Claim Reduction is a monthly series by the ASCE Committee on Claims Reduction and Management designed to help engineers learn from problems that others have encountered.
Whenever a claim against an engineer goes to trial, valuable lessons can be learned. The following case study has two key takeaways:
- Treat underground plastic stormwater detention systems with caution.
- Your professional responsibilities when specifying engineered products.
This article discusses the first lesson, with the other to be covered in a second part.
Manufacturers and distributors often promote plastic stormwater detention systems in below-grade applications to civil engineers. These systems appear to be a cost-effective approach to stormwater detention, often located beneath parking lots. However, several have failed, including the one described here.
In this case, expert testimony identified several causes for the failure. However, a key factor was largely overlooked – the structural behavior of plastics, an aspect many civil engineers might not consider when designing or specifying plastic stormwater detention systems.
Background
A civil engineer contracted directly with a church for services to include designing an on-site stormwater management system. The site required stormwater detention of approximately 26,000 cubic feet. It was decided to place the detention system below a 94,500-square-foot surface parking lot. The solution selected was a plastic [polypropylene] tank system composed of individual plastic boxes, each measuring 16 inches wide, 18 inches high, and 27 inches long, with a capacity to detain 4.2 cubic feet of water.
The design arranged these boxes in a rectangular pattern in two layers, covering an area of 124 feet by 78 feet. The contract documents specified the use of the tank system by incorporating the manufacturer’s prescriptive specifications and installation methods. The tank system would be buried beneath up to 9½ feet of soil, which is deeper than the engineer’s previous applications of the system but, importantly, within the upper range of the burial depth reported in the manufacturer’s literature.
It’s worth noting that the civil engineer had used the same stormwater detention system on other projects, all without incident.
Construction
The design was completed and permitted, and the church hired a general contractor to perform construction. Construction inspection was assigned to a third party under contract with the owner. The civil engineer did not observe the tank placement and was not under contract to monitor construction.
The failure
The first sign of a problem could be seen when the parking lot above the tanks began to settle, indicating a failure of the plastic tanks to support the overburden. This failure occurred four months after the overburden was placed, raising the question: why didn’t the tanks fail when initially loaded?
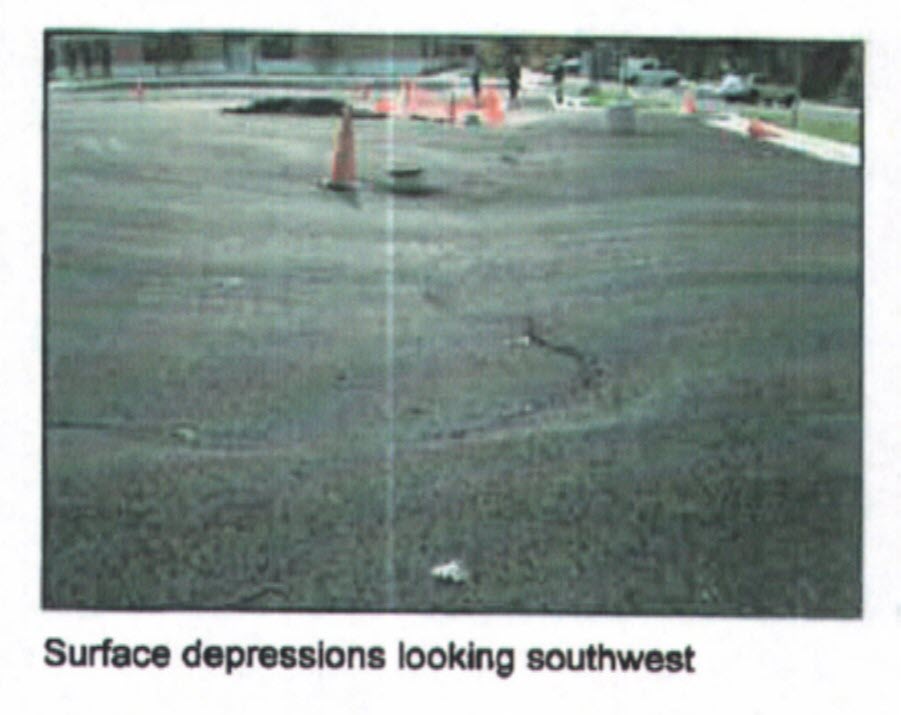
Thermoplastic creep
Not widely recognized in civil engineering, thermoplastic polymers are susceptible to deformation over time, known as creep, under load. Materials like polypropylene and other plastics experience creep, meaning they permanently deform over time when subjected to constant stress, even if the stress is below the material’s yield limit.
The fundamental problem is not that the compression member shortens; creep diminishes its buckling resistance. A small irregular compression load on the plastic box will result in out-of-plane deflection, which will continue to increase until the sides of the box buckle. This is the familiar P-delta effect, explaining the church project's failure four months after its completion.
Strength data in the tank manufacturer’s literature did not address creep potential other than a note that creep after 90 days should be 0.40%. The literature does not provide allowable construction tolerances for the tanks, nor does it discuss the exacerbating effect of irregular loading on tank performance. It offers nothing on how due to creep, buckling resistance, and the compressive and shear strengths of thermoplastic materials decrease as the duration of loading increases. Thus, a tank loaded for four months under field conditions is not as strong as a tank loaded for minutes or hours under ideal conditions in a laboratory.
Ultraviolet light exposure is also known to degrade thermoplastics, which lose strength when exposed to sunlight. Therefore, when handling these products, they should be protected from sunlight.
Repeating failures
This failure is not isolated; similar issues have occurred before and will likely continue. Other examples include:
- Triangle Realty Mall, North Attleboro, Massachusetts
- Fluvanna School, Palmyra, Virginia
- Tanger Outlets Mall Parking Garage, Lancaster, Pennsylvania
In summary
Sharing this story will raise awareness of the potential challenges in designing projects with thermoplastics. The Committee on Claims Reduction and Management is not discouraging plastic detention systems, only encouraging engineers to pay more attention to the design and specification of thermoplastic products.
If the makers and promoters of such products could provide more comprehensive and higher-quality technical information, these products would be used more effectively and with a reduced risk of failure.
Read more about this case study, including a breakdown of the second key lesson learned: the engineer's responsibility when specifying engineered products.
John Godwin Tawresey, S.E., F.SEI, FTMS, Dist.M.ASCE, has 52 years of experience as a structural engineer. As chief financial officer of KPFF Consulting Engineers for 35 years, he was responsible for the firm’s risk management education program.