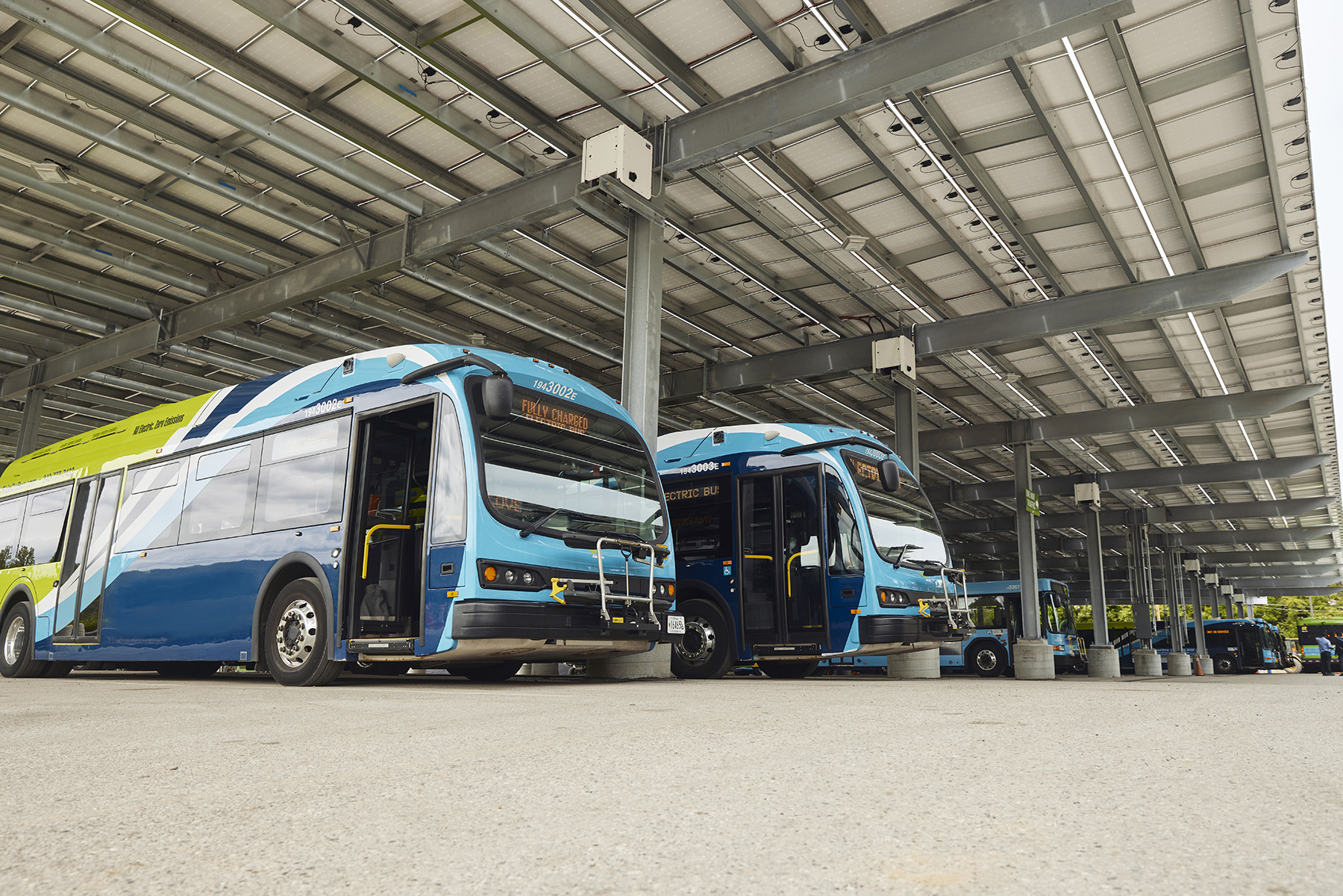
By Robert L. Reid
As the transition to electric vehicles accelerates, civil engineers are helping transit agencies make it happen. Such efforts require careful planning and proactive measures with multiple parties to ensure that EVs get the power they need, when and where they need it. It also involves thousands of miles of new transmission lines, structures to support charging and energy storage systems, and strategies to address unique fire safety concerns.
Cities and states across America are setting ambitious goals for switching from fossil-fuel-powered cars, trucks, and buses to electric vehicles. The New York Metropolitan Transportation Authority, for example, plans to replace its entire fleet of 5,840 buses (most of which operate on diesel or are diesel hybrid EVs) with zero-emission vehicles by 2040. (In transportation, the term “zero emissions” generally refers to EVs, though hydrogen fuel cell vehicles would also qualify.) MTA also plans to replace its so-called nonrevenue vehicles, such as cars and maintenance trucks, with their zero-emission equivalents.
California and New York, among other states, have also proposed either banning or severely restricting the sale of new gasoline- or diesel-powered cars and trucks by 2030, with more states considering similar measures. And the U.S. Environmental Protection Agency has proposed tough federal vehicle emissions standards starting in 2027 “that will accelerate the ongoing transition to a clean vehicles future,” according to an April 12 EPA announcement. In response, the American Petroleum Institute labeled the EPA’s move as a “de facto ban on gasoline powered cars and trucks.”
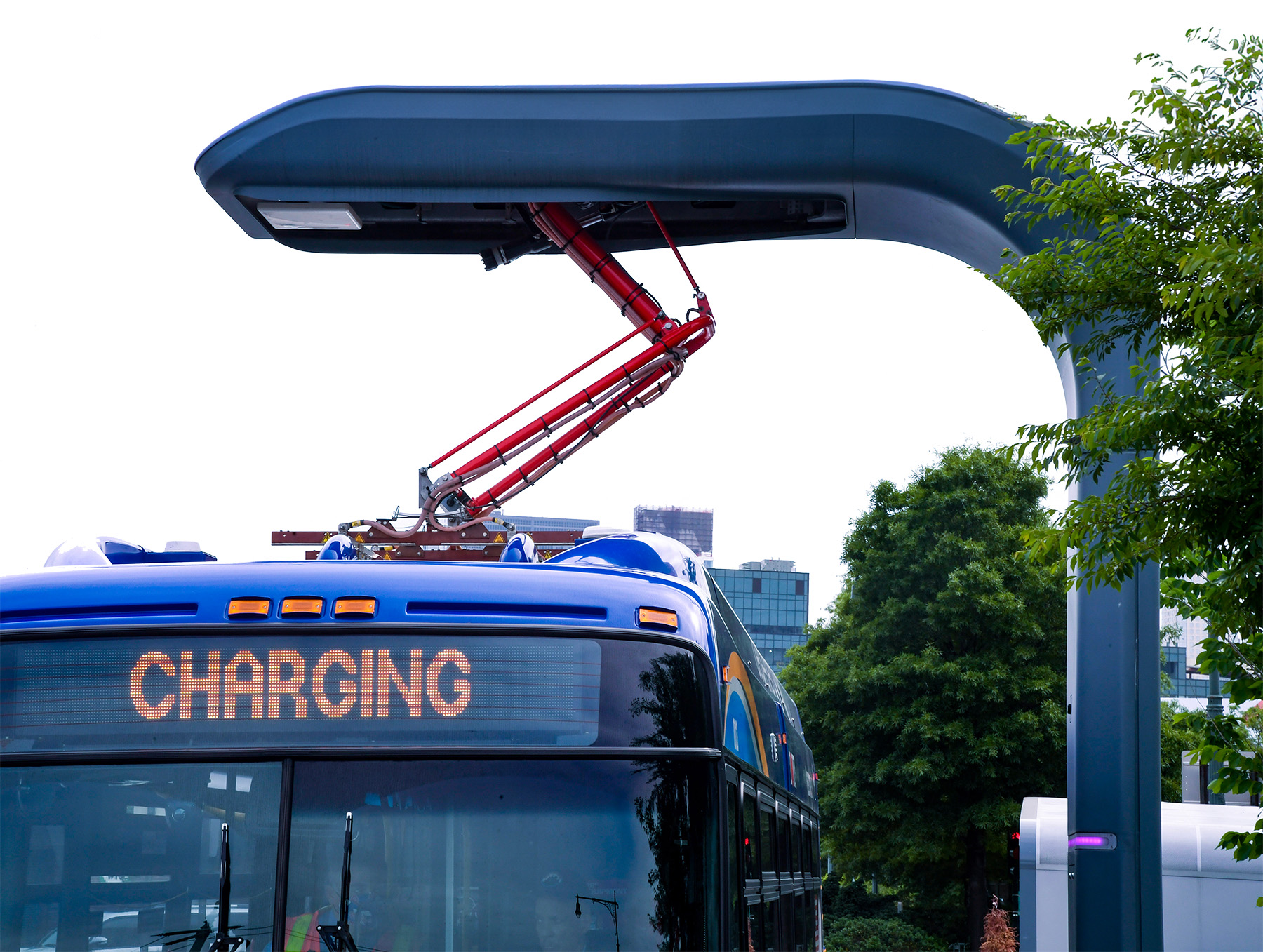
In addition, the 2021 Infrastructure Investment and Jobs Act strongly encourages the transition to EVs by investing $7.5 billion in developing an EV charging network in the U.S., $10 billion in clean transportation efforts, and another $7 billion for the development of EV battery componens and other critical aspects of the EV industry.
As the nation, and especially its city and regional transit agencies, moves toward this electric future, civil engineers will play a vital role in planning, designing, and installing new EV infrastructure and in adapting or updating existing systems.
Grappling with the grid
Perhaps the most important infrastructure challenge in the push for EVs involves, not surprisingly, the nation’s electric grid, which consists of some 600,000 mi of transmission lines, according to the U.S. Department of Energy. But to meet President Joe Biden’s goals of carbon-free electricity generation by 2035 and an overall net-zero economy in terms of greenhouse gas emissions — for transportation and other energy needs — by 2050, the U.S. must construct more than 1 million mi of new transmission lines and make other major upgrades to the grid, notes a February 2022 policy brief, “The Challenges of Decarbonizing the U.S. Electric Grid by 2035,” from the Belfer Center for Science and International Affairs at the Harvard Kennedy School.
New transmission lines are especially critical for adding renewable energy sources to the overall grid, given that great distances can separate where the renewable energy might be generated and where that power is most needed. “In the United States, the greatest potential wind energy resources are in the Midwest and along the (East and West) coasts, while the greatest solar energy resources are in the Southwest and in Florida,” the Belfer policy brief explains.
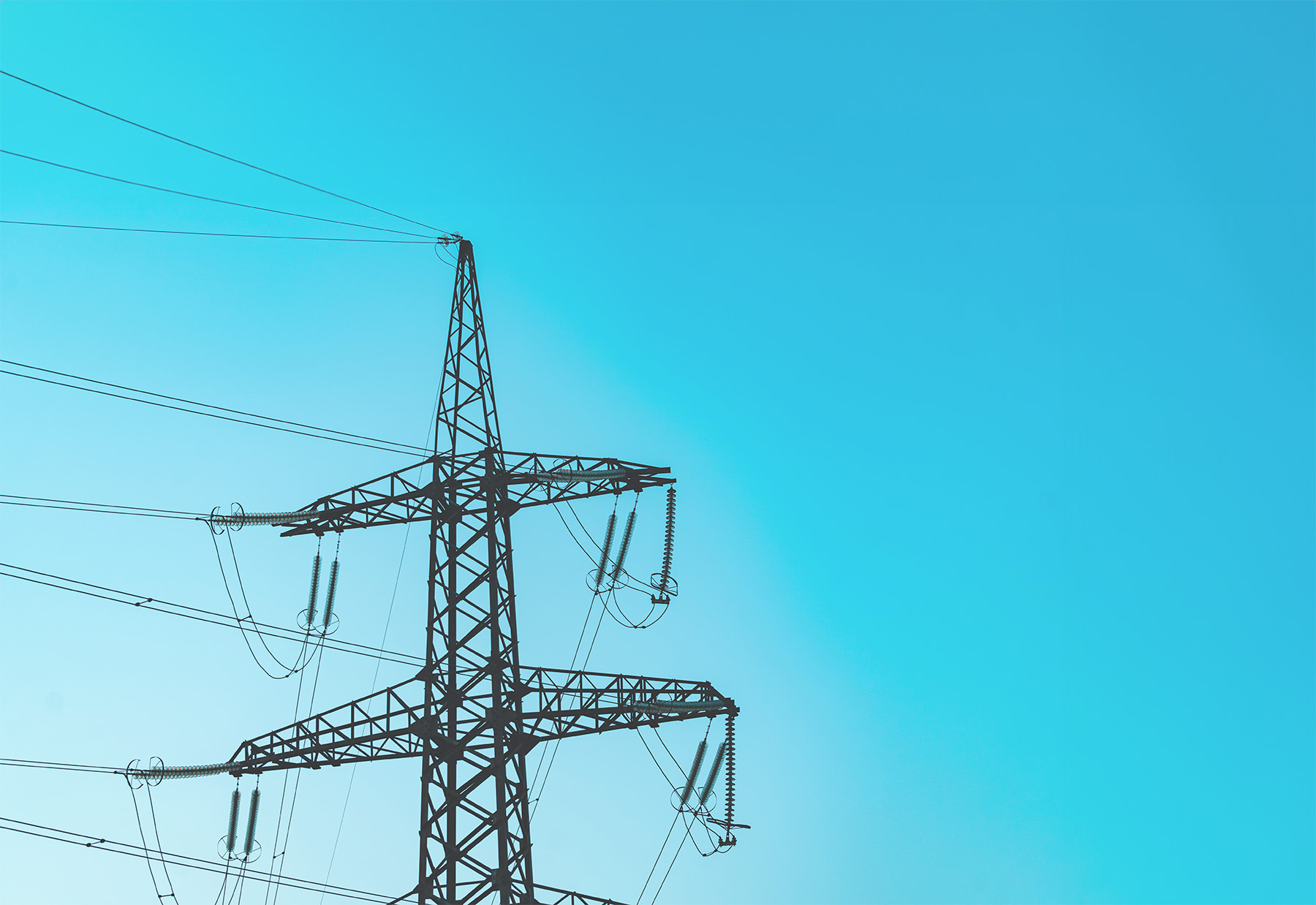
Unfortunately, the U.S. is not very good at building new transmission lines in any sort of timely fashion, warns Otto Lynch, P.E., F.SEI, F.ASCE, a vice president at Bentley Systems Inc., based in Exton, Pennsylvania, and the head of its power line systems operation. It takes at least 10 years and sometimes as much as 20 just to get the regulatory approvals needed to construct a new transmission line, especially a line that crosses multiple states, says Lynch.
The process can involve more than 40 government agencies — local, state, and federal — all of which might request additional information or have different, sometimes conflicting, requirements and even varied definitions for key terms, such as what qualifies as wetlands and how those wetlands can or cannot be built upon, he explains.
“It’s just a huge time sink!” says Lynch, who stresses the need for a single point of contact to help the energy industry cut through all that government red tape.
In at least one hopeful sign for energy producers, the U.S. Federal Energy Regulatory Commission issued a final rule in July titled “Improvements to Generator Interconnection Procedures and Agreements.” The rule is intended to streamline the process by which new sources of energy generation — which often involve renewable energy sources — connect to the existing transmission system, explains Jay Landers, a contributing editor to Civil Engineering Online, in a Sept. 12 article, “FERC takes aim at electric generation interconnection backlog.”
Weighing the concerns
Another concern regarding EVs is a lack of codes and standards for the interaction of EVs with existing infrastructure, notes Eva Lerner-Lam, NAE, M.SAE, F.ITE, M.ASCE, the founder and president of Palisades Consulting Group Inc., in Tenafly, New Jersey. Lerner-Lam, who is working with ASCE’s newly established Standards Department to develop a market-driven program for developing new codes and standards regarding EVs, points out that they can be as much as 40% heavier than comparable gasoline- or diesel-powered vehicles and can accelerate much faster with higher torque.
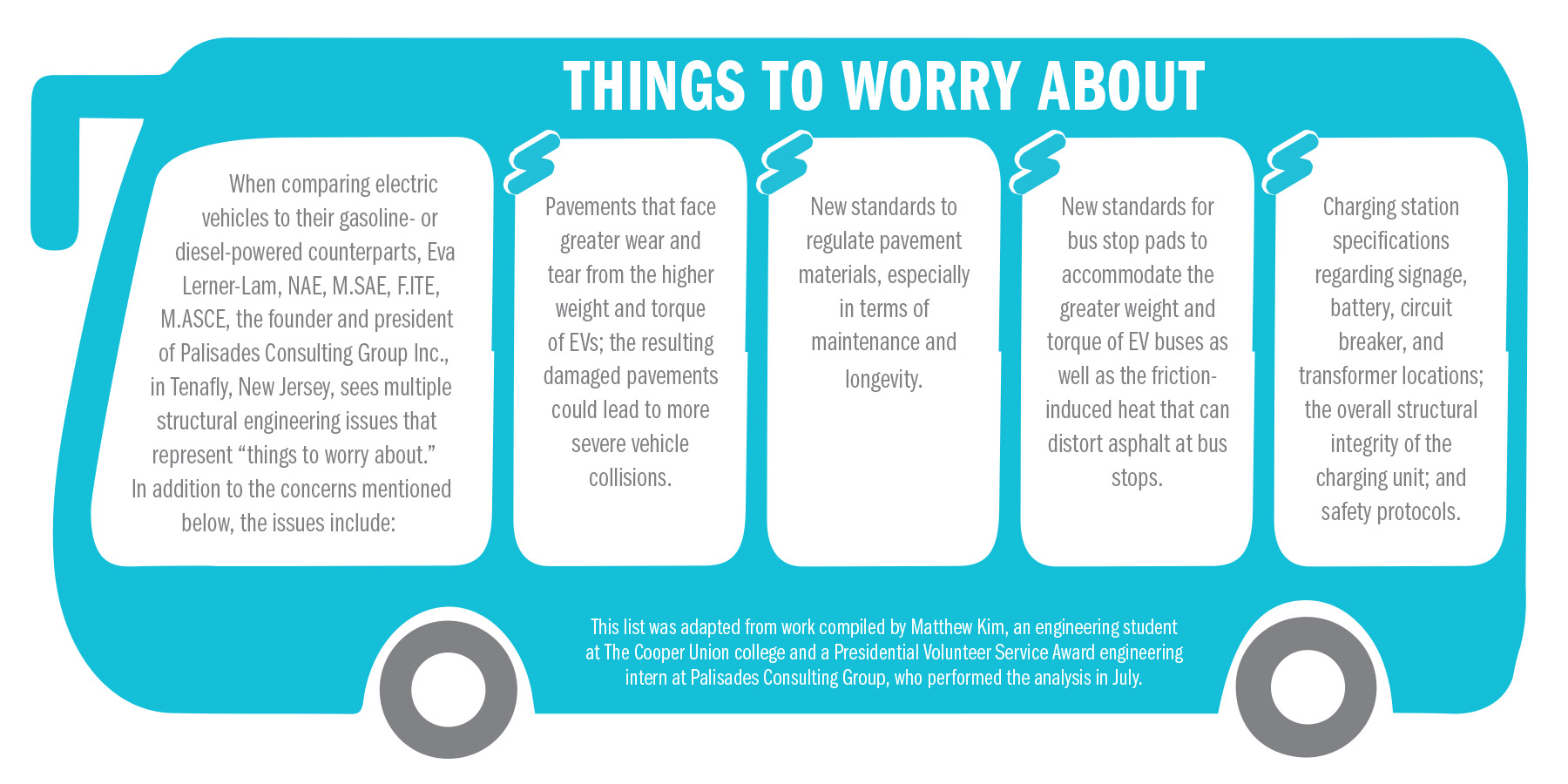
Such differences raise a number of structural issues for everything from bridges, ramps, and parking garages that must support those heavier EVs to the placement of utility poles. In some cases, those poles are just a few feet from curbs that the higher-torque EVs can easily drive over, which leaves the poles at greater risk from collisions, explains Lerner-Lam (see above).
The battery systems in these vehicles also can pose new and complicated challenges regarding fire safety that civil engineers must address (see “EVs and Fire Safety” see below).
For transit agencies and other entities that operate fleets of vehicles they intend to electrify, civil engineers are resolving EV infrastructure issues with careful planning and innovative solutions. These include measures ranging from traditional civil and structural engineering, such as metal frameworks designed to support overhead charging systems or ground improvements to accommodate poor site conditions, to the creation of microgrids to ensure adequate electrical capacity through the use of solar panels, battery storage systems, and generators to provide greater renewable energy and resiliency.
The global sustainable development consultancy Arup has supported the implementation of these solutions at two locations in the eastern U.S. Working with Boston-based energy consultant AlphaStruxure at the Brookville Smart Energy Bus Depot in Montogomery County, Maryland, for example, Arup supported the design of a 6.5 MW microgrid that includes a steel canopy to support overhead photovoltaic panels. These panels will cover most of what used to be an open parking lot for roughly 100 diesel buses, which the Montgomery County Transit Service plans to switch out for electric buses by 2035, says Geoff Gunn, P.E., LEED AP, an associate principal and Americas East Energy leader in Arup’s Boston office.
Steel structures also elevate the charging systems — primarily plug-in devices but also a few pantographs — and support a battery energy storage system that is about the size of a standard shipping container and weighs roughly 70 tons, Gunn says. The BESS is a rechargeable system that can store excess energy generated by the solar panels during the day while the buses are on their routes. That power can then be accessed at night or when the grid is down, too expensive, or otherwise not the best choice for charging, Gunn explains. The site also features natural-gas-powered generators that, like the BESS, provide a resilient, supplemental power system.
Elevating the charging equipment helps keep the site from becoming overcrowded with new infrastructure, which is especially important because the solar panel canopy already involves the addition of columns that diminish the available space for parking buses, Gunn notes. So putting the actual chargers overhead “means one less thing for the buses to worry about hitting when they drive around on-site,” he explains.
A gabion wall was constructed on a sloping portion of the site to support the natural gas generators and minimize the loss of available space for buses, Gunn adds.
Arup also designed a microgrid system on a somewhat smaller scale for the Martha’s Vineyard Transit Authority in Massachusetts, which currently operates 17 electric buses, representing half its fleet; the agency plans to electrify a further seven buses next year, Gunn says. In addition to solar power, a BESS, and backup generators, the Martha’s Vineyard project also features inductive charging technology at two sites along the bus routes. Inductive charging uses in-ground systems and pads that can be lowered to wirelessly charge the vehicles when they stop at the end of a route or have 10 minutes or so during a layover.
“The idea is that (inductive charging) should give them enough of a top-off so they don’t have to return to the main depot in the middle of the day” for a complete charge, Gunn explains.
The inductive charging systems were chosen because they are less physically and aesthetically intrusive for sites on Martha’s Vineyard that are “historically sensitive,” Gunn adds. Other systems, such as overhead pantographs, would never have been approved at those sites, he adds.
Driving flexibility
Flexibility is a critical trait in preparing transit agencies for the electric future, notes Gunn. The EV industry and its technology are relatively new and rapidly changing. And since it can easily take five years or more to design and construct a new bus depot to accommodate electric buses, that design has to be flexible enough in case the charging system designed for today is no longer manufactured by the time the facility opens. Or the vendor might have a new version that uses different connections or weighs significantly more than what was originally expected. “So you need to plan for that even within the life cycle of a single project,” Gunn explains.
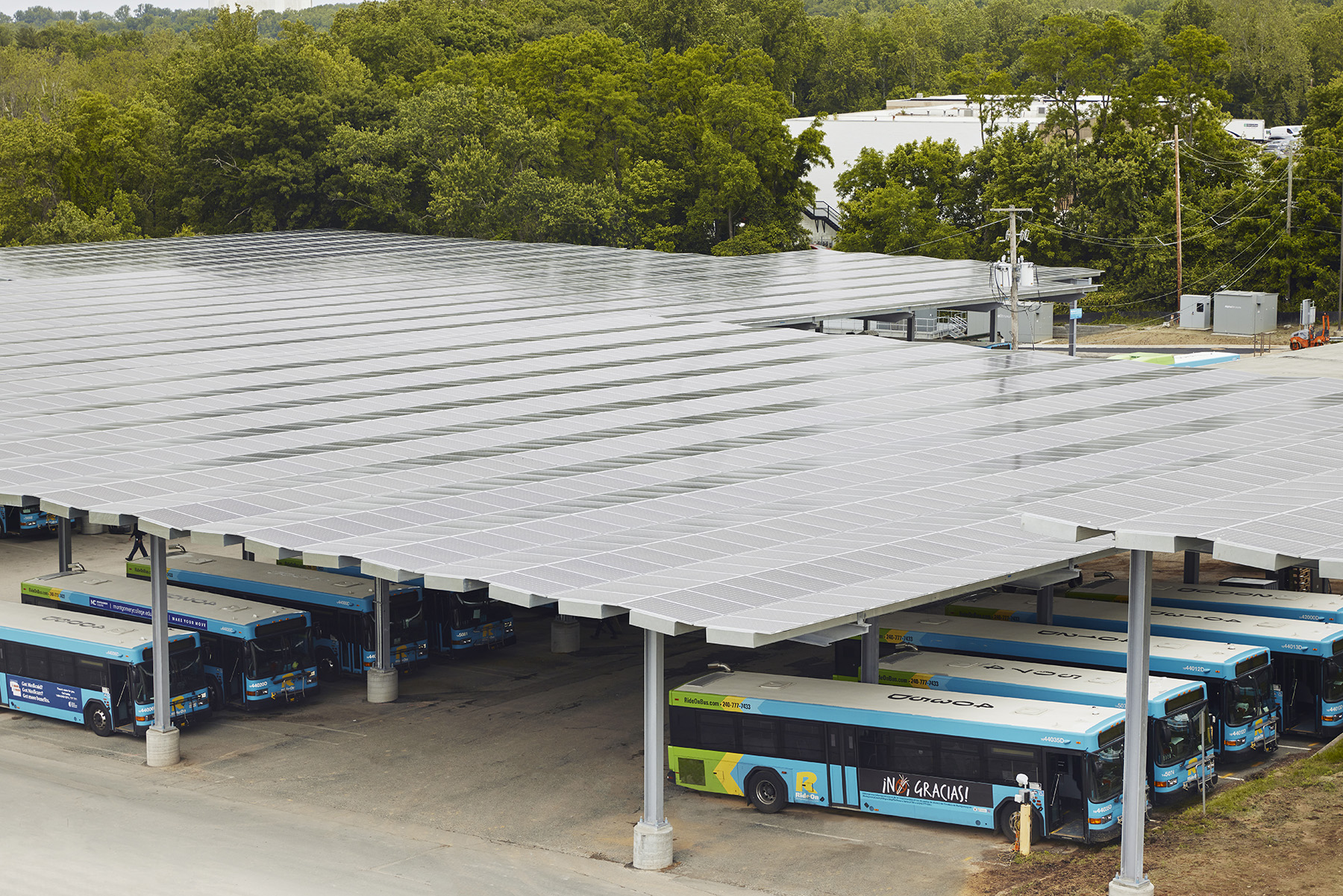
In Georgia, the infrastructure-focused professional services firm STV is partnering with the Metropolitan Atlanta Rapid Transit Authority on the Clayton Multipurpose Operations and Maintenance Facility that will eventually accommodate 300 electric buses. Expected to be operational by the end of 2026, the facility will initially accommodate three power sources for MARTA buses — diesel (until 2036), compressed natural gas (until 2040), and electric charging on an ongoing basis, says Jeffrey Messinger, P.E., LEED AP BD+C, an STV vice president and the firm’s national practice leader for transportation maintenance facilities. Moreover, MARTA’s current fleet of six electric buses uses plug-in chargers whereas the Clayton facility is being designed for pantographs.
“The challenges are trying to make sure we think about the different modes and make sure we’re setting up the facility to be flexible, to work with the three modes we’ve got today, the future buses we’ll have down the road, and also making it work for MARTA’s changing needs over time,” Messinger says. “As they expand, they’ll get more buses, and as they change their routes, they’ll have new areas they need to serve, so we need to make the facility flexible enough to handle the changes” that MARTA’s going to face.
New York’s MTA certainly must remain flexible as it expands from a fleet of just 15 electric buses today, with 60 more due by the end of 2024, to its goal of electrifying thousands of buses by 2040. Back around 2018 or so, the MTA installed plug-in chargers for its electric buses, says Sunil Nair, the MTA’s chief officer for zero emissions fleet transformation and fleet technology systems. But going forward, the agency plans to use pantographs, which represent “a whole different civil engineering puzzle,” Nair says.
The plug-in chargers were relatively easy to install on one side of a depot building where the buses park, Nair explains. But the installation of pantographs will be far more complicated, requiring “a fairly extensive depot constructability survey.” That survey will help determine whether the chargers can be installed inside the depot or outside the building. If outside, engineers must determine if the soil conditions can support the structural weight of the gantry or other structure that will elevate the pantograph systems, Nair says.
If the pantographs go inside the building, the survey should examine the existing structural columns to determine if they can support the additional weight of the pantograph system. Engineers must also determine if the ceiling heights are tall enough to provide the overhead space needed for the buses to pull under the pantographs and for the system to operate properly. The industry standard is about 15 ft, Nair says.
“A lot of our depots are fairly old, and some depots might not have ceiling heights amenable for the charging infrastructure setup,” Nair adds. Or the depot might need to relocate existing pipes or mechanical system equipment to make room for the charging systems.
At the same time, the engineers must also make sure that the depot’s ventilation system can accommodate the additional heat generated by the charging system and move that heat away from the depot to ensure that the chargers work as efficiently as possible, Nair says.
In some situations, engineers must even design an EV charging site to accommodate two types of charging systems for the same vehicle. A utility’s electric bucket maintenance truck, for example, can require a 50 kW or higher Level 3 DC fast charger for the vehicle itself but a separate 240-volt AC Level 2 charger for the bucket arm system. Engineers must design the facility so that each bucket truck “gets all its chargers placed in proximity to where they need to plug in,” explains David Taylor, a vice president in the Baltimore-area office of the engineering firm Dewberry. “So you can do multiple plug-ins with the same vehicle at the same time and don’t need to move the truck to a different location.”
Speaking with power
To successfully electrify a transit fleet, the agency and its civil engineering consultants need to stay in close contact with the electrical utility that will supply the power. As Nair explains, MTA “had to work with (the New York City utility) Con Edison to make sure we had appropriate metering to find out exactly how much power we were using on a regular basis.” The agency even collaborated with the utility to “test the chargers before the buses got there to ensure that when (they did get) there you could just plug in the chargers and the system was ready.”
Mark Peckover, P.E., a principal in the Portland, Oregon, office of engineering firm Stantec, recommends having ongoing conversations with the energy provider: “Anywhere from a quick conversation because the utility already has the capacity in its system to absorb the new loads or a multiyear conversation and multiyear master plan development to allow the utility time to upgrade its infrastructure,” Peckover explains. He stresses the need “to start those conversations with the utility as soon as possible because this could (require) a systemwide assessment for the utility.”
Moreover, the increased electrical demand could lead to “rate structure differences that require a legislative approval process, which always takes some time!”
To help transit agencies determine the costs and operational implications they can expect from electrifying their fleets, Analy Castillo, Ph.D., Stantec’s zero emissions technical lead based in the firm’s Salt Lake City office, developed a software tool called ZEVDecide that models the expected performance of electric and hydrogen vehicles, including their ranges, under the specific operational conditions of each fleet. The tool predicts the fleet’s anticipated power requirements and other factors, including cost and equipment specifications.
The tool is “crucial to understanding how many buses can be charged simultaneously,” Castillo explains.
“We simulate different charging dynamics, taking into account the fact that vehicles will come in at different times with different charging needs,” says Castillo. Thus, “we can simulate what will happen on a daily basis with an hourly resolution to make sure we have enough charging equipment and to accurately predict what the power demand load will be at the facility.” Such details are “crucial to inform the conversations with the utilities.”
STV also used its PEER modeling tool, which stands for Performance Evaluation of Electric Bus Routes, on the MARTA project and other fleet electrification projects nationwide, says Messinger. The software considers geographic data, such as inclines and slopes, to determine how much energy is needed for an electric bus to travel the route. “We look at passenger loads at different points along the route (and) dwell times when the bus is at a station or stopped for passengers, traffic, or other reasons,” Messinger explains.
“We look at all the metrics that affect the operation of buses in a fully electrical environment,” Messinger concludes.
EVs and fire safety
The most important thing to understand about the lithium-ion batteries that power most electric vehicles is that if the battery catches fire, it is difficult to extinguish. “Nothing really puts out a lithium-ion battery fire,” says Jeffrey Messinger, P.E., LEED AP BD+C, an STV vice president and the firm’s national practice leader for transportation maintenance facilities. Lithium-ion batteries “create their own oxygen and will burn until they burn themselves out!”
So the goal in fighting a lithium-ion battery fire is to “prevent the entire bus from being engulfed in flames or letting the flames spread to other buses or other infrastructure within the facility, destroying the building,” Messinger explains.
The technology behind lithium-ion batteries is evolving rapidly and produces numerous designs and chemistries that pose “different levels and mixes of risk,” notes Ali Ashrafi, Ph.D., P.E., CFEI, M.ASCE, a principal in the Washington, D.C., office of Thornton Tomasetti. When a lithium-ion battery experiences what is known as thermal runaway, the temperatures can reach a point at which combustible gases can be released, resulting in a fire or explosion, Ashrafi explains. And as these gases are toxic and flammable themselves, they are hazardous and potentially pose risks to people nearby, especially in enclosed spaces, adds Juan Londono, Ph.D., a senior associate in the New York City office of Thornton Tomasetti.
But because the technology is so new, “we are looking at things that are not fully within the range of the current codes,” Ashrafi notes. Thus, lithium-ion battery fire safety measures — which are still being developed — are not standardized nor do they follow a recognized template. Instead, they depend “on the context and specific needs of specific locations,” Ashrafi says.
For example, the approach is different if electric buses are housed inside a depot building — where there will be concerns about helping people egress and providing access to firefighters — or outside in a parking yard. The risk can also depend on how close together the buses are parked; some engineers even point to a possible future in which self-driving buses could move themselves out of harm’s way.
Active fire-suppression systems, such as sprinklers, can also be considered. While a lithium-ion fire is hard to put out, the application of water can mitigate the fire and directly protect adjacent vehicles, thus helping contain the event, says Londono. It does, however, take a larger volume of water to contain an EV fire than a fossil fuel vehicle fire, notes Ashrafi.
And while some engineers warn that fighting thermal runaways with water can wash hazardous chemicals into storm sewers, Ashrafi says recent studies suggest the risk is similar to the possible contamination from fighting conventional fires. Besides, “no better solution (than water) is out there yet,” he says.
In addition, new developments in sodium batteries might someday provide “a safer and cheaper alternative to lithium-ion batteries,” according to researchers at Australia’s Deakin University and the University of Queensland.
Ashrafi also notes the importance of keeping the risks of lithium-ion fires in context. The switch to electric buses is one part of the overall effort to combat climate change, which itself poses serious risks of more frequent and more intense wildfires and hurricanes. “So as we look at the risks, as a society, we need to look holistically.”
Robert L. Reid is the senior editor and features manager of Civil Engineering.
This article first appeared in the January/February 2024 print issue of Civil Engineering as “Accelerating Electric.”
This article focused on the infrastructure needs of transit agencies regarding electric vehicles. Readers interested in public charging networks for electric vehicles should read "Why privately owned EVs need public charging infrastructure."