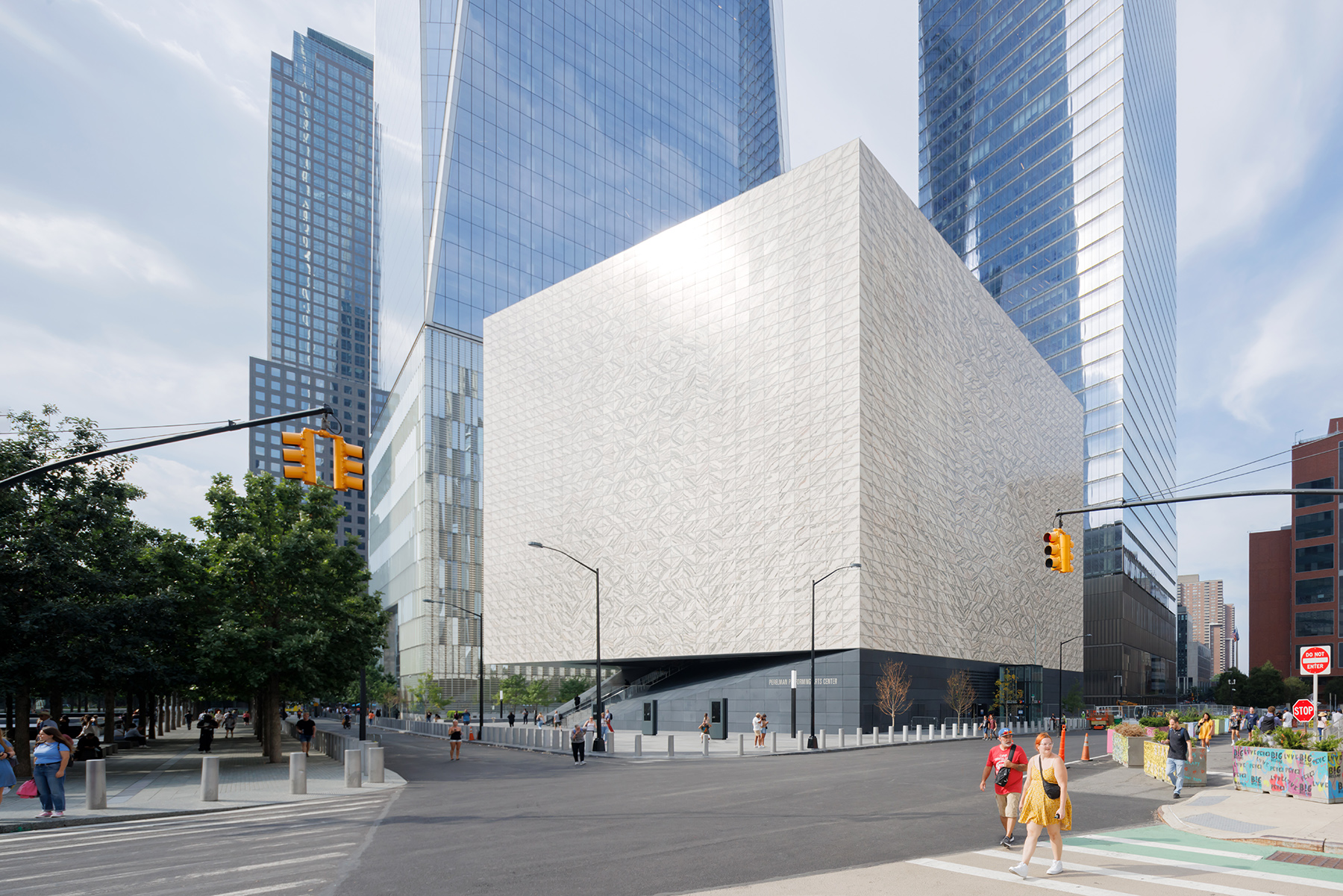
By Jay A. Taylor, P.E., S.E.
The new Perelman Performing Arts Center’s simple and elegant cube exterior belies layers of intricate structural engineering underneath.
Just like the actors on its stages within, the exterior of the Perelman Performing Arts Center at lower Manhattan’s World Trade Center in New York is a bit of an “actor” itself, showing different facets of its personality to visitors and passersby. By day, it is an elegant and translucent prism wrapped in veined marble and pristine glass, but by night it illuminates from within, evoking curiosity. But whatever time of day it is, the building’s simple form conceals an extremely challenging, multifaceted structural engineering puzzle made possible by complex and ingenious solutions.
Opened to the public in September, the 129,000 sq ft venue is replete with a grand lobby, bar and cafe, rehearsal spaces, and, most notably, three nimble, reconfigurable performance spaces that redefine multi-form theater design. The center’s agile and highly adaptable interior is as much a machine as a building or theater. Quickly transforming from an intimate black box venue for fewer than 100 guests to a combined auditorium with a capacity of 1,200, this “theater machine” can accommodate more than, at last count, 60 different performance and seating configurations.
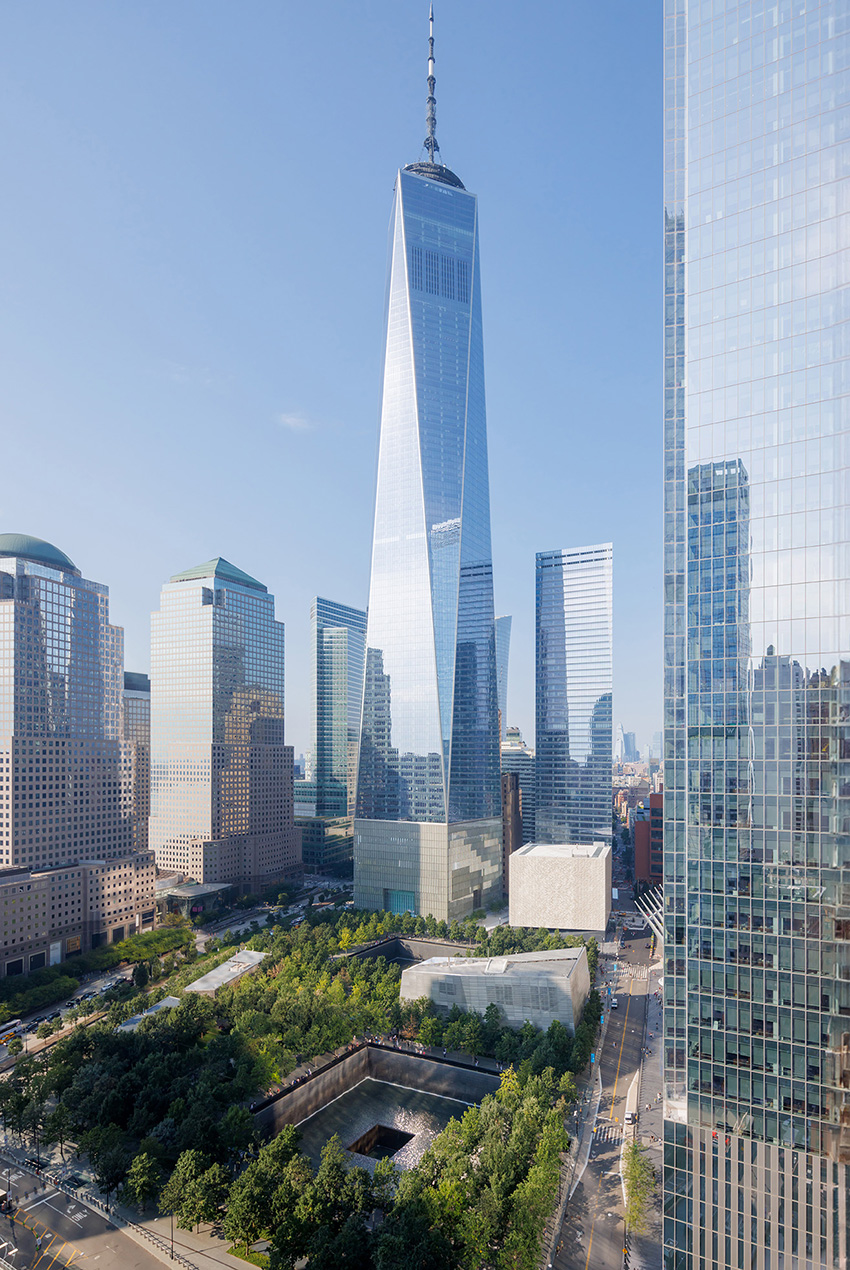
The structure, known as PAC NYC, is a beautiful and respectful addition to the World Trade Center site — the final piece to Ground Zero’s redevelopment, claiming a place alongside the 9/11 Memorial & Museum’s solemn pools; One World Trade Center’s soaring, 104-story facade; and the Oculus’ outstretched “wings” that symbolize a dove in flight.
Setting the stage
In 2002, Studio Libeskind won a design competition held by the Lower Manhattan Development Corp. to develop a plan for revitalizing the area in the aftermath of the terrorist attacks on the city on Sept. 11, 2001.
As part of the studio’s master plan, architecture firm Gehry Partners LLP was tasked with designing a performing arts center on the World Trade Center site. In 2004, Gehry Partners engaged engineering firm Magnusson Klemencic Associates to provide structural engineering consulting services.
Gehry envisioned a 234 ft tall, 250,000 sq ft venue that would serve the Joyce Theater and occupy the entire 200 ft by 200 ft site immediately east of One World Trade Center at the corner of Greenwich and Vesey streets. The building was designed to include vertically stacked performance spaces that could accommodate 1,000 people, four rehearsal spaces, and one dedicated theater space outfitted with a full fly loft, orchestra pit, and trap floor.
By the late 2000s, design and construction of neighboring One World Trade Center was underway, with foundations placed and four below-grade levels constructed. Those below-grade levels, which included Port Authority Trans-Hudson subway platforms and tracks, ran beneath the Joyce Theater site. Meanwhile, MKA actively engaged in the development of Gehry’s design and provided a plan diagram and narrative description of the anticipated building loads imposed on the project’s site. This allowed WSP Cantor Seinuk, the structural engineer for One World Trade Center and the below-grade levels, to progress its design while accounting for the future performing arts center’s building loads.
But financing and design issues delayed the Joyce Theater plan for several years. By the early 2010s, the project’s leadership changed, and Gehry’s Joyce Theater plan faded; however, not long after, a revised vision emerged. This reimagined performing arts center would include theater, music, and dance in three small and flexible spaces.
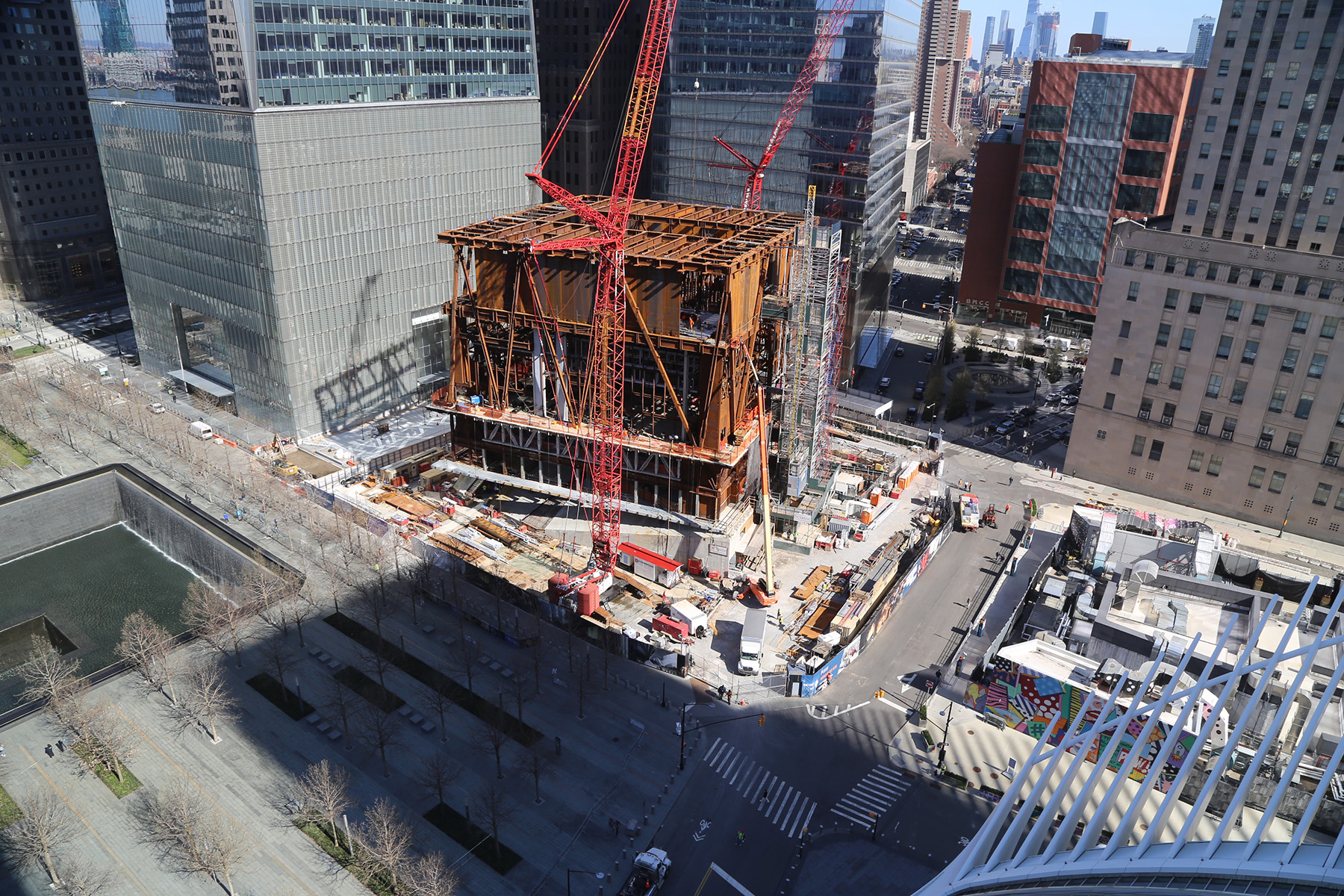
In 2015, Joshua Ramus, founding principal of REX, and Davis Brody Bond were chosen as the design architect and executive architect, respectively, for what would become PAC NYC. MKA joined the project team as structural engineer with Silman joining as a consultant on the structural team due to the company’s experience and roots in New York City.
REX’s building design was smaller than Gehry’s original plan: 129,000 sq ft versus 250,000 sq ft, 136 ft tall instead of 234 ft tall, and a site footprint of 160 ft by 160 ft compared with 200 ft by 200 ft. Moreover, the Helix (a circular vehicle ramp that leads from the plaza level to One World Trade Center) loading dock, One World Trade Center’s exhaust shafts, and a large service elevator for the theater level resulted in a building orientation that did not extend to or align with the site’s boundaries.
With One World Trade Center’s foundations and below-grade levels already built, REX engaged MKA to establish what accommodations had been made for the performing arts center’s building loads in the WSPCS-designed below-grade structure. WSPCS provided MKA with a plan diagram identifying available points of support and a spreadsheet with the load capacity of each potential support point. This information revealed two things: The site’s north and south boundaries contained the location points with the greatest capacity, and while this was ideal for Gehry’s building design, it caused a major problem for MKA and Silman, given the orientation and footprint size of REX’s design.
To easily comprehend the restrictions and limitations of the below-grade supports and develop strategies to merge the two designs, MKA distilled the information provided by WSPCS down to what became known as the red dot diagram. A red dot identified each location of potential support, and each red dot was scaled to represent its load-carrying capacity: the bigger the dot, the bigger the capacity.
With potential “foundation” locations predetermined and 55% of the performing arts center floor plate off-limits to columns because of the column-free requirements within the performance and rehearsal space footprint, MKA’s solution was to reverse-engineer the building. Instead of the more traditional design process of working from the top down or roof to foundation, MKA started by aggregating red dots to determine probable support locations. The team then explored and tested multiple structural system concepts that could support the building loads, avoid columns in the performance spaces, and deliver loads to those probable points of support that did not exceed their capacity.
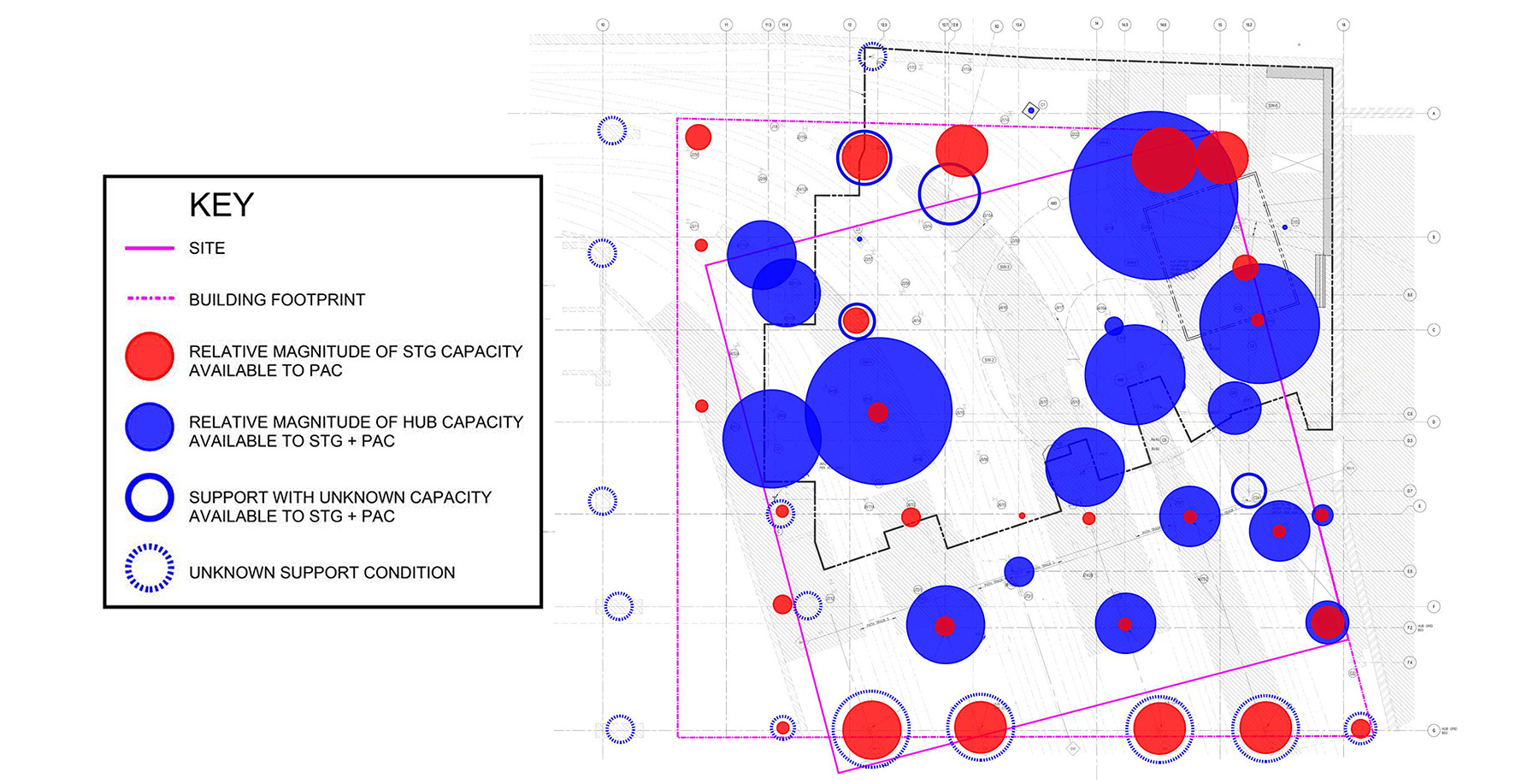
The process involved multiple iterations and extensive coordination with the WSPCS team. MKA discovered early in concept design that several transfer structures would be needed to distribute building loads to more than one WSPCS support point (red dot) since no existing point of support could handle the loads from the new PAC NYC configuration.
Through this process, MKA also discovered that the capacity of the foundations under several of the existing below-grade columns exceeded the column capacity because the original structure was to be significantly larger than the final iteration. These locations and capacities were mapped as blue dots on the red dot diagram. In this way, the team identified locations where existing columns could potentially be strengthened or retrofitted to increase their capacity to match that of the footings, thus increasing the capacity of the red dots.
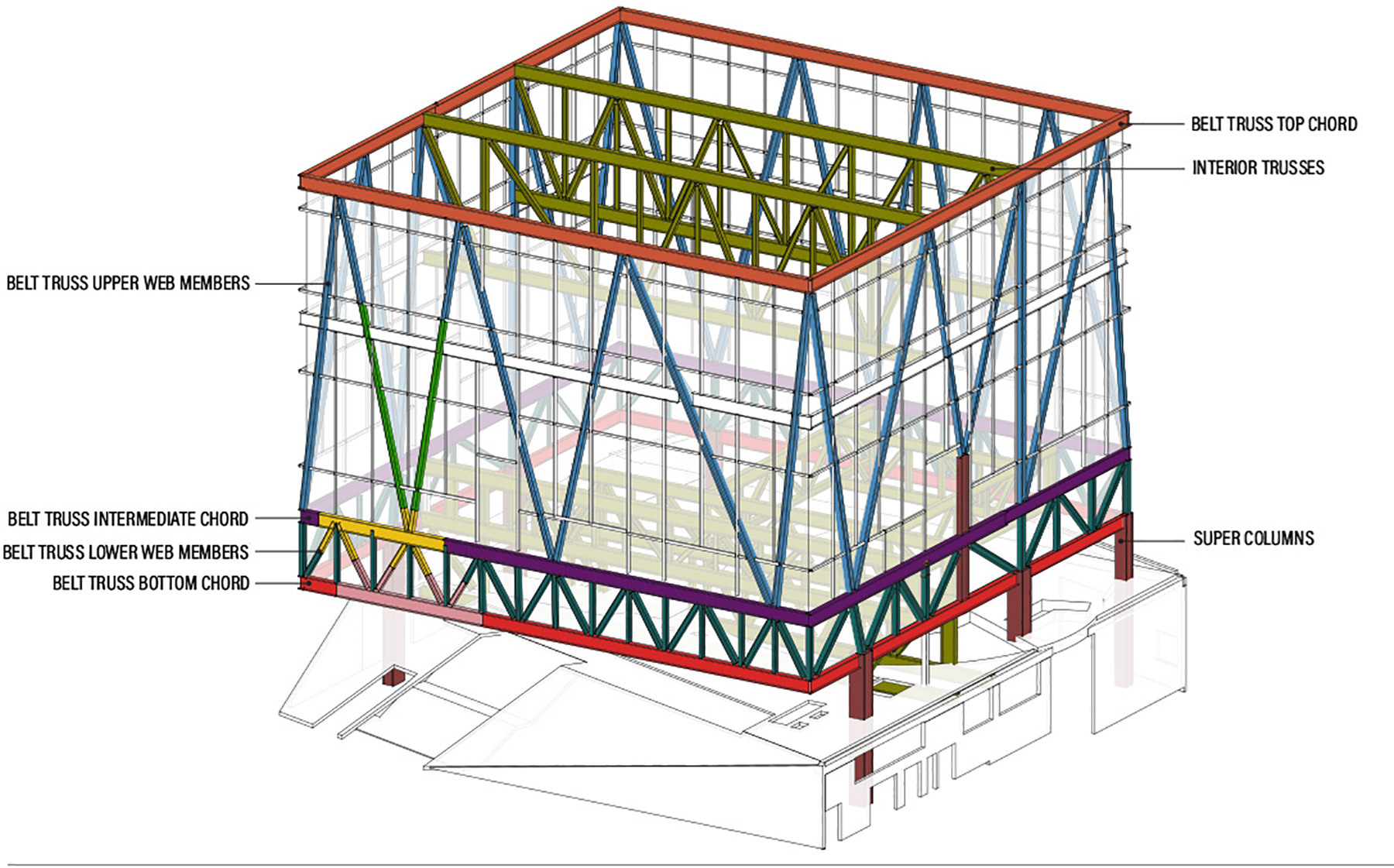
MKA developed initial concepts and multiple options for these interventions, reviewed them numerous times with WSPCS, and, ultimately, signed off on them to WSPCS, the engineer of record for the entire below-grade structure, for final design.
MKA and WSPCS collectively identified seven “workable” points of support, dubbed super columns: PAC 1 through PAC 7.
A structural design dance
With potential foundation locations and capacities established, MKA’s structural design proceeded. But difficulties remained — the team now navigated three more significant challenges (structure, vibration, and security), each more complicated by the foundation/support limitations.
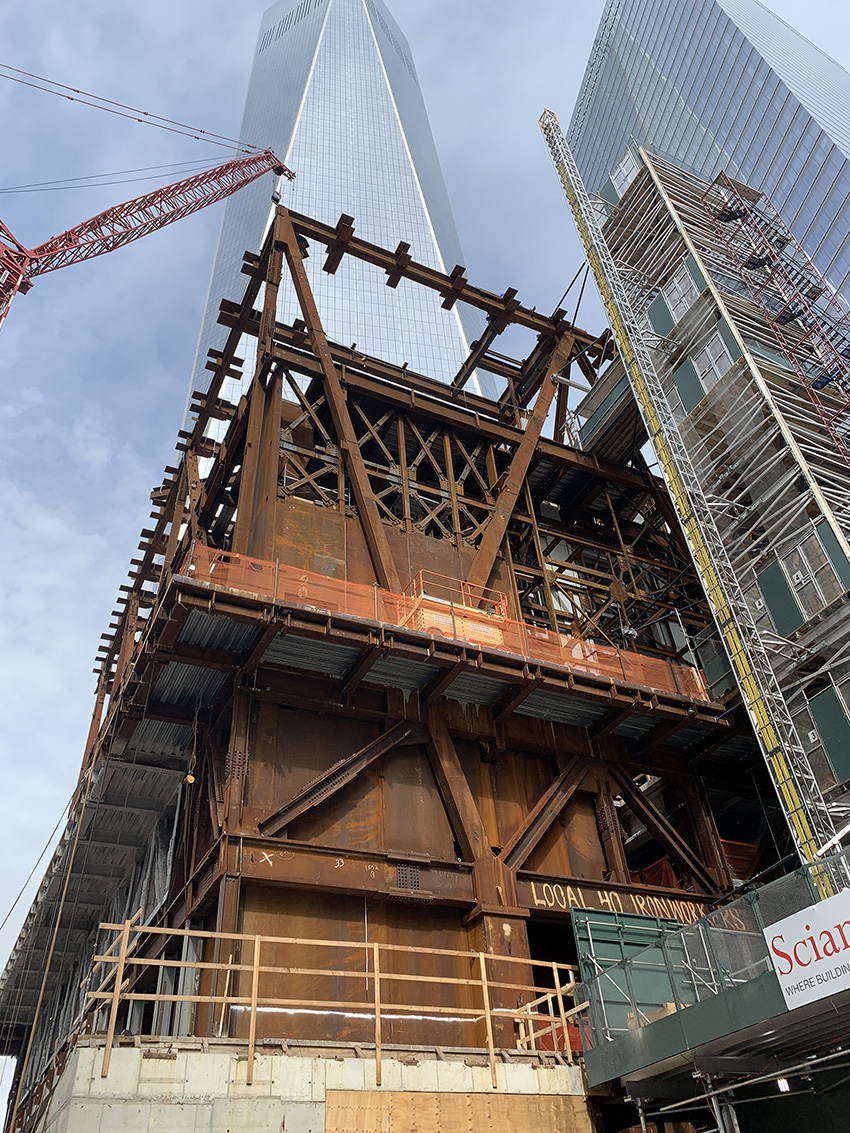
The first challenge was the superstructure load alignment. MKA developed framing schemes to deliver building loads to the super column locations without exceeding capacity. Supporting the entire building on only seven seemingly randomly located columns resulted in long spans and supports not always in the most efficient or ideal locations.
Full-height perimeter belt trusses wrapping all sides of the building provided maximum flexibility for spanning long distances between supports, efficiently supporting the heavy building loads, and accommodating large, cantilevered corners.
The belt trusses’ stiffness could also be “tuned” to distribute loads to supports that did not exceed their capacity. The perimeter belt trusses also doubled as the lateral system for the entire building.
With the primary support lines located at the perimeter and 160 ft apart and only one interior support location (PAC 7), MKA introduced four interior, two-story trusses.
Two are between the lobby and play level and span east to west to reduce the span of the floor framing, and two are between level 8 and the roof level and span east to west to reduce the roof’s span and the framing for the mechanical equipment room.
Three interior one-story trusses support the trap floor framing suspended below the largest theater at the play level.
The design team evaluated floor and roof framing directions that span in the north-south and east-west directions to ensure the floor and roof loads delivered to the trusses, and ultimately to the super columns, did not exceed the capacity of the super columns.
This, at times, resulted in less efficient floor or roof framing, but it achieved a distribution of loads that aligned with the capacity of the super columns and foundations.
Vibration mitigation
The limitations on the number of super columns and load alignment issues only exacerbated the typical challenges of any performing arts center: vibration and sound mitigation. But nothing about the PAC NYC design is typical. While audiences enjoy concerts, dances, plays, and other vibration-sensitive performances inside the venue, four levels of below-grade infrastructure rattle and hum from rumbling subway trains, noisy delivery trucks entering and exiting One World Trade Center’s loading docks, and the chatter and footfalls of tourists moving through the Oculus’ retail shops.
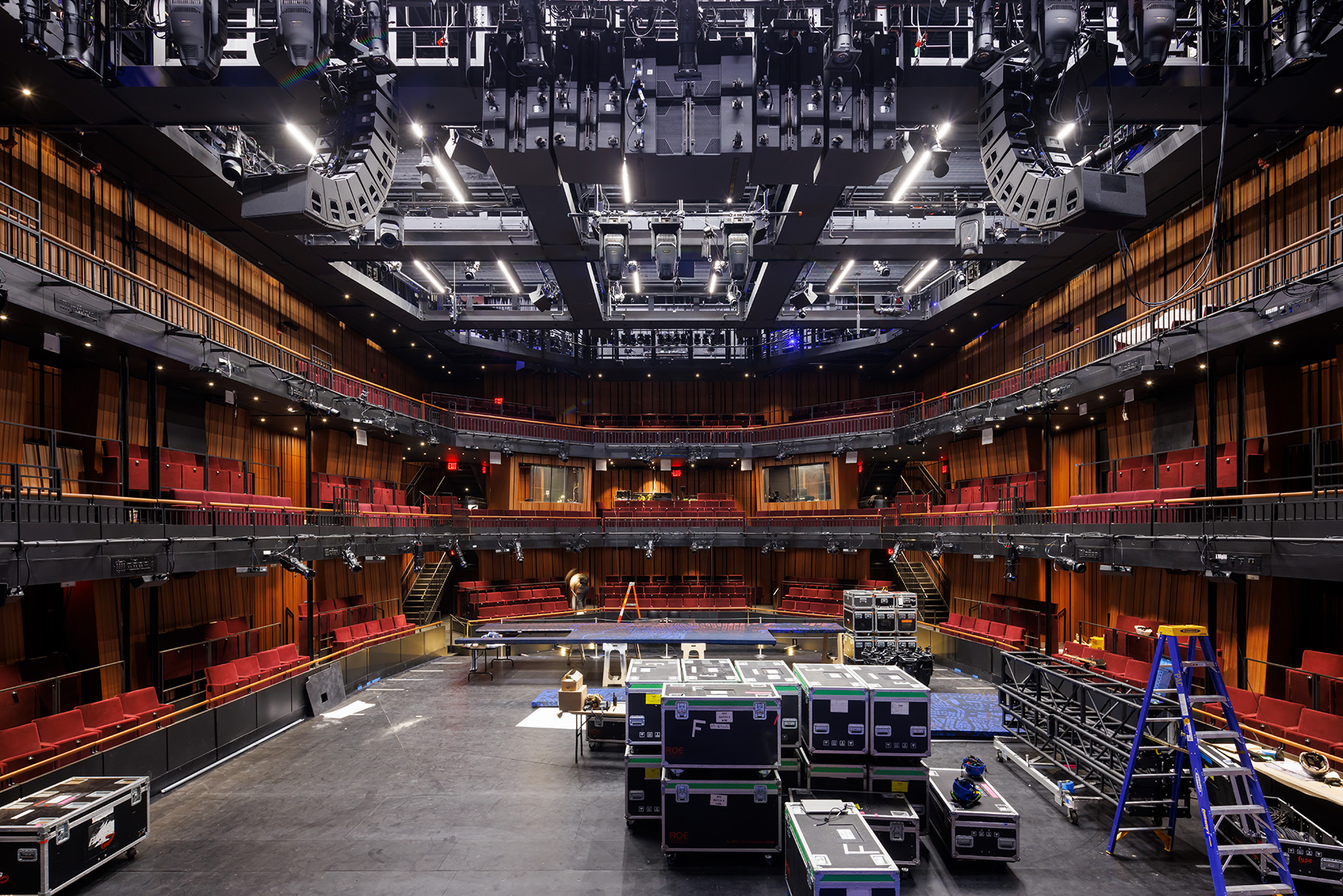
Another layer of design obstacles was added to these less-than-ideal conditions (i.e., the vibration and sound transmission challenges from the below-grade activities). The artistic director, theater consultant, and design architect envisioned the three theaters as a completely flexible space capable of hosting three concurrent and simultaneous events, morphing into two performance spaces, or even combining all three theaters for one large event.
MKA worked in concert (pun intended) with the acoustic and vibration consultants to develop a design informed by the following performance criteria:
- All theaters must be isolated from site-induced vibration and noise (trucks and trains).
- The individual theaters must be isolated from one another and from the dual-purpose area housing the scene dock (where scenery is stored) and hallway between theaters A+B and B+C.
- The isolation strategy must allow the scene docks to be “attached” to one theater and isolated from the adjacent theater.
- The theaters must be isolated from adjacent internal building program spaces above, below, and on all sides.
Engineering gymnastics requiring innovative design techniques to mitigate noise and vibration were essential to addressing significant site- and aspirational-related program challenges.
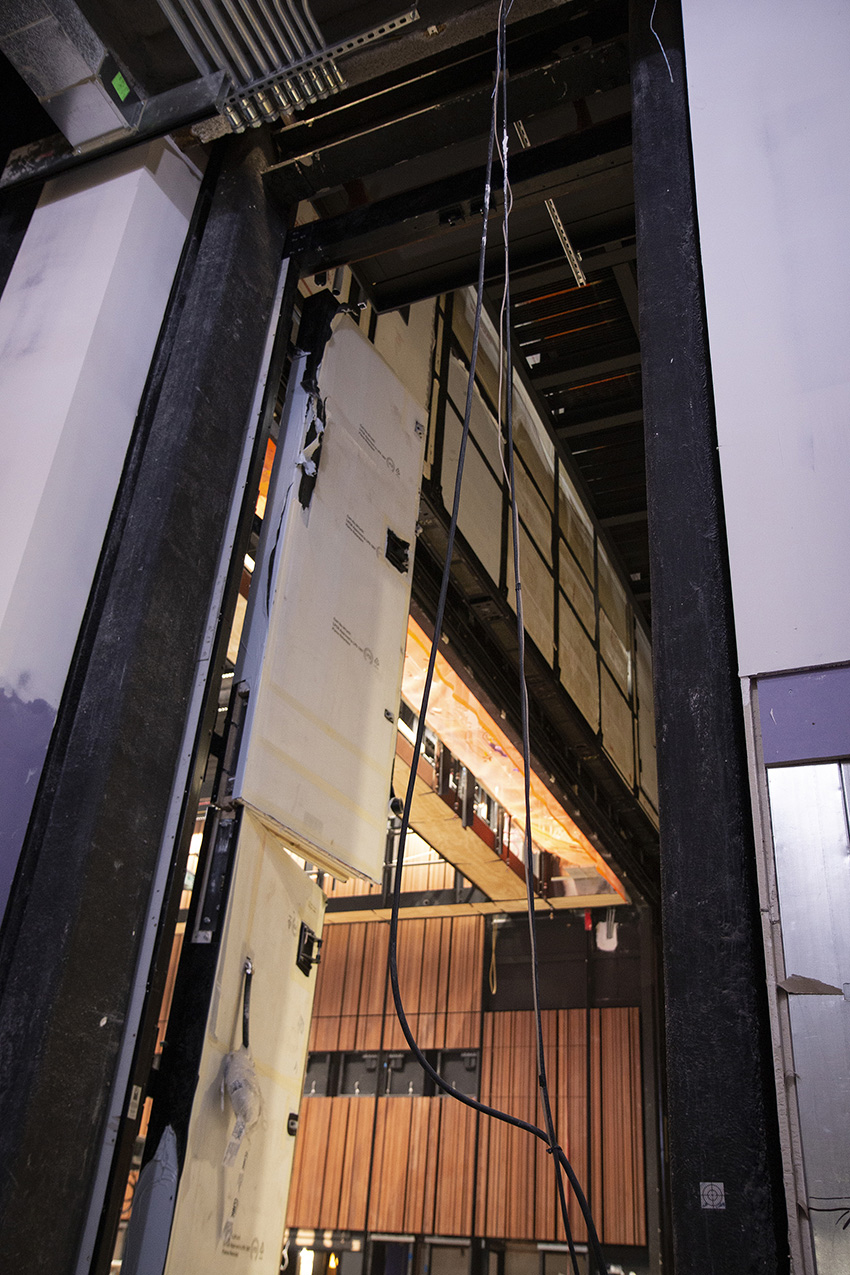
The theaters were configured in plan to provide a dual-purpose scene dock/hallway between theaters A+B and B+C. MKA borrowed a page from seismic design and incorporated steel and rubber bearing pads into PAC NYC’s design. The floor of the theaters and scene docks consists of 12 in. thick reinforced-concrete slabs supported on steel and rubber bearing pads that, in turn, bear on the building’s primary floor structure.
Instead of dampening and dissipating the energy and forces generated by an earthquake, the venue’s steel and rubber bearing pads dampen and dissipate noise, vibration, and other aural pollution caused by below-grade subway trains and delivery trucks.
To prevent acoustic bleed from the other theaters, each theater and scene dock floor slab are separated from one another — and all other adjacent floor framing — by a 2 in. wide acoustic isolation joint. The ceiling/lid of each theater and scene dock is independently supported by a steel-framed perimeter theater wall that bears on the isolated concrete floor slab. Each theater is effectively a free-standing building sitting on the bearing pads.
MKA’s design goes one step further by isolating the theaters from the building itself, much like three ships in a bottle: three free-standing, independently framed, structurally complete theaters isolated from one another and from the building in which they reside. Any vibrations or noises generated below could be transferred through the 3D vertical belt truss system but never reach the theaters.
It is challenging enough to create myriad theater configurations from three primary theater spaces and two scene docks. But the need to preserve world-class acoustics in each configuration required that the walls between the theaters and scene docks be removable when “attached” to one or both theaters and acoustically sound when functioning as one of the four walls of the theaters. Four acoustically sealed guillotine doors designed by Clark Door retract into the space above the theaters, projecting into the mechanical equipment room level at the top of the building.
MKA worked closely with Clark to design and detail a complex secondary steel structure to support the hoists, mechanisms, and platforms required for a pair of 33 ft tall, 65 ft wide, 55-ton doors between theaters A and B and a pair of 26 ft tall, 42 ft wide, 27-ton doors between theaters B and C — all while ensuring the significant weight of these doors and their supporting structures did not exceed the capacities of the super columns.
Simple elegance defined
Despite the design and structural hurdles that had to be overcome, PAC NYC achieves an unmatched level of abstract elegance. Its acoustically superior environment offers no hint of the noisy and vibrating loading docks
and subway tracks below.
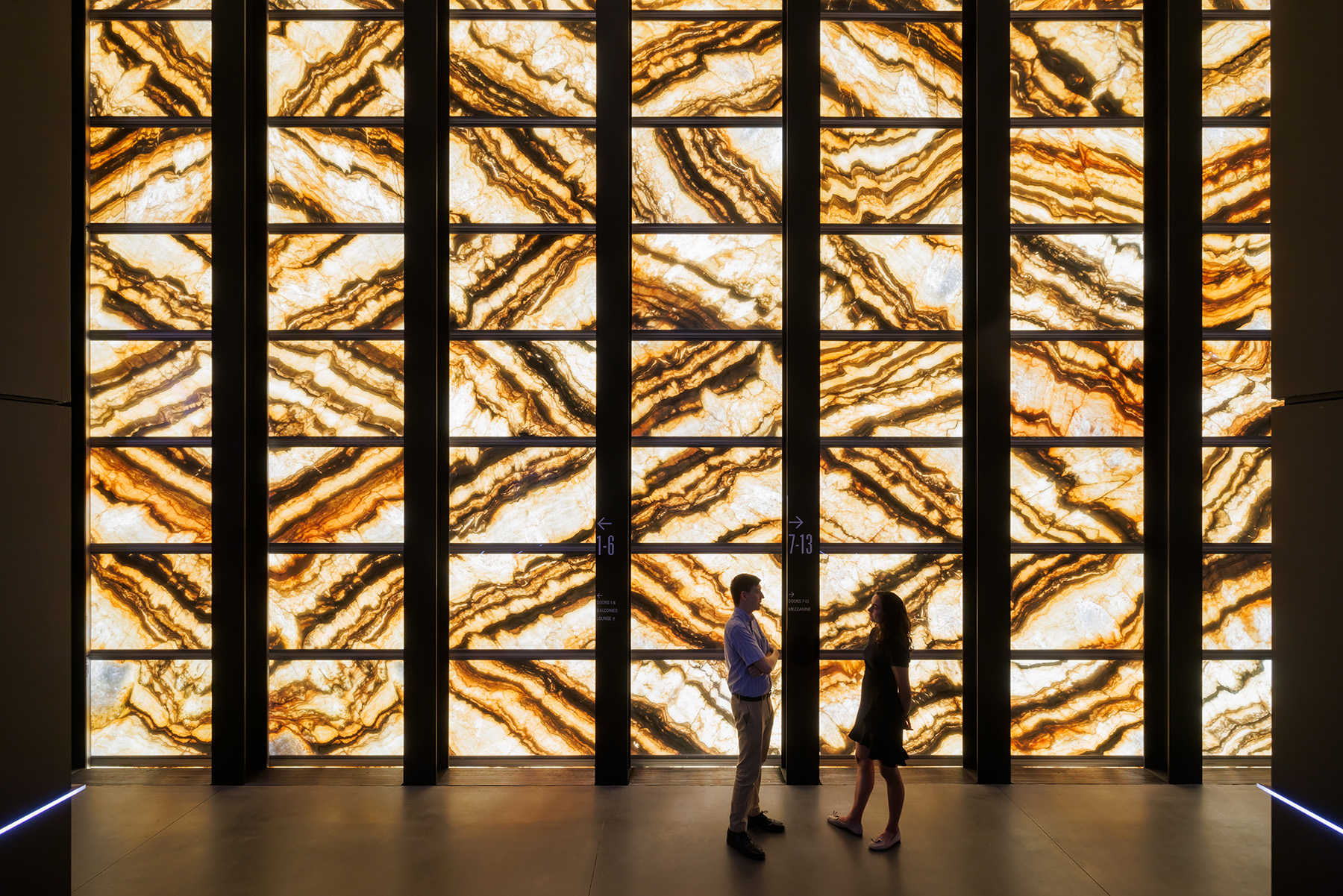
Furthermore, its visually minimalist box form conceals intricate and innovative structural engineering that will remain a mystery to many of its visitors, its facade hiding many secrets. But for PAC NYC’s architects, engineers, and project team, there’s no mystery at all. This building stands in this iconic spot simply because of collaborative, choreographed design creativity and engineering innovation.
Jay A. Taylor, P.E., S.E., is a retired senior principal of Magnusson Klemencic Associates, where he worked for 25 years and led the firm’s cultural, civic, and education specialist groups.
Project credits
Owner: Lower Manhattan Development Corp., New York City
Architect: REX, New York City
Executive architect: Davis Brody Bond, New York City
Structural engineer and engineer of record: Magnusson Klemencic Associates, Seattle
Consulting engineer: Silman, New York City
Mechanical, electrical, and plumbing engineer: Jaros, Baum & Bolles, New York City
Specialty theater consultant: Charcoalblue, New York City
General contractor: Sciame Construction, New York City
This article first appeared in the November/December 2023 print issue of Civil Engineering as “Sublime Complexity.”