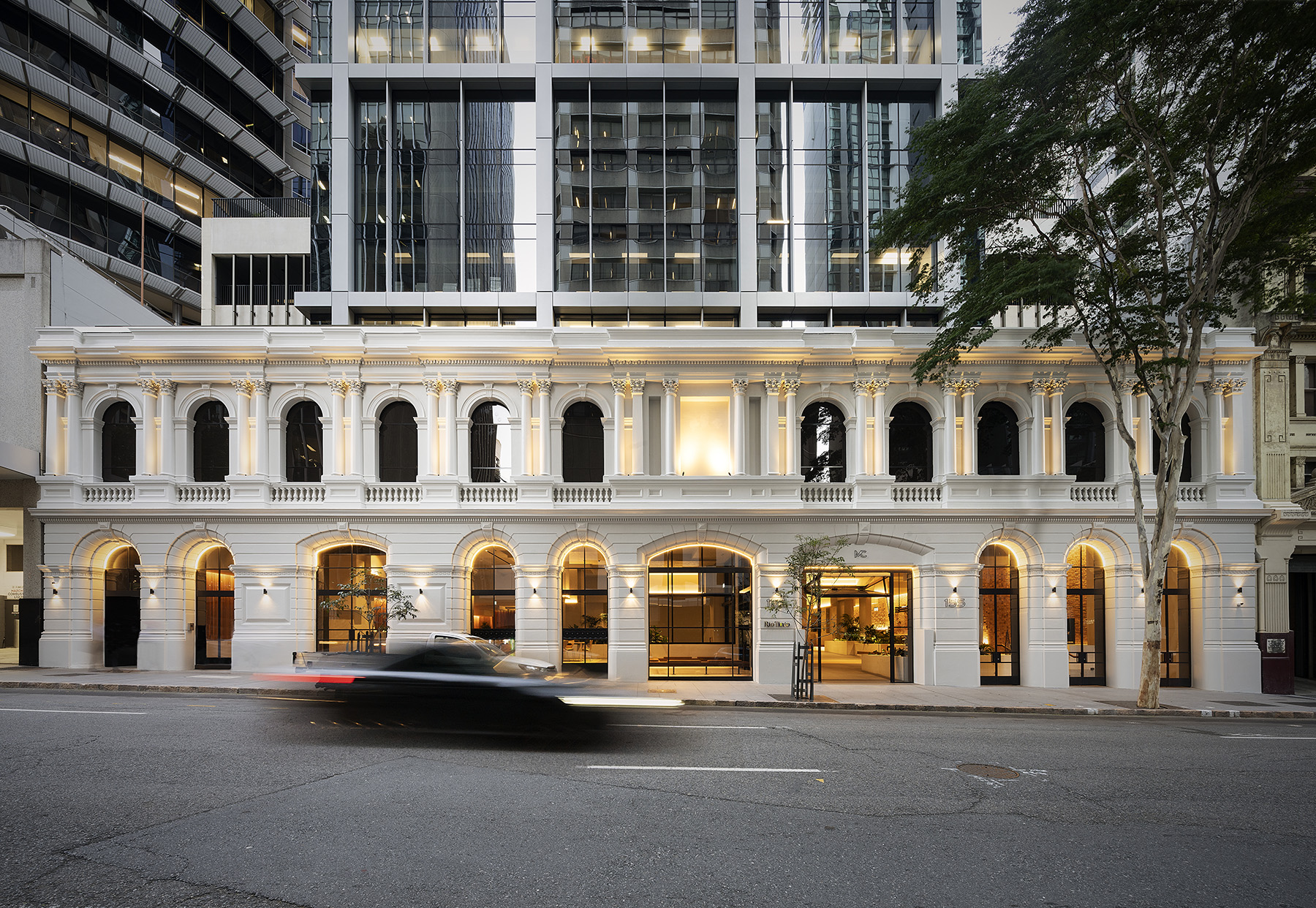
Edited by Robert L. Reid
An innovative project in Brisbane, Queensland, Australia, combined two towers into a single, unified structure. The new mixed-use complex incorporates roughly 90% of the original buildings while decreasing the site’s carbon footprint.
The design and construction of Midtown Centre in Brisbane, Queensland, Australia, was a unique undertaking that repurposed two existing buildings to create a single structure by merging the floor plates and adding seven new levels to the top of the now-combined, mixed-use complex.
Located in the heart of Brisbane’s central business district, the 175 million Australian dollar ($120.7 million) project was designed by the Fender Katsalidis architecture firm for developers AM Brisbane CBD Investments, a joint venture of AsheMorgan and DMANN Corp., which purchased the buildings from the Queensland government.
Inertia Engineering served as the structural and civil engineer. Hutchinson Builders was the project’s general contractor.
Civil Engineering contacted Inertia to discuss the challenges involved in this innovative structural marriage. Two of the firm’s key engineers — Joshua Falco, RPEQ, MIEAust, CPEng, NER, an associate, and Scott Clements, RPEQ, MIEAust, CPEng, NER, managing director — provided joint responses.
CE: Please describe the two original buildings.
INERTIA: The original buildings — each 20 stories tall — were located off Charlotte and Mary streets in downtown Brisbane. Constructed in the 1980s, the two buildings were connected by sky bridges and had been used as state government offices, one for the Queensland health service and the other for the forestry service.
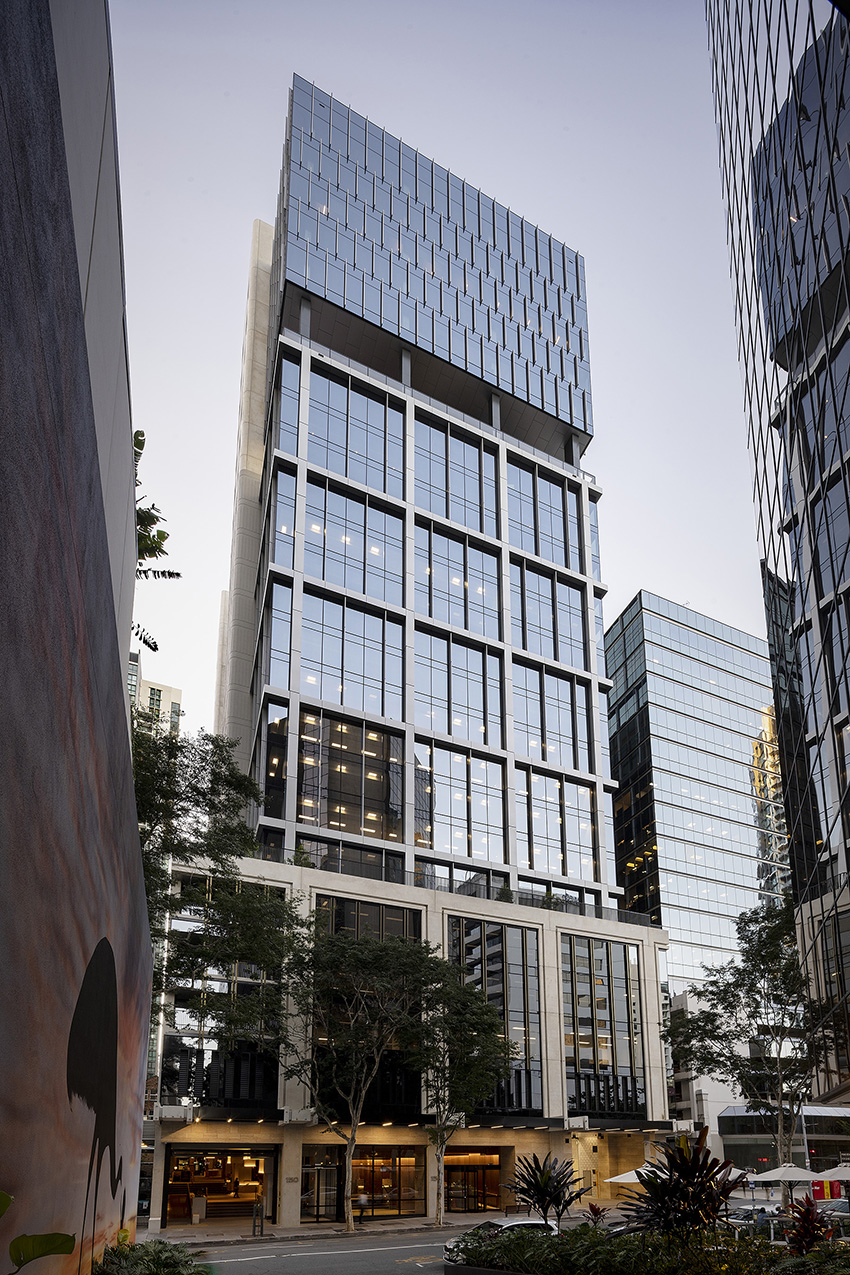
Made primarily from reinforced concrete, both buildings were designed by the same engineering firm — McWilliam Consulting Engineers, based in Spring Hill, Queensland. They were mostly mirror images of each other, except for some differences in the foyers and the fact that the former forestry building fronting Charlotte Street had a historical facade dating to the 19th century.
The original buildings had three key challenges in terms of repurposing the facilities: The existing floor plates were small, the floor-to-ceiling heights were low, and the interior spaces were dark because of the large upstand concrete slabs that blocked portions of the windows. A real estate agent advised the developers that the project needed to solve these three items to have a commercially successful new building.
CE: How did you decide to combine the two buildings into a single structure?
INERTIA: Because the Queensland government no longer needed the two buildings, several schemes had been considered in recent years on how best to capitalize on the existing structures or just the site itself. One concept was to use the buildings for student housing, or both buildings could have been demolished and a new structure built on the site with even more levels than what we ultimately constructed.
In the end, though, the most advantageous idea was to repurpose the original buildings as a new, combined facility. This plan offered considerable benefits in terms of the environment because the resulting new complex would reuse 90% of the original structures while also featuring a lower carbon footprint and producing less pollution than the alternatives being considered.
Timing and the real estate market were other key factors because the two-into-one plan would result in a new complex ready for tenants within just two years as opposed to at least four years for the other proposals.
The completed development offers as much as 42,000 sq m of A-grade office space, a beautifully restored heritage facade that is more than a century old, and new retail opportunities off a converted driveway.
Having decided to combine the original buildings, we then had to decide how to achieve this. We considered several options, including adding floors to the existing buildings without connecting them extensively and linking the two structures and infilling between each existing floor without adding any additional levels. However, the plan we ultimately selected was to connect and enlarge the two buildings by infilling between the existing floors and then constructing additional levels.
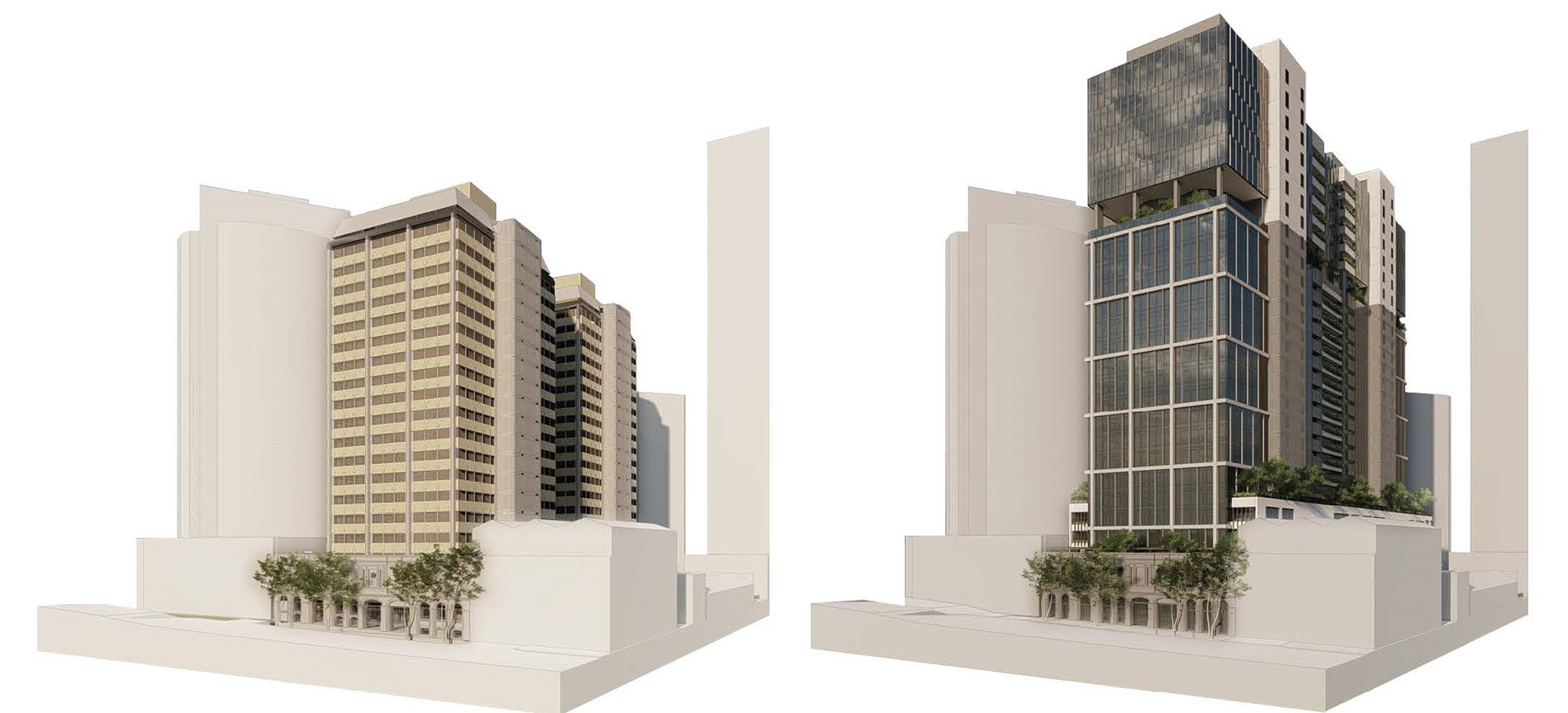
As we researched our chosen option, we could not find any similar projects. There have been other buildings that were enlarged by adding additional floors, of course, and some that added additional space onto the sides. But as far as we could tell, this was the first project in the world to tie two buildings together and add seven new levels on top.
CE: Please describe what was involved in combining the two buildings.
INERTIA: In the buildings themselves, there were no transfer systems, which made analysis of the existing structures a lot simpler, especially because there was only a limited number of original drawings of the two towers available.
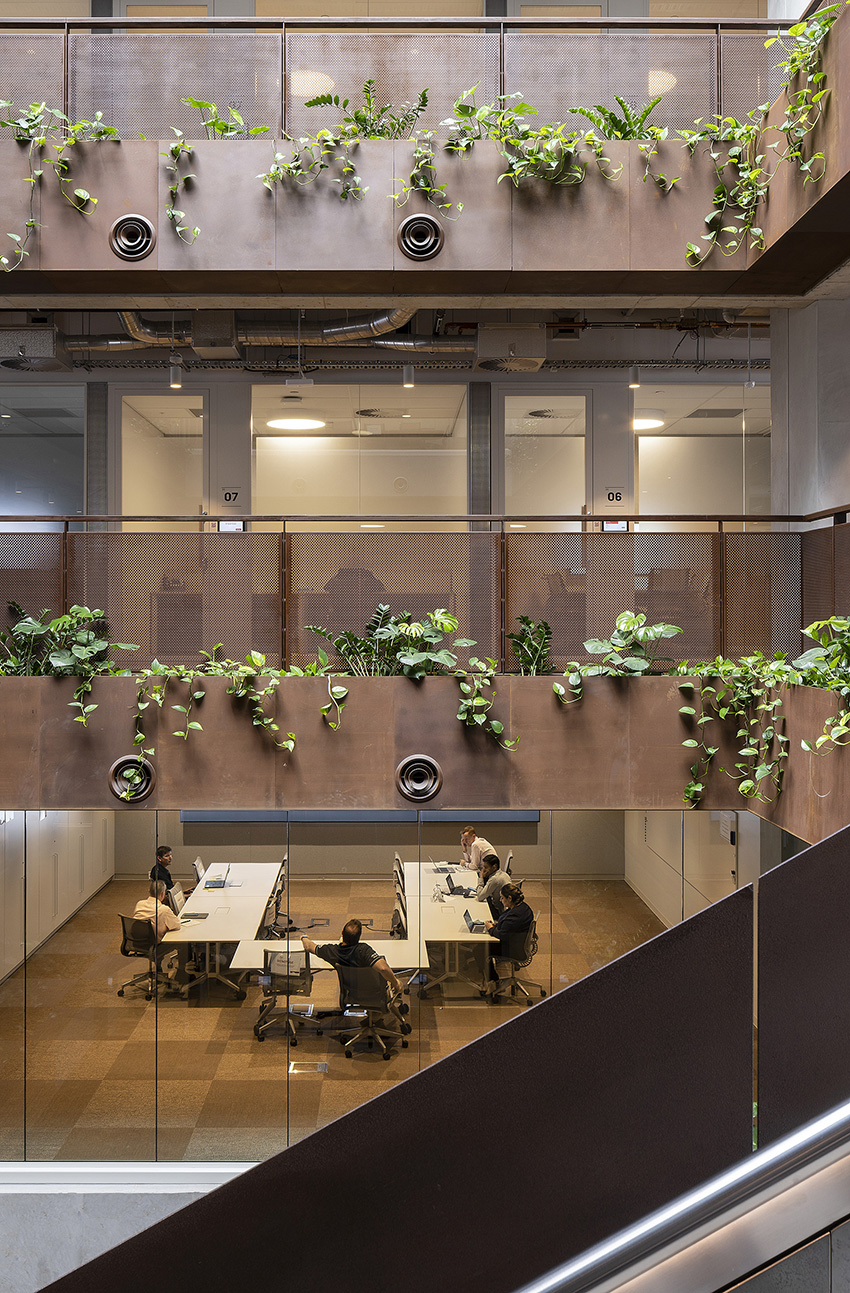
Key aspects of turning the two buildings into one included the addition of infill to most of the existing levels, which created 2,000 sq m floor plates, which were some of the largest in the Brisbane central business district. The infills featured one-way, posttensioned reinforced-concrete beams and slabs that were designed with flexibility in mind so that future tenants could add cutouts for stairs or atriums if required.
We also removed the upstands, which were replaced with full-height glazing. And a considerable investment in time and cost was made to the new mechanical services.
In each tower, the existing level 20 was demolished and then replaced by the first full new level. Each new level also featured one-way, posttensioned reinforced-concrete beam-and-slab construction. In addition, level 20 acted somewhat as a transfer system, supporting a new, double-height, open-air space that features a sky garden known as the Pit and a 250-seat auditorium. Level 21 serves as a mezzanine for the sky garden. Levels 22-26 feature a large central atrium topped by a skylight at the level 27 roof, which provides natural daylighting for the auditorium at levels 20 and 21.
The floor-to-ceiling heights in the original buildings measured 3.3 m tall, while the heights of the new levels vary between 3.8 m and 4 m.
CE: What were some of the engineering challenges you had to overcome?
INERTIA: The nature of the existing ground material — known as Brisbane tuff, which has an allowable bearing capacity of 10,000 kPa — made excavations difficult. But fortunately, no groundwater was encountered.
The major structural challenges we faced included the need for new foundations in key locations and the strengthening of the existing square pad concrete footings. Installing new footings posed a challenge for the general contractor because of the strength of the rock and the limited height and space available for excavations.
We did not want to undermine or expose the existing footings because they were supporting significant loads. As a result, we designed a system to ‘wrap’ around the existing footings. Two sides of this wrap featured concrete beams used to bear the new loads while on the other two sides were tensioned beams used to pull the bearing beams into the existing pad footings. The system also used multiple dowels and a special concrete mix.
Other work involved column analysis and strengthening, which required us to determine the strength of the original concrete and whether the original columns had been installed as per the existing drawings. We also had to determine how to strengthen the columns and what would happen when an entire level was removed.
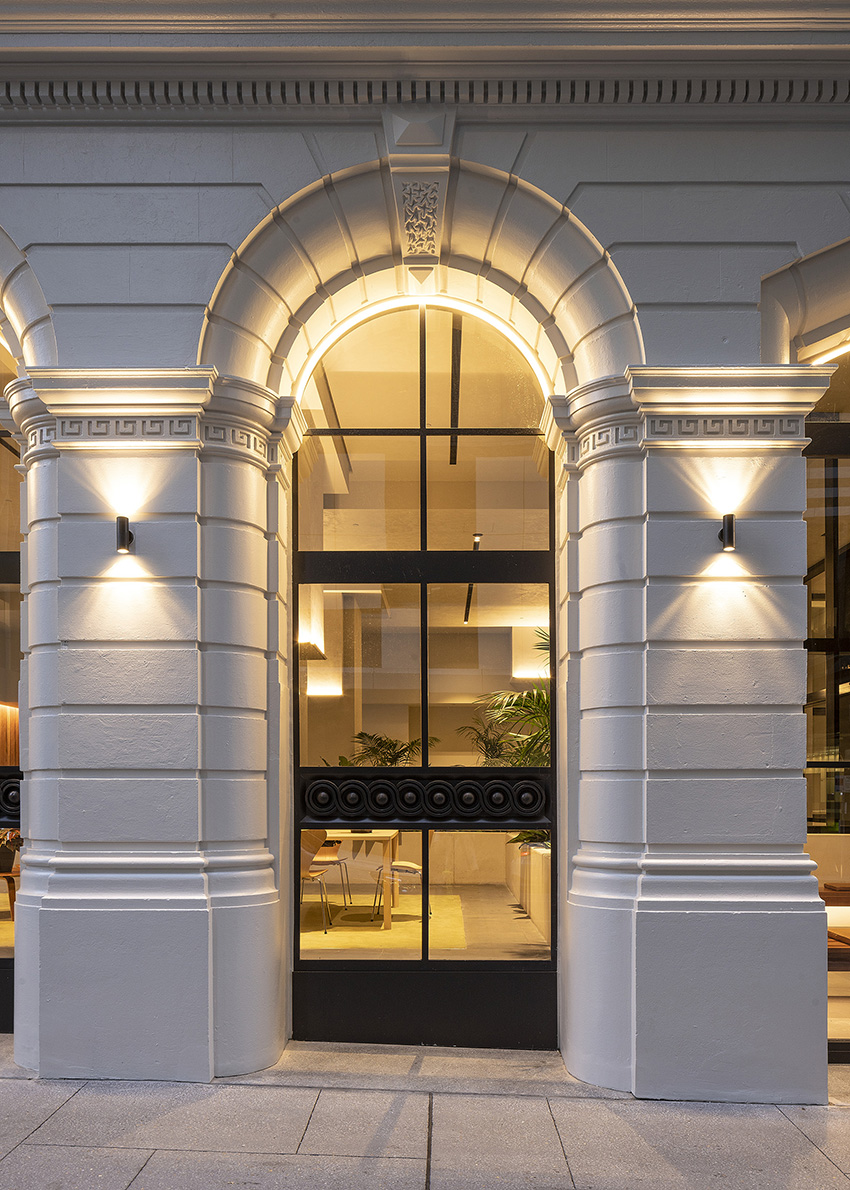
New columns were needed, starting at the basement level, to support the new infill sections. These aligned with the existing columns but required their own new footings. In addition, the increased loads imposed by the seven new levels required an increase in the size of the existing perimeter footings.
The new columns required axial shortening in comparison to the existing structure with a predicted differential of up to 20 mm. When we infilled the spaces between the original levels, we placed the new concrete flush with the existing levels and existing columns, which had already experienced creep and shrinkage over the decades since the buildings were constructed.
But there was a risk that the new columns would shorten after loading and thus create an unwanted step between the new and existing floor levels. To prevent this, we considered the use of high-strength concrete, composite columns, and many other options but concluded that precast concrete columns at 80 MPa would suffice. We decided to place the concrete for these precast columns at least 28 days in advance of their installation to eliminate the potential for shrinkage at the site.
We also had to strengthen the core. The existing core consisted of reinforced concrete with tie-down anchors. Following a wind analysis, conducted by MEL Consultants Pty. Ltd. we realized that the additional levels and infills did not create any issues related to tension, but they did for compression. To resolve this, a concrete strengthening wall was attached to critical sections of the core. Due to the varying strengths of concrete used throughout the building, ranging from 25 to 40 MPa, this strengthening system extends from levels 2 to 19.
CE: What work did you do to the buildings’ facades and interior spaces?
INERTIA: During a series of design reviews, we determined that the existing restrooms were suspended off the floor slabs on the eastern side of each building via full-height concrete walls on the perimeters that acted as beams. Additional reinforcement was added to these slabs to tie the perimeter walls back to the cores within each tower. The restrooms were rearranged and increased in size to bring the building up to current standards from a tenant-use perspective.
For this rearrangement, plus the addition of new mechanical systems, new loadings were imposed on and new penetrations made in the structural systems on the eastern sides. We, therefore, changed the structural behavior of these areas by adding columns and beams to create a simple, conventional system.
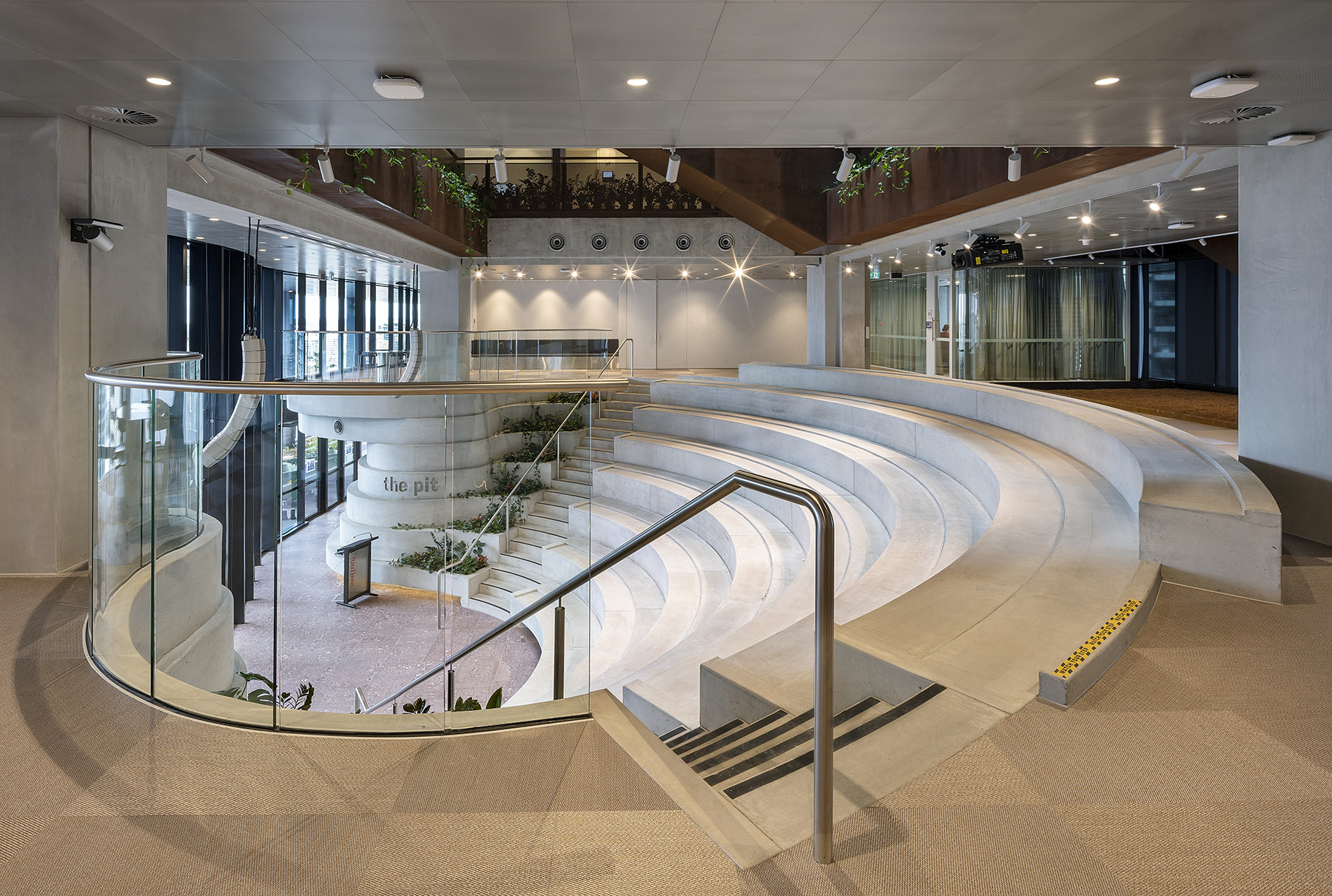
We also removed the existing facades of the original buildings, which were made of reinforced concrete and featured a precast panel cladding. Once the original facades had been removed, we extended the slabs 700 mm to match the edges of the existing columns. This, in turn, allowed for recessed facade attachments, which were simpler to construct and that also created significantly more gross floor area for the new combined complex — roughly the equivalent of constructing a full additional level.
At the ground level, a former driveway that had serviced the basements of the towers was converted into a new public retail space known as the Lane-way, which connects Charlotte and Mary streets and provides access to the new foyers. The reconstruction of the Mary Street foyer was made possible because the existing electrical supply needed to be increased, which required that an existing substation be demolished and reconstructed above the foyer level.
The foyer on Charlotte Street is reserved for the Midtown Centre’s major tenant, the mining conglomerate Rio Tinto. Here, the existing first level above grade was demolished to create a 7 m tall space adjacent to the heritage facade, which was strengthened to accommodate the removal of the interior slab and aesthetically restored.
Within the towers, the lower levels featured small spaces that had been compared with rabbit warrens. These spaces were opened up and the structural systems strengthened to accommodate the larger spaces that resulted. Other interior changes included the installation of new freight elevator systems — the walls of which helped to improve the structure’s lateral stability — and new enclosures for the existing fire stairs. These stairs were reduced from the original four to just two, a fire engineering solution made possible by joining the two towers.
CE: What were the environmental benefits of repurposing the original buildings into a new complex?
INERTIA: During the planning stages, the developers commissioned Edge Environment Pty. Ltd. to undertake a high-level life-cycle assessment of the potential environmental impacts from two of the key design scenarios. These scenarios focused on either demolishing the existing buildings and then constructing an entirely new building or refurbishing, retaining, and merging the two buildings.
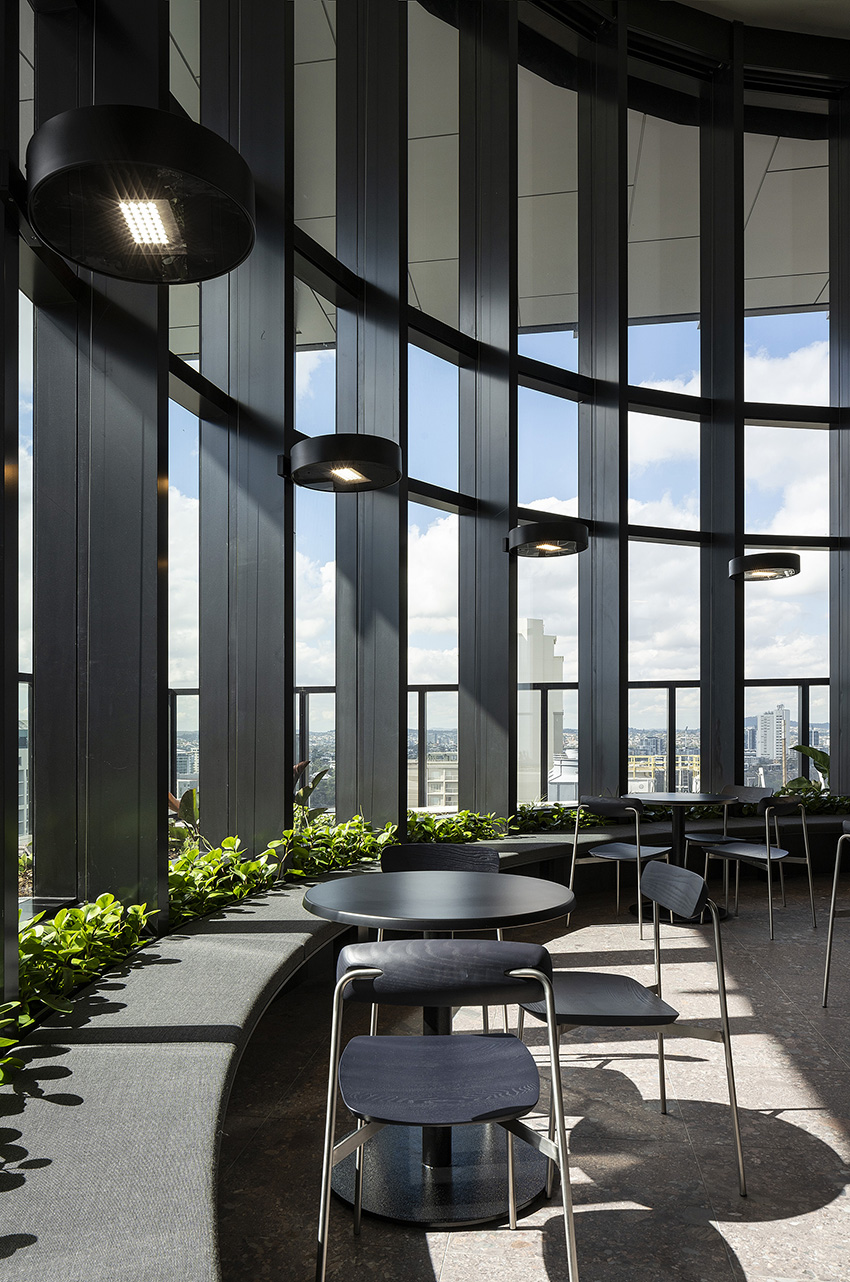
Comparing the two scenarios over a 15-year time frame, Edge Environment determined that the plan to refurbish and merge the two buildings would result in 36% less carbon emissions than if the original buildings were demolished and a new building constructed, especially in terms of operational energy and materials used.
Based on an estimated ‘social cost’ of carbon — focusing on the social impact of the project design scenarios — the analysis also determined that the refurbish-and-merge plan would ultimately have a social cost of roughly AU$3.6 million versus AU$5.7 million for the demolish-and-rebuild plan.
CE: What was the project timeline, and what can other engineers learn from this project?
INERTIA: The design phase started in June 2017, and Hutchinson Builders began work on-site during the summer of 2019. The completion date was in June 2021. This has been a fantastic project for Brisbane and a huge engineering feat for everyone involved. Although the project can appear to have been quite tricky, the most important items in getting it done right were our basic and fundamental understanding of structural design.
Constant communication with all consultants and builders was also critical. A key member of Inertia’s team worked closely with the construction team to oversee all facets of the construction procedure, spending six months at the site, working with the site manager and the multiple construction teams.
Summing things up, the Midtown Centre is a fantastic example of how buildings can be repurposed. As we see changes to working patterns, a move to more flexible working arrangements, and the use of technology for remote working, there needs to be a change in thinking about future design. That will involve taking established buildings and giving them a new lease on life. In a city like Brisbane, where construction costs are at the top end of the scale, this approach makes economic sense for developers and benefits the community by taking sites that could become outdated and unloved and turning them into cutting-edge, modern structures.
Robert L. Reid is the senior editor and features manager of Civil Engineering.
Project credits
Client: AM Brisbane CBD Investments, a joint venture of AsheMorgan, Sydney, and DMANN Corp., Brisbane, Queensland, Australia
Architect: Fender Katsalidis, Brisbane
Structural and civil engineer: Inertia Engineering, Brisbane
Service engineer: BSE, Brisbane
Geotechnical engineer: Pacific Geotech, Coomera, Queensland
Wind analysis: MEL Consultants Pty. Ltd., Melbourne, Victoria, Australia
General contractor: Hutchinson Builders, Brisbane
Life-cycle analysis: Edge Environment Pty. Ltd., Manly, New South Wales, Australia
This article first appeared in the November/December 2022 issue of Civil Engineering as “Structural Marriage: Two Become One.”