By Sarah Derouin, Ph.D.
A typical multistory building needs to be strong and cost-effective, but buildings fabricated with traditional methods require a lot of carbon-intensive materials and labor-intensive assembly. At the end of a building’s life, these traditional materials are rarely recycled, instead ending up in landfills.
Researchers at the Department of Energy’s Oak Ridge National Laboratory and the University of Maine wanted to change the one-and-done nature of multistory construction while using more sustainable materials. With this in mind, they developed a single-piece floor panel made entirely of biologically based materials. The panels – affectionately called cassettes because of their similar look to old-school cassette tapes – are as strong as the traditional steel-concrete versions, require no assembly, save on labor costs, and can be fully recycled.
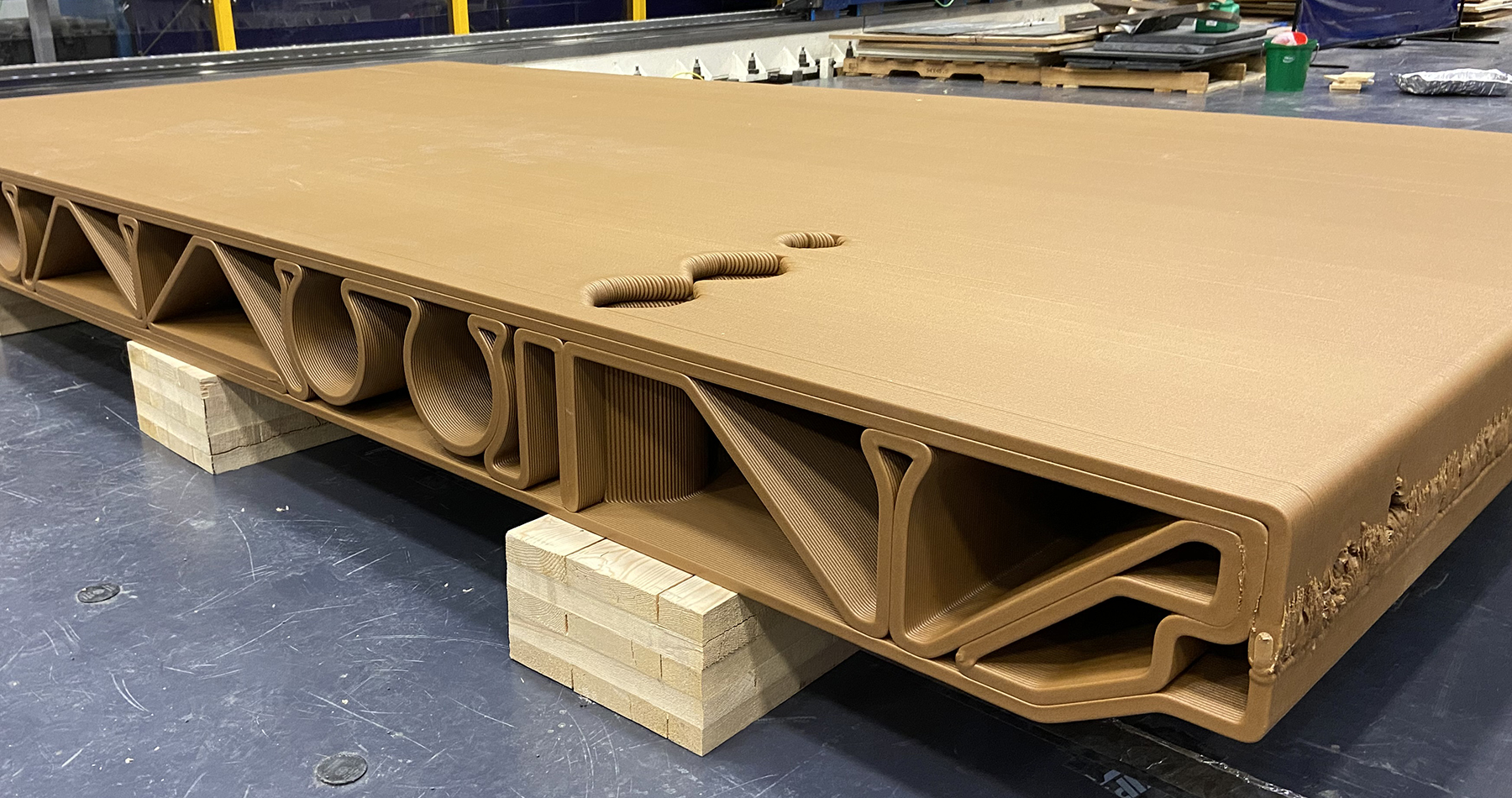
Limitations of traditional construction
Constructing a new building can be a time-intensive endeavor. Taking a page from the old Sears catalog and do-it-yourself home kits, some companies have turned toward prefabricating wall and floor panels and then assembling parts of the building on-site. The panels are transported to the site, lifted with a crane, and slotted into a metal skeletal structure.
While on-site labor is reduced with this modular building, these panels still require time-consuming assembly. Traditionally, floor panels were constructed around steel frames that had to be screwed together, explained Katie Copenhaver, Ph.D., a materials engineer at the Oak Ridge laboratory. “It's at least 130 screws, and it took (workers) well over an hour to assemble.” After the frame was assembled, the rest of the floor panel had to be built over the frame. The process repeats for each floor panel, with an added complexity: Each panel must be engineered differently to leave room for plumbing, electricity, and heating, ventilating, and air-conditioning configurations.
Further reading:
- ASCE releases groundbreaking standard for sustainable infrastructure
- Using waste materials to create sustainable building materials
- School design promotes readin’, writin’, and sustainability
Modular panels have layers of steel, aluminum, concrete, and wallboard. These materials, especially concrete, can be significant sources of carbon emissions. When a building is destroyed, the remnants end up in landfills. “I think one of the issues with traditional construction materials and why they're not recycled is just how many different materials are present,” Copenhaver said. She noted that with traditional floor cassettes, it simply isn’t worth the time and effort to tear the panels apart and reuse parts.
Benefits of 3D-printed, biobased floor panels
Oak Ridge partnered with researchers from the University of Maine to create a new way to construct modular floor cassettes that would address these labor and sustainability issues. Using large-scale 3D printers, the team created single-piece floor panels made from biomaterials. They used a biobased plastic called polylactic acid – a common 3D-printing material – made from corn residue. “If you have a home printer, then you probably have a spool of PLA,” Copenhaver said.
Fillers like carbon fibers or glass shards can strengthen PLA and eliminate expansion and contraction behavior in the panel feedstock, explained Halil Tekinalp, Ph.D., a chemical engineer at Oak Ridge. He said the team focused on cellulose-based fillers of various sizes, ranging from nanoscale to millimeter. Bamboo, flax, and poplar filler were considered, but the team found pine wood flour worked best. The resulting PLA and wood feedstock is fully biodegradable and as strong as steel.
Using this material, the team printed its floor panel in about 30 hours, creating a cassette made from one material with no need for assembly. The team estimates that using a 3D-printed cassette would result in labor savings of about 33% compared with constructing traditional steel floors. The panel design can also be easily changed, creating different configurations for internal wires and pipes without added assembly labor.
The biobased floor is also capable of having a second life. “Because this material is thermoplastic, you can basically just shred it and reuse it,” said Tekinalp, adding that he and his colleagues are currently testing the resiliency of recycled biomaterial over multiple shred-melt-print cycles. “You can use this material for different industrial processes like injection molding and convert it into less structural applications,” he said.
The adoption of 3D printing, or additive construction, was catalyzed by NASA’s 3D-Printed Habitat Challenge competition, said Shadi Nazarian, an architectural professor at the University of Texas at Arlington. She was not a part of the study. “There is a lot of research being done in various places around the globe by universities, firms, and startups,” she said. “There's a lot to learn, but there's a lot of potential for this.”
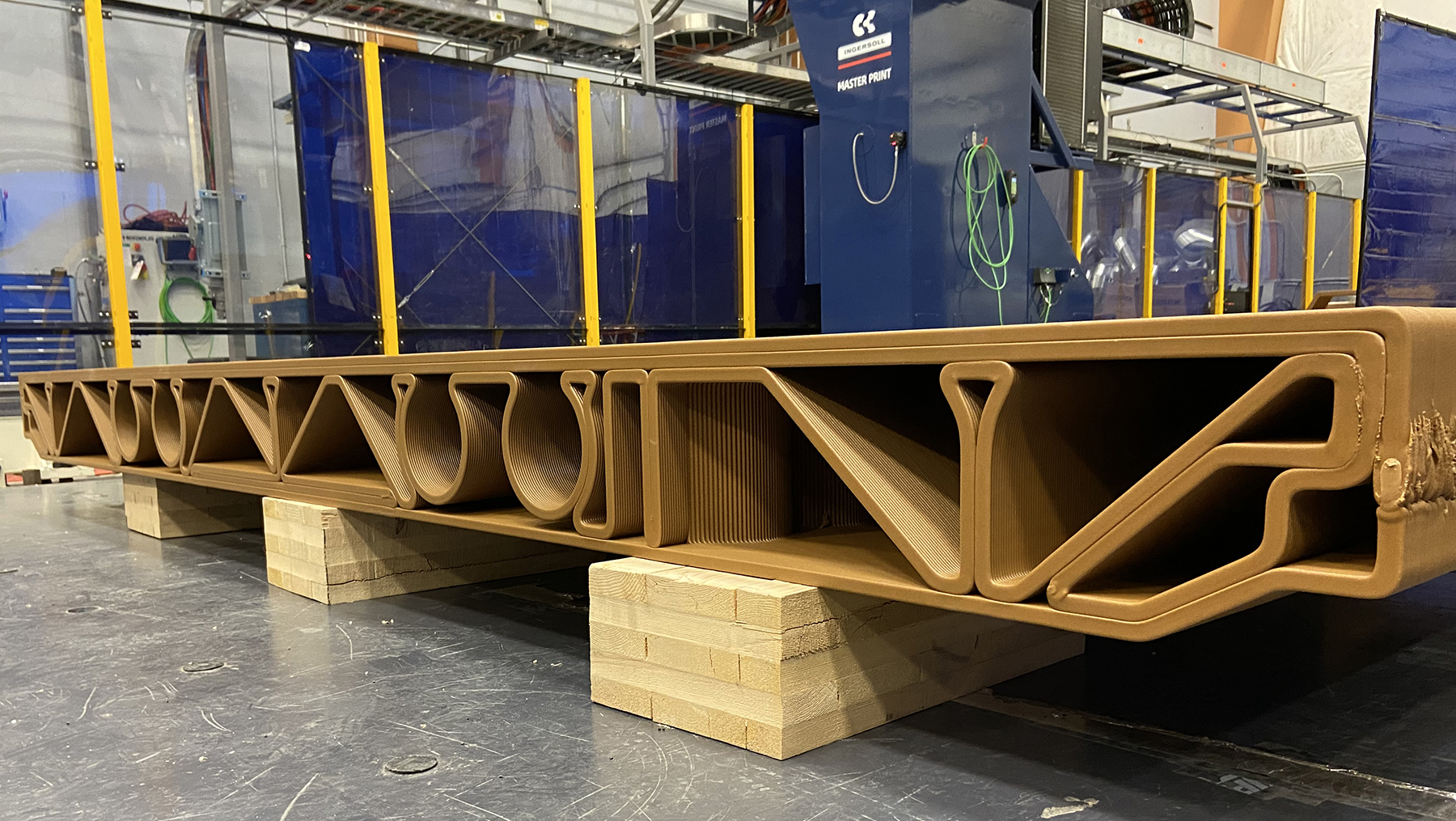
Nazarian said 3D-printing feedstock may also be a chance to reuse other industrial by-products. For example, fly ash, which used to be discarded, can be used to create alternative binders instead of ordinary Portland cement – a carbon-intensive product. Nazarian noted that 3D printing “not only enables us to use the exact amount of material needed to construct something but also avoid wasting wood used to make formworks for cast concrete.”
Despite the promise of 3D printing in construction, she stressed that “it is not always cheaper at the beginning to use this method of construction.” She said as more people learn how to use these materials and adopt 3D-printing methods, it will become more affordable.
Tekinalp agreed, adding, “When you go large scale, I think cost-wise, it should be comparable to what's already available in the other traditional metals. Even the cost of feedstock material is going to go down once you start producing large quantities.”
The researchers said their work proves the potential of 3D biobased printing in construction, but there are hurdles in building codes and production scaling that need to be addressed before printing reaches widespread adoption.
“There are a handful of large-scale additive manufacturing companies in the U.S. right now that do that kind of work. … It's a very niche area, but we're hoping that there's more and more of those,” Copenhaver said.
This article is published by Civil Engineering Online.