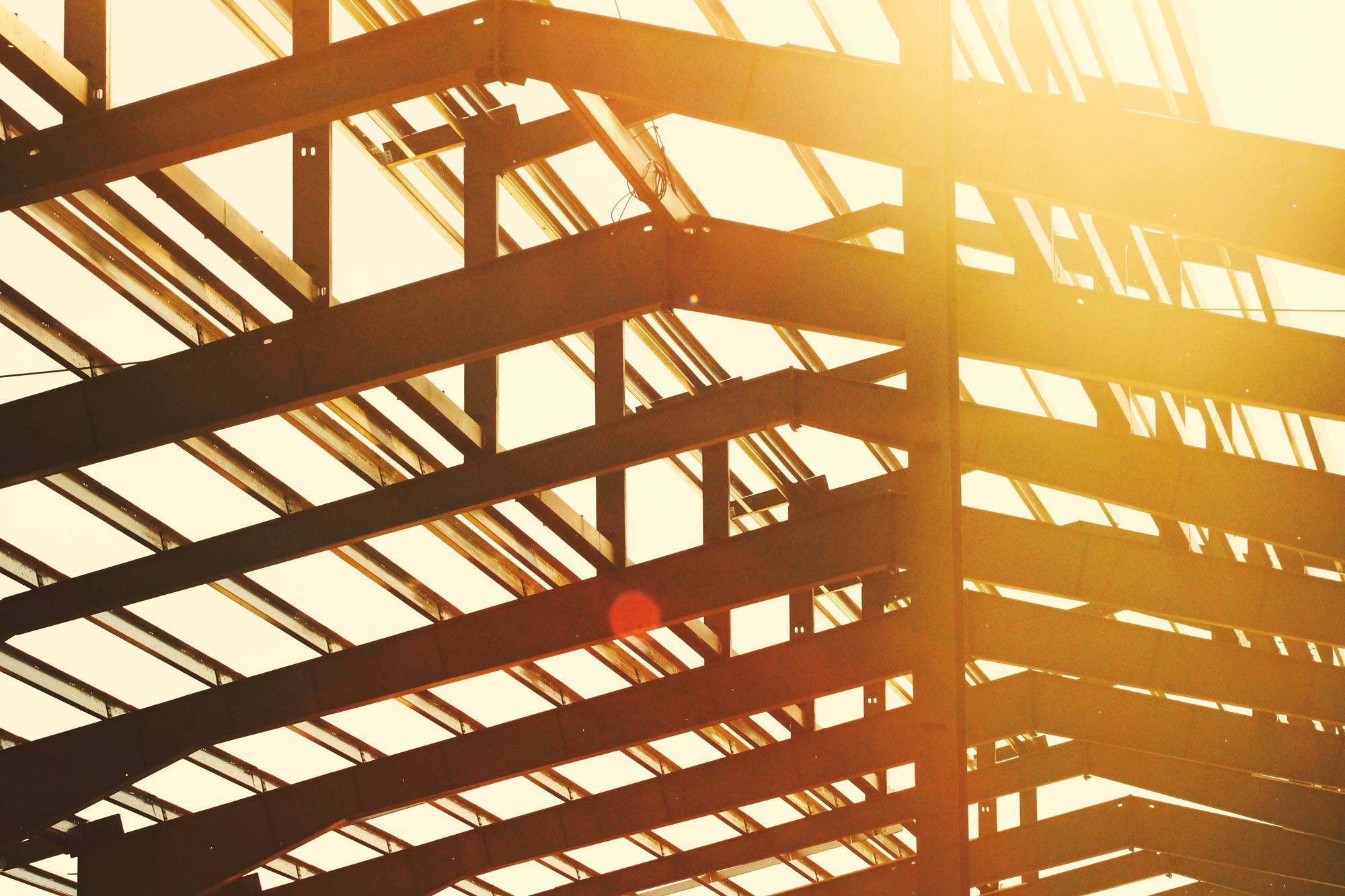
Modular construction is not new. It has been an effective approach for industrial structures for more than three decades.
However, there is a surprisingly scant amount of literature available for civil engineers who are looking to employ best practices in modularization for their projects.
The ASCE Energy Division’s Task Committee on Onshore Heavy Industrial Modularization Guidelines worked for six years to help fill that gap, and the result is the recently published Structural Design of Modules for Energy and Industrial Facilities.
Its lead authors will be presenting key findings April 10 at the ASCE Structural Engineering Institute’s Structures Congress 2025. They also spoke with Civil Engineering Source about their book, along with the how and why behind modularization.
Civil Engineering Source: What users did you have in mind when you wrote this book?
David Kerins, chair of Task Committee on Onshore Heavy Industrial Modularization Guidelines: The intended audience is mainly structural engineers tasked with designing the structure for a module.
It will also interest project team members to understand what goes into a module and what extra things you have to consider for a module compared to a stick-built structure.
Because module construction brings on a total change in mindset, you have to make a lot of decisions much sooner. For example, the schedule is compressed, so you have to work closely with other disciplines to build a good schedule logistic in order to build the modules offsite while building the foundations and infrastructure onsite.
And then third-party people like building officials and licensing officials may also be interested. Maybe they’re looking at a module project in their jurisdiction, and they need to know what they should review and how to understand what is different compared to stick-built.
Luca Magenes, Task Committee member and 2025 vice-chair of Energy Division Executive Committee: The main target is structural engineers working in industrial settings and on industrial types of projects, for the most part. However, it does extend into other markets and industries that can use the modular approach, constructing something partially somewhere and then transporting it to the final location.
Silky Wong, Task Committee member and 2025 past chair of Energy Division Executive Committee: I want to add that I sometimes teach structural and civil engineering students. And what I’ve realized is that structural designs in modularization – which is the main content of our guideline – are not in any textbook yet.
Currently, there’s no university design course for the design of modules, so I really hope that we will be able to use this guideline in the classroom, and students can better understand how the design of modules works in our industry.
Source: I feel like I’ve heard a lot more people recently talking about modularization as being a more cost-effective and generally just a better option. Is that anecdotal, or is this something you’re seeing become more prevalent on a large scale?
Kerins: Cost-effectiveness and quality depend on the site and the location. Originally, modules came up for remote areas.
I worked on a site in British Columbia that had absolutely no roads going to it, and so everything came in by boat. We did some modules on that project. For example, modular buildings for the camp were rolled off the barge and put in place; everything was connected, and the buildings were ready to go. There were also modular process units and pipe racks.
So the process has been around for a long time. Recently, we started to see it being used for congested areas.
I worked on a project in Belgium that was in the heart of the Antwerp industrial area. There was absolutely no land available, so we had to build the process units offsite, bring them by barge right next to the site, and unload them right at the site.
There are a number of studies done by the Construction Industry Institute that tell you when it is more economical to do a process unit as a module versus stick-built.
You’ve also got to deal with the availability of onsite skilled labor, which is in short supply across the world right now. There are many projects I have been doing on the Gulf Coast that are now being marginalized because of the lack of skilled labor here. So it’s not just the cost you’re considering.
Wong: And from a sustainability point of view, which we do cover in the book, what I’m seeing is that when it comes to shop fabrication, the onsite installation, and the construction materials being offsite in a more controlled environment, modularization actually reduces a significant amount of waste and thus provides some material savings.
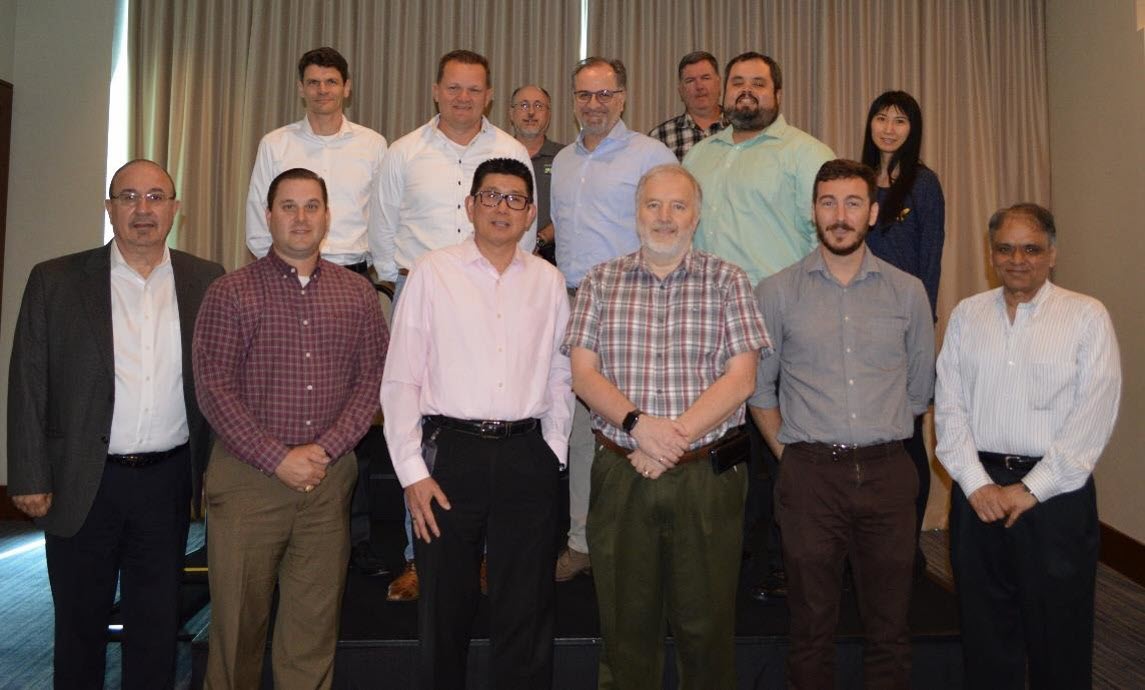
Source: When you shift the work hours offsite into fabrication yards, how do you maintain control of the work?
Magenes: I work for a manufacturer, and we do a lot of offsite fabrication and prefabrication. And you actually have a lot more control when you work in an environment where you can assemble things and check them through a quality department rather than out in the field, where, as David said, sometimes you have a shortage of skilled labor.
Let’s say you’re working on a project that may be far away. You have to hire and train those people near the site location. Whereas with modularization, you have them all here working on projects and sending out similar types of structures to those faraway locations.
This also limits your risk from a project management perspective. You’re trying to control how much time you’re spending onsite. You can have weather delays. It’s a lot safer to work in a factory where processes and procedures are in place, and people have been trained to use the same type of machines.
There are a lot of advantages to offsite fabrication.
Kerins: That’s one of the increased costs of modularization in that you need a project management team, including owners, at the fabrication yard as well as at the site. So your management costs go up.
But, like Luca said, you can get a lot better quality dealing with workers who do the same thing one project to the next, where they just finished the module for another company, and now they become more skillful in the subject area and are working on a similar module for your company. If you do it as a stick-built on that site, you might get workers who are working on this unit for the first time, which requires time and thus cost to train to meet the expected level of quality.
Source: If there’s one key recommendation here that you want structural engineers – or whoever is picking up this book – to add to their process, what would that be?
Kerins: For me, it’s schedule.
You make the decision to modularize as early as possible in your project. Even at the very beginning of the project, the question should be,
“Am I going to modularize it or not?” because it’s a fundamental change in how you lay out things.
You need to decide on that very soon, and you need to bring in all the parties involved and have the project team and sponsors committed to it (or committed to not modularizing), as quickly as possible. Modularization is not something you can do after you’ve engineered it.
Modularization is a lot more complex because now you have to consider transport and how big the module can be. It’s a big question because if you’re driving a module down the street, you may have to go under overpasses or through narrow areas. You need to know all those things up front.
Wong: I agree. I hope that the users of this guideline will become very proactive in their projects. Don’t assume that other disciplines fully know what they’re doing.
Modularization really stretches your ability to get to know the entire project team in some areas that you might have never thought of.
It takes some courage to ask questions outside of one’s discipline. It might sound silly to ask a question that might be a basic consideration for another discipline. Still, it is important to not to assume and limit each aspect of the project to one discipline as modularization has many more multidiscipline interfaces as compared to stick-built.
Magenes: The last thing I’d mention is that because there are no real codes out there – standards or official literature – sometimes the engineers who work on these projects must go back to basics. It’s a lot of like doing engineering in the original sense of the word.
You don’t have a standard that guides you. You have to make decisions based on your own judgment – and remember physics and remember mechanics!
Learn more about the guideline, Structural Design of Modules for Energy and Industrial Facilities.
Attend Structures Congress 2025.
And find additional ASCE resources on modular construction including the Special Collection on Modular Construction/Off-site Construction’ and infographic available in the ASCE Library.