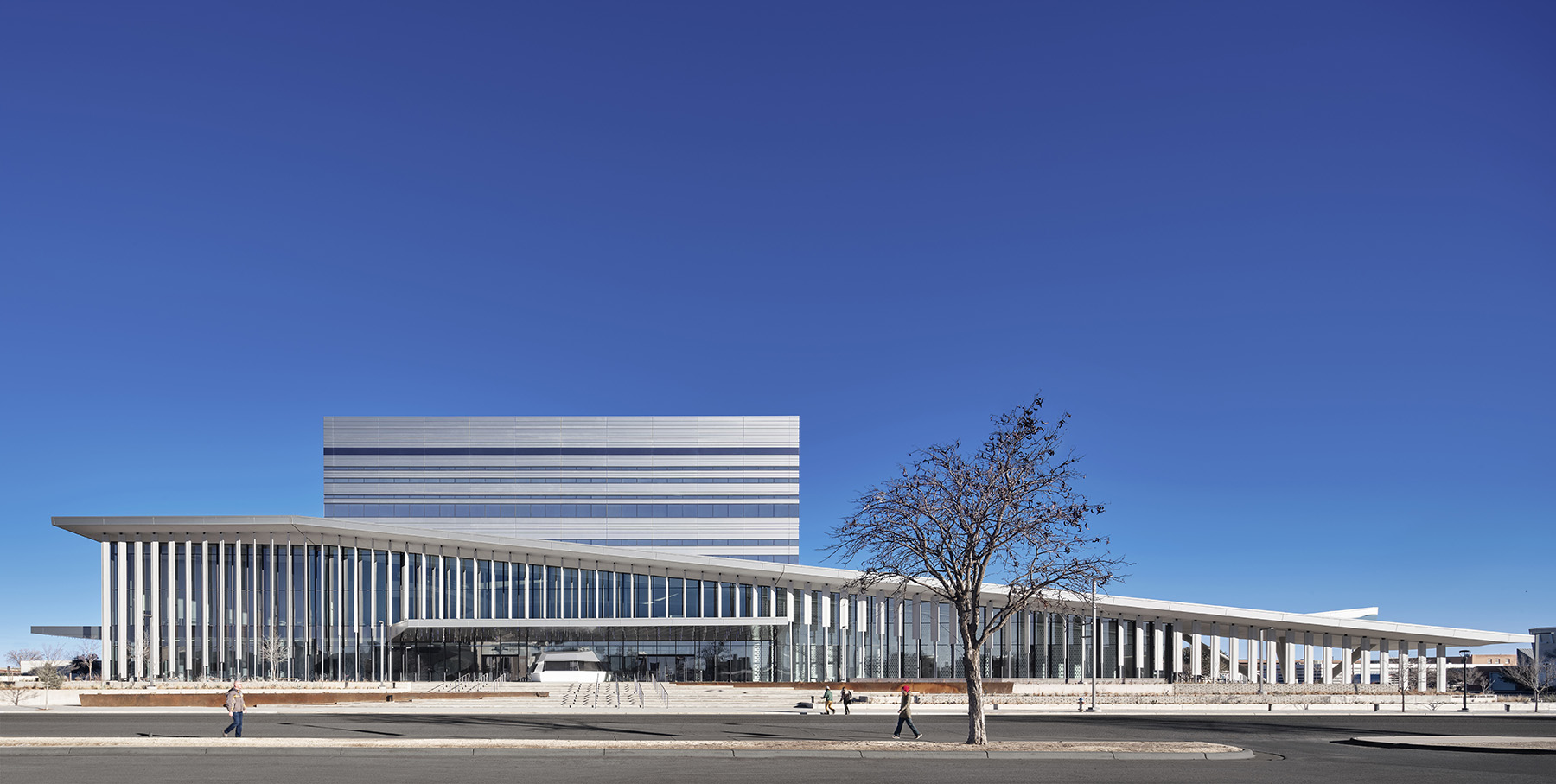
By Barry Charnish, P.Eng, and Tom Greenough, P.Eng
The Buddy Holly Hall of Performing Arts and Sciences in Lubbock, Texas, required group collaboration and carefully adjusted structural steel elements.
The Buddy Holly Hall of Performing Arts and Sciences, completed in early 2021, is a dynamic hub for the arts and culture community as well as a venue capable of attracting top talent for world-class performances.
The $158 million project was funded and is owned and operated by the Lubbock Entertainment and Performing Arts Association. The hall is now home to Ballet Lubbock, the Lubbock Symphony Orchestra, and the Lubbock Independent School District Fine Arts Department. The hall is named for Lubbock native Buddy Holly, who sparked a cultural revolution in the 1950s with his music, songwriting — and large-frame glasses.
The hall encompasses 218,000 sq ft and includes the 2,297-seat Helen DeVitt Jones Theater, the 415-seat Crickets Theater, a 5,600 sq ft multipurpose room, a 20,000 sq ft ballet school, a 3,300 sq ft restaurant, 21,400 sq ft of back-of-house space, the 36,100 sq ft Christine DeVitt Main Lobby, and a 6,000 sq ft covered outdoor event/performance space referred to as the Bird’s Tail.
Entuitive was the structural engineer for the Helen DeVitt Jones Theater, the Christine DeVitt Main Lobby — including a striking spiral staircase — and the main entrance canopy. MWM Architects was responsible for the foundations, basement, ballet studio, and the back-of-house area, and Parkhill was responsible for the Crickets Theater, the multipurpose room, and the Bird’s Tail (read “BIM Enhances Collaboration,” below).
Entuitive was invited to participate in the project by the design architect, Diamond Schmitt, largely due to previous experiences collaborating together on theater projects, including the Four Seasons Centre for the Performing Arts in Toronto and the Mariinsky II Theatre in St. Petersburg, Russia.
Although the hall appears to be one building, it is in fact three separate structures with an acoustic expansion joint between the Crickets Theater and the main hall, and the main hall and the multipurpose room. The lateral system of the building is provided by a combination of concrete walls, vertical steel bracing, and steel moment frames.
Christine DeVitt Main Lobby
The lobby is a three-story volume that includes a large gathering space sized to accommodate seated banquets, standing receptions, and prefunction use. The main floor includes a box office and concessions; a VIP lounge can be accessed via a bridge on the second level. Additional gallery and concession space overlook the main floor on levels two and three. These were created by balconies framed in structural steel. The playful, shifting geometries of the plaster-finished balconies overlooking this space draw the eye to the lightwell above.
The graduated elevation that visitors see as they approach the building required a complex feat of engineering. The exterior wall needed to shift inward at the upper levels for aesthetic and acoustics reasons. To keep the lobby space column-free, a truss spanning more than 150 ft was introduced to support many different elements, including the lobby roof, the exterior cladding, the sloping roof overhang, and the main entrance canopy.
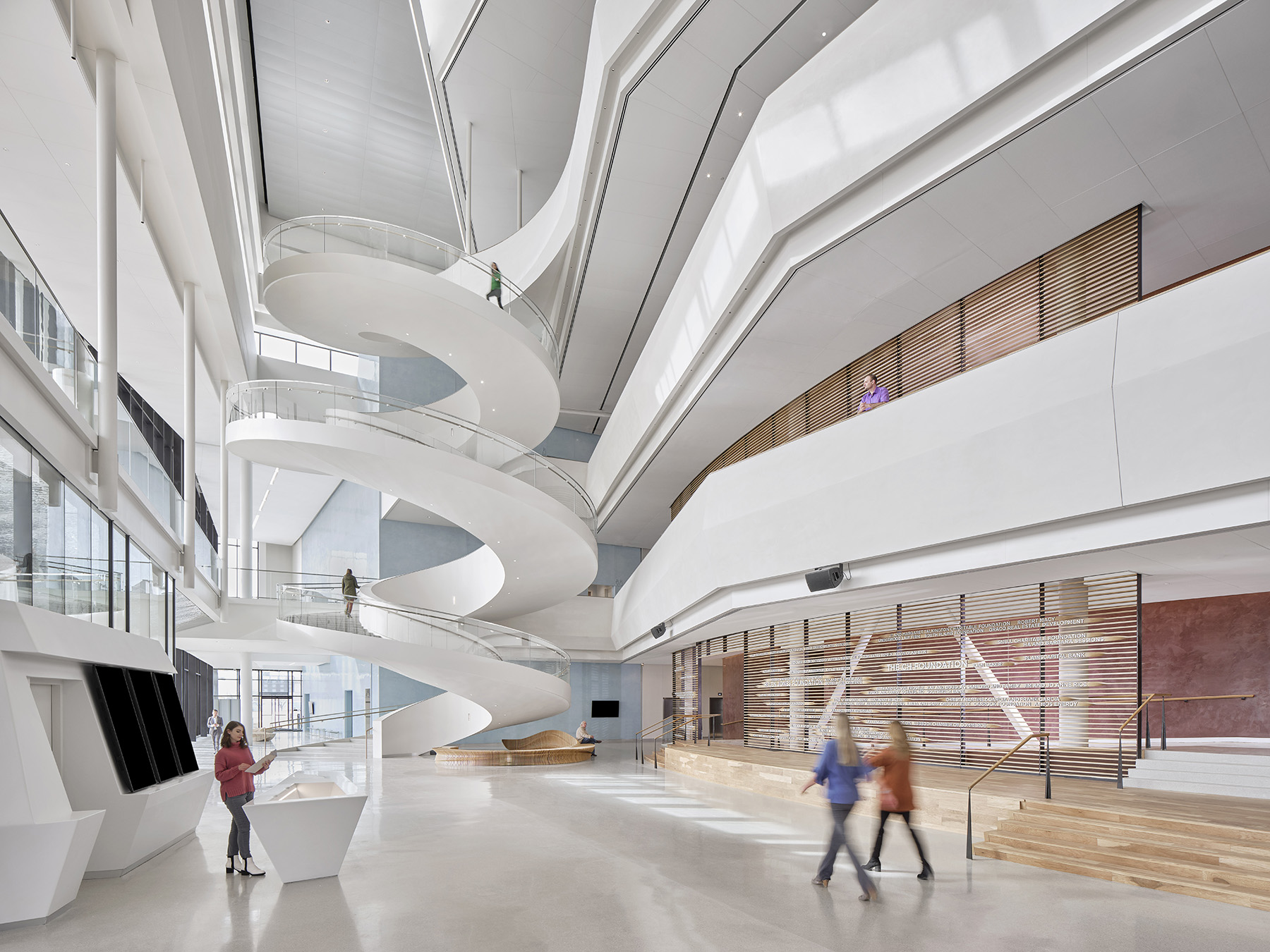
From this 45-ton truss, which varies in depth from 12 ft at the supports to 14 ft at midspan, hangers extend downward to support the exterior cladding, which is a combination of solid panels and linear windows, as well as a sloping roof that pushes out from this cladding line. The sloping roof also receives support from columns along the curtain wall below before cantilevering outward to provide a sunshade from the Texas sun.
Inside, round, slender, architecturally exposed structural steel hangers emerge from beneath the sloping roof and extend downward to support one end of custom-tapered plate girders at level 2. These custom-tapered plate girders then cantilever out 25 ft to create the main entrance canopy, which is a modern take on the marquee.
Finally, the introduction of glass-fiber-reinforced concrete fins on the elevation not only adds a dynamic aesthetic element but further contributes to shading the curtain wall. The challenge was how to support the undulating fins, which are located 5 ft away from the curtain wall, while giving the fins the appearance of floating.
The fins required a slender structural steel element to fit within their slender profiles, but the elements had to have sufficient strength to support the fin weight and sufficient stiffness to prevent wind-induced fluttering. The design innovation was to hang oval hollow structural sections from the sloping roof and then vary the profile over its height by splicing three sections together. Inside the fin an oval HSS 11x6 is used, and above and below the fin smaller oval HSSs are used.
The use of oval HSSs minimized the visibility of the supporting steel and maintained the architectural profile of the fin. Oval HSSs are a recent advancement in the structural steel industry.
Monumental stair
The monumental spiral staircase in the main lobby makes a grand statement, measuring more than 56 ft tall through three stories and featuring 145 tons of steel. The stair is constructed from HSSs and steel plates. A central spine supports cantilevering stair treads, which vary in length from 8 ft to 14 ft. The HSS chords for the central spine had to be bent in two directions by induction to form the helical shape of the stair. The HSS risers, steel plate treads, and outside HSS stringers were then connected to the central spine before the central spine web plate was welded to the HSS chords.
The stair was fabricated as continuous pieces, and once one-third of a flight was completed, it was moved out of the way to allow fabrication of the next section. A temporary support tree was used during erection to support the stair as it was installed in five pieces, requiring significant field welding between the sections.
The long spans, slender profile, low mass, and low damping ratio resulted in a low-frequency system that was particularly vulnerable to vibrations from human activity. Entuitive created a finite element model of the stair that included all the supporting framing. The engineers’ analysis revealed that supplementary damping would be required to meet the vibration limits, so a tuned mass damper was added on the second and third flights of the stair.
Spectacular seating
The Helen DeVitt Jones Theater is a 2,297-seat venue with premier acoustics providing an optimal theater experience, no matter the type of performance, sound level, or seat in the house. The seating is arranged in a horseshoe shape over a main level and three balconies. The main level is a reinforced-concrete, slab-and-beam system with fixed seats on removable raked platform sections. The platform sections can be taken down on the orchestra pit lift and stored below the main level to allow for general admission standing room for 900 guests.
Entuitive evaluated both reinforced concrete and structural steel for the balconies. Based on the local market conditions, the team selected structural steel as the primary framing system. However, the look and functionality of polished concrete for the risers and treads was still a design requirement.
The columns were placed behind the back wall of the theater, resulting in balcony rakers cantilevering up to 32 ft. To achieve this, 40 in. deep rakers bent in several locations to follow the profile of the balcony were used. To maintain a thin edge profile and lines of sight below, a shallower 14 in. deep section was added at the end to create the front section of the balcony. The horseshoe design proved especially challenging, as it made each of the balconies unique and required each of the structural steel members for the risers to be bent to follow the curvature of the space.
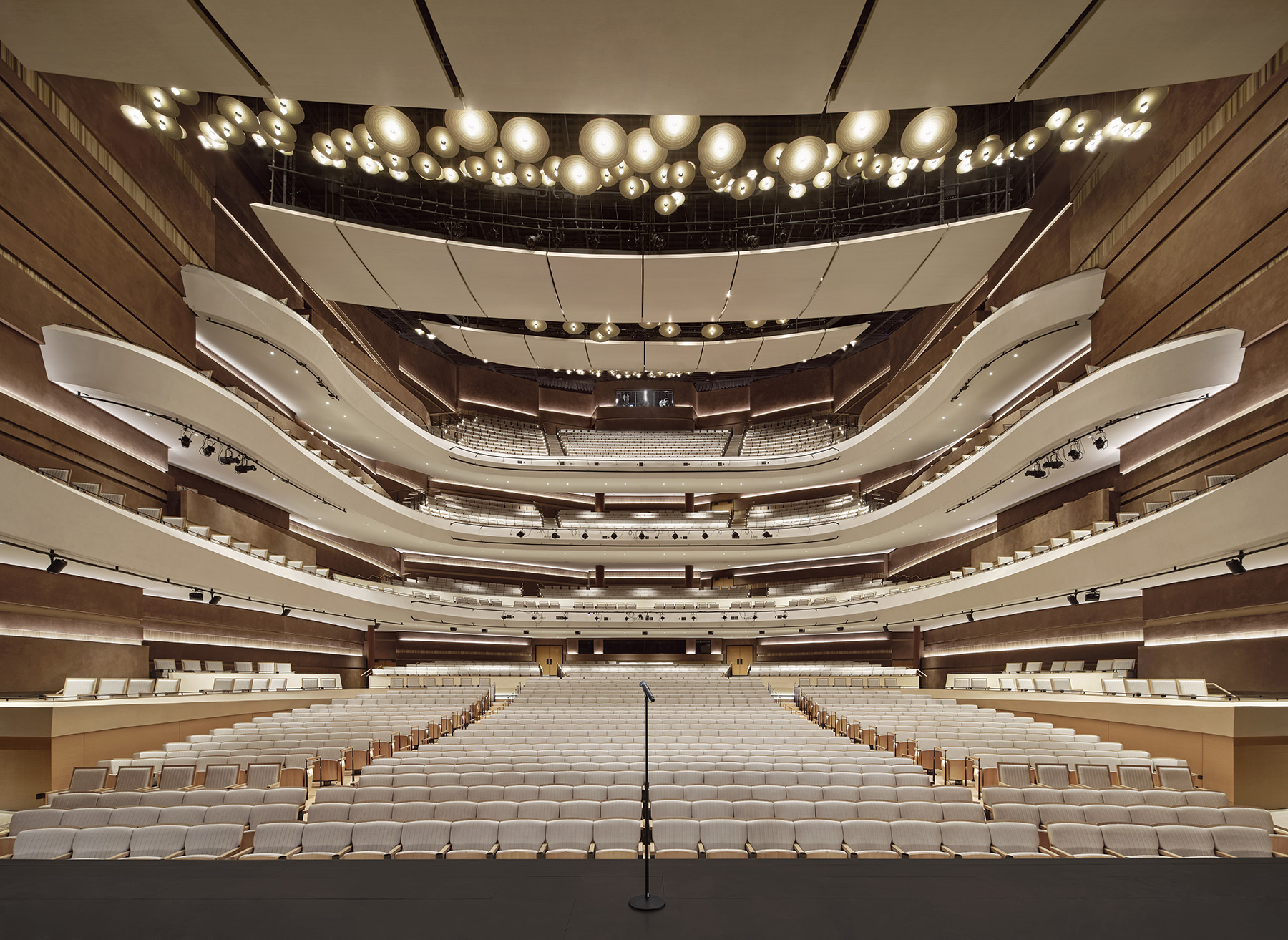
Vibration from rhythmic activities on the balconies was a major consideration, given the large cantilever length of the rakers. The team created a finite element model of the entire audience chamber and used the curved horseshoe shape to its advantage by adding a tension ring member near the front of the balcony to meet the vibration limits.
The horseshoe nature of the balconies also required each of the steel riser members to be bent to follow the curvature of the space. On the lower balconies, standard wide-flange beam sections are used for the risers, which span between the rakers, support concrete on deck for the treads, and serve as formwork for the concrete risers.
However, on the uppermost balcony, the height of the risers meant that the use of standard steel sections was not practical or cost effective, so the team designed a custom steel Z profile that was not only curved but varied in height to follow the profile of the seating. This was achieved by first bending an angle for the top flange and an angle for the bottom flange of the Z, followed by welding a steel plate of varying heights for the web. Web openings were then incorporated to allow for air distribution beneath the seats.
Above the audience chamber a series of structural steel trusses span the space to support the roof, and these trusses perform a second equally important function: supporting a cap designed to achieve the optimal audience chamber volume for acoustics. This ceiling cap required concrete on metal deck with sufficient mass and tailoring of the bottom chord elevation of the trusses. A series of openings are provided in this ceiling cap to accommodate retractable acoustic banners that enable additional tuning of the audience chamber. Suspended below this ceiling plane are catwalks for lighting, deflectors, and a uniquely designed chandelier which is meant to reflect the large, star-filled sky of a typical West Texas night.
The stage is 50 ft deep by 100 ft wide and 87 ft high to the gridiron with a 70 ft wide by 40 ft high proscenium opening. The walls of a theater stage are typically constructed of reinforced concrete, but again, structural steel framing was selected by the team. The walls are framed with steel columns spaced roughly 25 ft apart on center with bays of vertical bracing on each wall.
The requirement for unobstructed space on the stage and the significant mass of the wall necessary to meet the acoustics requirements led the team to use a double-wall construction, with the structural steel framing sandwiched between the exterior cladding system and fully grouted 12 in. wide masonry. To support the exterior cladding and the interior masonry wall, a continuous steel plate cantilevers from a series of horizontal HSS girts.
Group effort
The 415-seat Crickets Theater was constructed using tilt-up wall construction. Form liners were incorporated in the tilt-up wall casting to create the acoustic treatment profile on the walls. The balconies were framed with structural steel, and the roof was created from purlins and trusses.
The basement includes front-of-house services (coat check, concessions, and restrooms), back-of-house spaces (dressing rooms, rehearsal spaces, wardrobe, and workshops), storage, and mechanical and electrical rooms.
The foundations are a combination of shallow spread and strip footings and drilled piers founded on caliche capable of sustaining a net allowable loading intensity of 12,000 psf.
The project had a large and diverse group of stakeholders and best-in-class experts who understood that success depended on collaboration and teamwork throughout all phases of the project. The team worked closely to adhere to the budget, buildable area, users’ needs, and Lubbock Entertainment and Performing Arts Association’s aspirations for the project.
Buddy Holly was an innovative and influential artist who helped define early rock and roll. The Buddy Holly Hall of Performing Arts and Sciences pays tribute to his originality and brilliance with its creative, inspiring design.
BIM enhances collaboration
A unique aspect that invited collaboration on the Buddy Holly Hall of Performing Arts and Sciences project was the fact that three structural engineering firms worked on different aspects of the venue. The scope of work of each firm was tuned to its experience.
Given the complexity of the project, the combined structural engineering team made the conscious decision to share and work in one Revit model for the entire project and produce one consolidated set of construction documents. The use of BIM 360 by Autodesk made possible this level of collaboration and coordination between the different offices in real time.
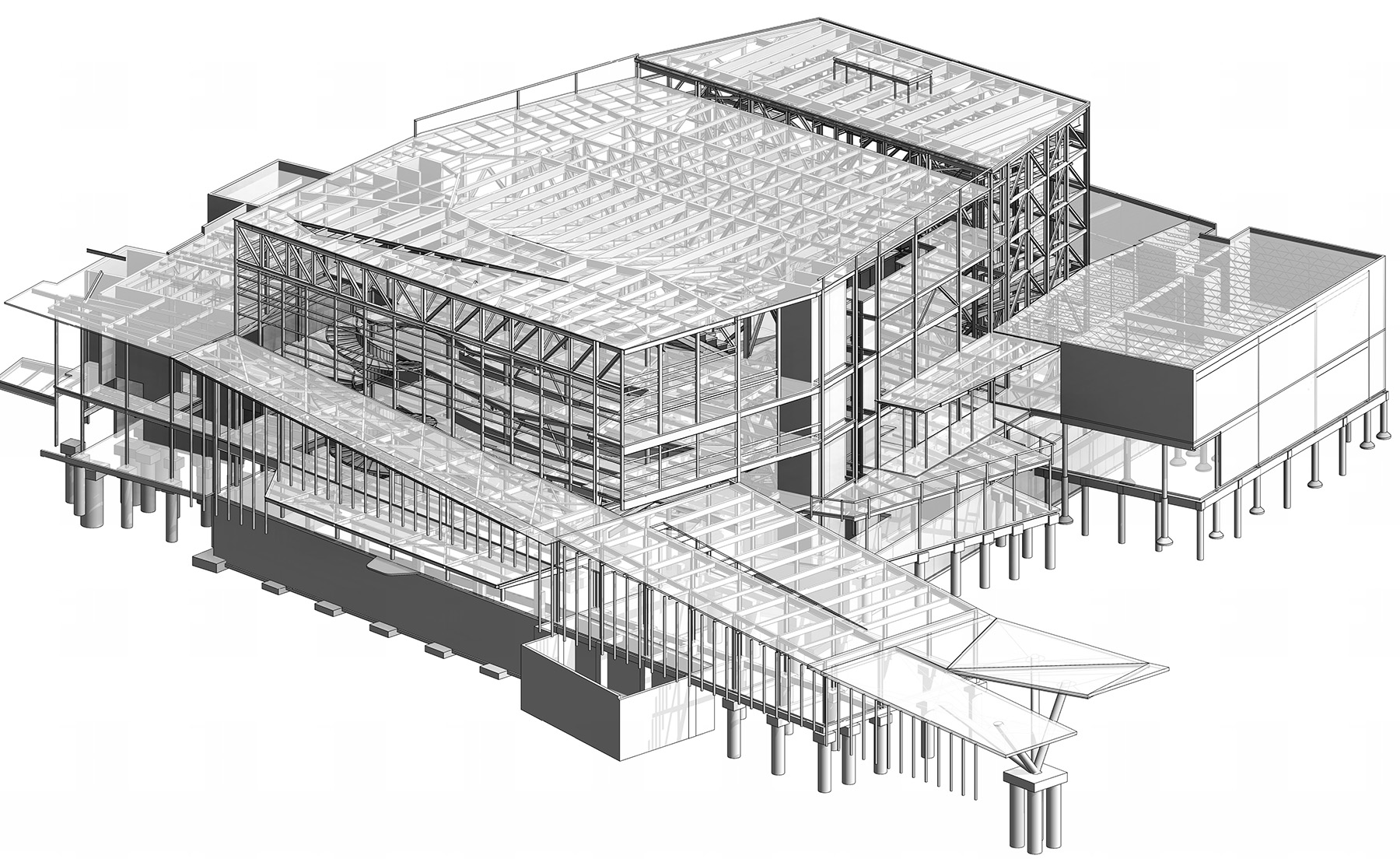
In one example, Entuitive collaborated with Parkhill to achieve the striking bird’s tail shape on the exterior of the building. The Bird’s Tail is a 64 ft by 90 ft covered outdoor venue, and Parkhill was responsible for this part of the project. Entuitive provided initial design consulting to aid Parkhill in bringing this feature to life. The Bird’s Tail is unique in that it is supported by one central column that splays out at four acute angles. The Bird’s Tail takes it name from the two separate sections of the roof that go in alternate directions — one flips down, and one flips up.
Another example is in the Helen DeVitt Jones Theater, in which close coordination between parties was required to ensure that the openings for air distribution in the balcony risers, including the web openings in the fabricated structural steel, were precisely located and centered below specific seats.
Finally, collaboration was also needed with respect to that theater’s stage, at which extensive rigging and lighting required additional steel for galleries, loft beams, catwalks, and the gridiron.
It was great to work collaboratively with the whole team. Entuitive’s team could feel, and shared in, the team’s pride in coming together to create this unique venue for Lubbock, Texas.
Barry Charnish, P.Eng, is a principal and Tom Greenough, P.Eng, is an associate at Entuitive, a consulting engineering firm with seven offices in three countries.
Project Credits
Owner: Lubbock Entertainment and Performing Arts Association, Lubbock, Texas
Developer: Garfield Public/Private LLC, Dallas
Design architect: Diamond Schmitt, Toronto, Ontario, Canada
Architect of record: Parkhill, Lubbock
Associate architect: MWM Architects, Lubbock
Structural engineer: Entuitive, MWM Architects, and Parkhill, Toronto and Lubbock
Civil engineer: Parkhill, Lubbock
Mechanical, electrical, and plumbing engineer: Crossey Engineering Ltd. and Parkhill, Toronto and Lubbock
Acoustics: Jaffe Holden Acoustics, Houston
Theater planner and consultant: Schuler Shook, Dallas
Geotechnical engineer: W.C. Hamilton Engineering Inc., Midland, Texas
General contractor: Lee Lewis Construction Inc., Lubbock
Structural steel fabricator: Basden Steel, Burleson, Texas
Monumental stair fabricator: Beck Steel Inc., Lubbock
This article first appeared in the May/June 2022 issue of Civil Engineering as “Finely Tuned Tribute.”