By Sarah Derouin, Ph.D.
The remnants of Roman architecture still litter the landscape in Europe and the Middle East. Concrete buildings and infrastructure have survived for centuries, withstanding the natural erosional forces of rain, ocean waves, and seasonal freezing.
This staying power of Roman infrastructure caught the eye of researchers from the Massachusetts Institute of Technology.
“Roman concrete is a fascinating material,” says Admir Masic, Ph.D., an associate professor who specializes in the science-enabled engineering of sustainable construction materials in the civil and environmental engineering department at MIT. “The material is there in the sea for centuries and millennia — you don’t need to be a civil engineer or material scientist to be impressed by walking on the beach and finding these blocks of ancient Roman Harbor that are still close to being intact.”
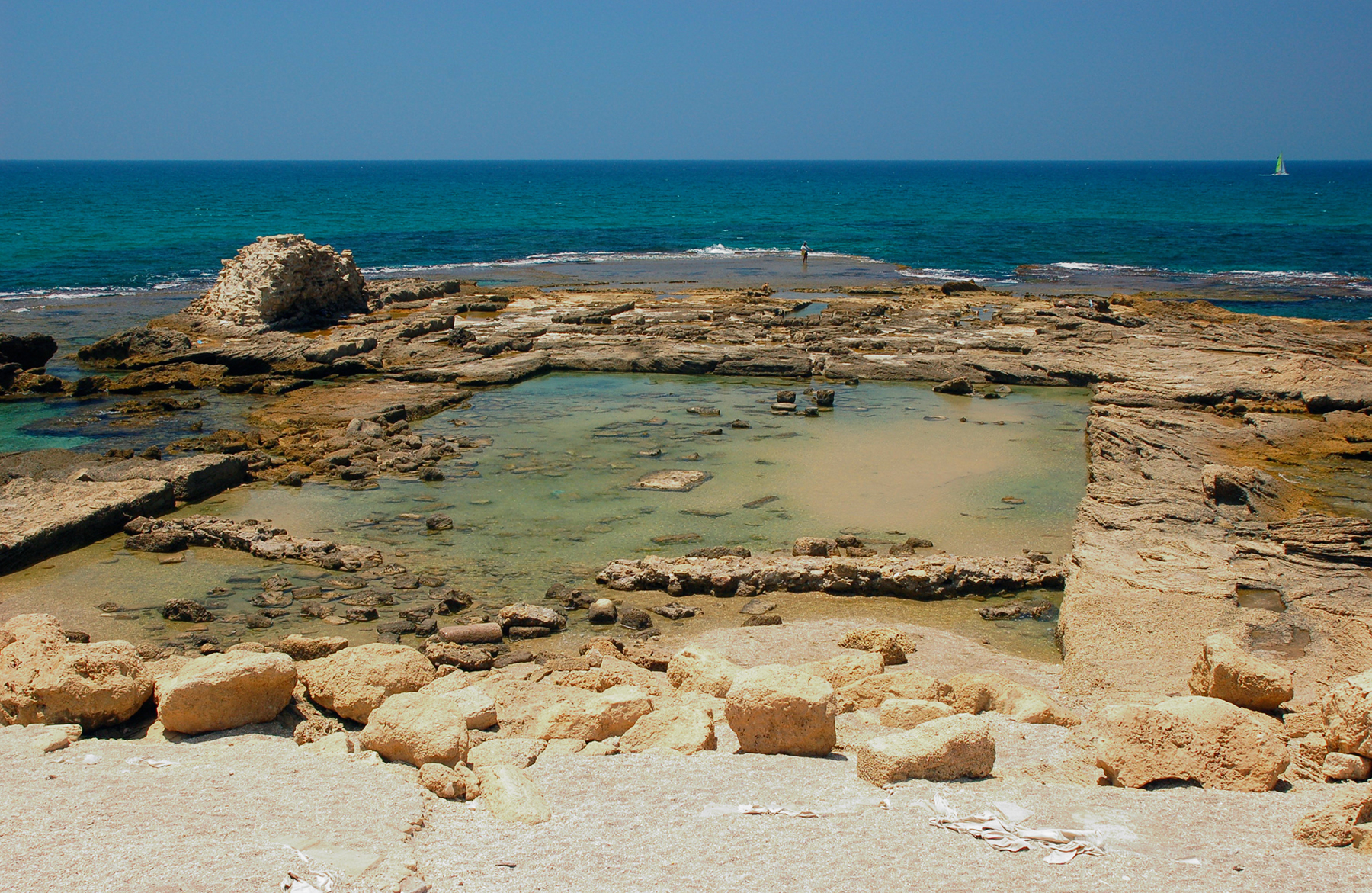
In a new paper in Science Advances, Masic and his colleagues looked at what the composition of Roman concrete could reveal about longevity and material durability. Specifically, the team wanted to understand the reasons Roman concrete was so great at self-healing and if those properties could be translated into modern-day building practices.
Concrete’s practicality, pitfalls, and persistence
Concrete is the ubiquitous and versatile construction material of our time. From buildings to dams to bridge supports, concrete is the cornerstone — literally — of many modern-day structures.
For all the pluses of concrete, there are significant downsides to the material. Modern-day concrete contains ordinary portland cement, a compound that has significant environmental impacts. For each metric ton of OPC that is manufactured, up to 1 metric ton of carbon dioxide is also released. And that adds up — the authors of the paper note that globally, the concrete industry is responsible for up to 8% of greenhouse gas emissions.
One way to temper the emissions is to make longer-lasting material in the first place. Strong, self-healing concrete could cut down on repairs and replacement, lowering the total emissions released by lowering the amount of replacement cement that is needed to be produced.
Today, much of the concrete used in construction is reinforced and includes steel rebar within the structure. But the very thing that now strengthens concrete might be what also weakens the material in the long term. Masic explains that as water seeps into the pore spaces, it interacts with modern concrete and creates calcium hydroxide carbonates. “This carbonation lowers the pH around the rebar, rebar starts to corrode, and eventually expands and causes spalling,” he says. “Chlorides are really problematic.”
The quality of cement used in concrete can also greatly affect its longevity, says Masic. “In some countries, we have buildings tearing apart in 40 or 50 years. If you use higher-quality materials, we (can) guarantee 100-150 years, depending on which type of cement we use in concrete.” But even these longer-lasting, century-plus structures do not match the durability of Roman concrete.
Chemical composition is key
The researchers investigated the specific components of Roman concrete to try to uncover more about its characteristics. They took samples of concrete from archaeological sites, including the mausoleum of Cecilia Metella.
“Roman concrete (was made) using lime, volcanic aggregates, and volcanic ash,” Masic says. “The key ingredients are lime and volcanic ash. So why not test the role of lime?” Lime is easy to spot in Roman structures, showing up as white specks in the concrete. The researchers looked at the concrete under scanning electron microscopy, X-ray diffraction, and chemical spectroscopy and noted the lime was porous and transformed from calcium oxide to calcium hydroxide.
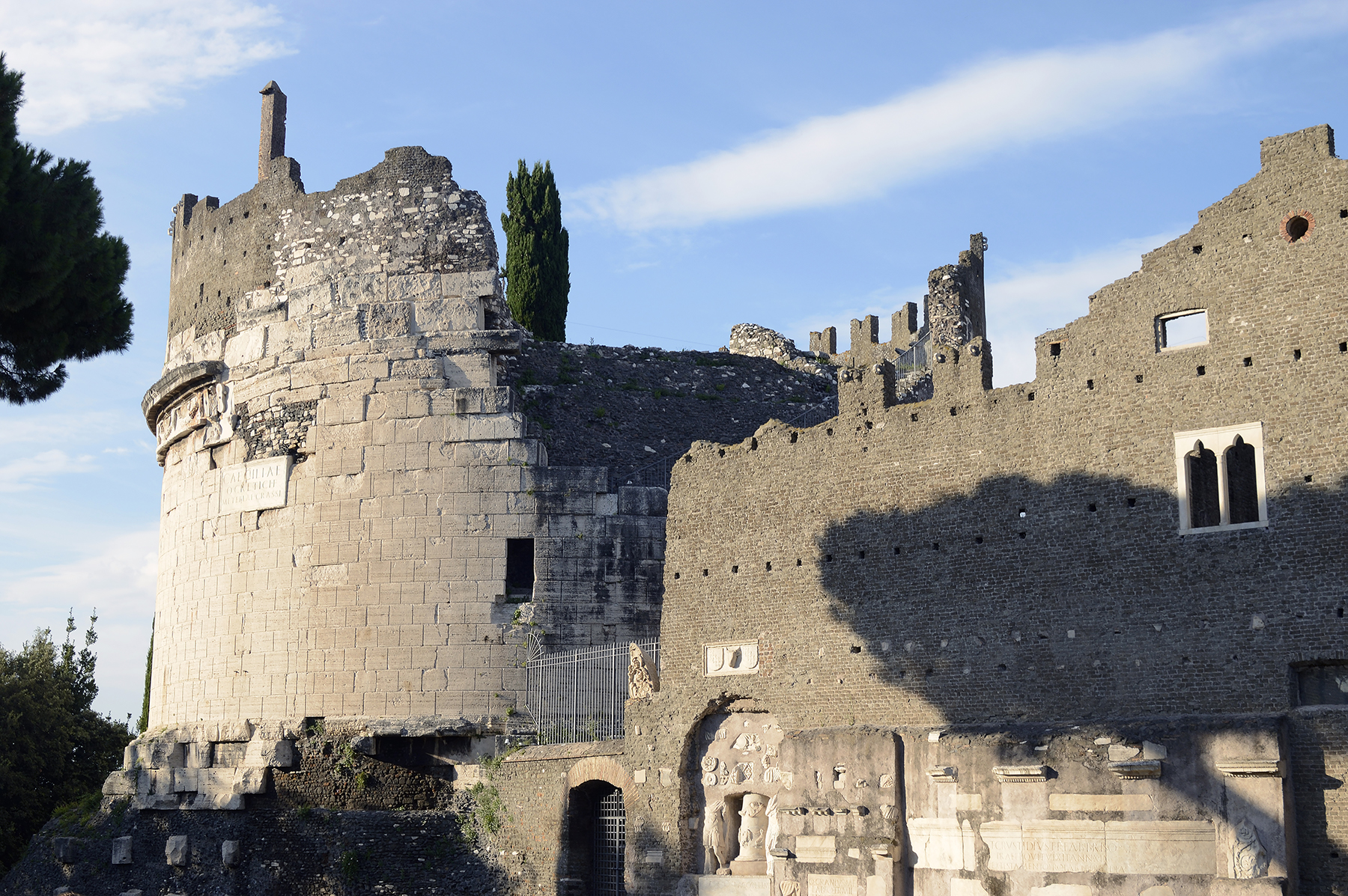
These morphological features and chemical aspects showed compelling evidence that quicklime was used in Roman concrete. “No one ever thought that Romans used hot mixing, because (famed Roman architect/engineer) Vitruvius suggests in his De Architectura to use slaked lime,” says Masic.
In a hot mix, quicklime, water, and aggregate are combined. Quicklime, a calcium oxide, is very reactive with water. When mixed, the water and quicklime produce an exothermic reaction. In contrast, slaked lime (calcium hydroxide) has already incorporated water into its structure and is nonreactive when mixed with water.
Using quicklime in the mortar of Roman concrete incorporates a source of reactive calcium that would be perfect for self-healing cracks. The researchers tested this theory by creating a modern, Roman-inspired concrete that used hot mixing preparations. They found that their mix was effective at healing induced cracks up to 0.5 mm wide.
“The paper provides strong evidence that Roman concrete was made by hot mixing,” says Lori Tunstall, Ph.D., an assistant professor in civil and environmental engineering and materials science at the Colorado School of Mines. While Tunstall was not involved in the research, she explains that an exothermic reaction would have occurred when the Romans included free lime (calcium oxide) into water to form the concrete mix.
“The whole process results in porous, reactive lime left within the concrete,” she says. “The increased porosity is significant because it means that when cracks are initiated within the concrete, they will tend to go through the lime clast since it's not very strong.”
Can old become new again?
The authors hope their results have implications for the longevity and climate impact of modern concrete structures. “If we managed to improve (the life span) through self-healing to extend concrete maybe 100 years — even a 50% life-span improvement would mean so much in terms of emissions and maintenance costs,” Masic says.
While concrete composition matters, Tunstall agrees with Masic that rebar is the main driver of concrete degradation in modern concrete structures. The Romans, on the other hand, “built massive structures all in compression, which is why their architecture utilizes so many arches,” explains Tunstall. “If we did this today, we might have more durable concrete, but we wouldn't be able to use it for all the applications we do today,” Tunstall says.
Forgoing modern reinforcements like rebar and designing structures with Roman design would mean more cement was needed — something that would, of course, increase cost and carbon emissions.
Tunstall also has also concerns with strength and longevity of relying on these carbonate clasts to seal cracks. “Calcium carbonate is better than cracks, but I think we can do better still,” she says.
This article first appeared in Civil Engineering Online.