Edited by Laurie A. Shuster
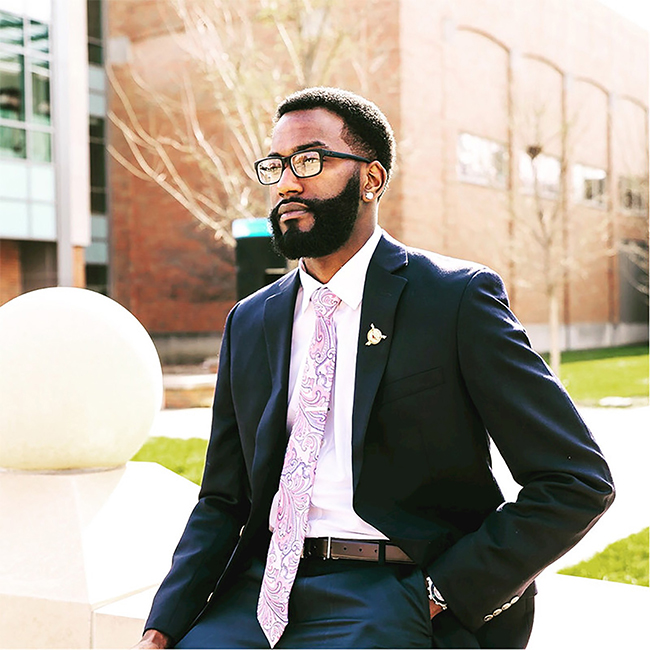
Timothy Alston, A.M.ASCE, is a busy man. Named one of ASCE’s New Faces of Civil Engineering, Professional, in 2021, Alston also serves as a committee member on ASCE’s Members of Society Advancing an Inclusive Culture and is an active member of the National Society of Black Engineers and the Illinois Section of ASCE. In summer 2020, he faced a pandemic-related layoff from his first full-time engineering job, at CDM Smith in Chicago. Undaunted, Alston networked his way to the flip side of the engineering world — the client side — and within a month had landed a new job, as a plant engineer for the Gary Sanitary District. There he optimizes plant processes and volunteers ideas to make improvements wherever he can. Alston also works part time for SMASH, a nonprofit academic acceleration program for high school students from traditionally underrepresented populations who show aptitude in STEM (science, technology, engineering, and mathematics). As an admissions coach, he helps students from three states who are graduating from SMASH’s three-year program create successful college applications.
Like many others, you faced a layoff during the height of the COVID-19 pandemic. How did you bounce back from that so quickly?
As an environmental consultant at CDM Smith, I had been coordinating a project with the Gary Sanitary District. I was helping set up hazardous materials surveys during preconstruction of a project. I had visited the site several times a week and had built a good rapport with the superintendent and some of the plant operators and engineers. So when I was laid off, I reached out to that superintendent, and because I was a known face and I had done good work, they scheduled me an interview. I was able to get a job with them as a process control engineer.
How does working in the public sector differ from working in the private sector?
One way is that, in the private sector, most of your hours are billable to a specific project and everything has a strict deadline attached to it. It’s very fast paced. In the public sector, things are usually a little slower, in part because you have to go through more levels of management to get things done. But it’s also more flexible because we are not tied to strict billable hours.
Here I have specific tasks I am supposed to get done, plus I am tasked additional duties as things come up. For example, it might be a rainy day, and that might cause an overflow in one of our tanks if there is a problem with the tank. We will have to address that right away. It’s never a dull day here.
Also, I know more about what clients really need now. We engineers tend to think we know the answers to everything, but until you go down to the site and get your hands dirty, you don’t really know. Because I’m here every day, and because we have both older and newer systems, I can tell right away if something new and innovative that the consultants want to try is going to work or not.
Your relationship-building skills have helped you succeed. How did you develop those skills?
I grew up an only child, so I learned to be outgoing and meet new people. When I went to college, my outgoing nature really came to the forefront, and I learned how networking can benefit you. I learned that people who may or may not be as skilled as you can sometimes get ahead because they know somebody or they put in a word with someone. I learned that wherever you go, you need to introduce yourself, whether that’s to your professors in college or upper management on the job.
What role have mentors played in your academic and professional career?
I graduated from Claflin University (an HBCU, historically Black college or university, in Orangeburg, South Carolina) with a bachelor’s degree in environmental science. During my sophomore year, my adviser and environmental science professor, Olanrewaju Johnson, Ph.D., selected me to go with him to one of the Department of Energy’s laboratories for a 10-week summer internship. I helped research the bioremediation capabilities of different bacterial types in the presence of toxic carcinogens in water.
That experience opened my eyes to the idea that there is another side of environmental engineering that has to do with water treatment and water resources — a side I really like. He encouraged me to apply to graduate programs for environmental engineering, and that conversation helped me eventually get into the University of Illinois at Urbana-Champaign, where I earned my master’s degree in environmental engineering.
What technical skills help you in your current position?
The work I do as a process control engineer doesn’t involve design work, but the skills I learned in my master’s degree courses apply. I took wastewater treatment and engineering courses, and honestly, I had no idea I’d ever be in that role again. We did a lot of modeling to determine how to improve wastewater treatment using biological phosphorus removal and other alternative technologies, and what’s cool is that’s exactly what I’m doing now. I’m looking at using alternative technologies in dissolved oxygen control to improve aeration, reducing contaminants from getting into the outfall.
So things have come full circle. I see how it actually works. Those courses really helped me out.
What personal characteristics help you most in your job?
I believe in myself. Going from a small HBCU in the South to a Big 10 school in the Midwest was not something I was sure I would succeed at. But I decided to do it. I prepared well, and I developed the confidence.
I also credit my versatility. I came from a nontraditional, nonengineering background; I took environmental science and chemistry in undergrad. But I ended up in environmental engineering.
And being outgoing has helped me participate in mentorship programs at ASCE and NSBE.
What do you like best about your job right now?
The flexibility. I have a few tasks I always need to do — checking the supervisory control and data acquisition system and trending that data — but I can also come up with projects I want to start. For example, if I think we can improve how we collect certain data or show data trends differently, I can suggest those ways to improve our operations. I can be innovative.
One example is we used to have these huge blowers that were run manually; the operators had to adjust the percentages of air coming out of them so that nitrification could work properly. When I got here, we had just gotten a contract with CDM Smith for automated blowers that would adjust automatically based on data from our sensors. But the operators were still walking around the aeration tanks, looking at the readings manually.
So I came up with a spreadsheet that could be updated daily with different factors that influence aeration, so we can make proper decisions based on the data and the trends in that data. Now the operators don’t have to walk past all the time; they can see it in the spreadsheet.
And in doing that, we noticed that between 4 and 8 p.m. every day, our blowers work the hardest because at that time the influent from earlier in the day has settled into the aerators. So we learned that we didn’t have to have all the aerators operating in the morning or early afternoon; we could wait. It saved us money.
What do you hope to accomplish in this new position?
I hope to help build a new culture — and it’s already starting to change since I have been here. They needed better collaboration and communication between departments. I promote the idea that we are all working together; if one person fails, we all fail. So we need to work together.
Also, I want to become a Class 4 certified operator; I am already a Class 4 apprentice, and that is the highest level apprentice you can be in the state of Indiana. I passed the exam last year, and I need another year or two of work experience before I can officially be licensed.
Where do you think the field of civil engineering is headed in the next several years, and where would you like to see it go?
The new thing will be incorporating JEDI — justice, equity, diversity, and inclusion — throughout all the different facets of engineering, not just at the organizational level but at the societal level. A lot of companies are trying to get a handle on that. Marginalized communities are the most affected by some of the problems with infrastructure across the country.
Why did you decide to take a part-time job with SMASH?
I really like to help give those who have been traditionally underrepresented an opportunity to get into STEM careers. Working there has opened my eyes to how much more work needs to be done to improve access to STEM education for marginalized communities and people of color. There is so much opportunity out there, but some students aren’t involved because of their environment or what school they go to. I’ve dealt with some very smart K-12 kids who come up with so many good ideas and are willing to learn — they just need the opportunity. That’s all they need.
What quote or principle do you try to live by, in your work or your personal life?
I am a man of faith, and I think prayer has been pivotal in my life. But it’s not just prayer; it’s prayer and preparation. I can pray that I pass the P.E. exam, but if I don’t study, I won’t pass! You have to do the hard work.
Is there one item that you can share from your personal or professional bucket list?
Personally, I want to be able to say that I have been to every continent — except Antarctica! I’m good without that. I love traveling, and I miss it.
Professionally, I hope one day I have my own organization dedicated to STEM outreach to traditionally underrepresented kids.
Laurie A. Shuster is the editor in chief of Civil Engineering.
This article first appeared in the January/February 2022 issue of Civil Engineering as “Have Confidence, Have
Faith — And Be Prepared.”