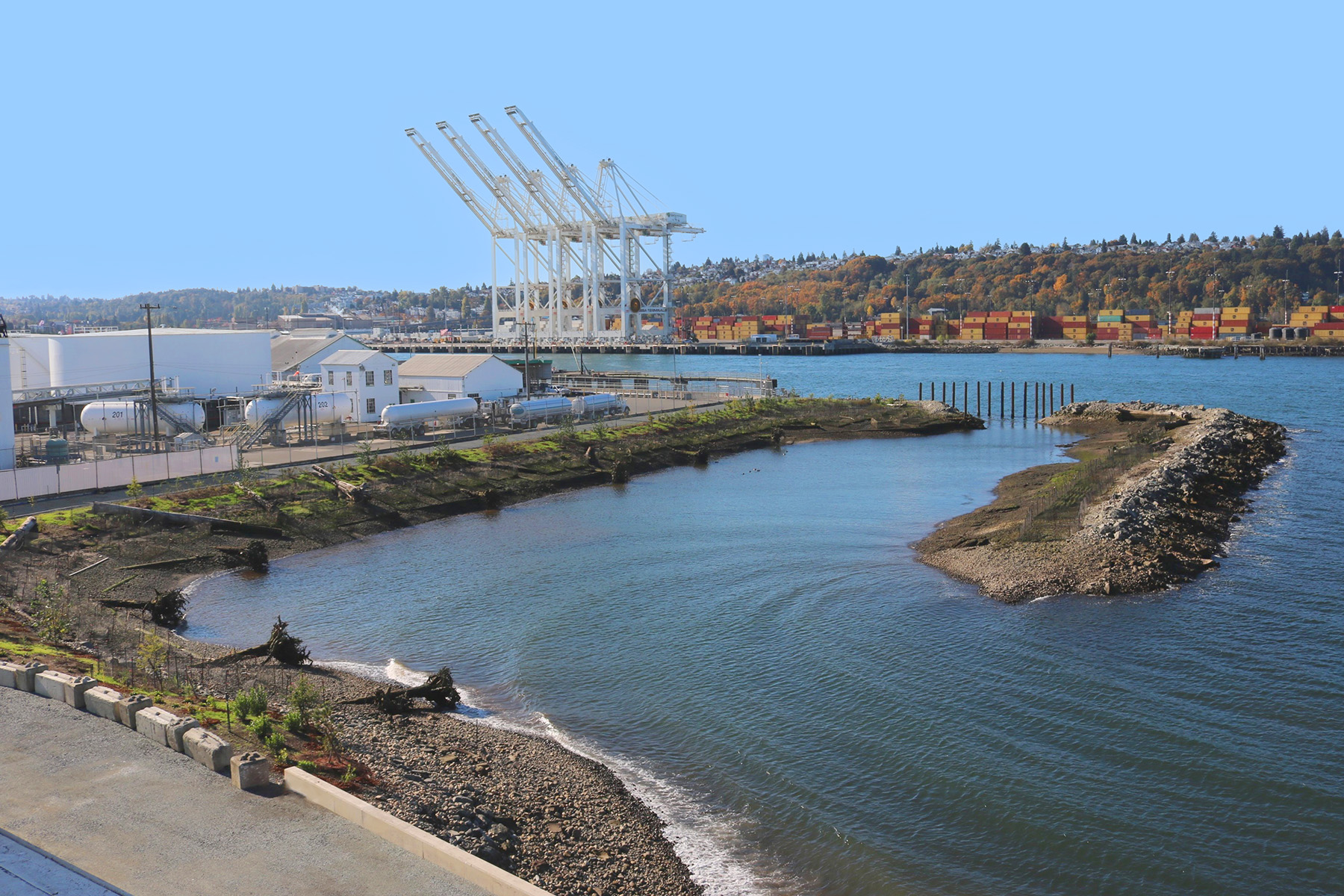
By Kate Snider, P.E., Scott Stainer, P.E., M.ASCE, and Johnathan Cook, P.E.
Vigor Shipyards has completed a 3-acre aquatic habitat restoration at its Harbor Island facility in Seattle. The $40 million project reintroduces a vital salmon habitat to an industrial waterfront and will serve as a blueprint for future efforts to boost marine habitats in urban estuaries.
Building an island
For millennia, the rich and healthy ecosystem of Washington state’s Duwamish River provided a refuge for salmon. Mudflats and marshes were their predominant habitats, and these areas were fished and cultivated by the Indigenous communities who resided along the waterfront. Eventually, however, settlers came to the area in the mid-1800s and quickly began to sculpt the land to suit their own needs, adjusting the flow of the river to facilitate a growing marine industry.
These large-scale civil engineering endeavors included building Harbor Island atop historical tide flats at the mouth of the Duwamish, a project that was completed in 1909. Dredge spoils from the construction of the river’s East and West waterways as well upland soil that was removed via sluice during the regrading of Seattle were used to create this 350-acre artificial island. The majority of these loosely placed spoils comprised silts and sands deposited by the river over the centuries.

Harbor Island has supported industrial uses since its creation, including shipbuilding and repair, bulk petroleum storage and transfers, cargo handling, smelting operations, and metal recycling and fabrication. The island and the surrounding marine transport facilities are now considered a major hub in the Pacific Northwest maritime industry.
Todd Pacific Shipyards (now Vigor Shipyards) was established on Harbor Island in 1916. Todd was instrumental in shipbuilding and repair of commercial and military vessels for the Klondike Gold Rush and World Wars I and II. As the business expanded, the shipyard acquired additional acreage on the island, including property previously used for petroleum storage. Today, Vigor provides new construction, repair, maintenance, overhaul, and conversion of commercial and military vessels. The shipyard consists of approximately 27 acres of land and 20 acres of open-water area at the northwest corner of the island, where the Duwamish River enters Elliott Bay.
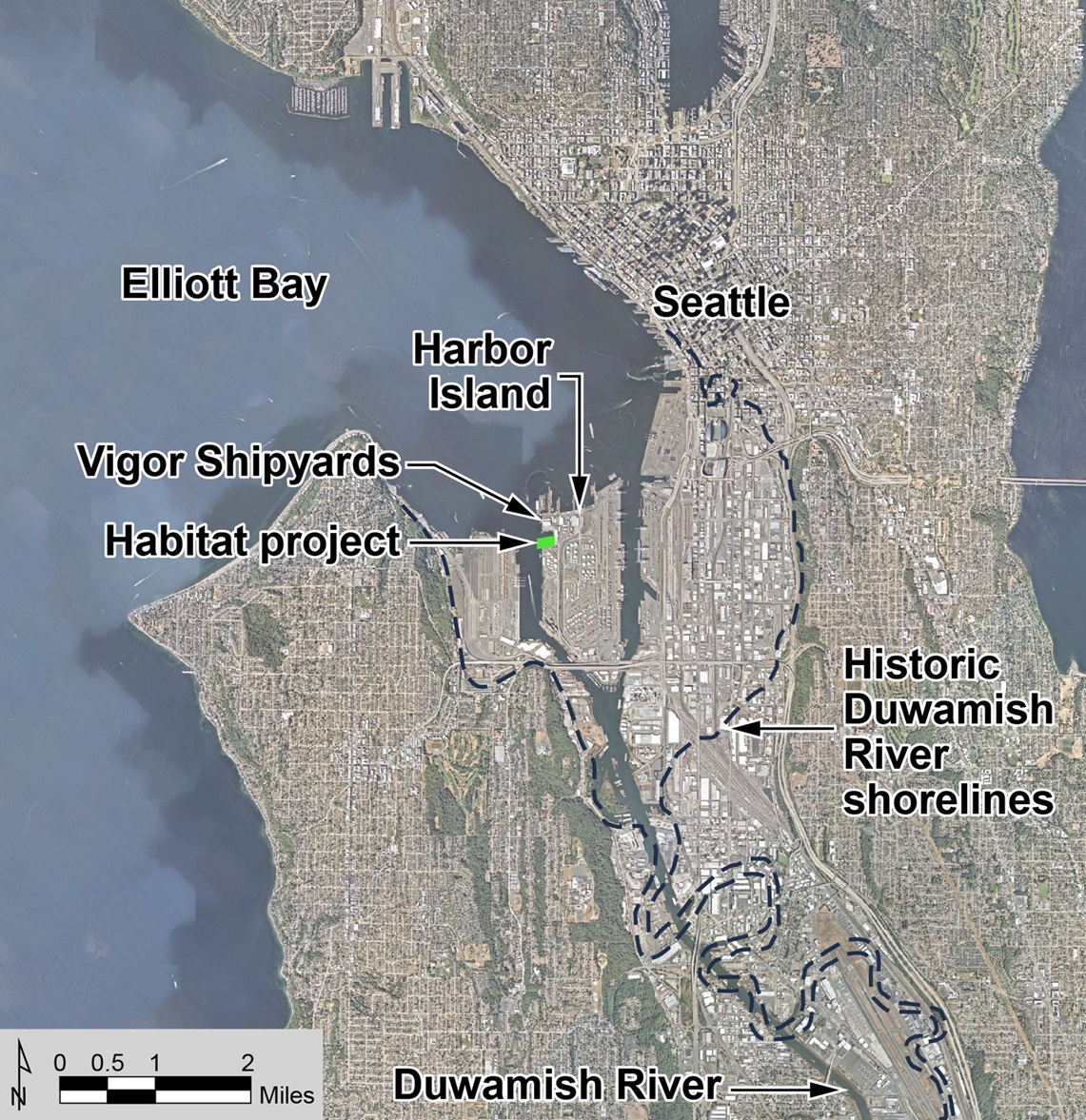
The facility and adjacent sediments are defined as the Todd Shipyard Sediments Operable Unit of the Harbor Island Superfund Site. Between 2004 and 2007, Todd performed remedial action at the facility in accordance with a Comprehensive Environmental Response, Compensation, and Liability Act consent decree that required dredging 32 acres of contaminated sediment in the open-water area and placing temporary sand caps beneath the facility’s five piers, where dredging was not possible. Superfund cleanup also included removal of oils from upland soil and groundwater associated with historical tank farms where petroleum was stored.
Inherited liability
Vigor acquired Todd in 2011, assuming the remaining liability for historical releases of contamination from the property into Elliott Bay and the Duwamish River. Upon acquiring the facility, Vigor evaluated several options for settling the Natural Resource Damages liability under CERCLA, including either direct monetary payment to the supervising agencies, off-site habitat construction, or on-site habitat construction.
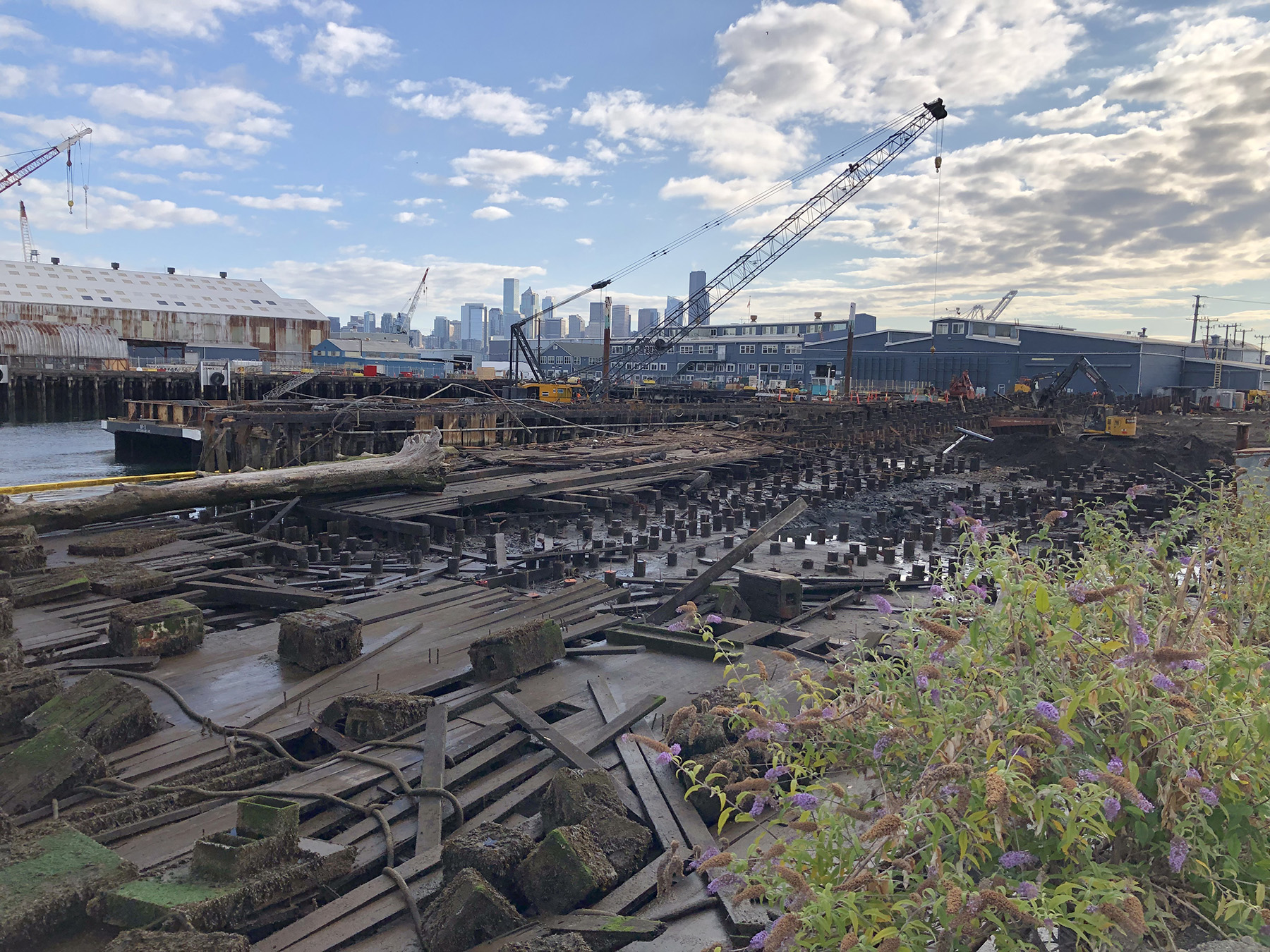
In April 2021, Vigor, along with ExxonMobil (as prior owner of portions of the property), entered into a consent decree with federal agencies and local tribal governments (the Natural Resource Trustees). The negotiated settlement required Vigor to demolish some of its shipyard infrastructure and convert approximately 10% of the active facility to a new aquatic habitat for juvenile salmonids.
Natural Resource Trustees were deeply involved in the development of the project, from conceptualization to monitoring plans. The trustees include the Muckleshoot Indian Tribe, the National Oceanic and Atmospheric Administration, the Suquamish Indian Tribe of the Port Madison Reservation, the state of Washington, and the U.S. Department of the Interior. Vigor also partnered with Seattle-based salmon restoration nonprofit Long Live the Kings and the University of Washington to perform pre- and post-construction fish surveys.
From industrial environment to vibrant habitat
Creating a viable habitat within a Superfund site was no small feat. There is very limited existing intertidal habitat along this reach of the Duwamish River as it flows into the bay. The end goal was for the refuge to resemble and function like the tidal flats had before the island was created and altered to suit industrial purposes.
The project team determined placing the habitat at the southwest corner of the shipyard was the most effective location financially and environmentally. This corner of the facility was the site of WWI-era timber shipways — a pile-supported sloped work surface on which ships were constructed and then easily launched from. Due to the condition of the historical structure and advancements in shipbuilding technology, the timber shipways were no longer in use.
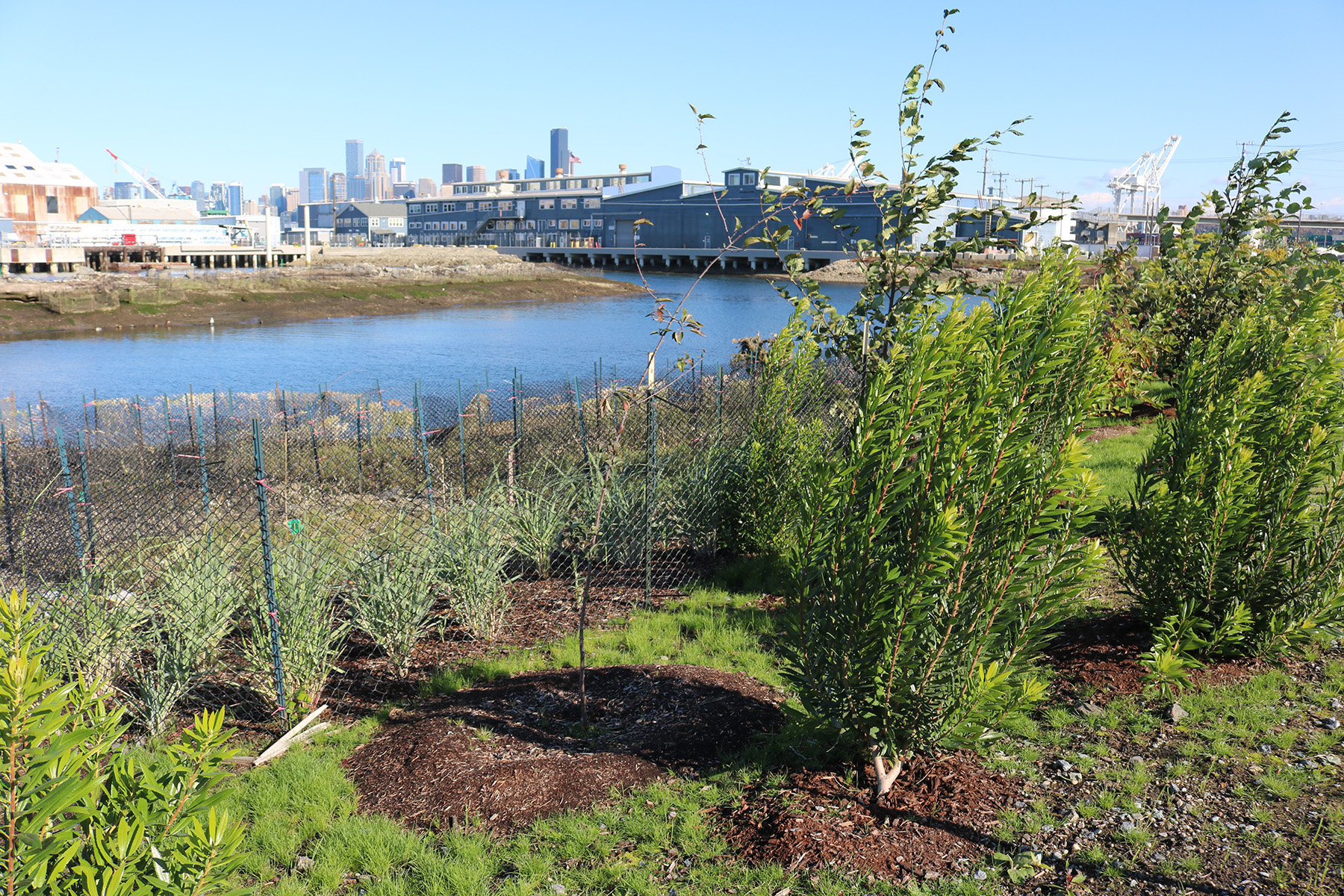
Between 2017 and 2021, Vigor and the consultant team collaborated with the Natural Resource Trustees on final design, acquiring project permits from the U.S. Army Corps of Engineers, the Washington Department of Fish and Wildlife, and the city of Seattle. The consultant team was a partnership between Seattle-based Floyd|Snider, an environmental consulting firm, and KPFF Consulting Engineers, with support from J.A. Brennan Associates PLLC (landscape architect), PanGEO Inc. (geotechnical), and Elcon Associates (electrical).
Vigor engaged Orion Marine Group as the general contractor under a cost-plus-incentive-fee contract, which enabled the contractor, owner, and engineer to work as a team. The benefit of this type of arrangement was that the contractor did not assume the risks of a lump sum contract and was incentivized to find ways to construct the project for less cost without sacrificing quality. This was especially powerful for an in-water construction contract like this one where there were many risks and uncertainties. UMC and Veca Electric & Technologies were key Orion subcontractors.
Vigor also entered into agreements with the Muckleshoot Indian Tribe and the Suquamish Indian Tribe of the Port Madison Reservation to take measures to minimize disruption to tribal fishing and financially compensate the tribes for any disruptions during construction.
Construction began in May 2021 with demolition of three piers and the timber shipways as well as excavation of upland contaminated soil. Approximately 5,000 piles that had been treated with creosote, a toxic wood preservative, were fully extracted and disposed of as part of demolition — providing a significant environmental benefit.
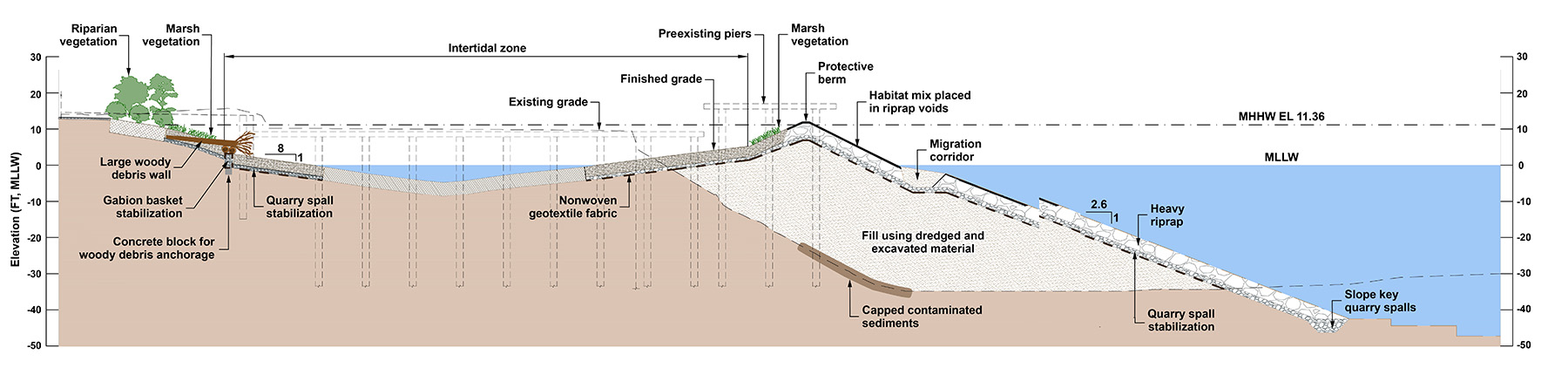
After pier removal, more than 7,000 cu yd of contaminated sediments below the western end of the shipways was dredged and then transloaded off-site for disposal at a permitted landfill for nonhazardous waste. Clean fill material placed as part of habitat slope construction serves as an Environmental Protection Agency-approved environmental cap for some contaminated sediments remaining in place.
After the contaminated sediments were removed, construction shifted to creating the habitat area, which was designed to optimize a new intertidal mudflat area with new adjacent marsh and riparian vegetation, creating the conditions essential for a juvenile salmonid refuge. Habitat construction required building up an extensive underwater embankment on the north and west sides of the habitat. Approximately 40,000 cu yd of clean sediment was dredged from the adjacent basin. This sediment was combined with approximately 20,000 cu yd of clean soil from the adjacent upland area and 5,000 cu yd of imported material.
Construction of an underwater embankment using dredged material is not done often and is extremely tricky. The Washington Department of Fish and Wildlife allows for a six-month construction window between September and February, the time period when the young salmon are not migrating. To accommodate this timeline, Orion worked around the clock to dredge and place the material, often in darkness using instrumented equipment.
The embankment slope was stabilized with rock armor as it was built up underwater. The embankment created a perched intertidal zone that maximizes the critical elevations (between -2 ft and +6 ft mean lower low water) for juvenile salmonid and an optimal amount of adjacent marsh (+6 ft to +12 ft MLLW) and riparian zones (+12 ft to + 15 ft). The embankment abuts the federal navigation channel within the Duwamish River that is maintained at a depth of -60 ft to support commercial navigation.
Due to the large wind fetch that that comes across Puget Sound into Elliott Bay, the project team employed innovative slope construction methods for the habitat embankment and adjacent shipyard shorelines. Imported heavy riprap, quarry spall bedding, and underlying geogrid were placed on the surface of the fill as armor to stabilize the exterior slope, with a protective riprap berm placed at the top of the slope to reduce potential impacts to the habitat area from wave action. The design included multiple openings to the off-channel habitat area in the perimeter berm to encourage fish passage.
Throughout the new habitat area, crews deposited a 4 ft thick layer of imported substrates consisting of rounded gravels of varying grain sizes mixed with organic topsoil. These habitat substrates were selected to create optimal conditions for the growth of algae and plants important to the salmon refuge. Since placement, algae and kelp have established quickly throughout the area. In addition, the team added rounded gravels to fill voids within the riprap slope, eliminating hiding places for predatory fish species.
To stabilize steepened slopes in an area with poor soil conditions typical to Harbor Island and assist in restricting lateral spreading during earthquake events, untreated timber pinch piles were installed as a stability measure. These piles are below the mudline of the slope in the steeper areas along the disturbed shipyard shoreline.
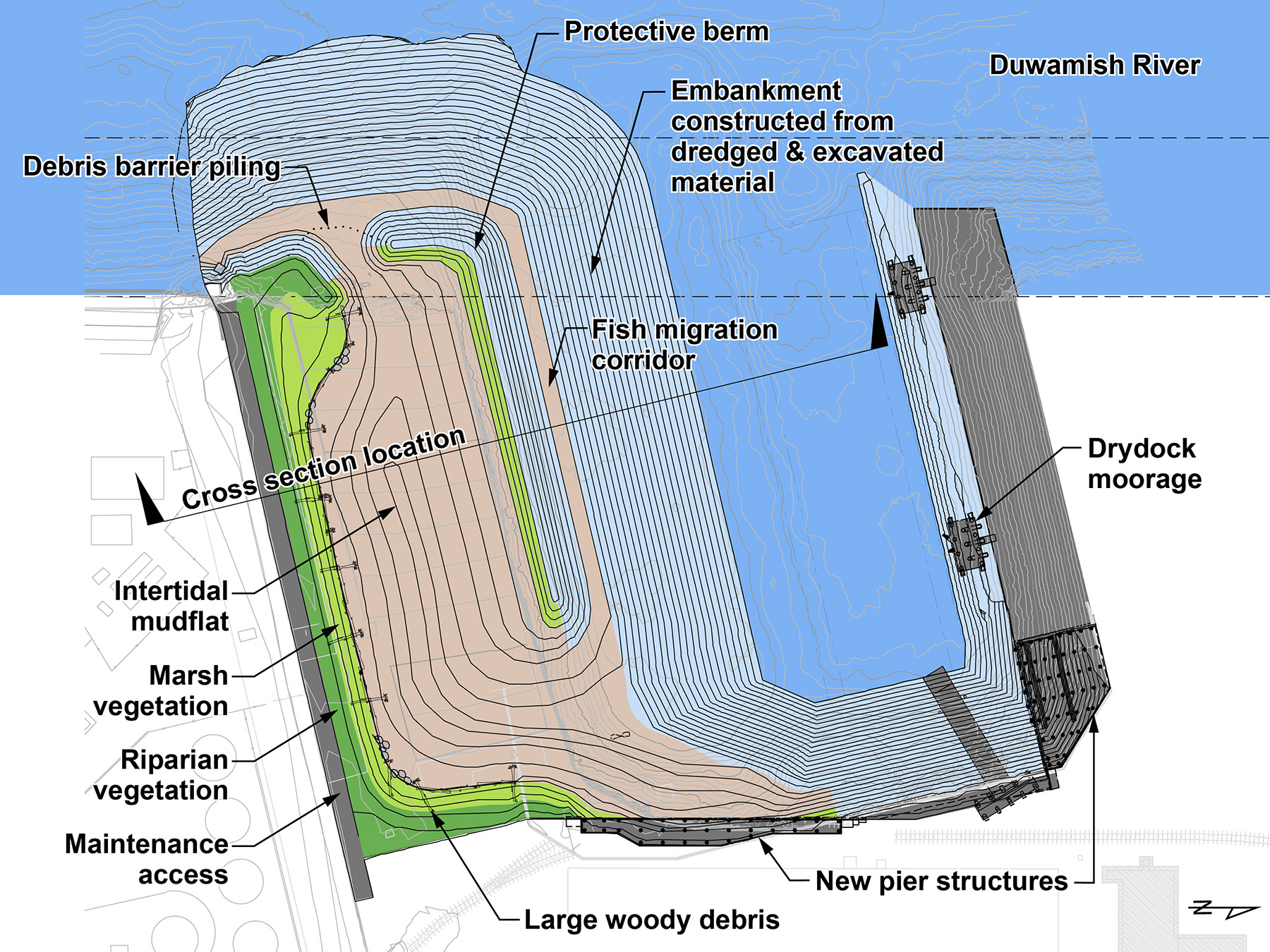
Within the habitat, crews built an approximately 3 ft high log wall to transition from mudflat elevations (-2 ft to +3 ft MLLW) to vegetated marsh and riparian elevations (+6 ft to +15 ft). In addition to their use in the wall, large logs, many with root wads still attached, were anchored to subsurface concrete blocks placed throughout the new marsh area. Biologists and natural resource agencies term this “large woody debris,” which adds desirable habitat complexity and shading to the near-shore aquatic environment.
Additionally, the habitat includes a migration corridor immediately offshore of the protective berm to facilitate fish migration into and out of the habitat area. A debris barrier consisting of 24 composite plastic piles crosses the opening between the habitat and the Duwamish River to protect the habitat from damage caused by floating debris while still enabling unimpeded fish passage.
The marsh and riparian buffer areas were planted with native vegetation that could tolerate saline conditions unique to this environment, including coniferous and deciduous trees, shrubs, herbaceous plants, and salt marsh plants. Their selections were based on evaluation of similar estuaries in Puget Sound, and the plantings will be adaptively managed during the maintenance and monitoring periods. A new irrigation system within the riparian area is helping the vegetation take hold and grow.
A common issue on multiple sites along the Duwamish is the destruction of emergent habitat plantings due to the large numbers of Canada geese grazing on them. This overpopulation is a result of purposeful relocation of the geese to Puget Sound in 1968 during dam construction on the Columbia River. To protect the young vegetation, exclusion fencing has been installed, prohibiting goose access.
As part of this project, piers directly adjacent to the new habitat area were rebuilt to support necessary shipyard access and address deterioration. Additionally, workers built a new dry dock moorage system and dry dock access ramps.
The project team also built a stormwater treatment system that conveys all stormwater from industrially active areas of the shipyard to a central treatment location. The new chitosan-enhanced sand filtration system treats stormwater flows from the project area and the remainder of the Vigor facility before discharging to the Duwamish’s West Waterway. This system protects the new habitat from the potential impacts of industrial stormwater runoff.
A fresh start
Construction of the earthworks finished in March 2023 and the plantings in May. Within weeks, juvenile salmon were occupying the new habitat.
With completion of this project, Vigor has become the permanent steward to a vital piece of salmon habitat in the Green River-Duwamish Watershed. In total, 1.5 acres of existing overwater coverage (the piers and shipways) were removed, and 1.5 acres of existing upland area were converted to intertidal habitat area.
Vigor and the trustees agreed to seasonal restrictions on shipyard vessel operations within the open-water area immediately adjacent to the new habitat to lessen impact to migrating salmon. To ensure the long-term success of the habitat, the project will be protected in perpetuity via a Washington State Department of Natural Resources conservation easement on the portions of the project on state-owned aquatic land and deed restrictions on the Vigor-owned property.
For 10 years post-construction, Vigor will employ adaptive management actions to monitor and maintain the habitat and ensure that the restoration project meets the trustees’ objectives. Vigor will also perform annual monitoring to assess intertidal habitat area integrity, material stability, tidal circulation, sediment and soil structure, and elevation and channel morphology.
The company will also perform biological and chemical monitoring to evaluate growth of tidal marsh and riparian vegetation, confirm fish presence, and assess benthic community development and potential contamination of the habitat substrates.
This project fully integrated objectives for a viable aquatic habitat, environmental cleanup, and industrial facility upgrades. For the authors, it has been the experience of a lifetime to take this project from conceptual alternatives analysis through construction completion. The results provide a substantial benefit to the Puget Sound ecosystem and demonstrate the potential of industrial-ecological integration.
Kate Snider, P.E., is founder and principal at Floyd|Snider in Seattle. Scott Stainer, P.E., M.ASCE, is an associate in special projects at KPFF Consulting Engineers in Seattle. Johnathan Cook, P.E., is the civil engineering project manager at Vigor Shipyards in Seattle.
Project credits
Owner
Vigor Shipyards, Seattle
Habitat design, project management, permitting, and construction management
Floyd|Snider, Seattle
Civil, structural, and mechanical engineering and construction management
KPFF Consulting Engineers, Seattle
Geotechnical
PanGEO Inc., Seattle
Landscape architecture
J.A. Brennan Associates PLLC, Seattle
Electrical engineering
Elcon Associates, Seattle
General contractor
Orion Marine Group, Tacoma, Washington
Mechanical contractor
UMC, Lynnwood, Washington
Electrical contractor
VECA Electric & Technologies, Seattle
Landscape contractor
Out West Landscape, Deer Park, Washington
This article first appeared in the March/April 2024 print issue of Civil Engineering as “Industrial Refuge.”