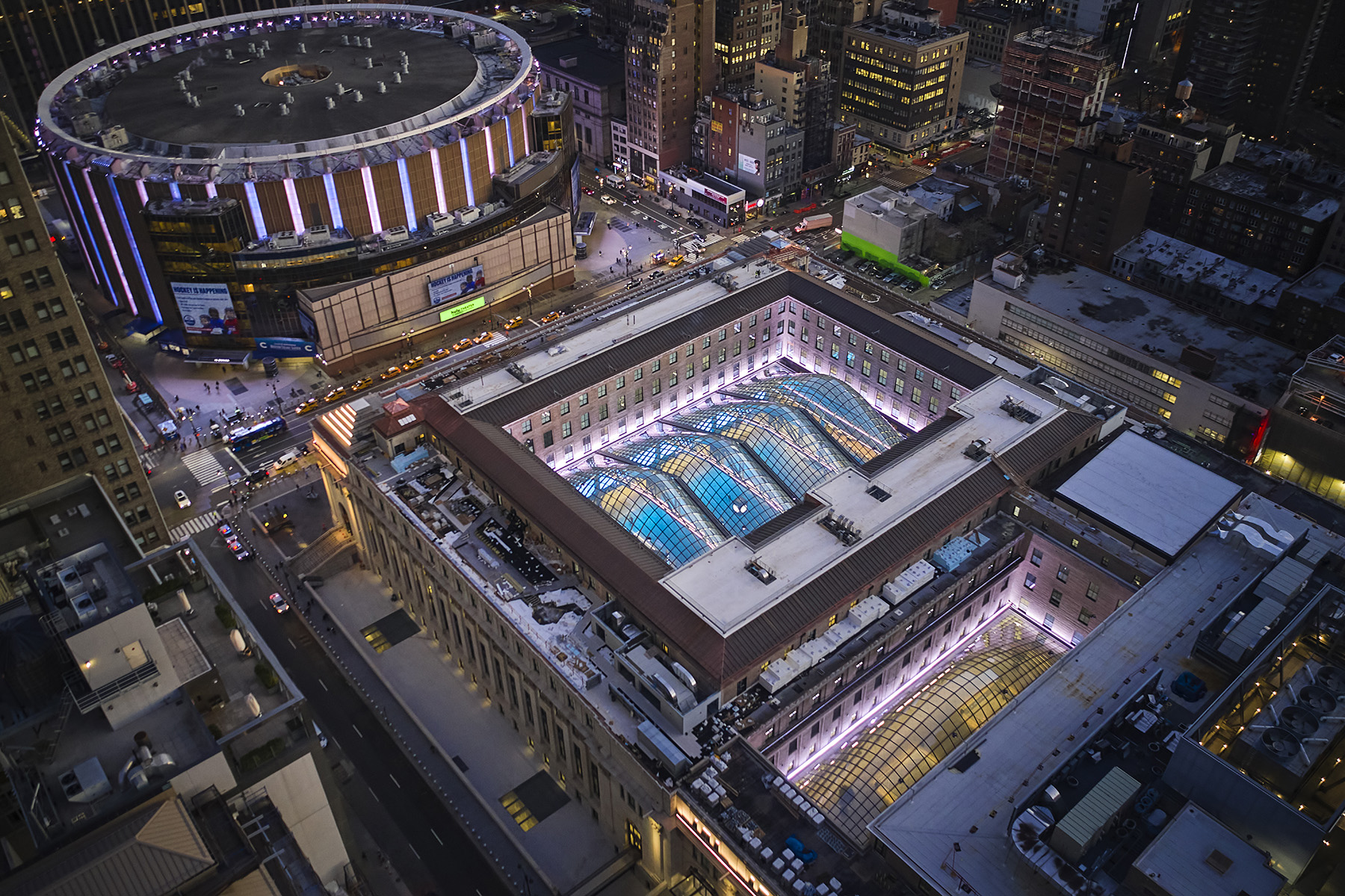
By Brian A. Falconer, P.E., S.E., SECB, M.ASCE, and Ick Kim, P.E., LEED AP
The new Moynihan Train Hall in New York City was designed to restore some of the glamour of train travel lost when much of the original Penn Station was demolished in the 1960s. Although the project ultimately took three decades to complete, the result is an extraordinary expansion.
Almost 60 years ago, the iconic New York City terminal of the Pennsylvania Railroad — known as Pennsylvania Station, or just Penn Station — was demolished, reducing the once-grand facility to a warren of below-grade concourses and platforms. By the early 1990s, however, Sen. Daniel Patrick Moynihan, D-N.Y., championed a proposal to convert a nearby structure — a mostly vacant former U.S. Postal Service building — into an expanded Penn Station that would restore a sense of dignity to rail travel and provide a grand public space for passengers returning home or arriving from afar.
It was a vision that had seemed hopelessly optimistic at the time. But thanks to the initial work and dedication of Moynihan, who died in 2003; the commitment of Empire State Development (the umbrella organization for New York’s two principal economic development public-benefit corporations, the New York State Urban Development Corp. and the New York Job Development Authority); and the persistence of many other supporters, the vision became reality in 2021 as the new Moynihan Train Hall.
Losing and protecting
In the 1950s, the Pennsylvania Railroad had a problem: Operating costs were increasing while passenger ridership was decreasing — in part because of the advent of the jet age and the ascendancy of the automobile. Faced with declining revenue, the railroad allowed its crown jewel, Penn Station, to fall into disrepair, further discouraging passengers. In response, the railroad sold air rights on the site to a developer who planned to demolish the above-ground portions of the beautiful beaux-arts-style station, which was completed in 1910 and has been considered the masterpiece of its original architects, McKim, Mead & White.
For the Pennsylvania Railroad, it was a business decision — but one that would have ramifications well beyond its impact on the company’s bottom line. Despite opposition by architects and preservationists, the air rights transfer was approved by the city and the 50-year-old structure was demolished in the mid-1960s.
The loss of Penn Station led to a preservation movement that has affected real estate development in New York City and nationwide ever since. As a result, for example, New York City created the Landmarks Preservation Commission to identify buildings of historic significance that, once designated landmarks, cannot be demolished or modified without review and approval. Not coincidentally, one of the first buildings protected by the commission was the James A. Farley Building, a former postal service facility located to the west of Penn Station, just across Eighth Avenue. Also designed by McKim, Mead & White, it was constructed in 1912 as a beaux-arts sister structure to Penn Station.
The ring-shaped upper floors of the older, eastern half of the Farley building surround a central atrium at the bottom of which was a column-free mail sorting room. Steel trusses spanning the width of the workroom supported a roof of glass and filigree that provided ample natural light. A retail post office was — and still is — located along the Eighth Avenue elevation at the top of a grand staircase, while a canopied loading dock was located on the west side. An annex, constructed in the 1930s, extended the building west to Ninth Avenue.
Initially, the building’s location above the railroad tracks greatly facilitated the distribution of mail by rail. But as long-distance delivery transitioned from trains to trucks, the postal service shifted work to other facilities — changes that by the early 1990s threatened to leave the Farley building empty and unused.
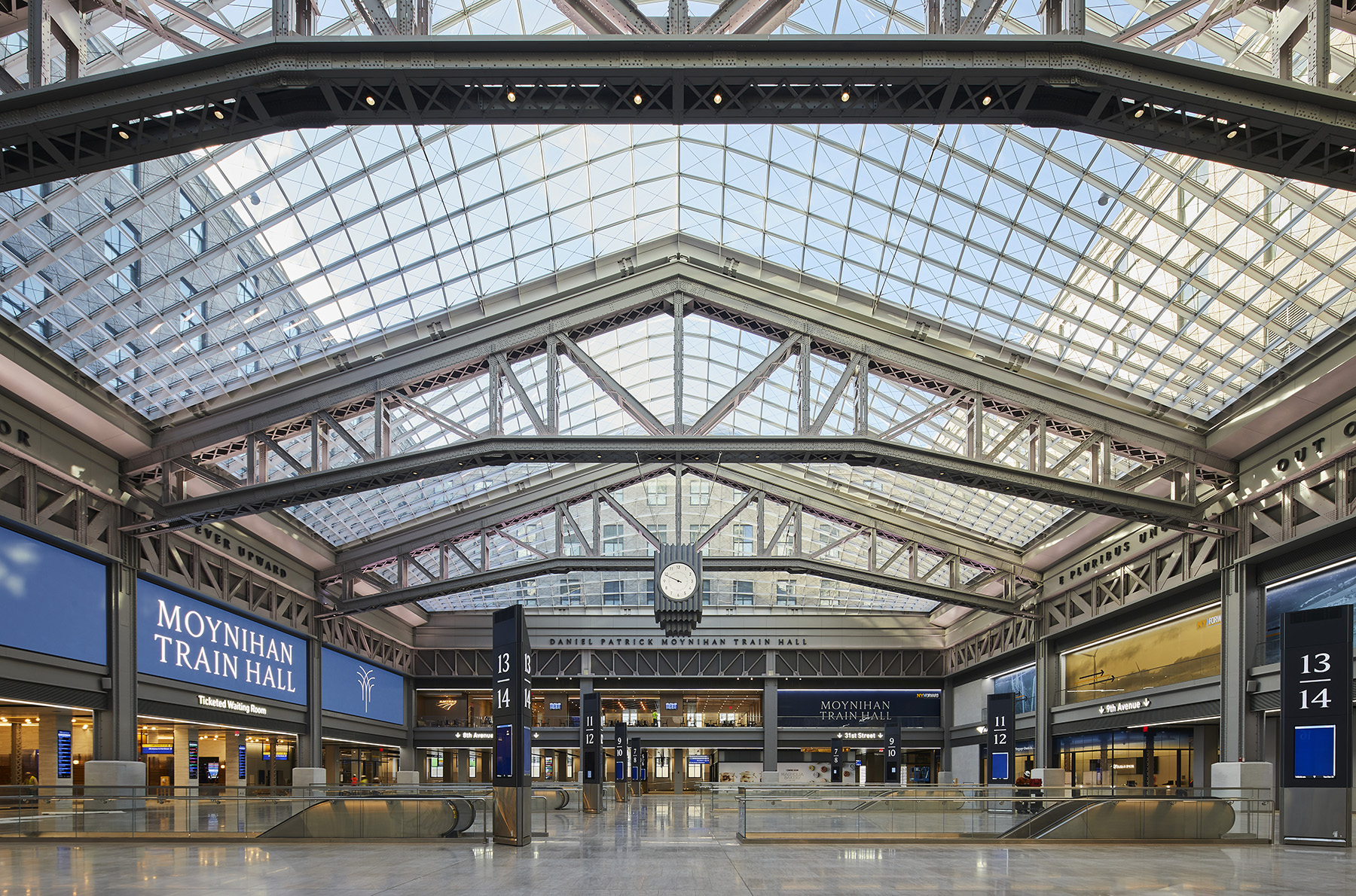
At the same time, Amtrak was looking to address the now-evident shortcomings of what remained of Penn Station. Those facilities were trapped beneath Madison Square Garden and Two Penn Plaza, leaving Amtrak and the station’s other operators — the Long Island Rail Road and New Jersey Transit — with no way to expand upward. Moreover, ridership had been steadily resurging and by the 1990s exceeded the capacity that the concourses and platforms could comfortably accommodate. But the Farley building, conveniently located above Penn Station’s platforms and tracks and already partially vacant, beckoned from the other side of Eighth Avenue.
That was when the idea of expanding the station into the Farley building developed — a seemingly simple concept that in fact faced formidable challenges in terms of the time, money, and cooperation among stakeholders required. But with the backing of Moynihan, the idea eventually secured the support of the U.S. Congress and President Bill Clinton, leading to the formation of the Moynihan Station Development Corp., a subsidiary of Empire State Development, which would see the project through to completion.
Evolving slowly
Plans for the new station evolved slowly during the mid and late 1990s. The first scheme by architect HOK, of St. Louis, featured steel parabolic arches spanning the width of the former mail sorting room to form a grand, 120 ft high space. In the next iteration, architect Skidmore, Owings & Merrill, of New York City, paid homage to the former Penn Station by retaining the existing sorting room trusses and replacing the roof with glass. This version proposed flat glass panels, however, whereas the final version would feature skylights with curved profiles. Large openings in the existing floors allowed views of the tracks below. In a contemporary vein, this scheme featured a folded glass and steel enclosure rising high above the full width of the midblock portion of the building that came to be known, affectionately, as the “potato chip.”
In 2003, the state of New York invited proposals for the public-private development of the Farley building to create the new train hall itself, plus nearly 1 million sq ft of other space in the building and another 1.2 million sq ft of future development rights. In 2004, the project was awarded to a joint venture of Vornado Realty Trust and The Related Companies, both based in New York City. The design team included structural consultant Severud Associates — which had extensive experience with Madison Square Garden as well as a previous redevelopment of Penn Station — and mechanical, electrical, and plumbing consultant Jaros, Baum & Bolles, both based in New York City.
The joint venture’s initial design scheme, by HOK and New York City-based James Carpenter Design Associates, involved the demolition of the existing roof, trusses, and floor of the Farley building’s sorting room to create the new train hall. Six slender columns would then be constructed to support the main roof of the structure, six levels above. The columns and existing walls of the central atrium would support an undulating skylight system — designed in collaboration with the New York City-based engineering firm schlaich bergermann partner. This new concourse space would have roughly the same height — 150 ft — as the old Penn Station’s waiting room. Another skylight would cover a new space constructed in the former loading dock located between the original Farley building and the annex.
Early in the project, the design team’s engineers collected and sorted through thousands of drawings, studies, reports, and anything else they could get their hands on — a process that is difficult under the best of circumstances but in this case was complicated further by the age of the building and the number of entities involved in its original construction.
Given the building’s longevity, it is not surprising that different types of steel had been used at different points in time. The oldest steels, from the original structure, were designed with an assumed yield strength of 30 ksi, while the steel in the 1930s annex was closer to 33 ksi; more recent work employed 36 ksi or 50 ksi steel. Engineers identified locations with those older steels and cut coupons from the supports for testing. Fortunately, statistical analysis of the results showed that the existing steels typically met or exceeded current standards for ASTM A36, which meant that the stresses could be increased where needed.
But some of the steel contained high concentrations of sulfur or silicon, which can affect field welding. And almost all of it had been coated with lead-based paint, which meant abatement was required wherever the framing systems were modified.
Field observations and condition surveys helped create a clearer picture of how the building had been constructed. Much of the existing framing, especially the heavier members, consisted of built-up sections, and most of the connections were riveted. Because rivets can be difficult to work around, their presence impacted decisions about how to reinforce and where to connect to existing members. And because individual connection details were not usually highlighted on structural drawings of the early 20th century, direct observation was required to enable the engineers to determine what to expect at key locations.
Stopping and starting
As the team, which now included SOM (read “An Unforgettable Public Space” on page 45), gained an understanding of the existing structure and its capacity, the proposed design evolved again. By 2006, the columns designed to support the roof over the train hall had been replaced with the curved skylights that would span the full width of the former mailroom at the existing roof level. The skylight over the former loading dock would be framed with aesthetically dramatic catenary arches.
Most design work paused during the economic recession in 2008. But the Moynihan Station Development Corp. separated out a transit-only component — the West End Concourse expansion — that was able to move forward as a stand-alone phase using federal stimulus funding. It proved the feasibility of the complex train shed work. The original West End Concourse, built by the LIRR in the 1980s, linked platforms 7 through 11, which serve only LIRR tracks. As a part of the Moynihan Train Hall project, however, the concourse had to be extended south to platform 3 to accommodate Amtrak and NJ Transit trains. Platforms 1 and 2 did not extend far enough west to be included.
Tucked beneath the retail post office and the grand stairway, the 20 ft wide passage for the West End Concourse was doubled in width, and the existing upturned girders were reinforced with plates and their tops cut off. This was necessary because the widened concourse would otherwise have been left with a band of girders sticking above the floor right down the middle. The tops of these girders were cut off to avoid creating such an obstruction.
The West End Concourse is one of the few areas in the overall project where significant load was added, so new foundations were necessary. Because the excavation for new footings would have interfered with train operations, the engineers worked with geotechnical consultant Langan, of Parsippany, New Jersey, to establish parameters for drilled piles that would clear the existing utilities and tunnels and deliver loads to the supporting rock beneath them.
Launching phase 1
Bid documents for what came to be known as the Moynihan Train Hall phase 1 project were completed in 2011. This portion also included new entrances at each end of the Farley building’s Eighth Avenue facade; ramps, stairs, and escalators leading to the concourse; and stairs and elevators from the concourse to the platforms.
The west side of the corridor featured sloped windows with views of the trains below. The original ceiling of the existing corridor was replaced by edge-lit LED refracting glass fins, which created a “sky” effect that generated a welcome sense of openness in the subterranean passageway. Skanska USA Building Inc., based in Parsippany, was awarded the construction contract in 2012, and work began.
In early 2014, as the ongoing construction of phase 1 bolstered confidence in the overall project, the phase 2 design of the recession-delayed train hall was restarted with the full support of Empire State Development and the Moynihan Station Development Corp. Plans for a third phase involving the redevelopment of the remaining Farley building also began; the final design of the entire project was completed in 2016.
Vornado, The Related Companies, and Skanska, along with SOM, were later awarded the design-build contracts for these subsequent phases of the project. WSP USA, part of WSP Global Inc., based in Montreal, was the program manager for the project’s second phase and served as a mechanical systems consultant, as part of a separate contract for Amtrak (read “Ready to Roll”).
Finalizing designs
The central feature of phase 2 involved the main boarding concourse within the 255,000 sq ft train hall space. Inspired by the original Penn Station’s grand waiting room, the spacious concourse is covered by arched skylights, the peaks of which rise to a lofty 92 ft above the train hall floor. It is a vast and modern setting designed to serve an increasing number of users: The combined passenger count for Moynihan Train Hall and Penn Station is expected to eventually exceed 650,000 travelers a day.
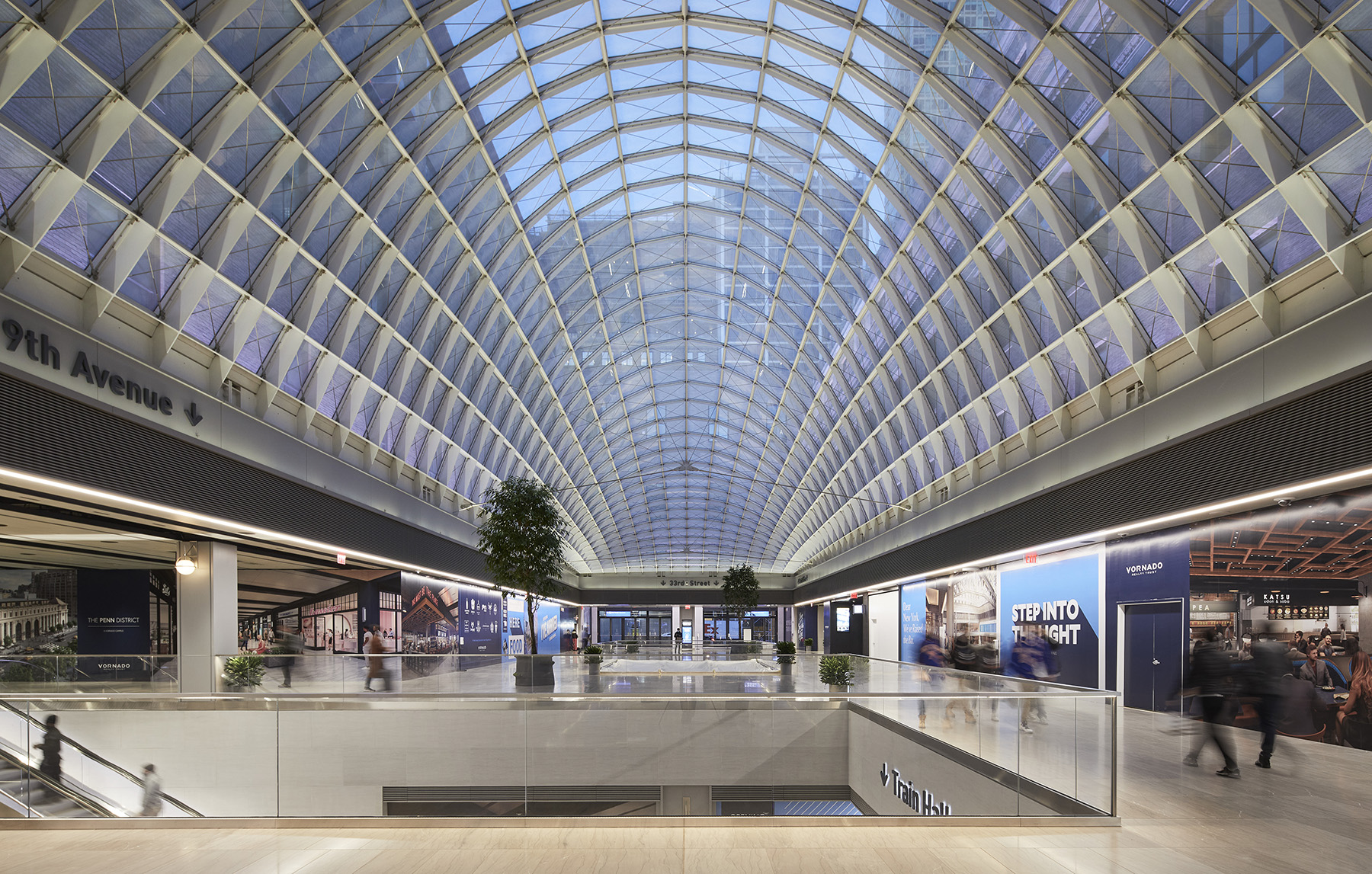
The final design reused the Farley building’s original trio of 150 ft long steel trusses, spaced at 50 ft on center, that had previously supported the mailroom roof. That roof’s skylights had been blacked out during World War II and later replaced by concrete slabs. Although the trusses had sufficient capacity to carry a new roof, the scheme involved placing the four arched skylights — designed by SOM and schlaich bergermann partner (read “Letting in Light”) — on top of the original supports. Consequently, the existing framing between the trusses had to be removed, which left the gabled top chords unbraced along their full span.
In addition to supporting the roof, the trusses had also served as overhead galleries for postal inspectors to observe the workers below. Accordingly, each truss was composed of two identical and parallel bents spaced about 3 ft apart. The bents were tied together with diaphragm plates and latticed straps that terminated about 6 ft above the bottom chords to allow inspectors to pass. This meant that the truss cross section was wider than might have resulted without the corridors.
The top of the box beams also provided an unobstructed bearing surface for the skylights. Each can be considered a hat, dependent on the building for vertical and lateral support but not adding any structural value. In addition to reinforcing the trusses to act independently, engineers also had to quantify the anticipated behavior of the century-old structure in terms of stiffness, wind excitation, and seismic response.
Although the former sorting room is located directly above the platforms serving Amtrak and the LIRR, its original floor was constructed two levels higher. Consequently, the intervening levels of concrete slabs and steel filler beams and girders were demolished. This demolition increased the space’s height by 20 ft, doubling the distance from the concourse floor to the spring point of the trusses, creating a surrounding balcony and dramatically increasing the feeling of openness in the hall.
And because the concourse framing transferred the weight of the demolished floor over the tracks, its capacity increased proportionally. This greatly simplified the design of the reframing that was needed to create openings for escalators.
The existing concourse level framing consisted of 9 ft deep steel plate girders spaced at 20 ft intervals and spanning up to 70 ft in the north-south direction, perpendicular to the platforms. The escalator openings are rectangular, with the long direction parallel to the platforms. This meant that typically one existing girder had to be transferred to provide the required clearances at each opening. In some locations, it was also necessary to notch the top of existing girders to allow the escalator and pit to pass above; in other locations the bottom of existing girders had to be notched to provide clearance over the escalator below. Either way, the girders were reinforced with field-welded steel plates before the notches were cut.
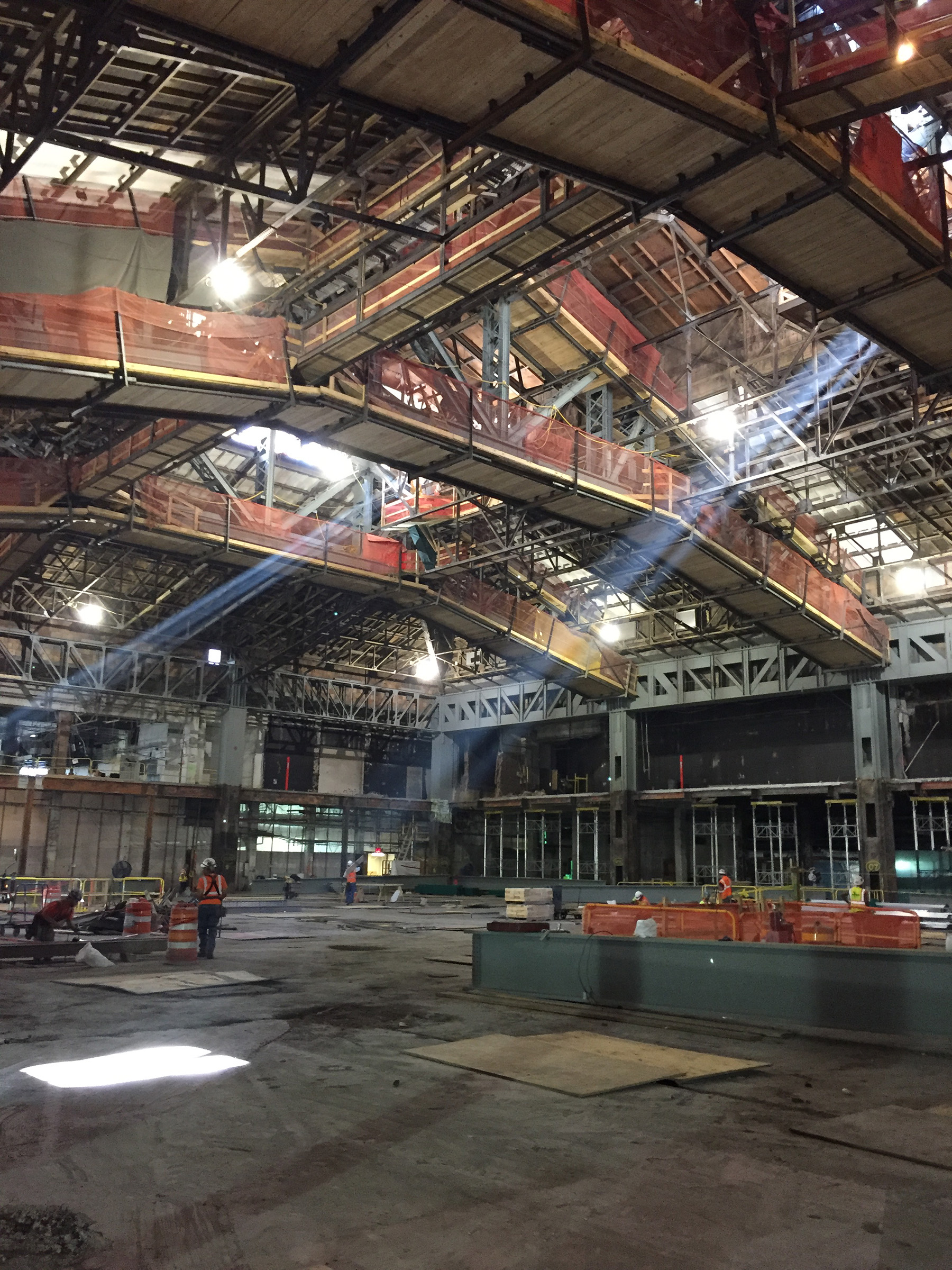
Where a girder was notched near its midspan, reinforcement alone was not sufficient to restore the necessary load capacity. In such cases, a column was added on one side of the notch, extending from the underside of the girder’s bottom flange down to a new foundation constructed underneath the platform below. Where a girder was notched near its end, a column was added if the notch interfered with the girder’s bearing over the existing column that supported it. In some cases, girder webs were sandwiched between field-welded steel plates to increase shear capacity, and in many locations, welds were added to the riveted connections to transfer the additional load.
Eleven escalator openings were created, 10 of them within the boarding concourse and one south of it. The new escalators extend from the concourse floor down to six of the 11 platforms serving Penn Station. For these escalators, 21 existing girders were transferred, which required 21 new columns. A twelfth opening, north of the boarding concourse, was created for an escalator that connects to the West End Concourse.
The designers followed a similar approach for the new space known as the midblock hall, located west of the train hall. Constructed in the original Farley loading dock, this space connects the train hall to entrances at 31st and 33rd streets. The space’s dilapidated original canopy was replaced with a skylight similar in width to those in the boarding concourse but longer, at 190 ft. Because there were no existing trusses in this location, cantilevered beams were installed within the existing roof framing on the west side, and a row of new columns was added along the east side. The design also added a new grand stairway, mirroring the stairs on Eighth Avenue, and escalators that extend up from the concourse level.
Making major alterations
Because the existing floor framing in and around the midblock hall area had been modified several times over the years, significant alterations were needed. In some areas, the existing structure was demolished and a new floor was framed. In other areas, the new floors were built up from existing slabs. Together, these efforts provided a level floor for the midblock hall and established consistent ceiling and storefront heights for the adjacent retail spaces.
The midblock hall entrances are located at arched openings in the existing granite facade on the north and south sides of the building. Each entrance was outfitted with a glass and architecturally exposed structural steel canopy cantilevering from the building face. Tubular members, hidden behind the stone to preserve its landmarked appearance, support each canopy.
Reconfiguration of the loading docks along 31st Street, west of the midblock hall entrances, was another significant component of the phase 2 work. The street-level framing was lowered in this area to facilitate operations, and it was decided to eliminate the intermediate columns (roughly two out of three) at the same time to further improve access. Consequently, new column transfer girders were added just below the second floor, one inside and one outside the existing framing and connected to the existing main columns.
After all the necessary supplemental framing and reinforcements were installed, the transfer girders were jacked upward to transfer the existing dead load of the columns into the girders. When the load to the columns was relieved, the column segment between the first and second floors was cut out, and the jacks were carefully released. Jacking and cutting operations were closely monitored to ensure that vertical movement stayed within tolerable limits and the existing facade remained unaffected.
Opening on time
Market demand made it clear that the remainder of the Farley building, occupying the majority of the superblock site, would be most attractive to prospective office tenants. The second through fifth floors, totaling 740,000 sq ft, can accommodate contiguous layouts with a generous column spacing of 40 ft by 32 ft. Moreover, these floors are connected by a central feature stair topped by a skylight like those in the train hall. At the fifth floor, 70,000 sq ft of existing roof framing was reinforced to support landscaping and tenant occupancy. A focal point of the outdoor space is a 6,000 sq ft, steel-framed and glass-enclosed pavilion with 25 ft clear to the underside of its roof trusses.
Work on the overall project continued smoothly through 2019 and up until March 2020, when the coronavirus pandemic brought most of New York City — and the rest of the world — to a standstill. Like other critical public infrastructure projects, however, Moynihan Train Hall was deemed essential, provided that the work could be done safely and that labor and supply chain disruptions could be navigated. Careful, nimble collaboration at all levels allowed the project team to assess risks and identify efficacious solutions, including alternative approaches and resequenced schedules.
Thanks to that teamwork, Moynihan Train Hall opened on time and to great fanfare on Jan. 1, 2021. This monumental infrastructure achievement has been well received by architecture critics, preservationists, and the traveling public alike. As the pivotal first step in other developments planned for the area, the redevelopment of the Farley building has become not a replacement for Penn Station but rather an extension. Conceived nearly three decades ago, the train hall’s success is due, in part, to the dedication and perseverance of many visionary public officials, design professionals, and contractors.
At press time, most of the phase 3 spaces had been turned over to tenants and fit-outs were in progress. Occupancy was nearing completion, bringing the highly successful project to a triumphant close.
Brian A. Falconer, P.E., S.E., SECB, M.ASCE, is a principal, and Ick Kim, P.E., LEED AP, is a senior associate in the New York City office of Severud Associates. Other contributors to the article include: Alexander Azero, P.E., M.ASCE, and Jesse Cooper, P.E., associates at Severud; Rebecca Milano, a senior engineer at Severud; Kyle Roshberg, P.E., a former associate at Severud; and Andrew Mueller-Lust, P.E., M.ASCE, a former Severud principal.
An unforgettable public space
By Colin Koop, AIA
In bringing the Moynihan Train Hall to life, Skidmore, Owings & Merrill’s design team and the project’s owner, Empire State Development (the umbrella organization for New York’s two principal economic development public-benefit corporations, the New York State Urban Development Corp. and the New York Job Development Authority), have at last realized the vision of the late Sen. Daniel Patrick Moynihan, D-N.Y., to transform the Penn Station complex into a gateway worthy of New York City.
The creation of the train hall did so by constructing a spacious facility of 255,000 sq ft, including a grand, skylit main concourse; improving accessibility through dozens of new escalators, stairways, and elevators; and adding crucial amenities, from new waiting and ticketing areas to elegant restrooms.
The new train hall reveals the advanced engineering that lay beneath the surface of the original neoclassical architecture.
But to truly reimagine America’s busiest transit hub, this project had to be more than just a utilitarian exercise. As one of New York City’s major rail stations and a former icon of America’s largest railroad, the original Penn Station was a place of deep symbolic importance. SOM and Empire State Development recognized that the creation of the Moynihan Train Hall offered a rare opportunity to put forward a new plan for the U.S. Postal Service’s historic James A. Farley Building and for Penn Station itself, together forming the Empire Station Complex that makes a bold case for the future of rail travel.
Further adding to the project’s complexity was the fact that the Farley building — designed in 1912 by the same architects as the original Penn Station, McKim, Mead & White, and located directly across the street — was a complex, century-old architectural masterpiece in need of extensive restoration. Any additions or modifications needed to respect and complement the existing building while reimagining it for use as a modern transit hub.
Seamless integration
By respecting the Farley building’s design logic, SOM’s team was able to take advantage of the building’s strengths and seamlessly integrate the new train hall. For example, the train hall’s new entrances and passageways emerge from McKim, Mead & White’s symmetrical, beaux-arts building plan, preserving the dramatic entry sequence that was characteristic of its work. And the new main concourse, the heart of the facility, adapted the former mail sorting room, which featured long spans and a lack of columns that made it an ideal space for the train hall.
As the project was being planned, Empire State Development’s design principles stressed the need to preserve historic elements. Such elements included the three massive, riveted trusses in the main concourse that were restored and exposed for the first time in the building’s history. As a result, the new train hall reveals the advanced engineering that lay beneath the surface of the original neoclassical architecture. They also serve as a reminder that the Farley building was always more industrial in nature than its facade let on.
On top of these trusses, a new, grand skylight was designed with four catenary vaults that rise 92 ft at their apexes. The dynamic contrast between the unabashedly contemporary skylight and the historic trusses brings the train hall to life and illustrates a lesson in the evolution of structural design.
Access added and expanded
The design also took advantage of the direct access that the Farley building provides to Penn Station’s underground platforms — a holdover from the era when mail was transported by rail. The train hall expands concourse space by 50%. By adding escalators and elevators and extending existing elevators, the design team was able to directly connect the new train hall to 17 of Penn Station’s 21 tracks. These efforts expanded circulation to the Penn Station platforms by 37% and seamlessly integrated the new train hall into the larger, exisiting station complex.
The result is a rail hub that brings dignity and grandeur back to Penn Station for the first time since the original station building was demolished in 1963. Once again, Penn Station is something more than a warren of underground passageways. It is a gateway and a landmark, a civic space that welcomes visitors to New York City.
Just as importantly, the Moynihan Train Hall serves as a model for future investment in rail transit. Thanks to the work of countless individuals and partner organizations, the transformation was completed in three and a half years of construction. By respectfully reimagining the Farley building, this effort demonstrates that preserving the past and modernizing infrastructure need not conflict. The Moynihan Train Hall brings together the old and the new in one unforgettable public space.
Colin Koop, AIA, is a design partner in the New York City office of Skidmore, Owings & Merrill.
Letting in light
By Michael Stein, P.E., M.ASCE
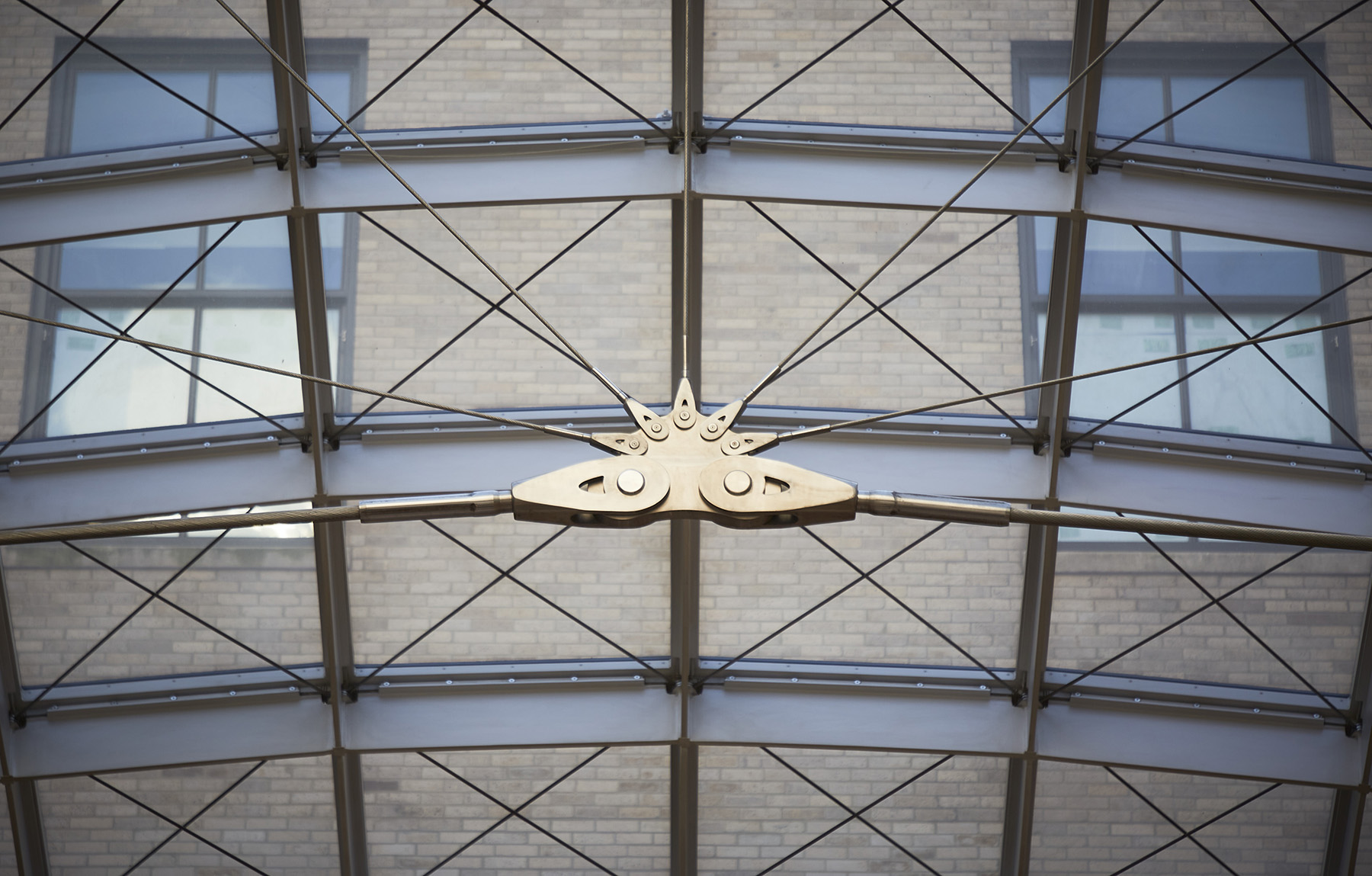
As engineers, the thrill of seeing our ideas come to fruition through the design of new structures and buildings must be balanced with the knowledge that the most sustainable building is the one that does not have to be built in the first place. Avoiding new construction as a paradigm for the construction industry is obviously far-fetched, but as an industry we need to be aware of our negative contribution to climate change and how we can mitigate the repercussions of our desire for new construction. In this context, the conversion of the U.S. Postal Service’s historic James A. Farley Building into the Moynihan Train Hall is a major step forward in an environmentally sustainable direction.
This project set an important precedent for large-scale adaptive reuse for transit-oriented projects in New York City. It was made possible through an innovative design that included the introduction of state-of-the-art glass roofs in two pivotal areas of the historic building.
Open and bright
Opening up the existing structure to provide natural light into the concourses — something that the existing, subterranean Penn Station lacked — was achieved by Skidmore, Owings & Merrill, of New York City, and the New York City office of the international engineering firm schlaich bergermann partner, through the introduction of monumental skylights. These skylights are transparent enough to raise the natural light level but also lightweight enough to be supported by parts of the historic building.
Several designs were initially considered, from structures that swept over the entire courtyard opening to umbrella-type roofs supported on the floor. Importantly, the final design included the preservation of the existing support structure for the main concourse’s original roof — a trio of triangularly shaped, riveted trusses. The characteristic appearance of the trusses allowed the design team to build a visual bridge between the historical building fabric and the modern construction techniques that were ultimately used.
The capacity of these trusses to support the planned new roof system was confirmed by the project’s structural engineer, Severud Associates, of New York City.
Shells and stability
A simple, planar skylight — assembled out of steel beams and large glass panes — would have done the trick with respect to transforming the century-old post office building into bright passenger halls. But this approach was considered an oversimplification that did not take into account the prominence of the project and the desire to create welcoming spaces for the busiest rail station in the Western Hemisphere.
To create the necessary grandeur, the design team arrived at curved shell structures assembled out of a steel grid in which the quadrangular openings are covered with glass. Free-form shells, like all structures in compression, are prone to buckling. But due to the three-dimensional shape of the shells, multiple load paths are possible — which makes the determination of buckling modes far more complex than in other structures.
Fortunately, advanced software systems — such as the advanced modules of the finite element analysis software from SOFiSTiK AG, of Nuremberg, Germany — enabled the design team to identify these modes and design the structures accordingly. The synchronization of analysis capacity with real-world constructability limitations was a key problem that in order to be solved required innovative and comprehensive design approaches.
Courtyards and curvatures
The Moynihan Train Hall skylights cover two distinct courtyards — in the main train hall space and at the area known as the midblock hall, which was created in a former loading dock. Both courtyards have rectangular shapes with dimensions of approximately 230 by 157 ft for the train hall and 194 by 62 ft for the midblock hall. For the midblock hall, the design team selected a single shell with the shape of a modified semi-cylinder in which the curvature was initially very shallow at each end and then increased steadily toward the center.
The larger train hall is divided into a system of four interacting shells, each supported on one of the three existing, pyramidal steel trusses. Using a similar geometrical approach of increasing the rise toward midspan as at the midblock hall skylight, the design team created a structure that features an impression of lightness and grandeur.
Because shells perform more efficiently once they are designed with a certain curvature, the dimensions of the structural elements are critical. In the case of the Moynihan Train Hall skylights, the steel elements are deeper in areas of low curvature toward the edges to resist the inevitable bending moments. In the center, the elements can be much shallower because they carry only the load in compression. The grid at the flat ends of the shells is much tighter, which reduces the demand on the individual elements and contrasts with the larger and much lighter grid in the curved central sectors. This combination creates wonderful effects of light and shadow from the publicly accessible concourse areas.
Steel and glass
The steel elements were constructed from slender T-shaped sections with approximately 0.8 in. thick plates and depths ranging from roughly 4 to 13 in. The flanges were kept constant at approximately 3.5 by 0.4 in. While these elements provide great stiffness in the direction of their strong axis, they are exceptionally weak with respect to weak-axis bending. To counteract this weakness, diagonal steel cables were used to brace the surfaces and establish the load-bearing behavior of a true shell. The cables run continuously at the top of the plates, directly beneath the glass panels, and are fixed at each node to the steel structure with clamping disks.
The degree of curvature of the shells differs substantially in the longitudinal versus the cross direction. The small curvature in the longitudinal direction required the introduction of stiffeners, which are typically necessary for cylindrical structures, to provide global bracing for the surface. To limit the visual impact of these stiffeners, they were designed in a prestressed bicycle-wheel-type cable configuration, which also balances out the horizontal thrust of the structure in the cross direction.
An underlying challenge of this type of structure involves balancing the structural requirements of the grid form with economic considerations, such as avoiding the use of more expensive, curved glass panes to clad the structure. This can be accomplished by laying out the steel grid in a way that makes the resulting quadrangles all planar. But for the complex boundary conditions at the train hall, the initial layouts created unsatisfying patterns with irregularly shaped openings and singularities.
Consequently, the design team decided to develop an exterior surface that was shingled and geometrically independent from the structural support grid. This meant that the glass elements on top of the steel structure could be planar and economical, while the structure itself could be formed from a highly efficient shell geometry. Although this solution made support for each individual glass panel more complex, it simultaneously simplified the design of the overall structure, made fabrication more accurate, and limited on-site tolerance issues.
The insulated glass units typically comprise approximately 0.3 in. thick toughened glass, a laminated layer of 0.08 by 0.2 in. thick heat-strengthened glass with a 0.6 in. thick interior space filled with argon. The glass panels also feature a low-emissivity coating and a ceramic frit that provide the necessary performance values.
Installation and collaboration
Like all structures that are prone to buckling, shells are sensitive to imperfections and require careful planning of fabrication and installation procedures. This work was closely coordinated by the project’s contractor, Skanska USA Building Inc., based in Parsippany, New Jersey, and its subcontractor for the skylights, seele GmbH, based in Gersthofen, Germany. The quality of the architectural and structural design was tested and approved in a series of mock-ups at seele’s fabrication facility in Europe. Following that, the steel grid was prefabricated in ladders on precision jigs and delivered to New York City.
Meanwhile the construction site had been equipped with extensive scaffolding that allowed the contractor to position the prefabricated elements with high accuracy before they were welded together.
The resulting structure was still not self-supporting until the diagonal bracing cables were installed and prestressed in a predetermined sequence. Following the installation of these cables, the scaffolding was removed, and the final step involved the installation of the glass panels. The entire erection process was accompanied by geometrical surveys and spot-checks of the cables at predetermined construction milestones to ensure that the shape and internal forces remained within a predicted range.
The Moynihan Train Hall skylights resulted from a close collaboration between the design team’s engineering and architectural experts, who found innovative solutions to balance the project’s complex and varying requirements. The result is a beautiful addition to one of New York City’s most important transportation facilities as well as a stunning new contribution to the city’s heritage of great building design.
Michael Stein, P.E., M.ASCE, is a partner and managing director of schlaich bergermann partner, of New York City.
Ready to roll
By Caroline Forbes and Paul Meyer, P.E., LEED Fellow
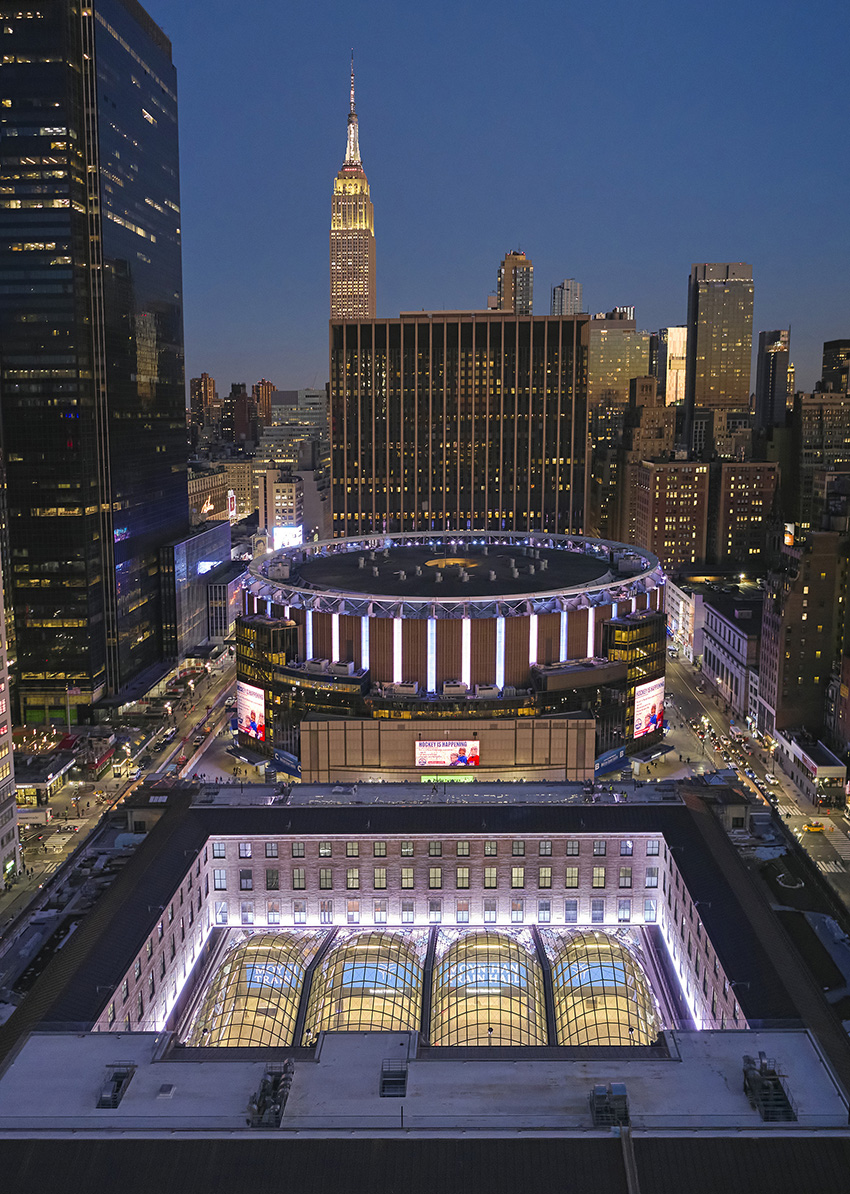
The WSP team consisted of New York City staff members and their subconsultants, supporting Empire State Development and the Port Authority of New York and New Jersey, both funding partners of the $1.6 billion project. WSP’s role involved project management, commercial management, technical oversight, construction oversight and compliance, and stakeholder coordination. These efforts focused on Empire State Development’s overall aim to achieve the highest standards for design and construction excellence as well as long-term operation and maintenance durability.
WSP was also hired under a separate contract by Amtrak as the mechanical, electrical, and plumbing engineer of record for Amtrak’s fit-out within the train hall and for the platform ventilation portion of the work. WSP maintained a strict firewall between this work and its project management teams.
The creation of New York City’s first new train hall in more than 50 years was a challenge in itself, an achievement made even more remarkable because it was the city’s first facility shared by Amtrak and the Long Island Rail Road. To best prepare all partners and stakeholders for the transition, the WSP team implemented an operational readiness activation and transition program — known as ORAT — using staff experienced in railroad operations in New York City to lead this effort.
Commonly used on airport projects, the ORAT program was useful for the train hall effort because the methodology supports collaborative planning and the testing of systems, scenarios, and procedures to ensure readiness for opening.
As part of this program, WSP conducted five virtual trial sessions on specific processes with the railroads and property manager before leading two in-person whole-station trials, allowing the findings and updates from the virtual sessions to be further tested. The first of the trials focused on ensuring that railroad and property management staffers were familiar with their responsibilities and the facility, while the second included public volunteers to best identify any issues and simulate opening day.
The detailed ORAT planning and trials undoubtedly assisted Empire State Development in providing the facility with a smooth transition to operations.
LEED the way
WSP also performed the Leadership in Energy and Environmental Design certification administration for the Moynihan Train Hall project. The train hall achieved a LEED Silver rating from the U.S. Green Building Council/Green Business Certification Inc., using the LEED for Transit rating system. The train hall is the first in the world to achieve LEED for Transit BD+C, according to the Green Business Certification.
The LEED points completed included location and transportation credits because the project’s location is within walking distance of diverse places such as restaurants and office buildings as well as for its intermodal connectivity to rail, bus, and ferry transportation. Social equity and disaster preparedness credits were also achieved. In terms of social equity, the project included extensive outreach via a variety of informal and formal processes, including environmental, historic preservation, and land-use studies and approvals.
By improving the passenger experience and operations and encouraging use of the nation’s most interconnected transit hub, the project will have an outsized impact on reducing carbon emissions, providing access to jobs and affordable housing, and improving regional mobility for people of all economic means.
On the disaster preparedness side, the facility’s design included advanced building security and communications systems, comprehensive emergency management plans, and regular coordination between stakeholders and the various responding agencies stationed on-site and nearby.
The project also received points for the renovation and restoration of an existing building, rather than demolition and reconstruction, as well as for the giant skylights that provide the facility with natural lighting and sky views. In addition, the construction plan for Moynihan Train Hall required the use of low chemical-emitting paints and adhesives and established an indoor air quality plan that protected workers and the new building.
The project also used a new pilot credit from the U.S. Green Building Council concerning the use of effective cleaning and disinfecting processes and ingredients to help fight the COVID-19 pandemic during reoccupancy and operations. The processes involve disinfectants that are registered on the U.S. Environmental Protection Agency’s List H for use against the coronavirus and are formulated with ingredients recommended by the EPA’s antimicrobial pesticide products program. These measures are intended to minimize adverse health impacts on cleaning personnel, building occupants and visitors, and the environment.
Caroline Forbes is a design manager, and Paul Meyer, P.E., LEED Fellow, is a senior vice president in the New York City office of WSP USA, part of WSP Global Inc., Montreal.
Project Credits
Client: Empire State Development/Moynihan Station Development Corp., New York City
Developer-builder team: A joint venture of Vornado Realty Trust and The Related Companies, New York City; Skanska USA Building Inc., Parsippany, New Jersey; the Metropolitan Transportation Authority, New York City; the Long Island Rail Road, Queens, New York; and Amtrak, Washington, D.C.
Architect: Skidmore, Owings & Merrill, New York City
Structural engineer: Severud Associates, New York City
Skylight engineer: schlaich bergermann partner, New York City (with seele GmbH, Gersthofen, Germany)
Mechanical, electrical, and plumbing consultant: Jaros, Baum & Bolles, New York City (WSP USA, part of WSP Global Inc., Montreal, also served as a mechanical systems consultant specifically for Amtrak.)
Geotechnical/civil/surveying and imaging consultant: Langan, Parsippany
Construction management/oversight: Phase 1: The Port Authority of New York and New Jersey, New York City, and STA, a joint venture of STV, New York City, and AECOM Tishman, Dallas; Phase 2: WSP USA; Phase 3: A joint venture of Vornado Realty Trust and The Related Companies; Skanska USA Building Inc.; and Skidmore, Owings & Merrill
Train systems consultant: Systra Group, Paris
Historic preservation: Higgins Quasebarth & Partners, New York City
Historic building restoration: Building Conservation Associates Inc., Philadelphia
This article first appeared in the March/April 2022 issue of Civil Engineering as “Magnificent Makeover.”