By Sarah Derouin, Ph.D.
When talking about building materials, concrete is the most ubiquitous player worldwide. It is used in everything from dams to building foundations and is produced in staggering amounts. In 2022, the U.S. produced 95 million metric tons of cement — the key ingredient in concrete — and was ranked fourth in global production. (China took the first spot, producing 2.1 billion metric tons.)
“Concrete is the second-most widely consumed material in the world after water — and I like to tell people that water gets an unfair bump because we use it in concrete,” says Zachary Grasley, Ph.D., P.E. F.ASCE, a professor and the head of the Department of Civil & Environmental Engineering at Texas A&M University.
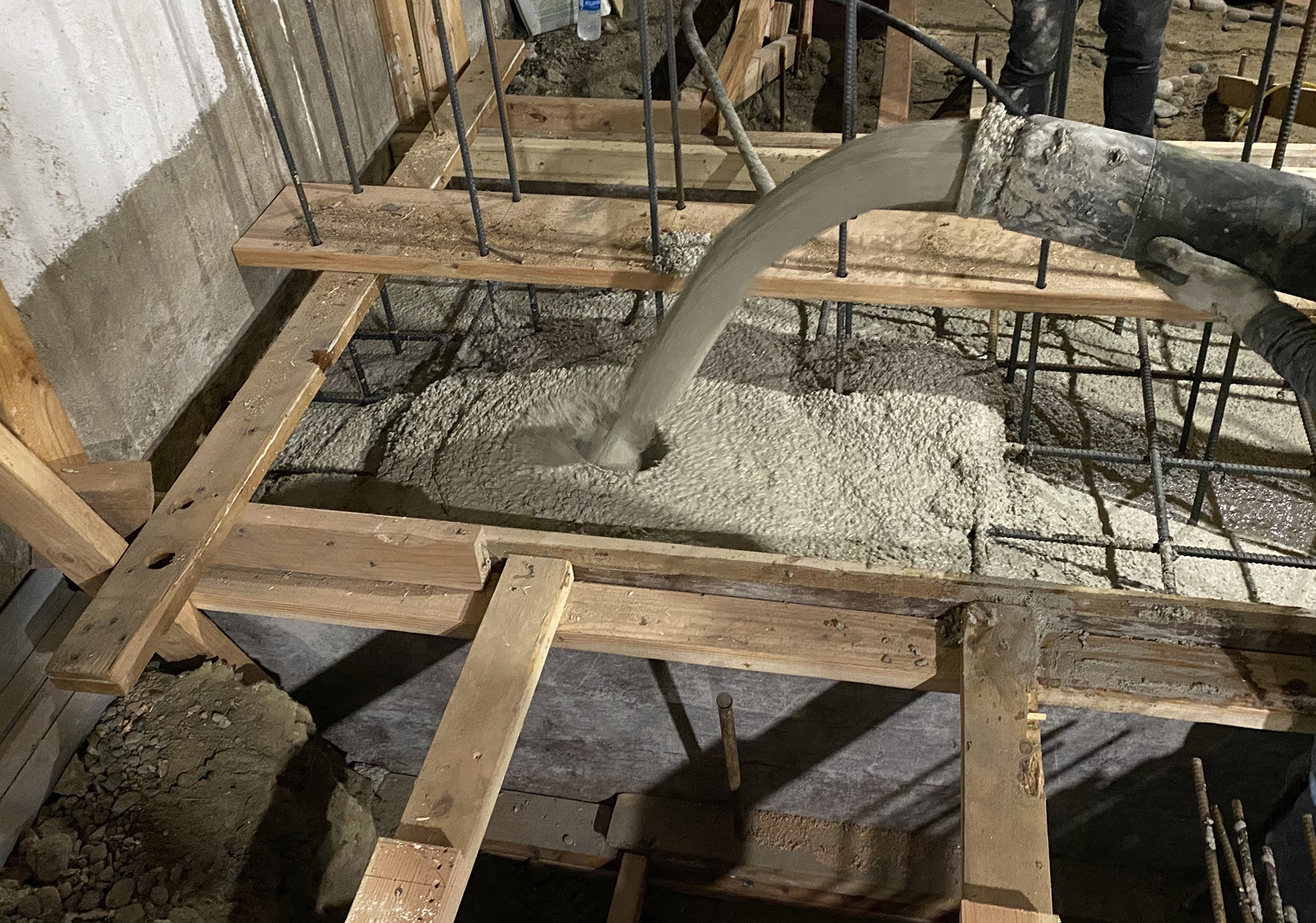
The cement industry has a heavy carbon footprint. Every year the production of portland cement is responsible for 8% of the global carbon dioxide emissions. “For every ton of cement, you produce up to nine-tenths of a ton of carbon dioxide emissions,” explains Grasley.
Considering the widespread use of concrete globally and the associated carbon footprint of the material, there is a lot of academic and industry research focusing on reducing the emissions produced from concrete. For instance, researchers have used different, more climate-friendly materials in concrete and cement. Other researchers tackle the energy-intensive process of producing concrete.
“(Portland cement) is a very highly energy-consuming material: Each ton of it requires 4-6 gigajoules (up to 1,667 kWh) to manufacture,” says Rouzbeh Savary, Ph.D., the founder and president of C-Crete Technologies. To put that energy use in perspective, 1,667 kWh could run the average home for about 57 days.
Companies and academic researchers are developing their own versions of low-carbon concrete. This includes Savary and his team at C-Crete, who this summer debuted their portland-cement-free concrete in a commercial building in Seattle.
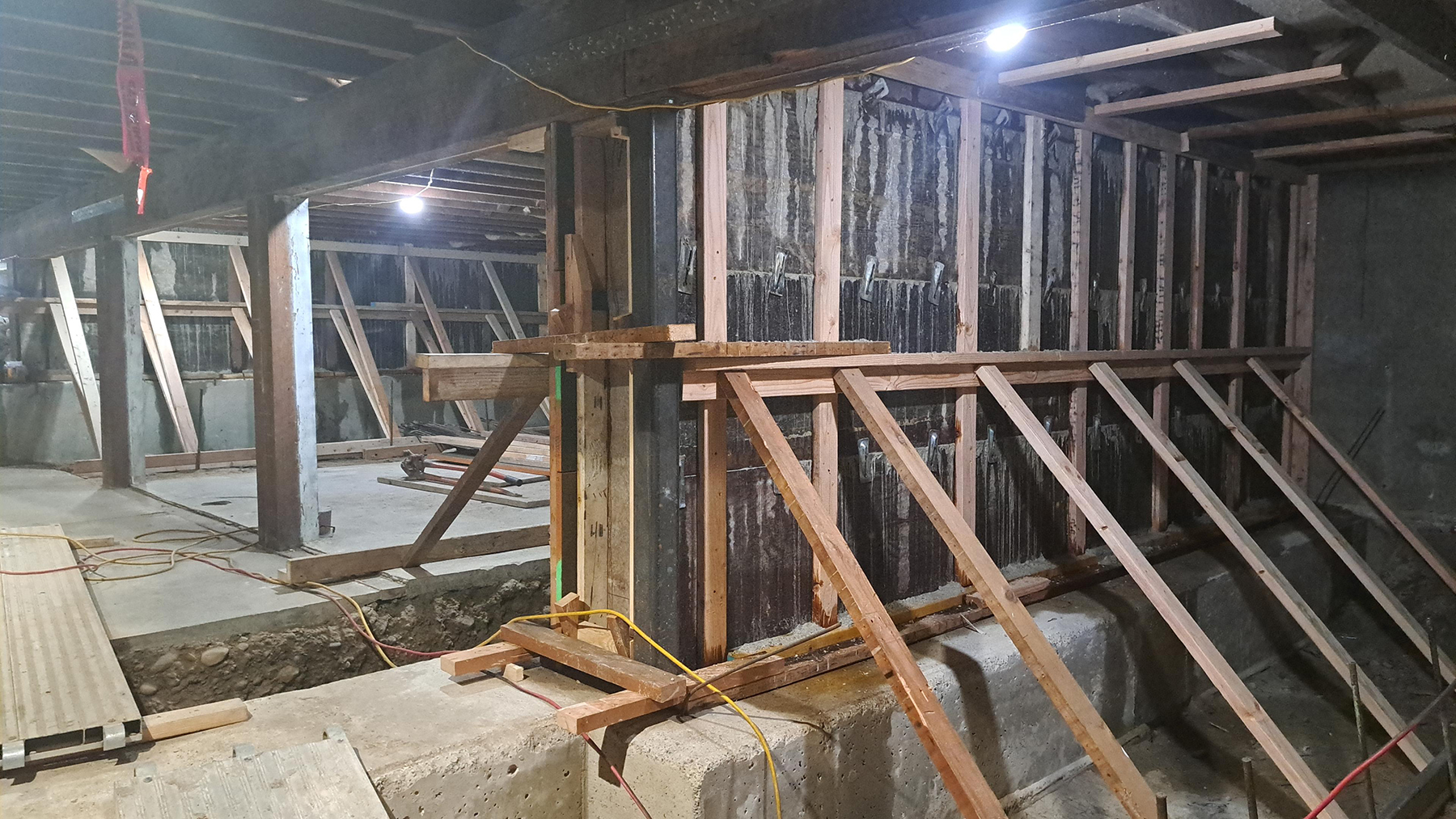
“This was the first pour of a portland-cement-free concrete in an actual building in the United States, making history,” says Savary. The pourable concrete had “great flowability” and was pumped into the foundations and shear walls as part of a seismic retrofit of a 120-year-old historic brick building.
Developing a portland cement alternative
Savary has been thinking about concrete for 40 years, beginning as a child watching his father build multistory buildings with concrete. He spent the last 20 years diving into how to improve concrete, especially related to carbon emissions.
“Portland-cement-based concrete did a great job (for) 150 years or so, but we cannot tolerate its CO2 emissions and energy consumption anymore,” Savary says. “There must be a new way.”
He and his engineers want to replace carbon-intensive cement, not just incrementally improve it. They have been reverse-engineering to create a new material that is comparable to, or even better than, portland cement.
“That was a big, big challenge,” Savary says. “Over the years we had hundreds of recipes that all failed. Typically, these failures are due to two reasons: One is you get something exciting, but it’s too costly. The other reason is lack of the abundance of the raw material, the feedstocks.”
Over time, they experimented with different binders derived from abundant feedstocks. Eventually, they created C-Crete, a mixture of natural minerals and industrial byproducts. These materials are locally available and are usually site-specific. For example, says Savary, an area may have industrial byproducts, such as slag from steel manufacturing, that can be incorporated into C-Crete for use nearby. “Another area may have a natural rock that fits well with our technology and thus locally accessible for use as a binder.”
Word has traveled in the construction community about an alternative concrete that is not only good for the environment but can use local feedstocks. “Companies are sending us their own local feedstocks to test so we have been accumulating a library of all different feedstocks that we convert to cementitious binders,” says Savary. “When we go to different states or countries, this library will enable us to quickly determine whether and how the local feedstock would work with our technology.”
The researchers put C-Crete through rigorous testing, including accelerated aging and load testing. In the Seattle building, C-Crete had a loading strength of more than 5,000 psi, verified by independent third parties, and greater than the ASTM standard of 4,000 psi for concrete footings. The mixture also met all key industry standards for durability and workability and had cost parity with conventional concrete.
Challenges to incorporating alternative concretes
A key requirement in introducing a new material for the conservative concrete industry is to make it feel familiar, says Savary. “Furthermore, the catch is to make it very easy to implement. … In our case, we just swap portland cement in concrete with our binder, and the rest is business as usual,” he says. “This is because the concrete industry, and construction industry in general, are very risk averse.”
Grasley agrees, noting that anything to do with structural engineering or building infrastructure that impacts human health and safety is scrutinized. “We tend to be very conservative and not just jump on to new material and start building skyscrapers out of it,” he says. “Because we're so risk averse as an industry, we develop these codes and standards and specifications, and those things are just slow to change.”
One option for ushering change, says Grasley, is to field-test some of these new products in a lower-risk setting. “We can start testing these things out in the marketplace and work out a lot of the wrinkles and a lot of the unknowns in some of these applications that are less regulated,” he notes. For instance, sidewalks and driveways could be low-stress testing sites. “There are lots of those kinds of applications where we can really start to prove out some of these materials and start getting them in the marketplace much more quickly.”
The slow pace of mainstream adoption has not diminished the development of new, low- and no-carbon building materials. “It's exciting to see all of these things happening,” says Grasley. He and his colleagues are also developing new materials, including carbon-negative hempcrete for 3D-printed houses, and working on replacing rebar with recycled steel fibers.
As for C-Crete, Savary says his team already has plans for future construction projects, including three other buildings in Seattle and a large project in San Francisco. The team is seeing strong interest in portland-cement-free concrete from architects, general contractors, structural engineers, and ready-mix companies and hopes to see that interest go mainstream. “If a new product benefits the environment, and it has the same performance and cost as compared to conventional concrete, then it becomes a no-brainer to use it.”
This article is published by Civil Engineering Online.