally sound again — but in a way that would not let anyone know we’d been there,” Butler explains.
Steel sides
This almost invisible engineering effort was intended to match aspects of the bridge’s original design. Although the majority of the crossing’s 2,162 ft length features concrete framing with a granite facade, the center portion of the structure was a steel-framed double-leaf bascule span 216 ft long. But viewers had to look at the bridge very closely to identify the point at which the granite section ended and the steel portion began, Butler says. “The reason your eye (didn’t) pick up the difference,” he explains, “is that there was a steel fascia designed by the architects in the 1930s to make (the bascule section) look like the granite facade.”
Although the bascule span itself was scheduled to be replaced, the steel fascia had to remain after any corrosion or other damage was repaired — which initially seemed difficult to achieve, Butler concedes. “We weren’t exactly sure how to approach removing (the fascia) from the bascule span,” he says. “We thought we might have to take it apart in pieces.”
But once the design-build team was able to examine the fascia system closely — after having had only limited access prior to being awarded the contract — it determined that it was possible to remove each of the four fascia panels as intact sections from each side of the bascule’s double-leaf span. A Kiewit-designed system of barges and a steel-framed platform afforded the design-build team access to remove the steel fascia sections and transport them to the Virginia side of the river, where the repair work was taking place.
On shore, the sections were then encapsulated so that the old lead paint could safely be removed and the corroded pieces refurbished. The restored fascia was then floated back out to the bridge and reattached to the structure — only now the sections were supported on the new fixed steel girders that had replaced the bascule section.
Since the new girders even mimic the arch of the bascule span, no one can tell that the drawbridge portion has been removed, Butler says. “They will see the same fascia they did before.”
Concrete solutions
When the concrete portions of the bridge were closely examined, they turned out to be “both in excellent condition and fully degraded” — depending on which piece was examined, Butler says. The longitudinal spandrel walls and transverse cross walls along the structure were in good shape, he explains. But the concrete frames in the arch piers were contaminated with chlorides and deteriorated due to decades of deicing salts that had leaked through the deck, seeped into the concrete, and corroded the reinforcing steel.
“As the rebar rusts, it swells, and that expands the concrete and causes spalling,” Butler says. Although the bridge could tolerate small amounts of such corrosion, that spalling led to more extensive delaminations that began to cause a loss of the structural section. “Basically, the continued loss of section over the decades had a direct impact on the concrete frames’ ability to carry and transfer load,” Butler explains.
The pier frames were replaced with new concrete supports using high-performance concrete and epoxy-coated reinforcing steel. Work crews installed a passive cathodic protection system in areas of the bridge along the cross walls that showed signs of chloride contamination. The drainage scuppers within the arch piers were repaired and unclogged.
In addition, the NPS and the FHWA specified a low-permeability, high-performance concrete for the new deck panels along with stainless reinforcing steel. An even higher-end material — a 21,000 psi ultra-high-performance concrete — was selected for the closure joints between the deck panels, and a 2 in. thick latex-modified concrete overlay was used to help prevent future ingress of deicing salts into the structural system.
Honoring the past
From an engineering point of view, the Arlington Memorial Bridge rehabilitation was somewhat unique in that “we were afforded the opportunity to put really high-end materials into the bridge,” Butler says. This is especially useful on complex bridge projects that carry high traffic volumes and have the potential to disrupt daily commutes during rehabilitation. It’s better to use higher-end materials initially for the sake of longevity and life-cycle maintenance costs, he explains, rather than risk the need to “go back and rehab it again.”
Butler praised the original engineers and architects for their wonderful design and great craftsmanship. “I’d like to think that we came in as a design-build team and honored that,” Butler concludes, adding that the historical significance of the Arlington Memorial Bridge “warranted the best we could possibly do as engineers.”
Robert L. Reid is the senior editor and features manager of Civil Engineering.
This article first appeared in the January/February 2022 issue of Civil Engineering as “Innovating to Preserve.”