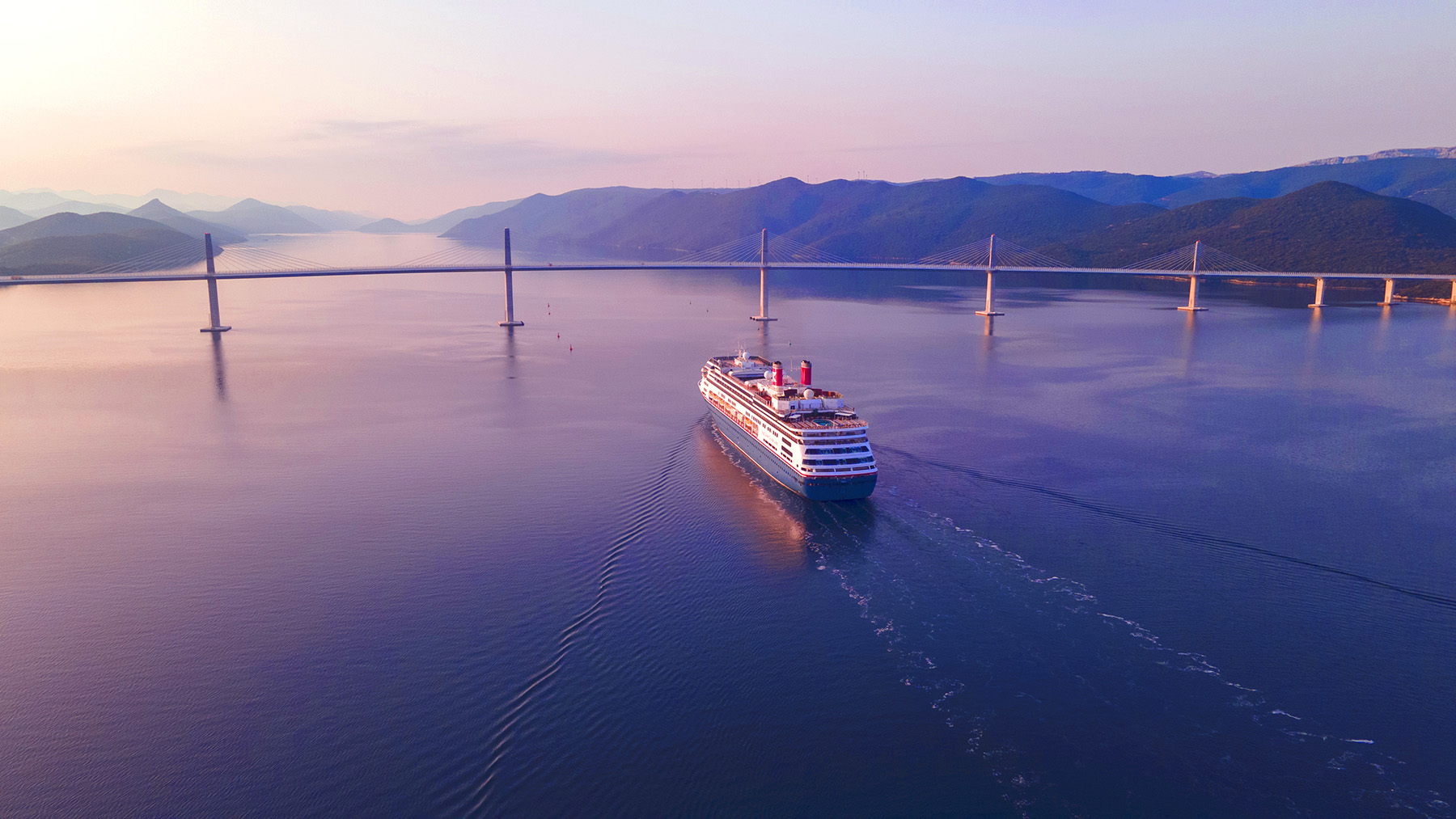
By Bicheng Tang, CEng, Xuefeng Wang, CEng, Igor Bilić, CEng, and Minghai Pei, CEng
Pelješac Bridge is Croatia’s largest and most iconic bridge engineering project to date. Spanning a marine conservation area in the Adriatic Sea, the bridge is the fulfillment of a dream in the country’s brief history.
For many years, two parts of the Croatian coastline had been disconnected by a section of Bosnia and Herzegovina’s coast at Neum. Pelješac Bridge fixed that when, upon its completion in July 2022, it united the mainland to the peninsula of Pelješac.
But getting to that point was no easy task. After decades of delays, in April 2018, the dream of building the bridge began to take shape. China Road and Bridge Corp. signed with owner Hrvatske Ceste, or the Croatian Road Authority, to serve as the main contractor for the project, and construction began a few months later in July. The anticipated cost of the bridge, 85% of which was funded by the European Union, was 2.08 billion Kuna (about $332 million based on 2018 exchange rates).
Bridge specifications
Pelješac Bridge is a 23.6 m wide, two-lane, 13-span, extradosed cable-stayed bridge. The five main spans are 285 m in length and are surrounded by two spans measuring 189.5 m, four measuring 108 m, and two measuring 84 m, for a total length of 2,404 m, 2,440 m including abutments. Six 40 m high centrally placed pylons are on the bridge’s single central cable plane. Access roads connect to both abutments.
On the curved portion of the bridge, the horizontal alignment has a curve radius of 450 m from abutment U1 to pier S4. The maximum longitudinal gradient is 2.98% symmetrically, and the vertical curve radius is 11,000 m. On the straight portion of the bridge, beginning at pier S5, the deck has a two-sided cross slope of 2.5%, and in the horizontal curved region, the cross slope is adjusted to a one-way maximum of 5.8% at abutment U1.
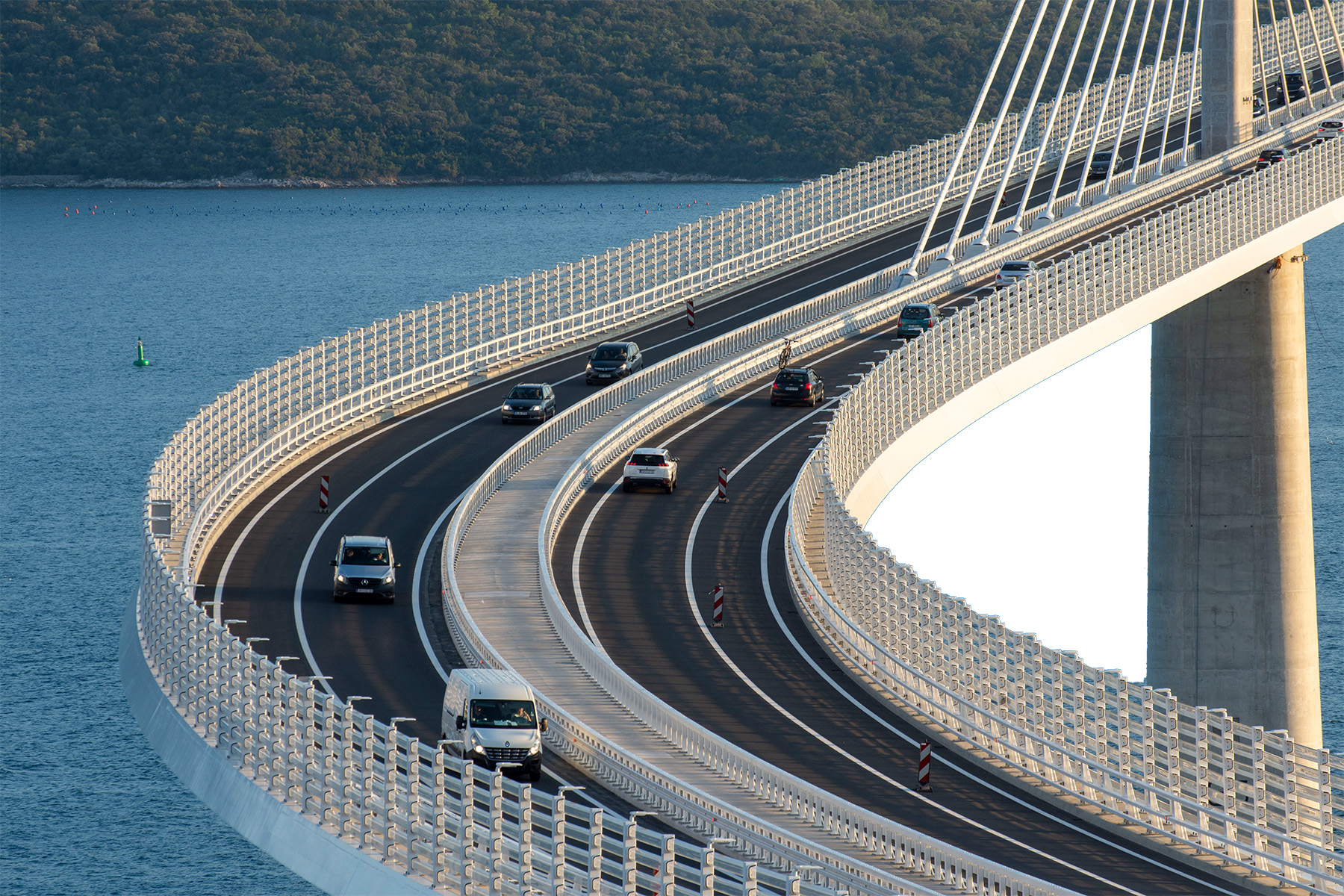
The average water depth along the alignment is 27 m, and the required minimum navigation clearance was 200 m wide by 55 m high. Because the bridge is in a high-seismicity zone, the design acceleration of soil at the bedrock level is 0.34 g. The bridge is also in a region susceptible to strong winds. The reference wind speed was 33.7 m/s, according to measurements taken between 2005 and 2014 at meteorological stations in Ploče and Komarna.
The foundations of the pile caps of piers S5-S10 (the main spans) comprise 18 or 20 steel-driven piles with a diameter of 2,000 mm and a wall thickness of 40 mm S355 steel. The tubular steel piles are filled with reinforced concrete in the upper 40 m. The pile shoes comprise S460 steel with 60 mm thick walls.
The foundations of the pile caps of the secondary piers are supported by nine piles per pier, which were designed as composite (steel pipes filled with concrete) with an additional 5-7 m long concrete socket under the steel pile shoes.
The steel deck was designed as follows: epoxy primer coating, waterproof epoxy resin and a 40 mm thick protective layer (mastic asphalt MA11) and a 40 mm thick wearing layer (AC11), both comprised of epoxy resin.
In addition to the two travel lanes, on both sides of the bridge are paths between the steel safety fence and wind barriers so that workers can access the bridge for maintenance and repairs.
Steel manufacturing
CRBC researched more than 10 steel fabricators worldwide, analyzing their production capacities, workshop dimensions, and degrees of mechanization and automation. Although the surrounding European manufacturers were ideal due to their proximity, not a single company met all the project’s steel requirements.
In the end, CRBC assigned the steel fabrication equally between Jiangsu Juxin Petroleum Steel Pipe Co. Ltd. and a joint venture between ArcelorMittal and Penglai Jutal Offshore Engineering Heavy Industries Co. Jiangsu Juxin and Penglai Jutal have an annual steel fabrication production capacity of 150,000 metric tons each. The two companies optimized scheduling and production to reduce manufacturing time, producing a total of 31,000 metric tons of steel piles within four months, which was ahead of schedule.
Welding complexities
According to the proposed design and execution sequence, the tubular steel piles were to be first processed in two 60 m long segments in the workshop, loaded onto a ship, and welded back together on-site. However, this would have compromised worker safety and product quality. The contractor noted four main technical issues with this approach:
1. The welders would have been forced to enter the narrow body of the 60 m pile from the top. However, the space within the piles was not large enough to safely perform the preheating process for the double-sided butt weld of the 40 mm thick seams.
2. The wind and waves would have had a major influence on the quality of the weld seams. Erecting temporary offshore construction platforms and renting flat storage barges would have resulted in unexpected costs and delays.
3. Execution Class 4 requirements (European Standard EN 1090-2: Execution of steel structures and aluminium structures-Part 2: Technical requirements for steel structures) for structural steel construction are extremely strict. In order to meet these standards, welders would have needed to be equipped with a costly production-control system to verify assembly accuracy for concentricity, verticality, and straightness.
4. The construction period for EXC4 products could not be controlled on-site, and the welding of the thick plates, repair, and nondestructive testing would have required too much time on-site.
For these reasons, CRBC abandoned the proposed design and execution sequence. Instead, it transported the steel piles to the site using COSCO Shipping’s extra-large pile-driving barge, which is usually reserved for pile construction of offshore wind and oil platforms. The barge was the largest available ship worldwide, capable of moving a 130.6 m long pile, which is highly uncommon in bridge engineering. It took six trips from China to Croatia to deliver all the piles.
Before beginning the pile-driving process, CRBC built an environmental air bubble curtain to protect Croatia’s underwater ecosystem and local oyster farms from lethal levels of construction noise. According to Yale Climate Connections, an air bubble curtain is created when a ship lays a tube on the ocean floor surrounding a construction site and air is pushed through holes in the tube to create a vertical wall of bubbles that trap construction sound.
Pile driving took five months to complete.
Bridge installation
Pelješac Bridge’s six pylons are 40 m from their tops to the deck. (The piles supporting the pylons range in depth from 46 m to 61 m.) The stay cables are made from parallel steel strands with a nominal tensile strength of 1,860 MPa. The steel strands are coated in polyethylene, and the outer protective cable conduits are made of high-density polyethylene with helical ribs that reduce vibrations from wind and rain. The number of strands per cable varies between 55 and 109.
Each pylon has 10 pairs of stay cables (20 per pylon). The stay cables are fixed and anchored to the pylons via steel links embedded in the pylons. The pylons were cast using self-compacting, high-strength concrete (C70/85) and coated with silane.
The design team chose box girder construction for the superstructure. Each girder is designed as a three-cell box with 22.5 m wide by 4.5 m high orthotropic deck plates. The bottom plate is 8.1 m wide, and both side plates are inclined 24 degrees horizontally, lowering the drag coefficient and improving the aerodynamic performance. The stay cables are connected to the deck via steel anchor boxes within the steel box girders. The stay cables were stressed inside the box girders.
The box girders were manufactured in China by Shanghai Zhenhua Heavy Industries Co. and China Railway Baoji Bridge Group, which have an annual individual production capacity of more than 250,000 metric tons. Both manufacturers are EXC4 authorized, as per European standards.
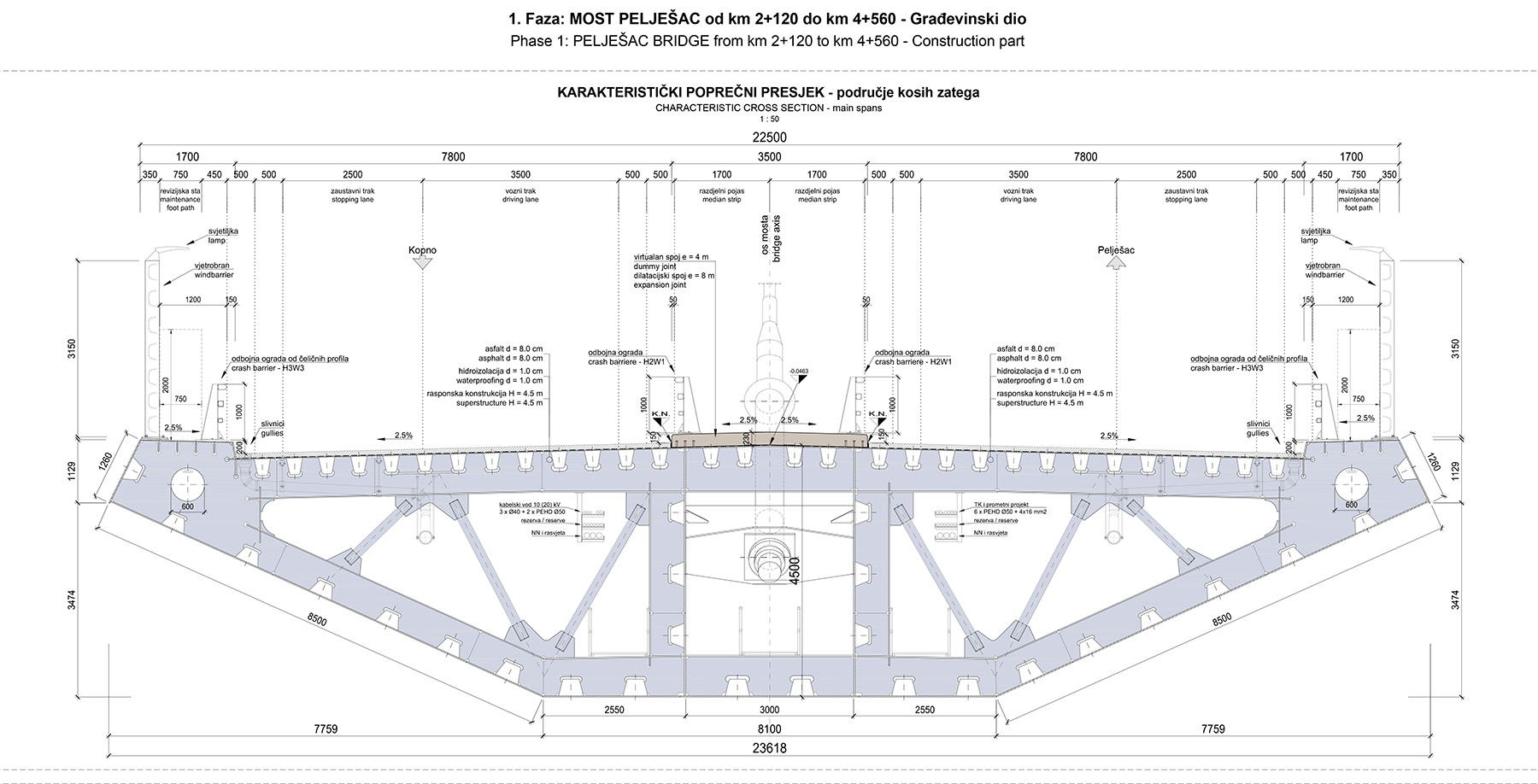
The main span girder segments are 12 m long and were installed via the balanced cantilever method. Ten pairs of girders were installed per pylon. Flat barges transported the pylons and girders to derricks that hoisted them into position.
To speed up erection of the bridge’s secondary spans and decrease the amount of on-site welding, the design team fabricated extra-long segments ranging from 36 m to 56 m and lifted them into place with a 1,000-metric-ton-capacity floating crane. The team also used a floating crane to raise the 12 m long curved and straight sections of the on-land portions of the bridge onto temporary onshore platforms. They were then moved along skip tracks using hydraulic jacks.
Challenges abounded
One of the biggest obstacles the contractor faced was the logistics required for hauling heavy equipment. It was not possible to set up temporary trestles in such deep water, so construction was performed from the ships. During construction, the contractor dispatched 19 ships from China. The dispatch and rental expenses for these ships were significantly more than using local ones, which ate into the project budget.
Another challenge was the lack of local skilled structural steelworkers. During the early stages of the COVID-19 pandemic, CRBC considered shutting down superstructure installation. But in August 2020, it decided to hire and transport Chinese engineers and workers to Croatia. During the installation of the superstructure, there were more than 400 Chinese employees on-site, including welders, assembly workers, inspectors, and anticorrosion professionals. The large labor force significantly reduced the installation period, taking only five months to place the steel box girders of the main spans. Construction proceeded from both abutments simultaneously, connecting in the middle at midnight on July 29, 2021.
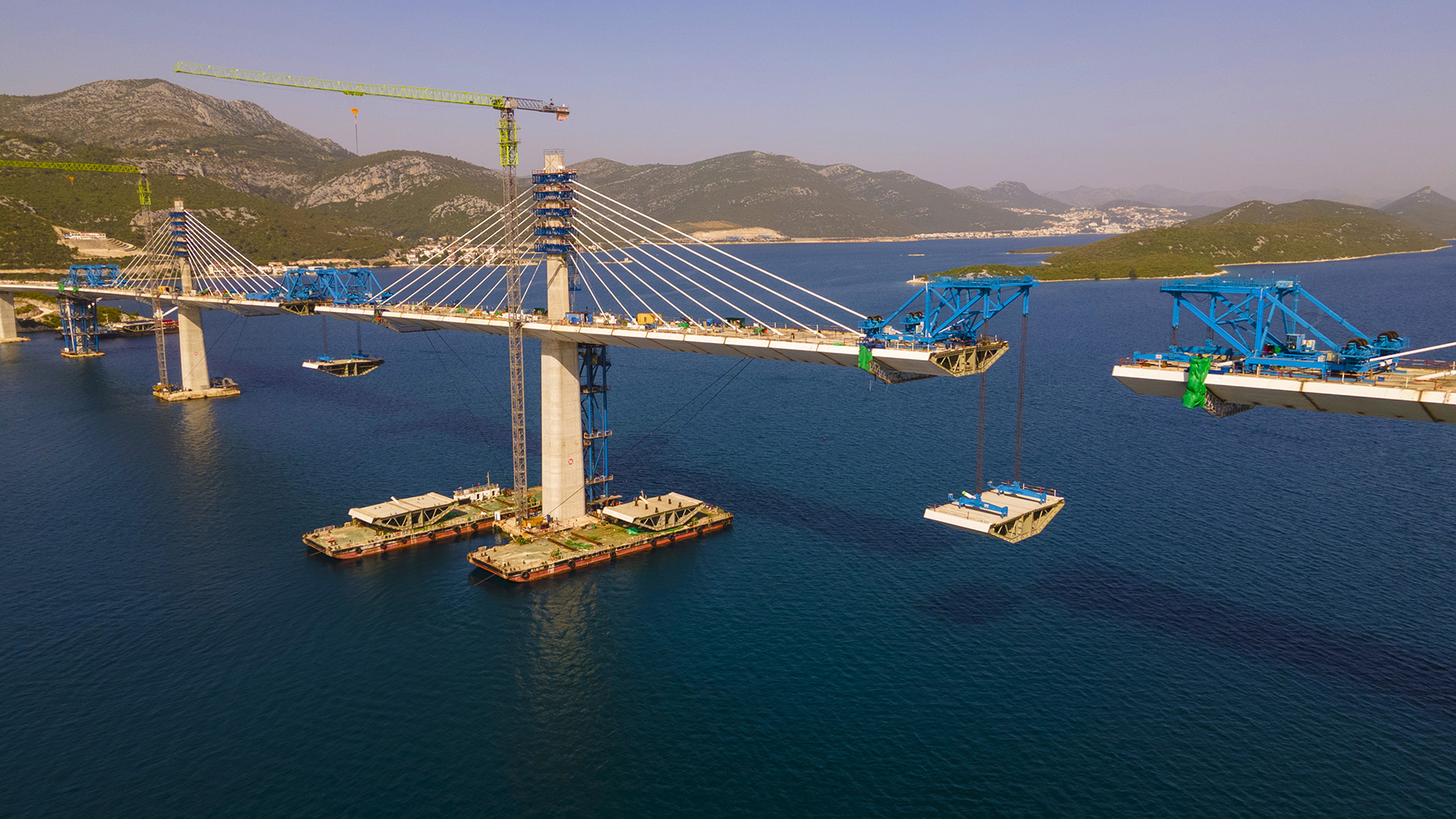
The deck surfacing also proved to be problematic. Orthotropic deck surfacing is a relatively new technique in the field of bridge engineering. Steel and asphalt have quite different material properties, and methods to combine the two materials to be highly durable are in their infancy. Despite these obstacles, deck surfacing and paving began in October but wasn’t completed until January due to heavy rain in November and the first half of December when paving stopped.
The design and construction of the roadway was performed per the German ZTV-ING (Additional Technical Contract Conditions and Guidelines for Civil Engineering Structures) series specifications. However, to adapt to the hot Mediterranean climate and improve high-temperature resistance, the melting point of the polymer-modified bitumen for the roadway was increased from 50 C to 65 C, in accordance with the Croatian Road Authority’s 2015 internal technical guidelines.
The entire pavement surface area is approximately 38,000 sq m.
Drainage wells were installed next to the curbs. Rainwater travels along the internal pipelines of the steel box girder to the abutments on both sides of the bridge, passes through the oil filtration device, and then is discharged into the sea. Traffic lights were installed on the tops of the steel column barriers, and landscape lighting illuminates the bridge at night.
Dream completion
The bridge opened to traffic on July 26, 2022, nearly four years to the day after construction started. During the summer tourist season, more than 12,000 vehicles per day drive across the bridge. Its construction has made travel between the mainland and Dubrovnik easier and faster, eliminating multiple security checkpoints into and out of Bosnia and Herzegovina and Croatia.
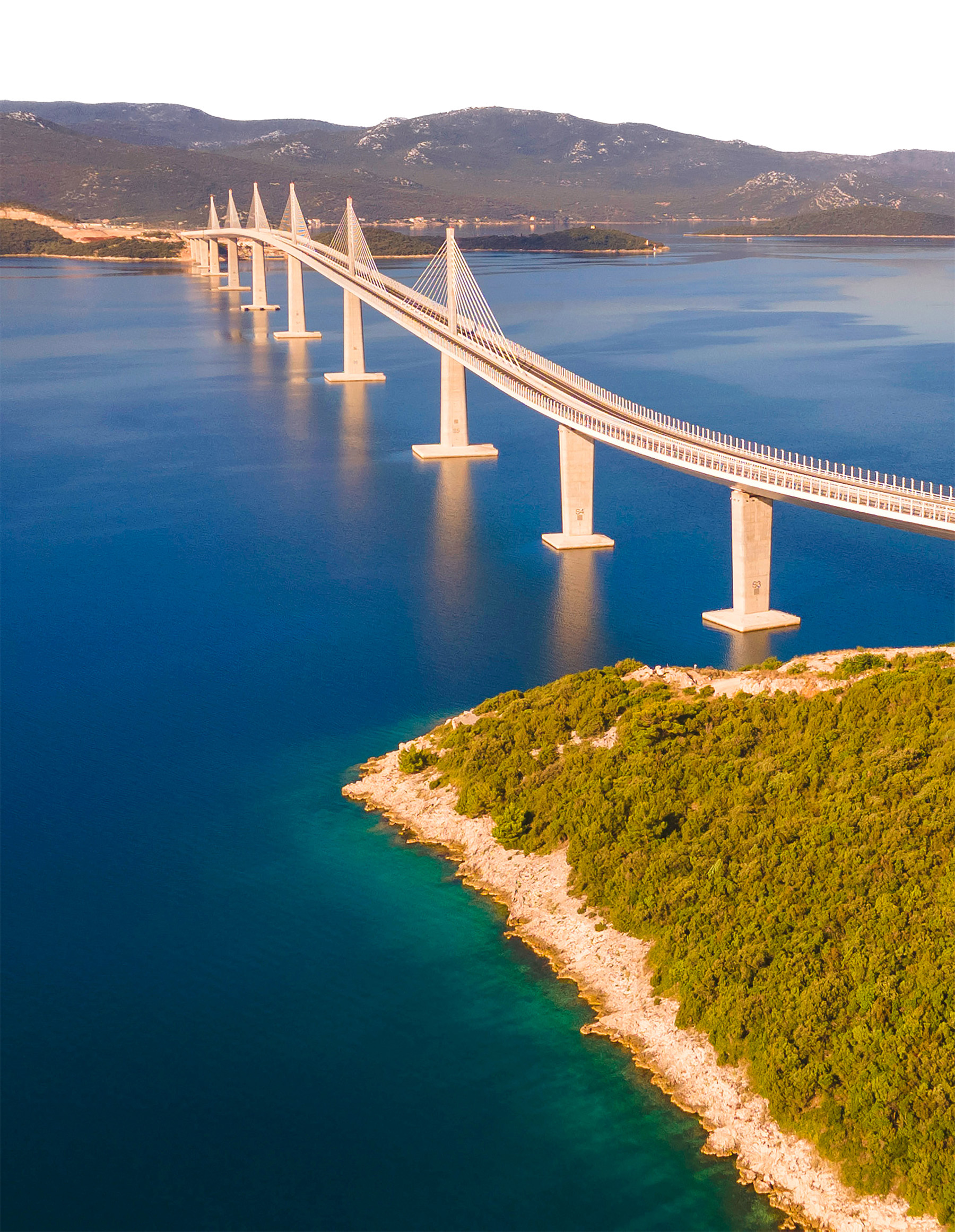
Pelješac Bridge was a groundbreaking project for Chinese contractors. CRBC complied with Croatian and European design and construction requirements and adhered to the environmental protection and safety requirements during all stages of construction. CRBC overcame numerous significant obstacles due to the COVID-19 pandemic but ultimately succeeded in delivering the completed project on schedule.
Bicheng Tang, CEng, is a senior bridge engineer at China Road and Bridge Corp. Xuefeng Wang, CEng, is a deputy manager at China Road and Bridge Corp., Croatian branch. Igor Bilić, CEng, is a senior civil engineer at China Road and Bridge Corp., Croatian branch. Minghai Pei, CEng, is a senior bridge engineer for CCCC Highway Consultants Co. Ltd. in Beijing.
Project credits
Owner
Croatian Road Authority
General contractor
China Road and Bridge Corp.
Construction supervisors
IGH Institute, Zagreb, Croatia; Investinženjering d.o.o., Zagreb; Centar za organizaciju građenja d.o.o., Zagreb
Design team
A joint venture of Pipenbaher Consulting Engineers, Slovenska Bistrica, Slovenia; Ponting Bridges, Maribor, Slovenia; and Zagreb University Department of Civil Engineering, Zagreb
Steel manufacturers
Shanghai Zhenhua Heavy Industries Co., Shanghai; China Railway Baoji Bridge Group, Baoji, China; and Jiangsu Juxin Petroleum Steel Pipe Co. Ltd., Yangzhou, China
Extra-long pile driving
Shanghai Shocktorm Ocean Engineering Co. Ltd., Shanghai
Steel deck pavement
Chongqing Special Paving Engineering Technology Co. Ltd., Chongqing, China
This article first appeared in the January/February 2024 print issue of Civil Engineering as “Crossing Croatia.”