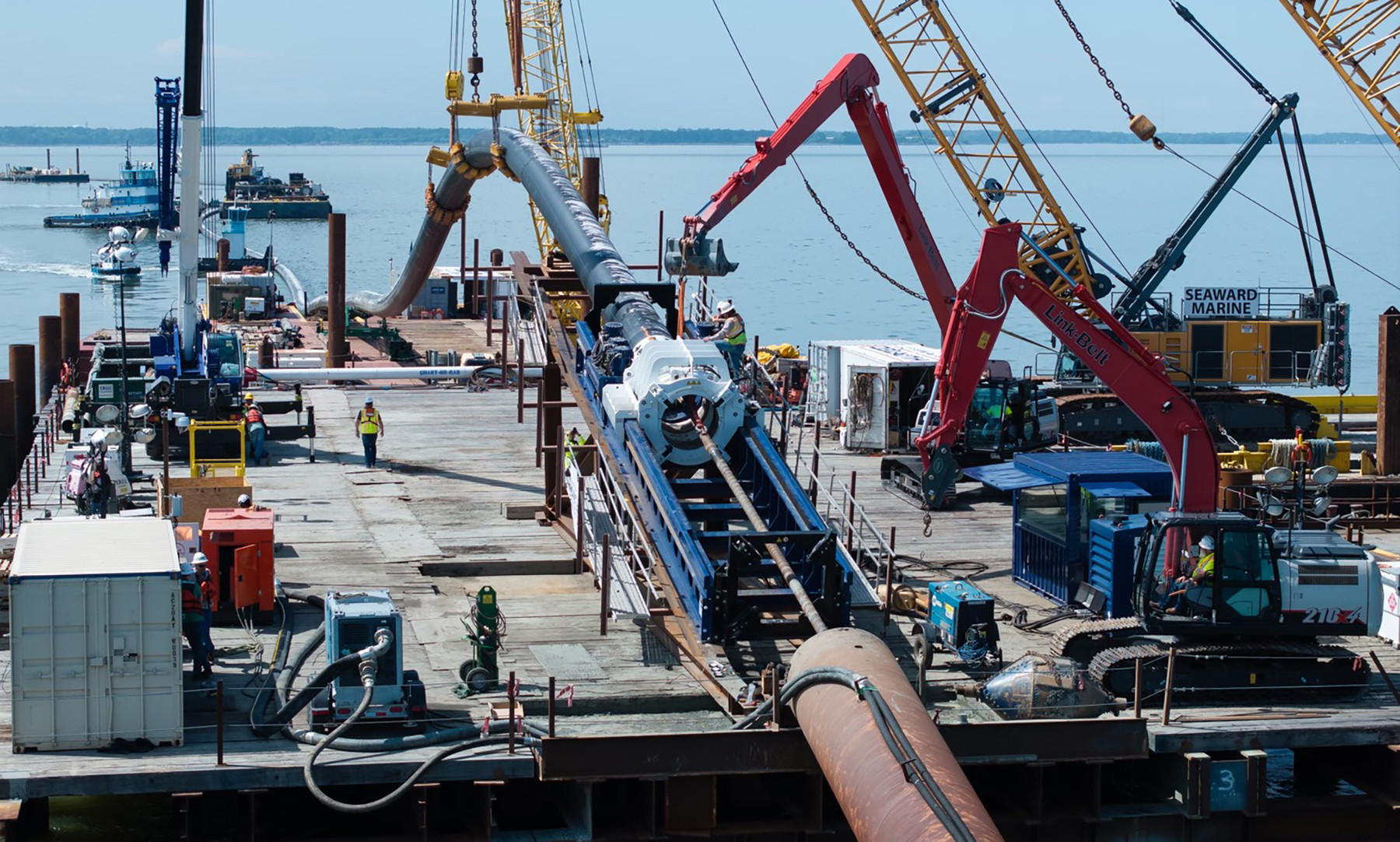
By Paul Longo, P.E., Associate DBIA, and Mark Peters, Associate DBIA
The James River Crossing project in Virginia represents more than a critical infrastructure investment that happened to set a world record.
It is also crucial to the Hampton Roads Sanitation District’s Sustainable Water Initiative for Tomorrow program, which is known as SWIFT and is designed to replenish groundwater resources and protect the Chesapeake Bay ecosystem. The project involved the installation of a nearly 5,700-foot-long force main beneath the Newport News shipping channel to convey wastewater from Newport News to the Nansemond Treatment Plant in Suffolk.
Further reading:
- If the Earth moves, this flexible iron pipe moves too
- $40 million aquatic habitat restoration in Seattle provides a home for salmon
- A California wastewater treatment plant is on track to generate its own power
In addition to its environmental significance, the project is a remarkable engineering achievement, setting a world record for the longest pullback of a 42-inch-diameter high-density polyethylene pipe using horizontal directional drilling.
A trenchless construction method that involves drilling a tunnel underground to install a pipeline or other utility, HDD was the preferred solution because it would not impede Navy and cargo shipping traffic in one of America’s busiest ports. To construct the project, HRSD selected the design-build team of Garney Construction and Dewberry, with Garney as the lead contractor and Dewberry as the design engineer. Huxted Trenchless, a specialist in HDD, was brought in to execute the drilling operations, using guidance and monitoring technology provided by Brownline USA. Brierley Associates was retained for geotechnical services during HDD work.
The project plays an integral role in supporting the goals of SWIFT, which is an innovative advanced water treatment project in eastern Virginia that further protects the region’s environment, enhances the sustainability of the region’s long-term groundwater supply, and helps address environmental pressures such as Chesapeake Bay restoration, sea-level rise, and saltwater intrusion.
SWIFT takes highly treated water that would otherwise be discharged into the James River and puts it through additional rounds of advanced water treatment to meet drinking water quality standards. SWIFT water is then added to the Potomac aquifer system, the primary source of groundwater throughout eastern Virginia.
Trenchless preparations
To facilitate HDD operations, the James River Crossing team built a large platform in the river, constructed using 36-inch steel piles driven deep into the riverbed. The platform serves as one of two entry points for the force main. The other was built on the north shore of the river.
Originally, the project plan included a second platform in the water. However, the project team devised a solution to remove that platform and extend the length of the pipeline by 2,500 feet, creating a land-to-sea connection. This adjustment not only reduced environmental impacts and disruptions to nearby marine terminals, but also achieved project cost savings of over $10 million.
At both entry points, 66-inch steel pipes were driven approximately 600 feet into the ground to secure the borehole entries. The conductor casing at the river platform provides stability within the loose river bottom soil and prevents inadvertent returns of bentonite slurry into the water. Injected into the tunnel during the HDD process, the slurry creates integrity for the tunnel and prevents it from collapsing under the weight of the riverbed.
Critical intersect
Given the tunnel’s length, the required tolerances, and the operational constraints of the drills, the project team employed a specialized version of HDD known as the intersect method. This approach involved two drills starting at opposite ends, 5,700 feet apart. Each drill created its own pilot hole, eventually meeting nose-to-nose deep underground to form a continuous bore path.
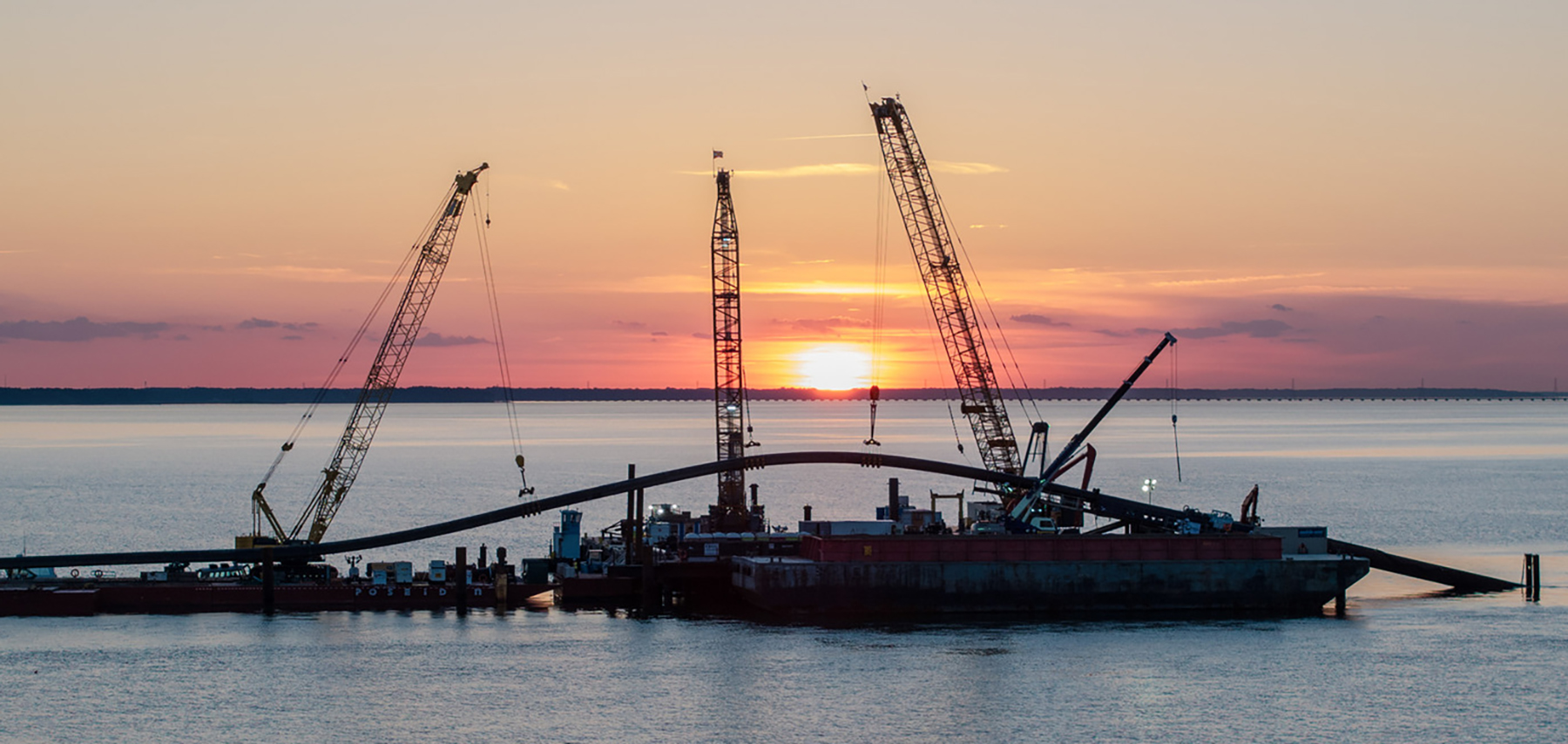
The drill heads were equipped with a Brownline USA Drillguide Gyro Steering Tool, which provided continuous measurements of the drill head’s position. Real-time positional data was combined with the drilled length to calculate displacement, allowing the drill heads to be guided along their intended routes. Brownline’s Pressure-While-Drilling module monitored annular pressure throughout the pilot drilling process to avoid inadvertent returns beneath the riverbed.
As the drill heads approached each other, Brownline’s radar system measured the relative distance between them. This enabled Huxted to adjust the drill heads’ trajectories so they intersected at the optimal point – 100 feet below the riverbed.
Installing over a mile of continuous pipe
If the drilling involved extreme accuracy, the nearly 5,700-foot-long force main installation was an exercise in logistics, coordination, and precision machinery. Once preparations were complete, a series of barges towed the HDPE pipe from its location on the south shore, navigating 3.5 miles across the James River to the platform.
To counter the river’s strong currents, barges were strategically stationed every 1,000 feet along the pipe’s length to stabilize it in the flowing water. Upon reaching the platform, the pipe was carefully maneuvered using crane cradles and rollers, guiding it to a custom-built pipe pusher machine directly above the 66-inch steel casing entry point. The first 150 feet of pipe was directed into the conductor casing.
Meanwhile, from the north shore, the drill rig had extended a continuous length of drill stem through the tunnel to connect with a pull head attached to the pipe. The drill stem is composed of 31-foot-long segments, linked end to end. As the pullback operation began, the first section of the force main was pulled 31 feet into the tunnel. The drill stem was then disconnected, attached to the next section, and the process repeated, systematically advancing the pipe.
The biggest risk with HDPE pipe relates to its safe allowable pull force. HDPE is like bubble gum in that it can stretch under significant force. At pull force levels of 600,000-700,000 pounds, it can eventually break. This is where the pipe pusher came into play. Designed in Germany specifically for the pipe’s dimensions, the machine was engaged when the pull force from the drill rig became too high. Using a clamp to grasp the pipe and move it forward, the pipe pusher acts to relieve the pulling force tension on the HDPE, mitigating the risk of overstressing the pipe and ensuring it remained below its critical breaking point.
Construction officially began in September 2023, starting with work on the north shore portion. The project team completed the record-breaking pipe installation on May 2 after nearly 24 hours of continuous pipe pullback operations.
Remaining tasks and lessons learned
Further work remains to extend the pipeline another 3.5 miles to the south shore of the James River, which will be accomplished using a marine open cut installation. Additionally, a new pump station will be constructed on the north shore, and the Nansemond Treatment Plant will be upgraded and expanded to increase capacity and enhance nutrient removal.
The key to executing a project of this complexity – and overcoming the extensive technical challenges it presented – was the project team’s ability to collaborate and engage effectively. Success at every stage depended on meticulous coordination, sequencing, and timing, making the design-build approach essential for a cohesive and integrated planning process.
The project team included industry leaders and world-renowned HDD experts, but what truly made a difference was bringing everyone together in workshops to generate ideas, listen to concerns, and operate as a unified team to solve challenges.