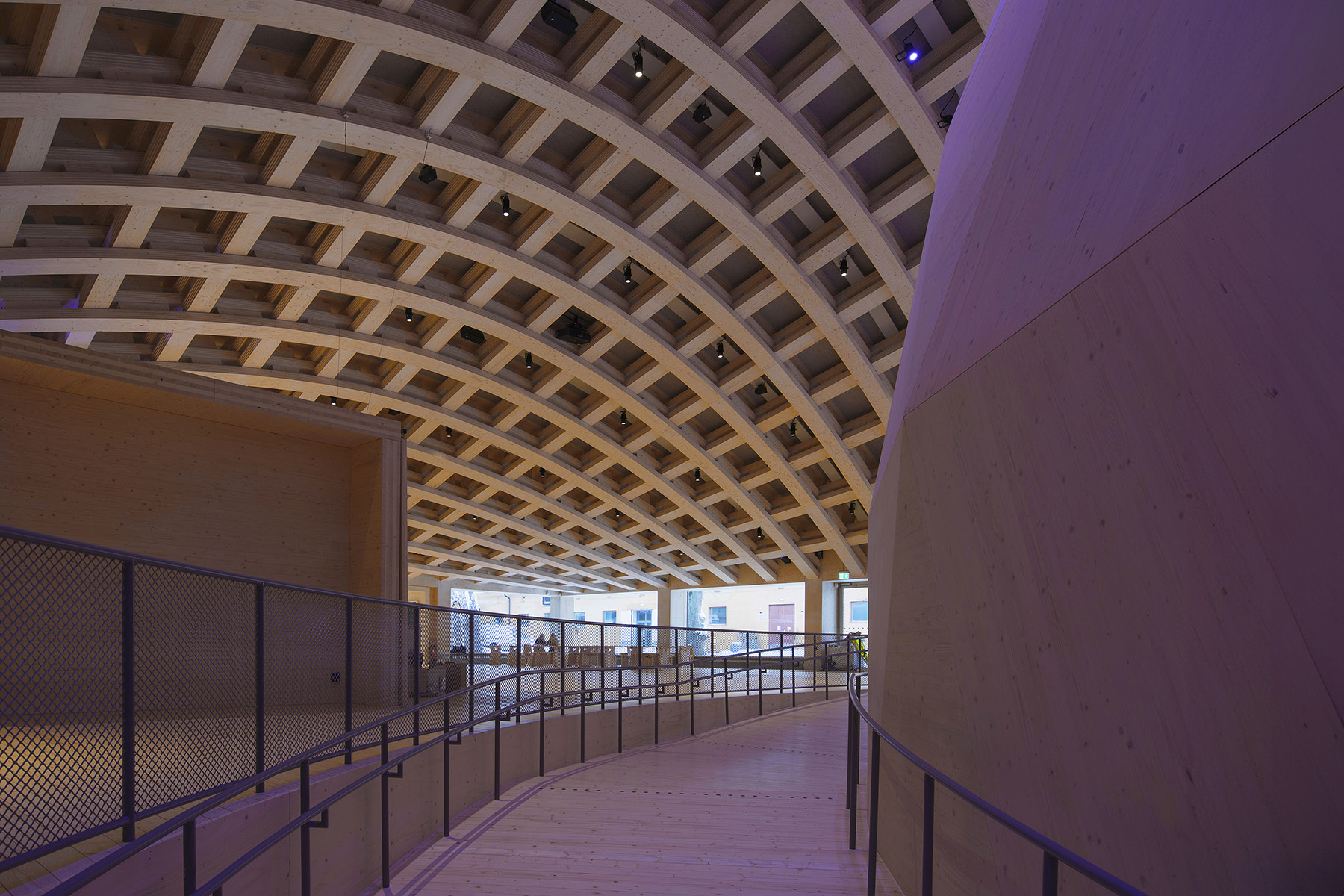
By Robert L. Reid
An extension to Stockholm’s science museum relied on a complex, free-form timber structure. Interestingly, most of the crisscrossing roof beams that cover the facility’s 3D experience dome were bent on-site.
Wisdome Stockholm is a new 1,325 sq m extension to Sweden’s National Museum of Science and Technology that features a unique timber design. The facility consists of a roughly 22 m diameter wooden dome that houses a 3D cinema. The dome is covered by a free-form, grid-shell wooden roof that creates a column-free interior space measuring 48 m long by 26 m wide. Sharing a wall with the science museum’s main building, but separated by a movement joint, the Wisdome extension was designed to “showcase the possibilities of timber construction,” says Jessika Szyber, a civil engineer and the business development manager for Stora Enso, a wood products manufacturer and supplier headquartered in Helsinki.
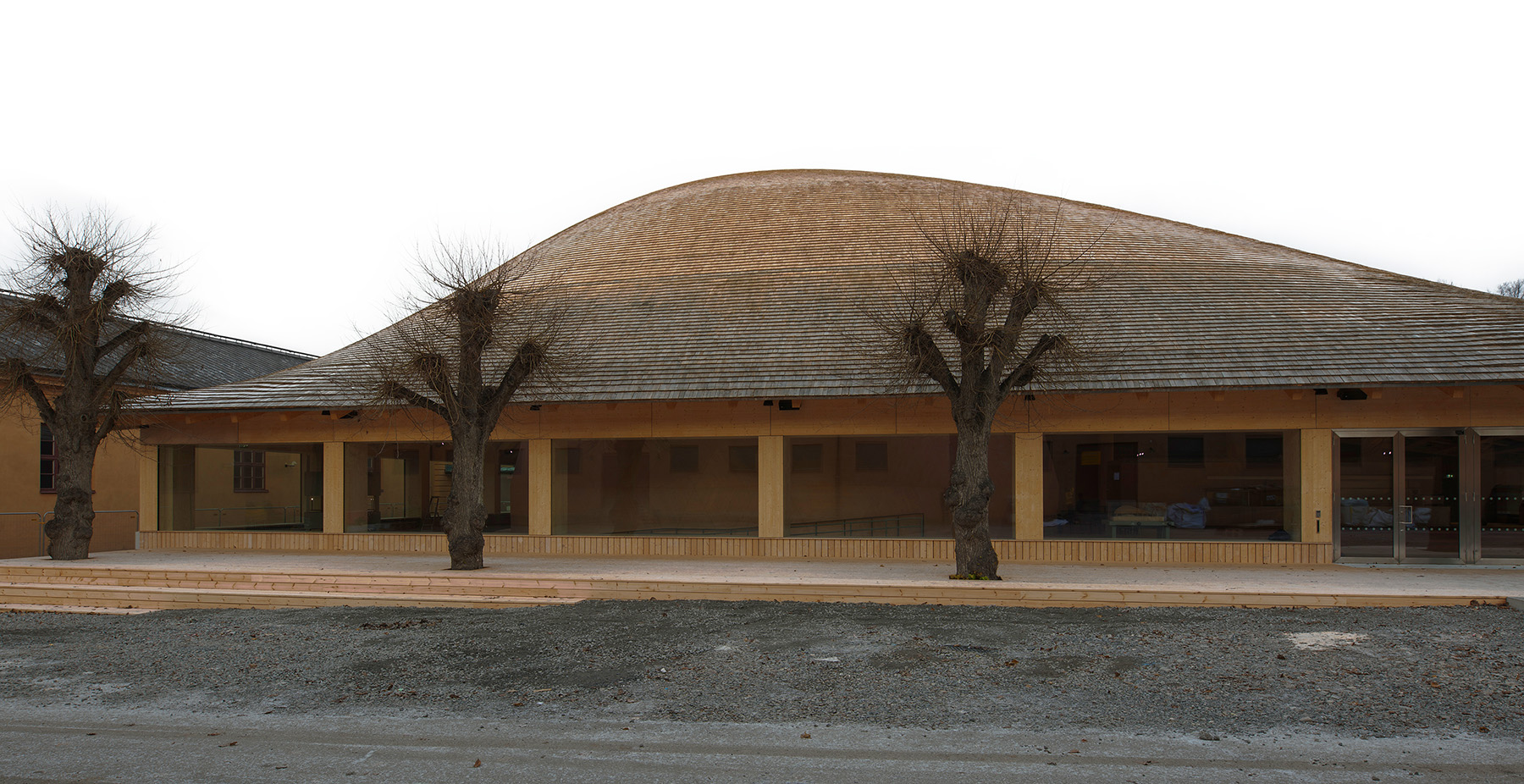
As one of the leading partners in the development of the Wisdome project, Stora Enso provided the timber material used in the construction. Specifically, the grid shell roof was formed from crisscrossing layers of laminated veneer lumber beams, while the dome was constructed from cross-laminated timber triangular sections.
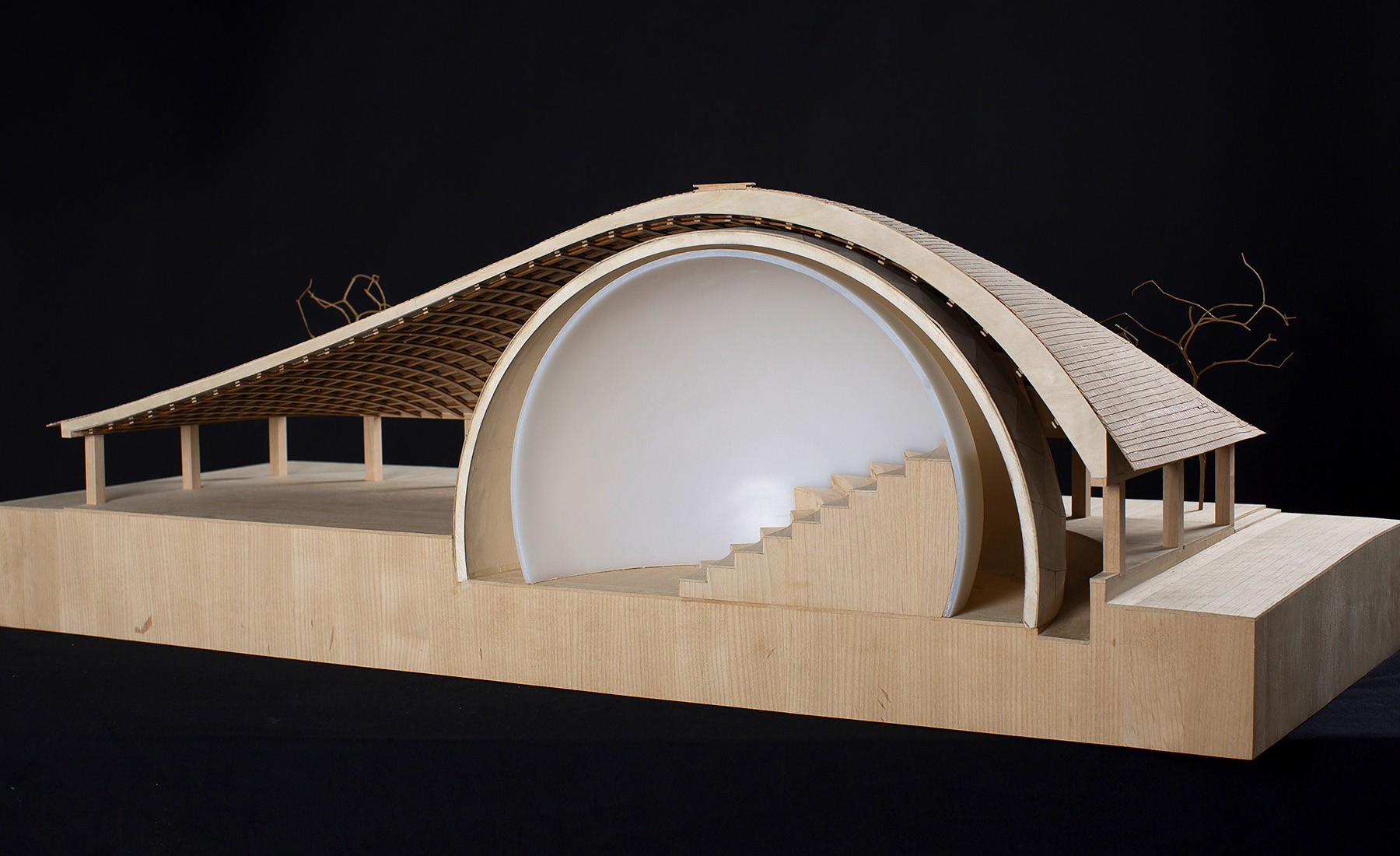
A 2019 architectural contest specified the use of LVL and CLT on the Wisdome project. In addition to Stora Enso, the Wisdome design team chosen through the contest included architect Elding Oscarson, based in Stockholm, and structural engineer Dipl.-Ing. Florian Kosche AS, based in Oslo, Norway. SJB Kempter Fitze, of St. Gallen, Switzerland, was the timber engineer; Blumer Lehmann, of Gossau, Switzerland, was the specialist timber subcontractor; Design-to-Production, of Zurich, Switzerland, was the parametric design and timber consultant; and Oljibe Stålbyggnads AB, of Stockholm, was the general contractor.
Courtyard extension
The museum sits within the Royal Djurgården, a national park in the center of Stockholm owned by King Carl XVI Gustaf of Sweden. The Wisdome Stockholm building was constructed on a former courtyard — between four existing buildings — that had been used for parking at the science museum. The king personally cut the ribbon to inaugurate the new facility when it opened to the public in December 2023.
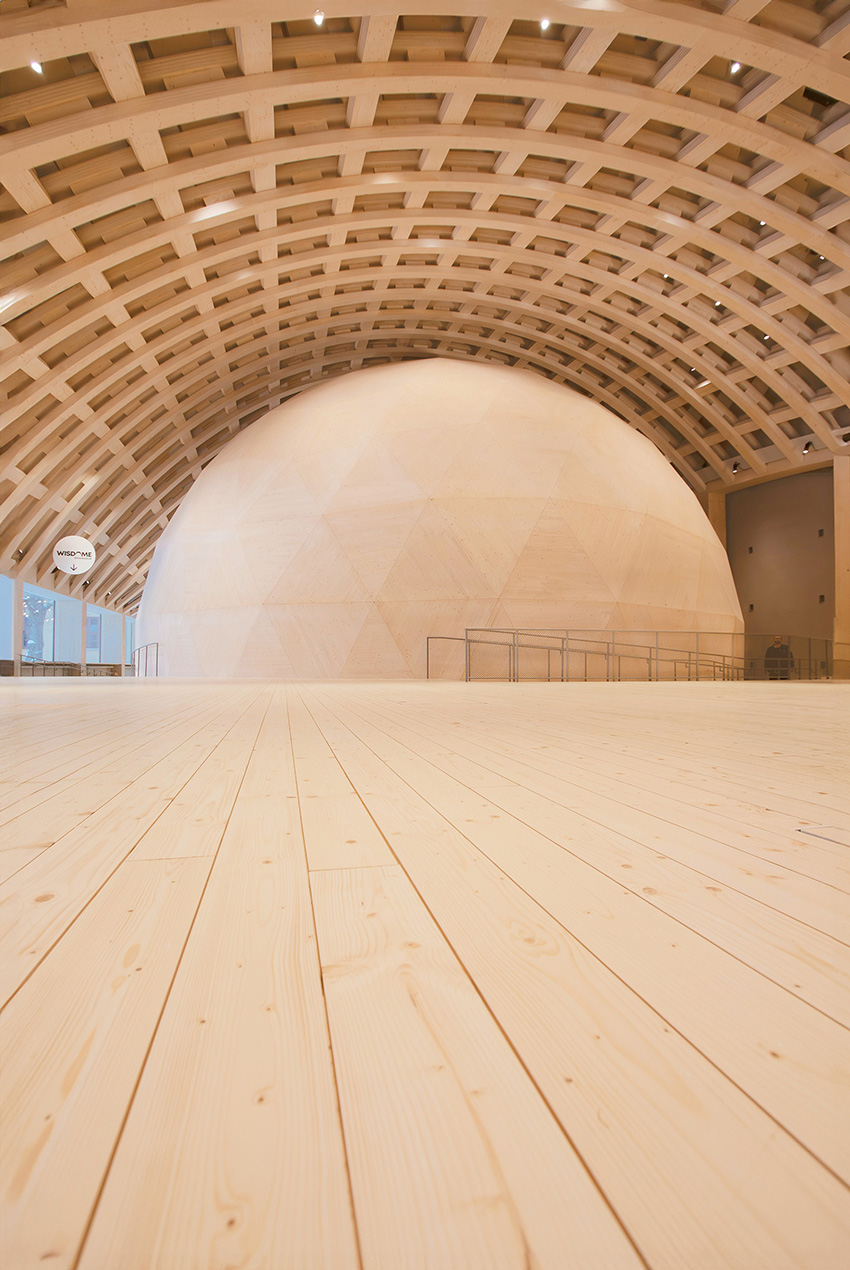
On the courtyard site, the project team drilled roughly 100 boreholes to depths of 240 m as part of the extension’s geothermal heating system, Szyber notes.
NIBE Industrier AB, of Markaryd, Sweden, designed the geothermal system and served as a sustainability consultant on the project. According to the firm’s 2022 annual report: “The building’s energy requirement will be 232,000 kWh per year, of which as much as 165,000 kWh will come from renewable energy, corresponding to energy savings of 71% and a reduction in greenhouse gases of 15 tonnes per year.”
Likewise, “for the large cooling requirement, 60% will be covered by free cooling from the boreholes,” the NIBE annual report noted.
The foundations for the extension consist of a new concrete slab that was installed on the courtyard site — 260 mm thick generally but with select locations of 750 mm and 950 mm to accommodate the perimeter columns that support the edges of the roof, according to Szyber.
Free-form feature
Perhaps the most striking feature of the extension is the undulating, vaulted roof that sweeps up and over the hemispherical dome inside the building. The roof was formed from five layers of beams arranged in alternating patterns along the longitudinal and transverse directions of the structure.
Each beam, in turn, features five lamellae — individual LVL panels — stacked atop each other. In total, the Wisdome roof was constructed from roughly 20 km of LVL panels, according to the Blumer Lehmann website.
Only the lamellae in the first, lowest beams were glued together, while those in the remaining beams are held together via a series of dowels and pegs, also made of LVL material, says Stefan Rick, a timber engineer at SJB Kempter Fitze. The conical dowels serve two purposes — to connect the LVL layers where they cross each other and to accommodate shear forces, Rick adds.
The beams for the first layer of the roof were also the only ones to arrive at the worksite already bent into their final shape, which allowed that layer to serve “as a scaffold and structural aid for the complex assembly process,” according to Blumer Lehmann. The rest of the roof beams were delivered as flat elements that were bent on-site — an unusual approach, Rick states.
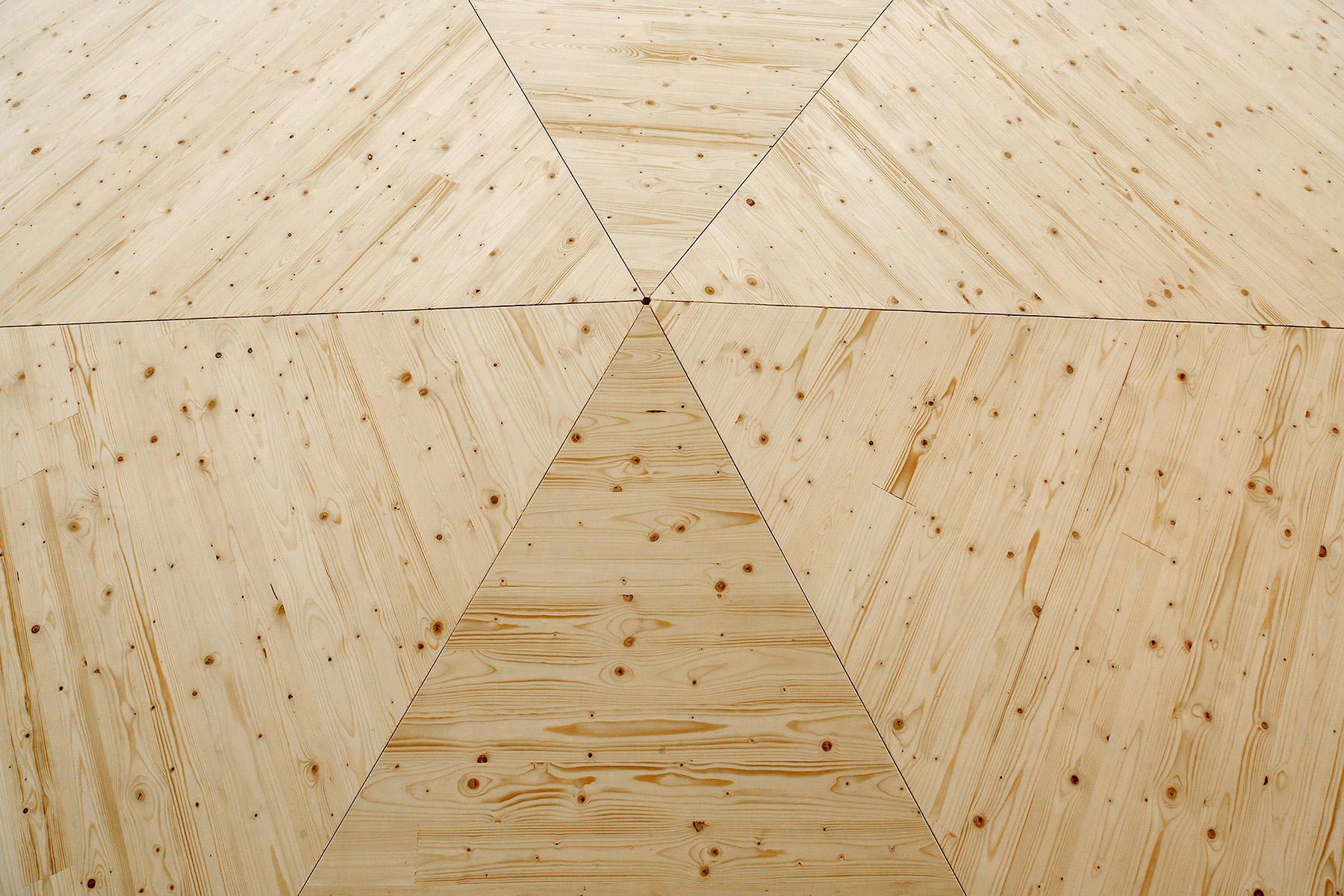
Traditionally, a free-form structure such as the Wisdome roof is made from glulam products that have already been curved by a computer numerically controlled machine, Rick says. But on the Wisdome project, the milled lamellae were transported to the site and then bent and twisted into final shape. Because of the dowel and peg connections, the project required “maximum precision in planning and producing the components,” according to Blumer Lehmann, “because once bent, the holes for the connections — milled into the flat panel strips — must fit exactly.”
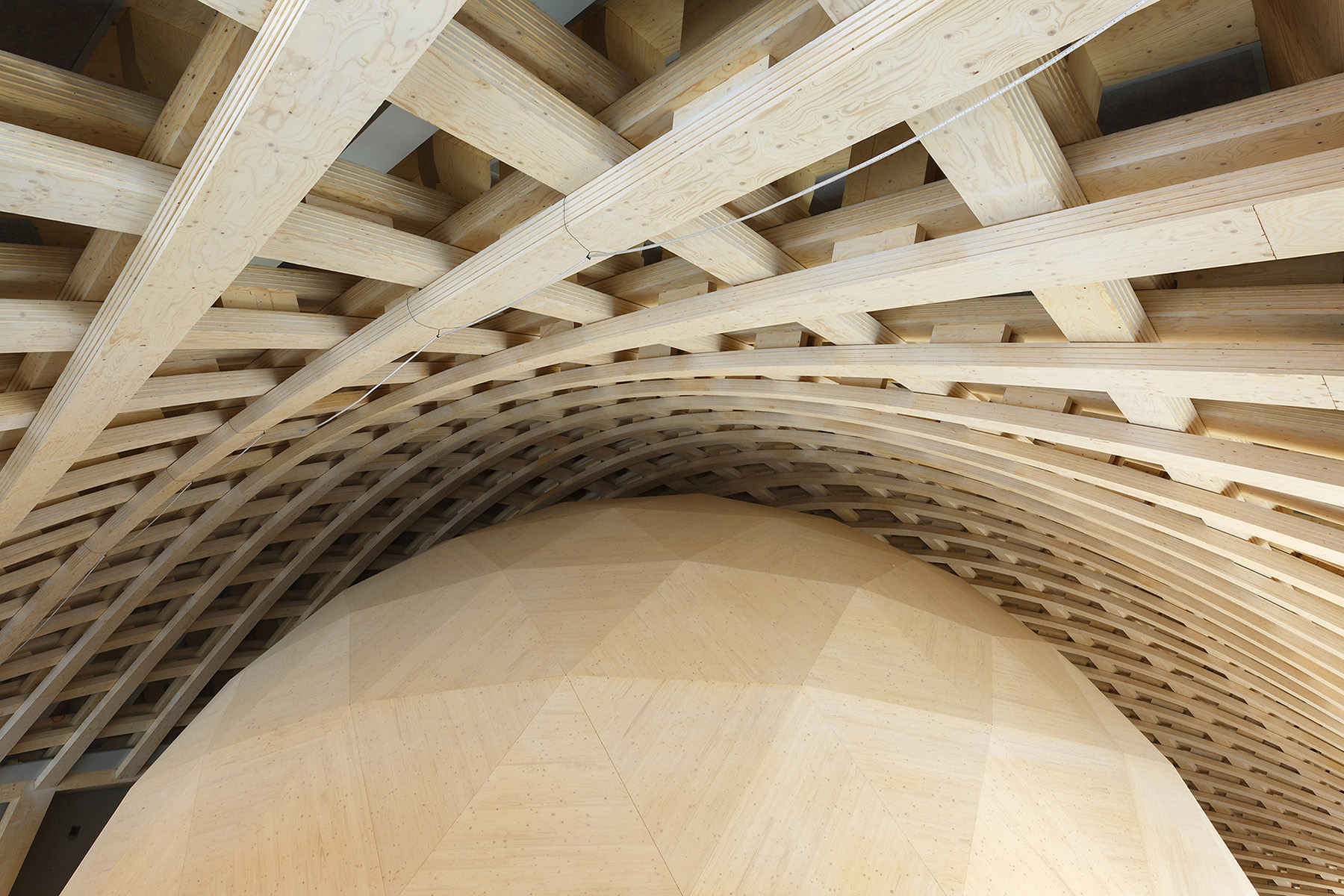
To help work with such precision and to determine factors such as the springback forces in bent LVL beams, Blumer Lehmann developed several full-scale mockups for the roof, says Szyber. These mockups helped the design team resolve challenges ranging from beam thickness to whether the final forms of the beams would meet the aesthetic designs of the architect and the museum, Szyber says.
Pretensioning and protection
The roof accommodates a fundamental wind velocity of 24 m/s and a basic velocity pressure of 0.36 kN/sq m, as well as a snow load of 2.0 kN/sq m. The structure is supported along its edges by 24 columns made of block-laminated LVL, measuring either 60 cm by 80 cm or 60 cm by 60 cm in cross-section. Because the arcing shape of the roof “creates horizontal forces that want to push the columns out ... we had to create a connection that can push against those horizontal forces,” says Rick.
“The first thing we did was make a fixed-moment connection at the bottom of the columns to the concrete (slab) — but this was not enough,” Rick says. So, in addition to the moment connections, the design team also added pretensioned rods inside most of the columns “to create a counter moment that is able to push inward at the top of the column against the horizontal forces of the roof.”
The pretensioning was not needed at the corner columns because the horizontal force created through the arched shape of the roof was negligible at the corners. In each of the other timber supports, however, two pretensioned rods were installed down through the columns and connected into a coupling at the concrete base. A timber edge beam was then installed at the top of the columns “to enclose the free form construction (of the roof) all the way round,” Blumer Lehmann notes.
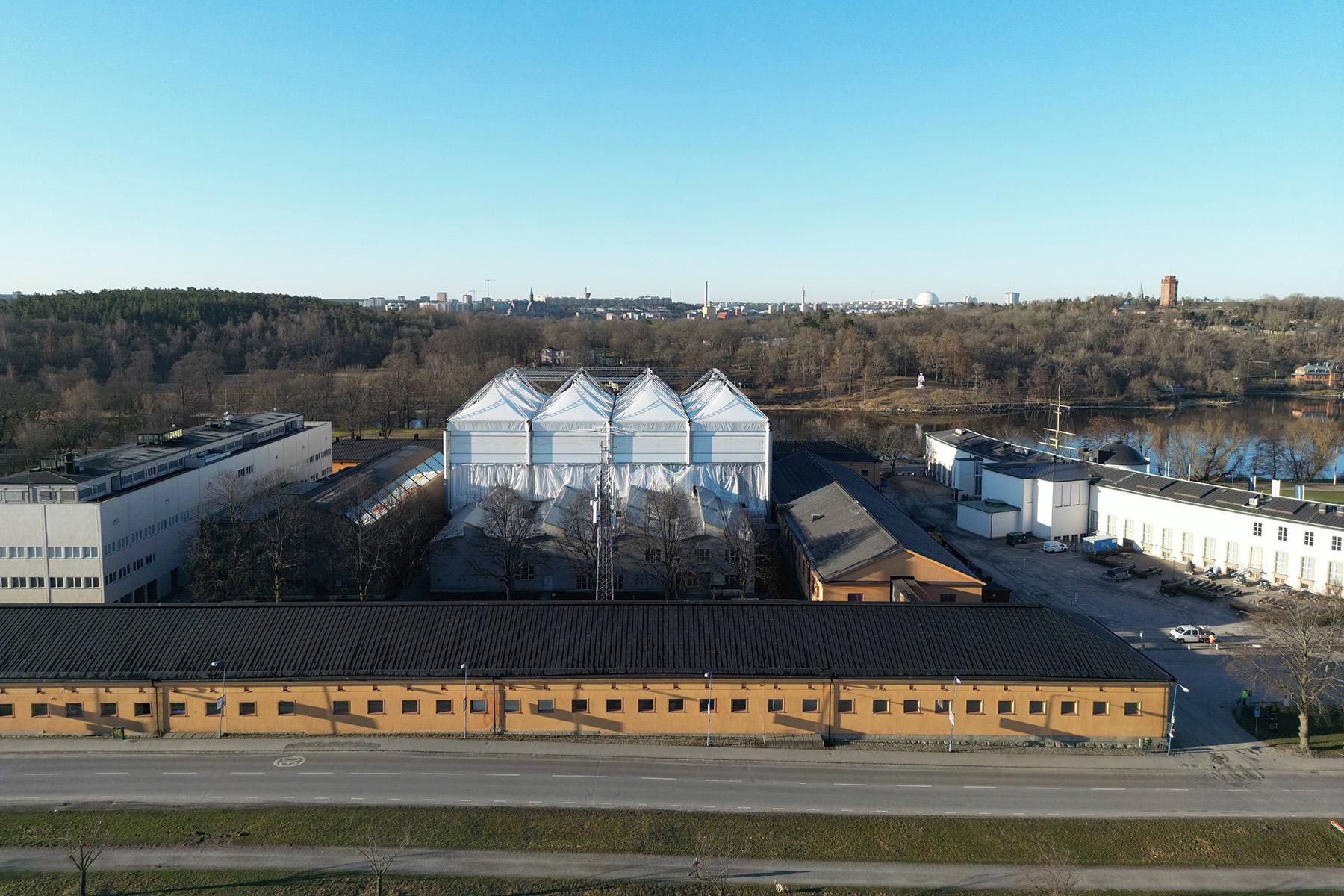
The extension features a glazed facade that runs between the columns. Wooden shingles — coated against moisture penetration — cover the roof. To further protect the timber material during construction, the team raised a giant tent over the worksite for a year, from May 2022 to May 2023. During the construction of typical wooden structures, weather protection is not needed, Szyber says. “But here, everything required tolerances of just 1 mm, and if the material got moist, it could change its shape,” she explains.
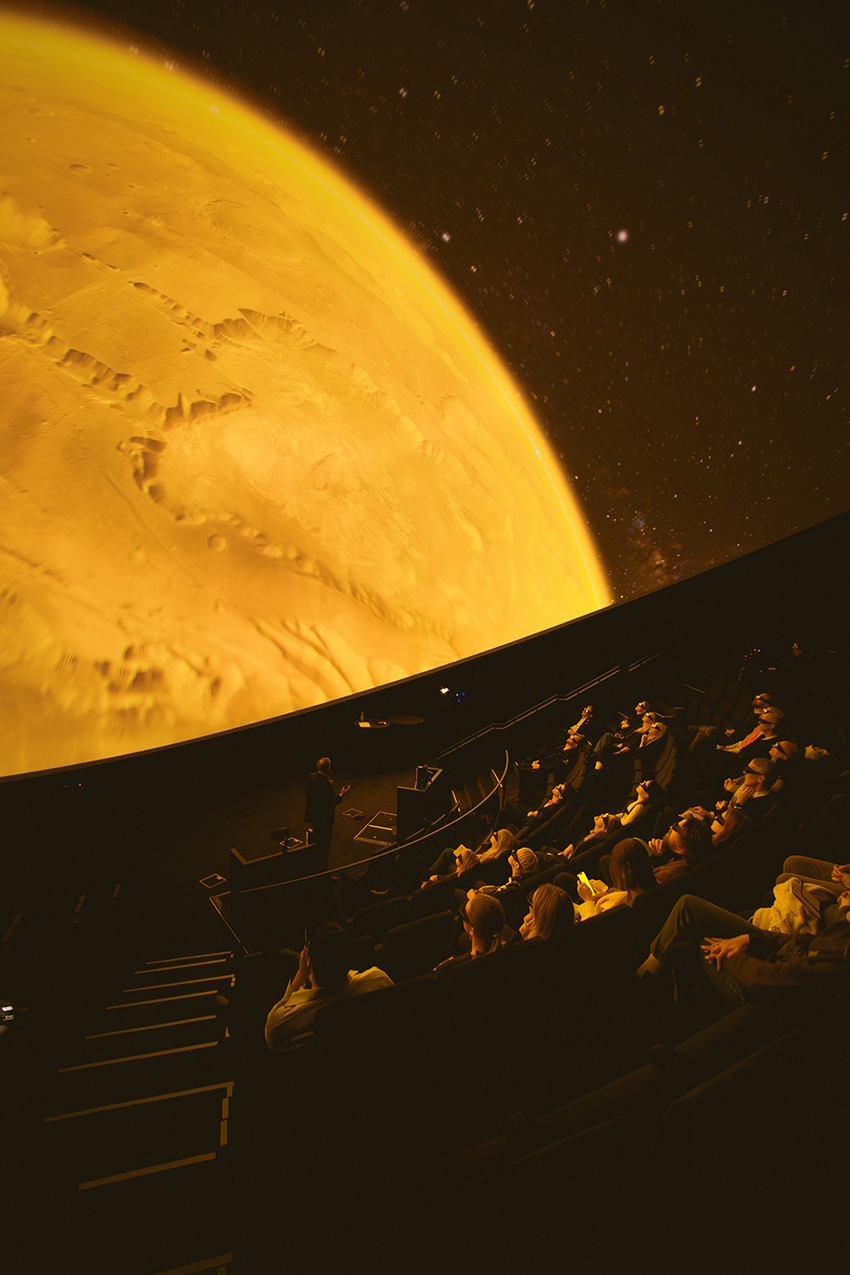
The Danish company SiteCover A/S provided the tent, which featured a “self-supporting, flexible system with telescopic steel legs and an umbrella-like roof,” according to the website of KI Consulting Engineers, of Copenhagen. KI was responsible for structural design and verification services for the tent system’s steel structure.
Designed to protect the site against heavy snow, wind, and rain, the tent structure covered an area measuring 58 m long by 43 m wide and featured a crane with a hook height of 20 m. “Since the new building was so close to the existing museum, one side of the tent had to be kept open,” KI noted.
Dome design
The eponymous dome for the extension was formed from 277 uniquely cut triangular sections that were then combined into hexagonal panels and mounted to the dome structure, says Rick.
The dome features an inner shell — which encloses the 100-seat 3D cinema arena — and an outer shell, with layers of fireproofing and acoustical materials in between, says Szyber.
To construct the dome, additional mockups were created, and several digital tools were used, including Stora Enso’s proprietary software systems Calculatis for the planning phase and Sylva360 for the installation phase.
In addition, sensors manufactured by Wiiste Oy, of Tampere, Finland, were installed to monitor moisture in the wood elements over time.
The timber elements in the dome and roof were all sprayed with a fire retardant.
Timber testament
Designed as a science-focused educational venue for the general public, Wisdome Stockholm can also serve as a learning tool for future engineers and architects, notes Szyber. This is especially true regarding the project’s use of digital planning and fabrication methods as well as the building’s role “as a testament to the possibility of timber construction,” she adds. For example, although the construction involved certain off-the-shelf timber products, these materials were used in new forms — such as the pretensioned LVL perimeter columns — and assembled in innovative ways, such as the on-site bending of the roof beams.
Although the design initially “seemed impossible, we made it possible,” Szyber says, concluding: “The project really pushed us to discover new things.”
Robert L. Reid is senior editor and features manager of Civil Engineering magazine.
Project credits
Client
National Museum of Science and Technology, Stockholm
Architect
Elding Oscarson, Stockholm
Structural engineer
Dipl.-Ing. Florian Kosche AS, Oslo, Norway
Project sponsor and timber supplier
Stora Enso AB, Stockholm office
Timber engineer
SJB Kempter Fitze, St. Gallen, Switzerland
Specialist timber subcontractor
Blumer Lehmann, Gossau, Switzerland
Parametric design and timber consultant
Design-to-Production, Zurich, Switzerland
General contractor
Oljibe Stålbyggnads AB, Stockholm
Sustainability consultant and geothermal system designer
NIBE Industrier AB, Markaryd, Sweden
Design management
Civita AB, Stockholm
Tent system design
SiteCover A/S, Store Merløse, Denmark
Tent system structural design and verification services
KI Consulting Engineers, Copenhagen
This article first appeared in the January/February 2025 issue of Civil Engineering as “The Wisdom of Wood.”