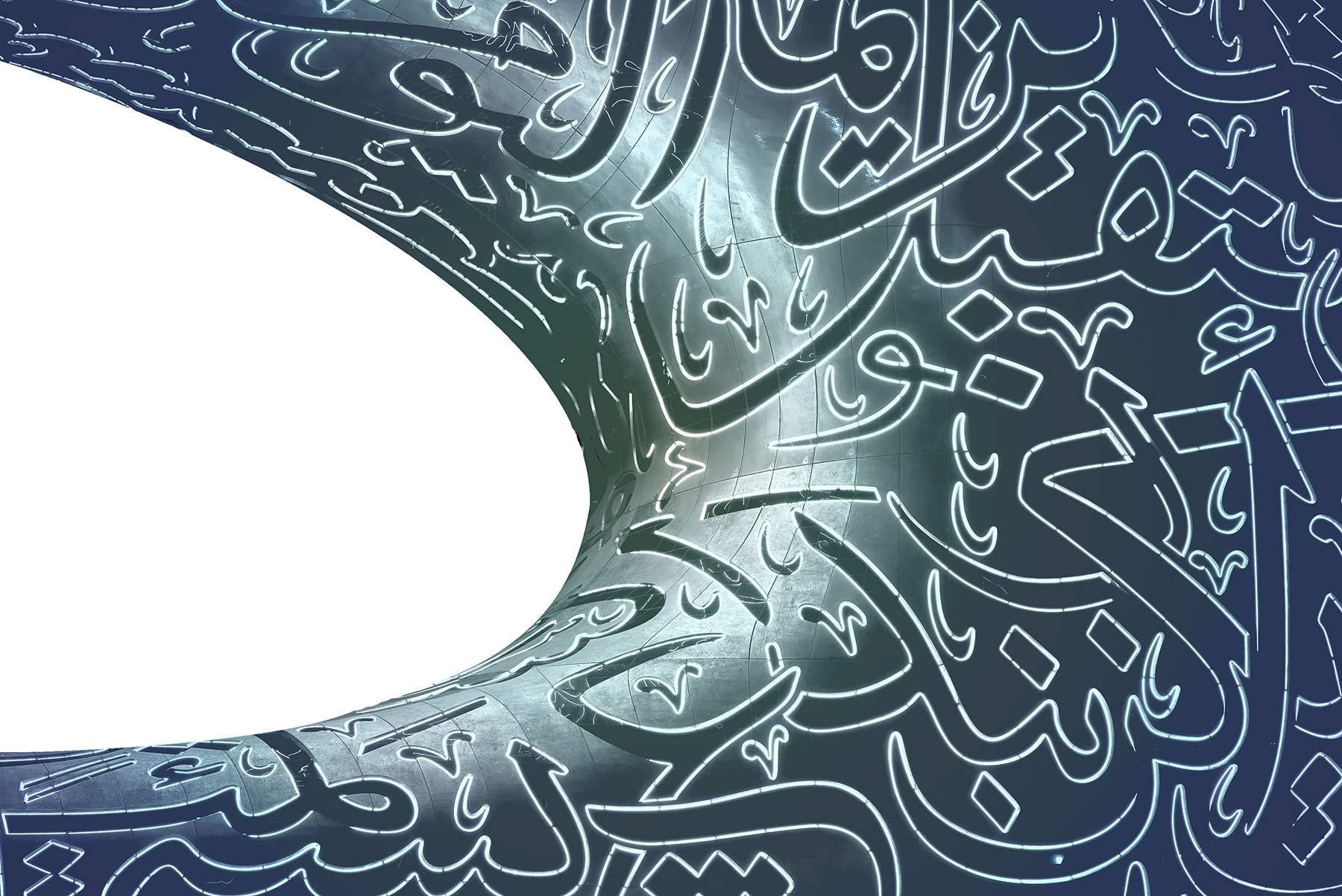
By Tobias Bauly, MICE, CEng
Overlooking the autonomous metro system near the financial district in Dubai, United Arab Emirates, the Museum of the Future is a striking landmark — a dramatic, unconventional structure that is a symbol of progress and innovation. Covered in windows that form calligraphy, the facility is a geometrically challenging and environmentally green creation, and its unique and complex shape sets a new standard for digital design.
Designed by architect Shaun Killa of Killa Design, the site is composed primarily of three artistic elements: the green mound, the museum building, and the elliptical void. Front- and back-of-house functions are within the vegetation-covered mound, which, according to Killa, “represents the earth, with (its) solidity, permanence, and rootedness in place, time, and history.”
The museum building’s unique torus shape represents the “eye that sees tomorrow,” per a museum press release. The building’s stainless steel facade is covered in windows in the form of Arabic calligraphy depicting quotes from Sheikh Mohammed bin Rashid Al Maktoum, the ruler of Dubai. The script is considered an embodiment of the museum’s purpose as an incubator of futuristic ideologies and technologies.
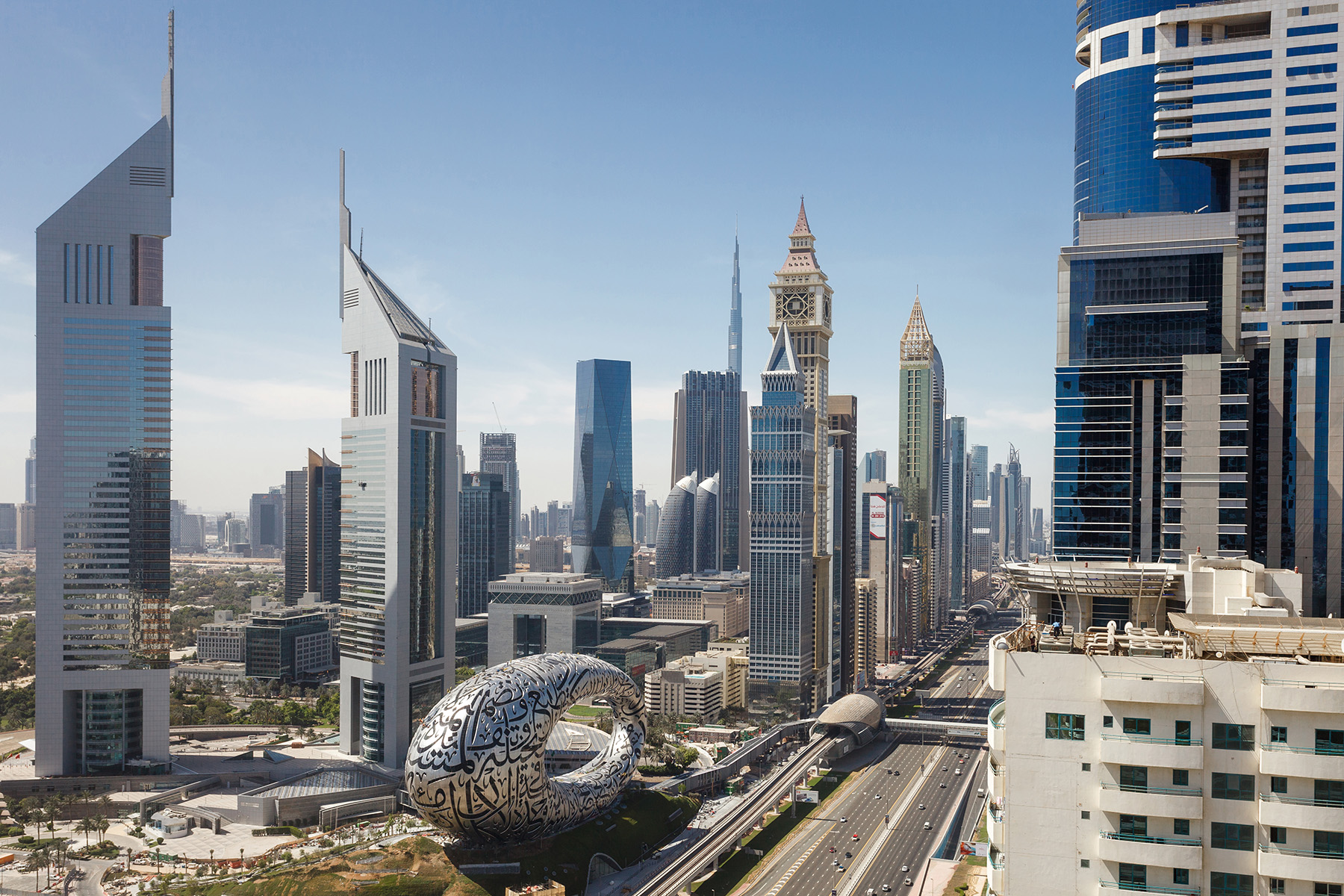
And lastly, the elliptical void created by the museum’s torus shape is a visual illustration of the unknown, of what is yet to be created and discovered.
At 77 m high, the museum building has seven floors — five for exhibitions and two for back-of-house operations and events. There is also a three-story podium that includes a 420-seat auditorium, restaurants, lobby, retail, parking, and other services, according to the architect’s website.
The museum affords visitors opportunities to explore and imagine a better future as it relates to the fields of climate change, ecology, space travel, future and emerging technologies, and health and wellness, among others.
All these elements combine to form an interactive, futuristic, and fantastical site that inspires all who come to experience its wonders.
Making the impossible possible
The Dubai Future Foundation, which owns the museum, set out its bold vision for a state-of-the-art exhibition facility that would prioritize energy efficiency, arrange the exhibition space in a clever fashion, and achieve Leadership in Energy and Environmental Design Platinum certification.
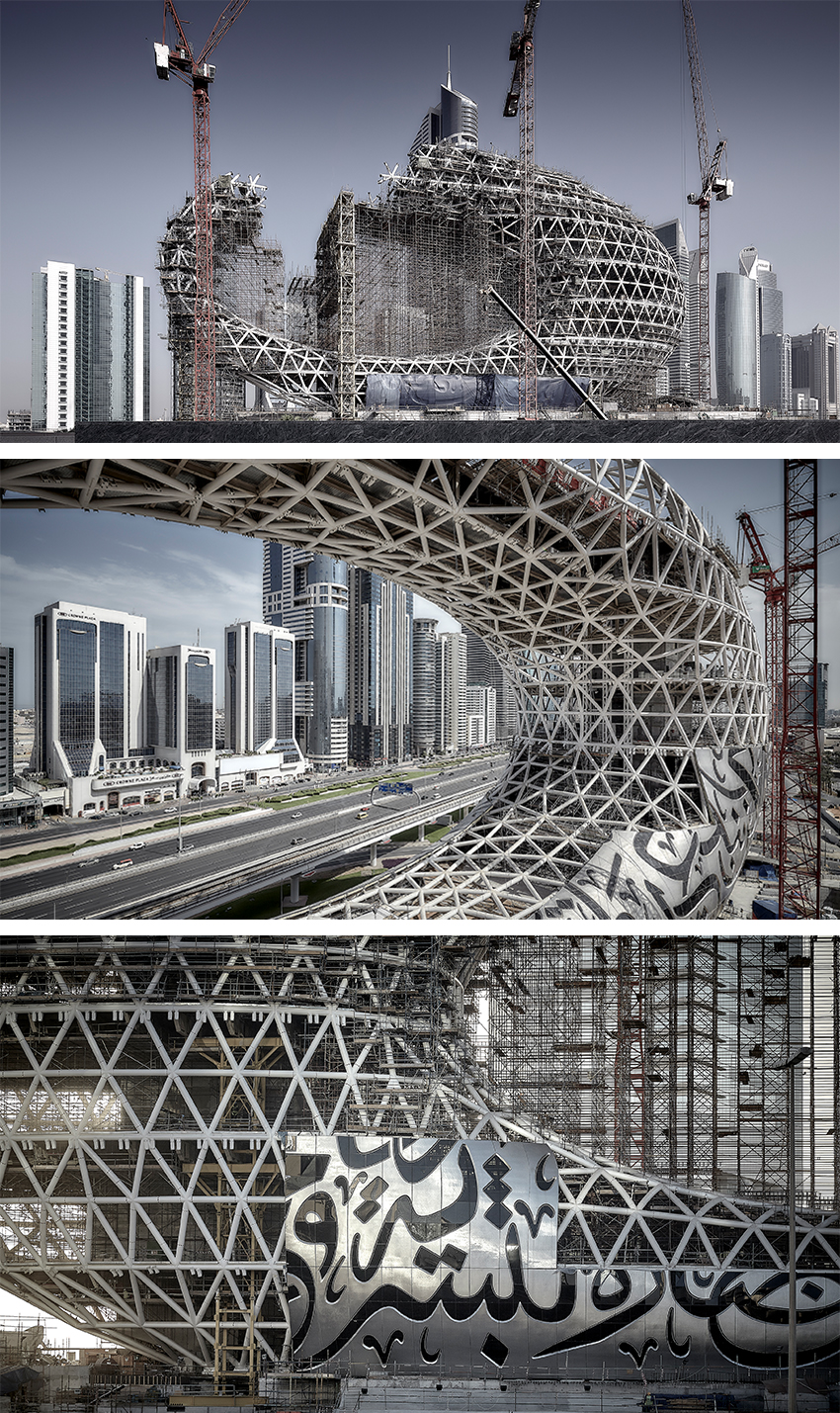
Presented with the architect’s groundbreaking design, Buro Happold’s engineers needed to determine how to build a feasible structural solution — blended with all the other critical aspects of the building — without deviating from the original design. Simultaneously, they also needed to balance efficient material use with buildability and building systems integration.
The starting point for the project team was to evaluate a variety of conceptual structural solutions to deliver the torus shape of the building. From there, the team progressed to studying concrete shell and steel-plate forms as well as more unusual options such as timber-based shells. A structural shell element for the outer surface proved to be effective on initial structural models and would ensure the exhibition areas were column free.
After conducting research, the team selected a steel diagrid as the most viable option for the building’s shells based on performance, buildability, and, more unexpectedly, logistics. Because the building sits in the middle of the city, every structural piece was restricted by size to only what could be transported on inner-city roadways; therefore, a jigsaw piece transport-and-assembly approach would be needed.
The next step was the seemingly impossible task of developing the real geometry of each element, taking into account how the geometry integrated with the floor levels, the facade thickness and its thermal performance requirements, the calligraphy windows, and other geometric and discipline requirements.
It became clear to the project team that a pioneering use of engineering technology would be required.
Pushing the boundaries of digital design
At a time when technologies like digital twin and building information modeling were not yet widespread, the team was entering an unexplored space in the field of digital design, prototyping these very principles.
The concept for the building’s shape was one challenge, but delivering this shape while integrating the different disciplines to deliver a high-performance exhibition facility was another challenge entirely. Early in the process the design team realized it needed to develop a set of custom digital design tools for this project, tools that proved to be essential for unlocking the architect’s vision.
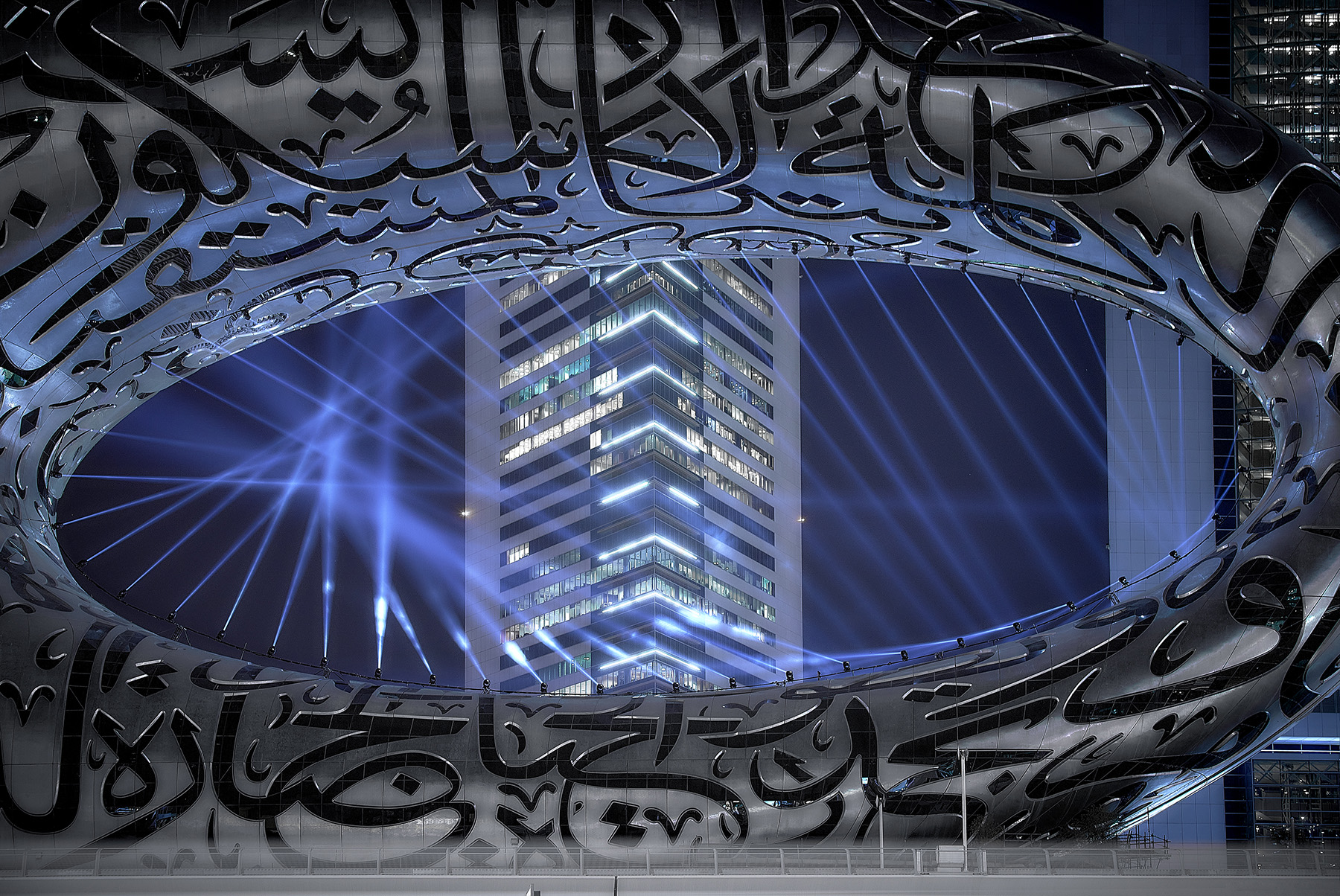
Using computational tools, Buro Happold created a bespoke growth algorithm to “grow” the theoretically optimal arrangement of the steel diagrid structure. The engineers built into the algorithm a range of design criteria and geometric rules, including common element diameter size, to attain a consistent facade thickness, assist in procurement of materials, and lower the cost. With a single element diameter, the connection design and fabrication process were also optimized.
The various lengths of the structural elements were also constrained by the transportation logistics. These constraints required curved members, again facilitating efficiency in the design and fabrication processes.
Set to run, the algorithm generated thousands of theoretical geometries before converging to provide the final design.
From the moment the final diagrid geometry and member sizing were defined and the steelwork fabrication and erection chosen, no element diameter or design element length was altered. This astonishing feat had endless benefits for the project in terms of risk, cost, quality, program, and safety. It also ensured that only the minimum amount of material was used to deliver the main structure of the building.
Modeling the future
The project began in 2015, and Buro Happold and Killa Design spent about two years developing what was effectively a full digital prototype of the building. The digital model of the diagrid design evolved to become a comprehensive 3D model of the building, turning upside down traditional ways of working.
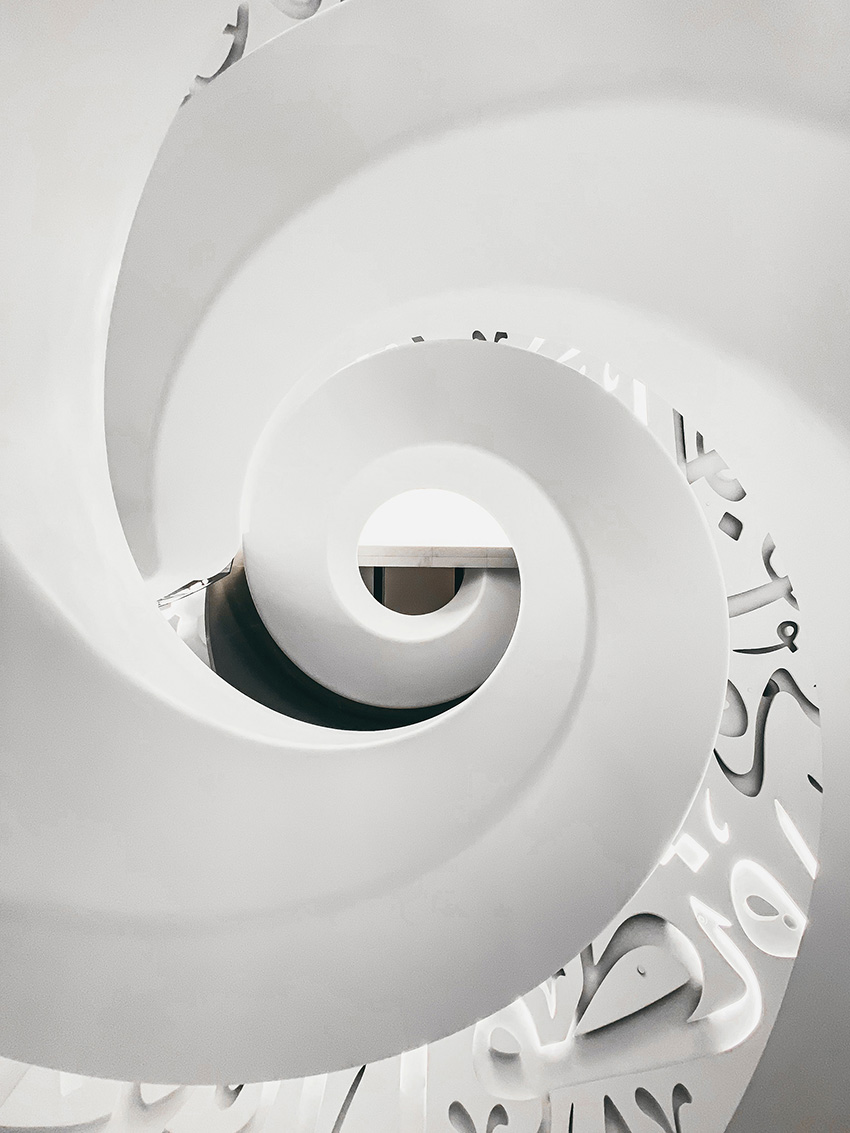
What made this stage of the design process noteworthy was that instead of having only a conceptual level of input from engineers during the concept design stages, there was input into the digital model at the outset from the architectural and engineering disciplines. As a result, the design team consisted of nearly 40 people from different disciplines, which was a complex undertaking. However, in the end, it removed many of the typical quality and time risks that are encountered during later construction phases.
The prototype digital model was also essential for determining the facade. The Museum of the Future occupies an overall area of 30,548 sq m. The exterior is composed of 1,024 stainless steel-clad glass fiber reinforced plastic panels — each unique in size and shape — integrated with more than 10,000 bespoke pieces of glass that give the calligraphy its shape. LED lighting outlines each calligraphy window.
The team used the digital model to position the calligraphy glass panels on the surface. This allowed the shape, size, and positioning of the calligraphy fonts to be adjusted to ensure diagrid connections would not be visible through the windows or block the light.
The glass panels were treated locally and cut into individual shapes using water jets before placement into the GFRP panels. Here again, the technology helped the design team achieve what many would consider to be logistically infeasible. The team was concerned about the viability of creating digital cutting patterns for the thousands of different glass shapes, but it was a much speedier process than expected when the analytical modeling was set up.
The water jet machinery followed the “path” the data provided; the machinery was indifferent to whether the pieces were identical or not. This meant the team could match the glass panels to the calligraphy created by artist Mattar Bin Lahej.
Modular construction is a recent push in the industry, and the museum’s facade panels are an example of a modularized approach, where the digital data enabled vast variability in the end product. The milling of the facade panel molds was an identical manufacturing process for each facade panel, but it was based on different geometric data for each mold.
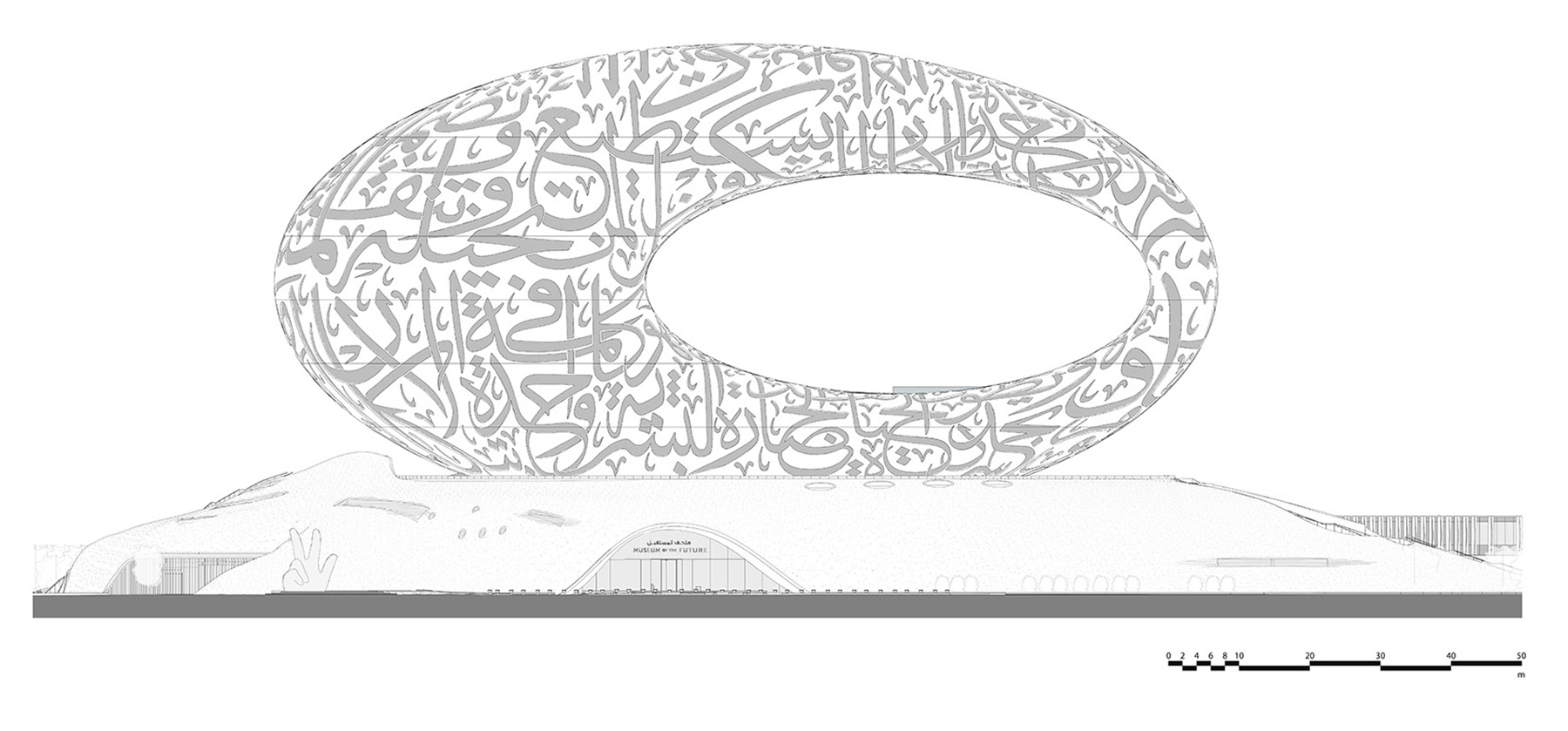
Further, the openings in the chassis (into which the glass was laid) and the laser-cut shapes of the stainless steel (bonded to the chassis) are all geometric variations but together form an overall modularized system of manufacturing. Without the design digital data to bring fabrication efficiency into what is a widely varied product, the facade panels would not have been achievable in their current form.
Fulfilling its green goals
The client envisioned a building symbolizing present and future innovation, but it also needed to be energy efficient. Delivering an ultra-energy-efficient building required the project team to again harness its digital capabilities. Energy modeling was integrated within the 3D digital prototype, allowing for interaction between the full range of engineering and architecture disciplines in real time. The design could be altered to make energy savings where possible but in a holistic manner across a number of disciplines.
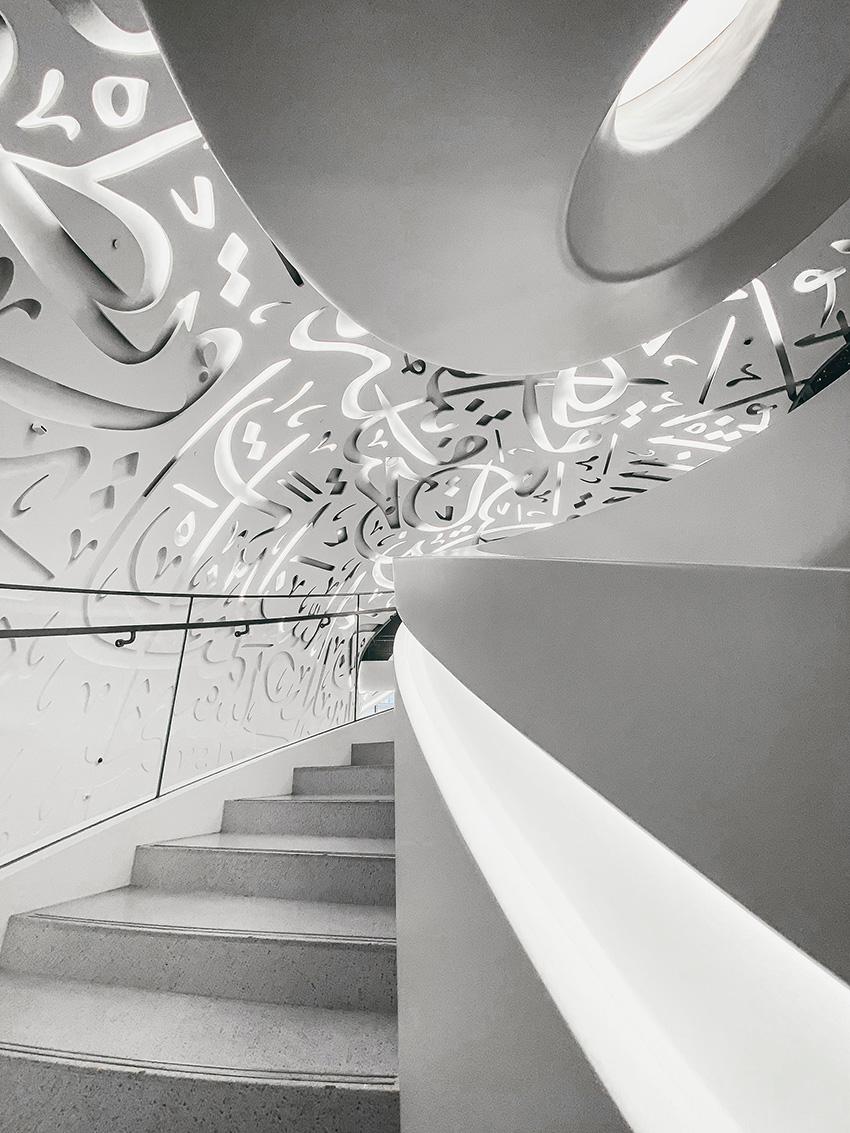
The areas of calligraphy glazing were determined by parametric scripting in order to optimize energy use, balancing thermal gain; light entering the museum; and heating, ventilating, and air conditioning system designs. With the energy optimization and high-specification glazing, the facade blocks external heat 66% better than the regulatory requirements in Dubai while still permitting daylight to enter the building, further reducing reliance on internal lighting.
Additionally, the museum has its own green power source. A dedicated solar farm provides a direct power link to the building, supplying 30% of the building’s power demand. Because of its energy-efficient design, energy use has been reduced up to 50% compared with a conventional exhibition building of a similar size. The site is on its way to achieving LEED Platinum certification. Digital design made this possible.
Energy efficiency continues to be paramount now that the building is in operation. The Dubai Future Foundation has continued to build on the digital foundations laid by Buro Happold by adopting and developing the same project information produced from the digital prototype to operate the building. Sensor technology has been added to the building, taking the project one step closer in form to its digital twin.
Another sustainability effort included transforming an existing parking lot into a leafy haven at the heart of the city, and the building itself is positioned on a landscaped green mound replete with trees and other plantings. A concerted effort to minimize water usage led to the design of a novel, gray water recycling system. Wastewater from the building and the site’s water features are used to irrigate the green mound and surrounding trees, while a recirculating collection system ensures any drainage runoff is recaptured.
And to further the project’s green goals, the design team limited visitor parking. Instead, the museum encourages visitors to travel on foot or use public transportation. New pedestrian bridges that connect to the Dubai metro system were built to further discourage car use and provide an indoor route to the museum, which is especially useful during the hot summer months.
A safe building environment
The more complex a building’s structure, the greater the number of health and safety hazards during its construction. Keeping workers safe posed a number of challenges for the design team.
BIM helped solve these issues by permitting the design and contractor teams to sequence construction, computationally predicting sequential structural movements during construction and allowing the teams to compare real-time movements on-site with movements using the virtual models.
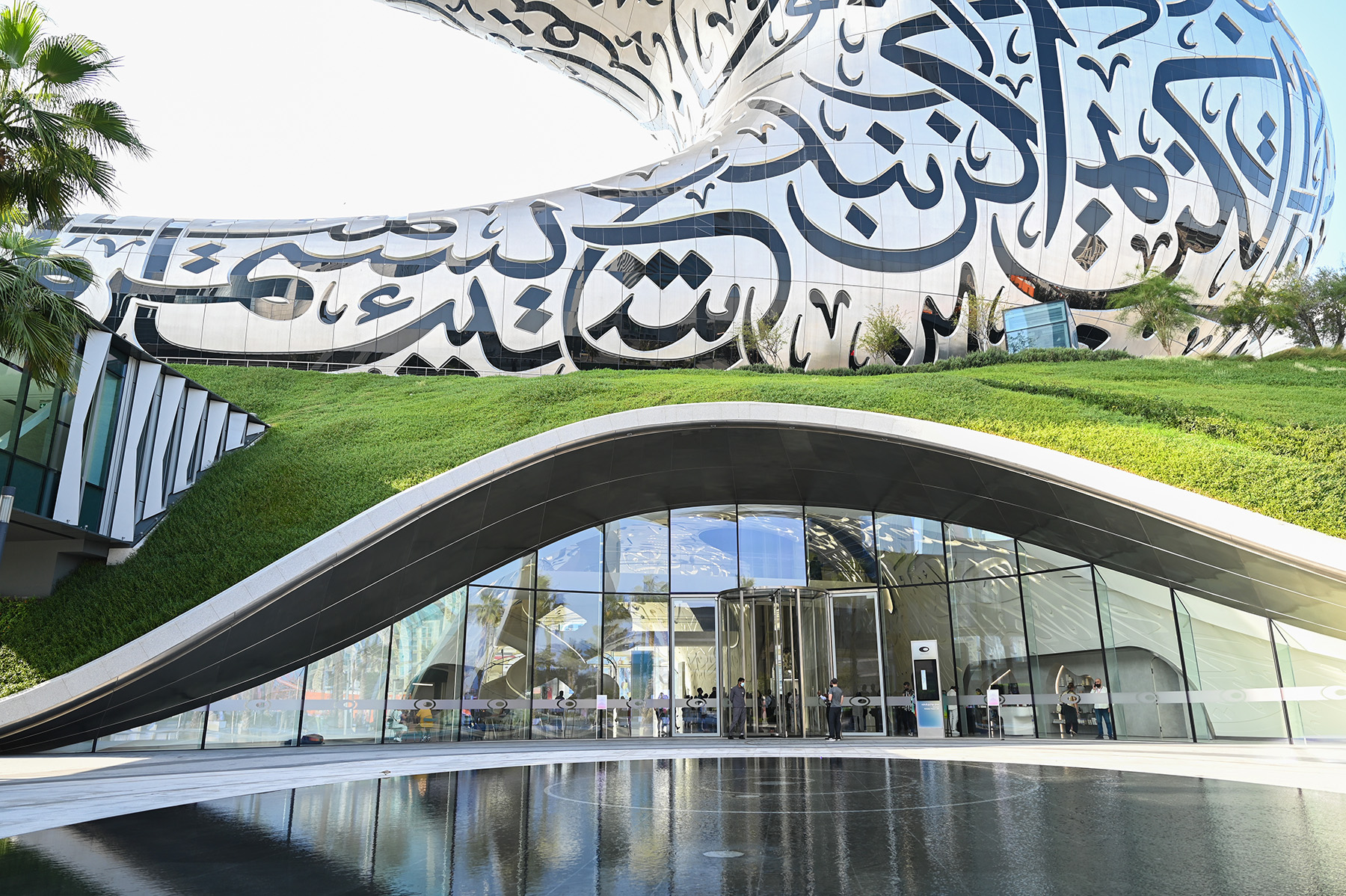
The project’s main contractor, BAM International, continued the digital push, driving further innovation through its own construction practices and those of its subcontractors. The BIM model that BAM developed brought together the bespoke geometry of the building with the installation of all the work programs: diagrid; mechanical, electrical, and plumbing; facades; lighting; fire systems; finishes; etc., down to the smallest duct hangers and door handles.
The level of health and safety risk that BAM removed through the digital model — by defining and understanding work fronts, work sequencing, and individual installation activities — was instrumental in the firm attaining an exemplary safety record for the project.
The models and available information also enabled the streamlined delivery and erection of temporary works, and assessments could be made about the locations of crews working at height as well as complicated crane lifts and jacking and dejacking operations.
The digital design approach taken — be that BIM or specific activities related to the structural engineering design — lowered the level of risk on the project during construction.
The 3D model also played a part in creating a safe building environment for occupants. The team used the 3D model to virtually analyze movements within the building. As a consequence, the team could identify points of congestion, pinch points, and queueing patterns during everyday building use as well as simulate evacuation strategies in a fire scenario.
The building operator will continue to use a version of this model to carry out fire and life-safety analyses as well as conduct evaluation strategies to assess movement during different types of events.
Sharing the wealth
The level of innovation that was re-quired to deliver such a complex building, especially in the digital sphere, was a learning curve for the core design team and the wider teams involved. Digital modeling revolutionized the way work was performed. A major change like this does not come without its difficulties, but the exhaustive and comprehensive planning put into developing the 3D prototype paid off in the end.
The Buro Happold team was eager to share what it learned from the project in order to help the industry evolve and benefit from a computational approach in engineering. The team has captured these solutions in the form of written code that can be adapted and used on other projects.
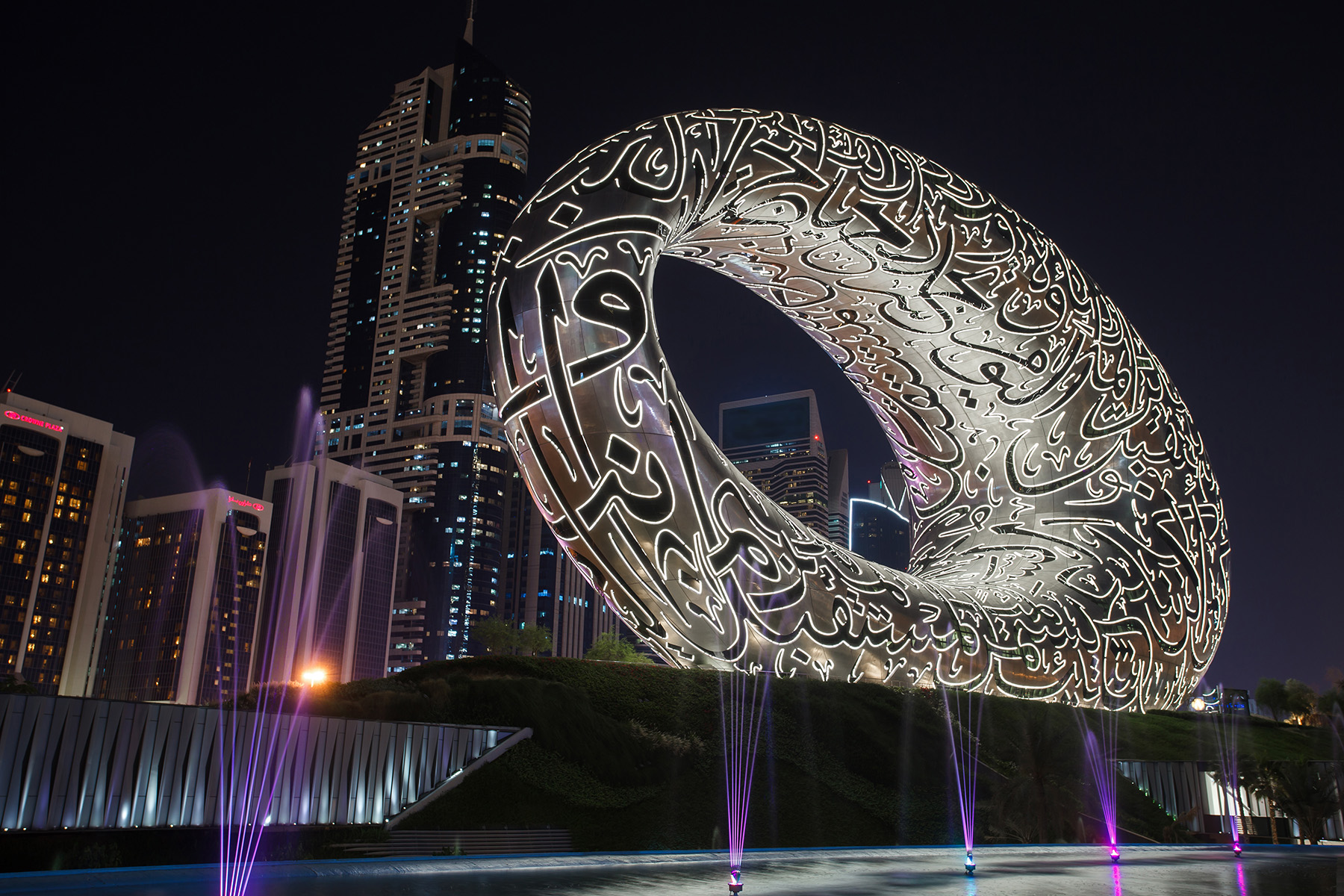
The functionality created for the Museum of the Future is accessible on an open-source framework designed by Buro Happold. Known as Buildings and Habitats object Model, the framework is an industrywide computational project that aims to encourage greater collaboration between architecture, engineering, and construction professionals to share code and standardize design data. It is an initiative intended to promote the dissemination of knowledge and experience to reach a common goal: better design.
The Museum of the Future demonstrates what can be accomplished using a digital design approach. Its design and execution put people and planet at the forefront, offering insight into the exciting future of all building design.
Tobias Bauly, MICE, CEng, is a director in the United Arab Emirates office of Buro Happold.
Project credits
Client/owner: Dubai Future Foundation, Dubai, United Arab Emirates
Architect: Killa Design, Dubai
Lead consultant (design, site supervision, and contract administration), structural, facade, and building services engineering, sustainability, bridges, transport, geotechnical engineering, people flow modeling, fire and life safety, specialist lighting, acoustics, waste and logistics: Buro Happold, Dubai
Developer: North25, Dubai
Contractor: BAM International, Gouda, Netherlands
Project manager: Matthews Southwest, Dubai office
Landscape architect: Cracknell, Dubai office
Cost consultant: AECOM, Dubai office
Architect/engineer of record: Rice Perry Ellis, Dubai
This article first appeared in the January/February 2023 issue of Civil Engineering as “Shaping a Symbol.”