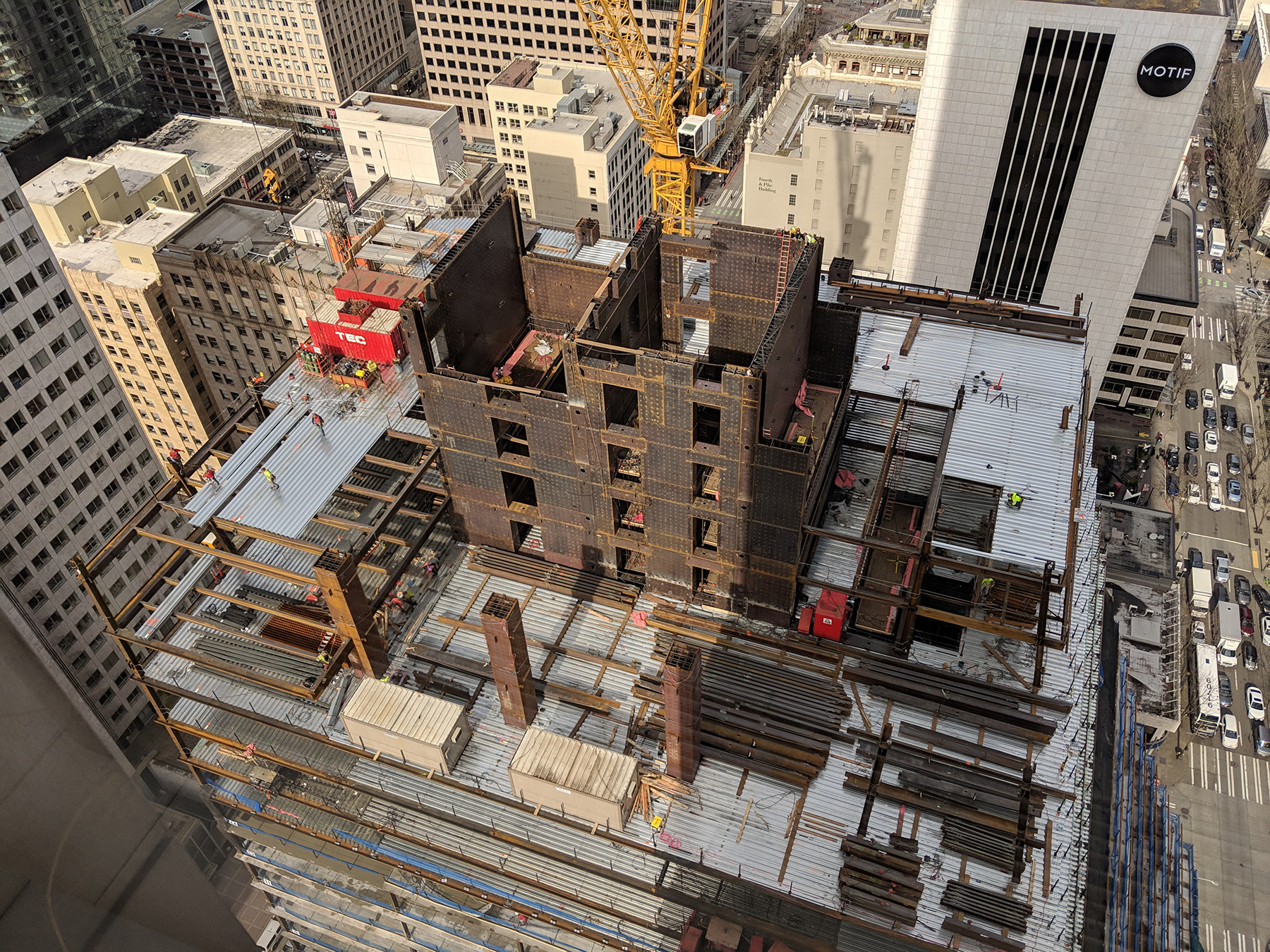
By Catherine A. Cardno, Ph.D.
Cast-in-place reinforced-concrete cores have been the structural system of choice in high-rise construction for decades. However, that could now change: Practitioners and researchers have worked together to design and test a concrete-filled, composite steel-plate shear wall core system based on technology previously used for blast and impact protection in the defense and nuclear industries. The nonproprietary system — dubbed SpeedCore — has already been written into the ASCE 7-22 Minimum Design Loads and Associated Criteria for Buildings and Other Structures standard and will be included in the American Institute of Steel Construction’s 341-22 Seismic Provisions for Structural Steel Buildings standard.
Created by Magnusson Klemencic Associates, Supreme Steel, Turner Construction, Cives, J.F. Stearns, and Banker Steel, the steel-and-concrete system has the benefit of speeding construction by as much as 43% over a traditional cast-in-place reinforced-concrete core design, according to information from AISC.
“The development of SpeedCore really is another steppingstone in the evolution of structural systems,” explains Ron Klemencic, P.E., S.E., NAC, NAE, Hon.AIA, Dist.M.ASCE, who championed the SpeedCore technology for application to commercial buildings. Klemencic is the CEO of MKA, a structural and civil engineering firm.
In the 1960s, highly efficient exterior structural systems, such as the exterior braces used for the John Hancock Center in Chicago, were the norm, according to Klemencic. “The structural bracing system for (this type of design) was at the perimeter of the building, which made it super-efficient but in many regards compromised views and reduced the attractiveness from a leasing point of view,” he says. “Over time, the commercial real estate market put a lot of pressure on the structural engineering community to come up with a different approach that didn’t involve structure at the perimeter.”
By the 1980s, those braced frames evolved into core-braced buildings with large composite mega-columns, such as were used in the Two Union Square building in Seattle, Klemencic says. But the necessary size of those concrete columns became very impractical for especially tall buildings. “It solved the perimeter problem (and) gave the clients and the tenants what they wanted in terms of views and wide, expansive column-free spaces, but it put these huge columns in the core, which impacted elevators and stairwells and hallways,” Klemencic says.
The next structural system evolution came in the 1990s with reinforced-concrete cores, which solved the internal geometry problem presented by the mega-columns, Klemencic says. “So now the walls were more uniform in thickness and were more easily planned around from a leasing and architecture point of view. (And) it kept the structure in the core.”
The problem introduced by the reinforced-concrete core structural system, however, was the rate at which a steel-frame high-rise could be built. Or rather, the rate at which it could not be built: The steel for a building can be erected twice as fast as its concrete core can be placed because of the curing requirements of concrete.
“What became a common state of practice … is that the reinforced-concrete cores are built well ahead of the steel erection, so that the concrete core will finish at its top at about the same time that the steel catches it, which results in a big lag in the schedule on the order of months,” Klemencic says. “And so the whole prompting of SpeedCore was how do we solve that problem?”
The system is formed from pairs of prefabricated structural steel plates. Each wall module is formed from two parallel plates that are connected to each other with tie bars to create a sandwich that will ultimately be filled with concrete. The modules are then connected to one another to form the structural core of the building. Because the modules are nonproprietary, they can potentially be manufactured by any steel fabricator.
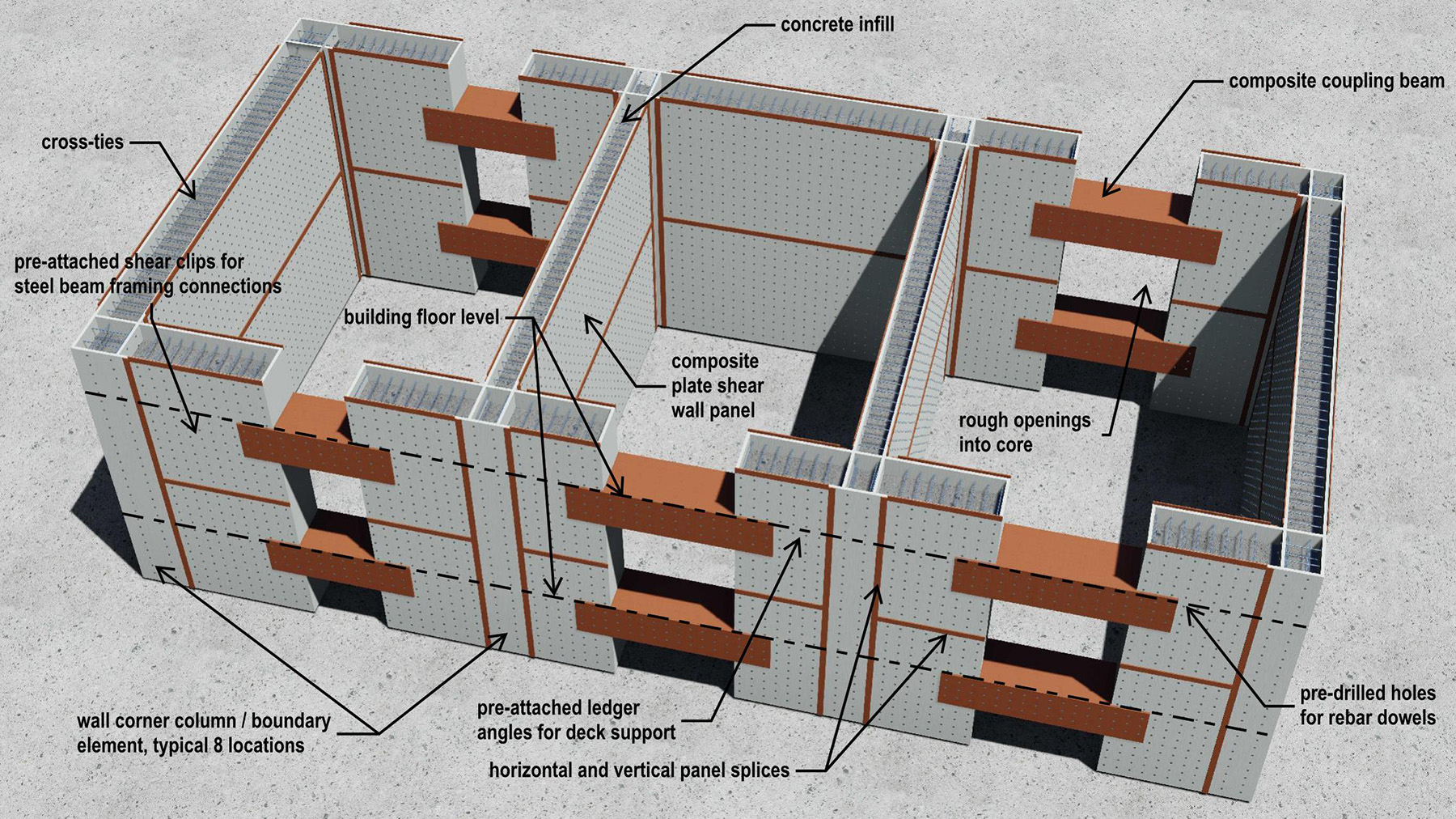
Concrete is placed within the panel modules in the field in a trailing operation once the wall modules have been erected on-site, according to Klemencic. (The SpeedCore structural core will also contain the building’s elevators and stairwells, as is the case with reinforced-concrete cores.)
The steel plates are designed so that as many as eight floors of the system can be constructed before concrete must be placed inside the wall modules, according to Klemencic. Floors can be erected as quickly as one per day. In comparison, a reinforced-concrete core typically takes from three to five days per floor to construct.
The system is an evolution of a now-discontinued British Steel product from the early 1990s called Bi-Steel, which was primarily used in U.S. and United Kingdom defense industries as blast walls because of their robust performance, Klemencic says. It was also later developed for use in the nuclear industry. “So we adopted and adapted this technology … and said, ‘How do we make it work for a commercial high-rise building?’” he says. “That’s where we departed and went on our own path.”
In the SpeedCore system, stresses are shared between the steel plates and concrete infill via the tie bars that connect the two sides of the steel shear walls as well as by smaller, optional headed studs that are welded to the plates, according to Amit H. Varma, Ph.D., M.ASCE, the Karl H. Kettelhut Professor of Civil Engineering and the director of the Bowen Laboratory of Large-Scale CE Research in the Lyles School of Civil Engineering at Purdue University. Varma was the principal investigator of SpeedCore technology.
Together, the headed studs, tie bars, and steel plates sandwich the concrete infill so that the system behaves as one integral composite unit. The thickness of the steel plates, the amount of concrete infill, and the sizing of the headed studs and tie bars are all contingent on the design of the building itself.
Significantly, however, “the tie bars are what makes the empty steel modules stable and strong,” Varma says. “In the empty phase, they serve to make the steel module behave as a structure” and are able to withstand the casting pressure introduced by filling the panels with the concrete.
A special mix, developed by Stoneway Concrete, is used in the system. “It’s more like a grout (without coarse aggregate), and it easily and readily flows through the SpeedCore panels, even around the corners,” Klemencic says. Because the geometry of the SpeedCore panel system is so precise, contractors can monitor the volume of concrete that is placed within the panels, “so that you can rest assured that there aren’t any big voids anywhere.”
Laboratory testing of the system for seismic and wind loading took place in Varma’s lab at Purdue and the University of Buffalo, according to Klemencic. The tests also determined how far in advance the steel shear walls and steel framing for a building could be erected before the steel modules had to be filled with concrete.
To date, two buildings have been constructed using SpeedCore technology: the 850 ft tall Rainier Square Tower in Seattle and the 250 ft tall 200 Park Avenue in San Jose, California. MKA served as the engineer of record for the buildings. The former saved 10 months on the construction schedule out of an estimated 32 months, and the latter saved three months on the schedule and $10 million, according to Klemencic.
Both buildings have welded connections between the prefabricated panels, but a designed — but not-yet-constructed — building in Boston will use bolted field splices. “We know in many markets around the world that bolting is a preferred field connection methodology,” Klemencic says. “People like to bolt things in the field because welders are expensive and short in number.”
Catherine A. Cardno, Ph.D., is the managing editor of Civil Engineering Online.
This article first appeared in the September/October issue of Civil Engineering as “Composite Core Speeds Construction.”