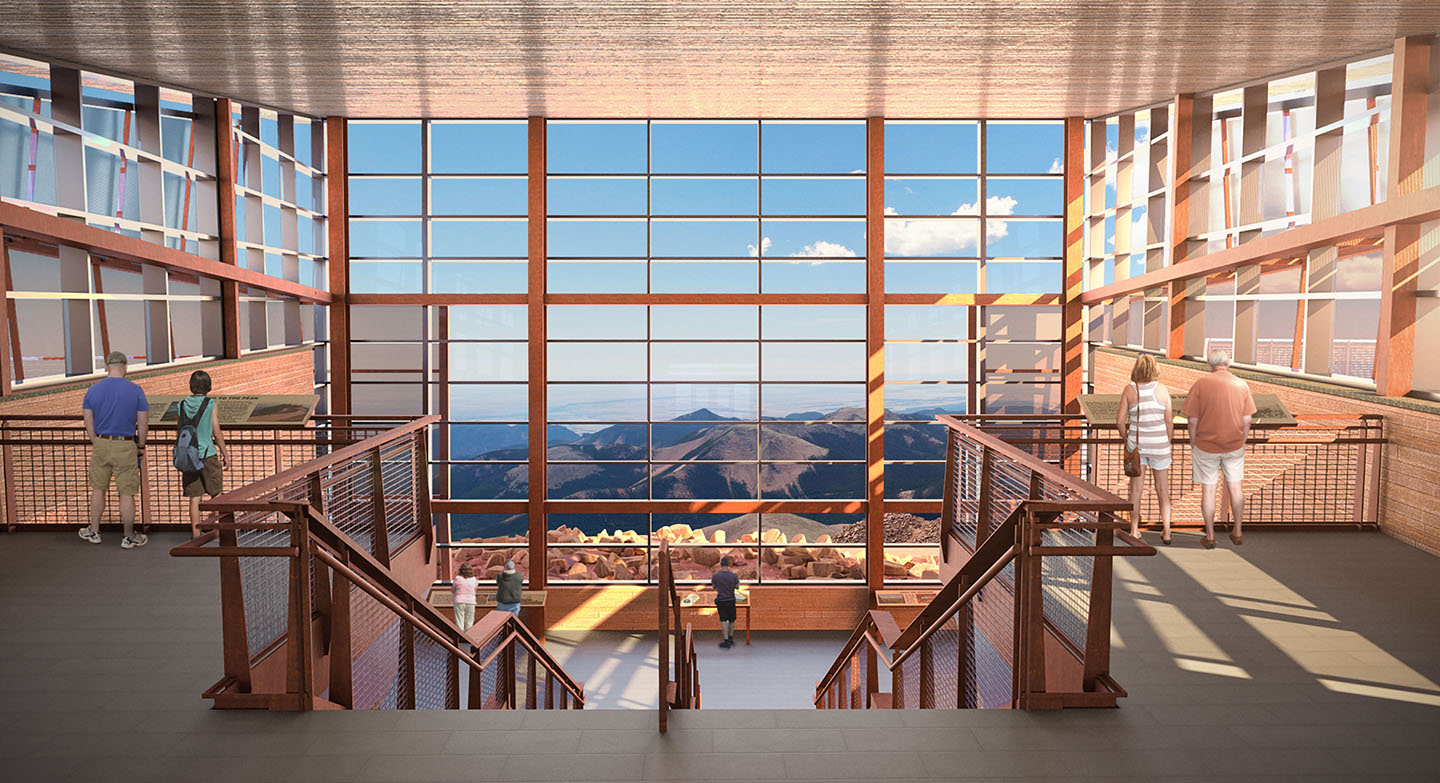
Colorado has more than 50 mountains that exceed 14,000 ft in height, but Pikes Peak is one of a kind. Named for the famed explorer Zebulon Pike, the 14,115 ft summit, which is also known as America’s Mountain, inspired poet Katharine Lee Bates to write the patriotic song America the Beautiful. Located 12 mi west of Colorado Springs, this National Historic Landmark has long attracted tourists, who have the option of traveling to the mountaintop by car, cog railway, or foot. For decades, those reaching the top of Pikes Peak have been met by the Summit House, a modest facility known mainly for its novel high-altitude doughnuts. After three years of construction, the new Pikes Peak Summit Visitor Center is set to open in early summer. Built to significantly enhance the experience of visitors at the summit, the new center was designed to survive the rigors of the summit while also minimizing its impact on the environment.
The visitor center is the centerpiece of the $60 million, 38,000 sq ft Pikes Peak Summit Complex and features a pavilion with a main lobby that has a large, glazed curtain wall that enables expansive views. An exhibition area, gift shop, dining area, and mechanical space for utilities also are located within the two-story pavilion.
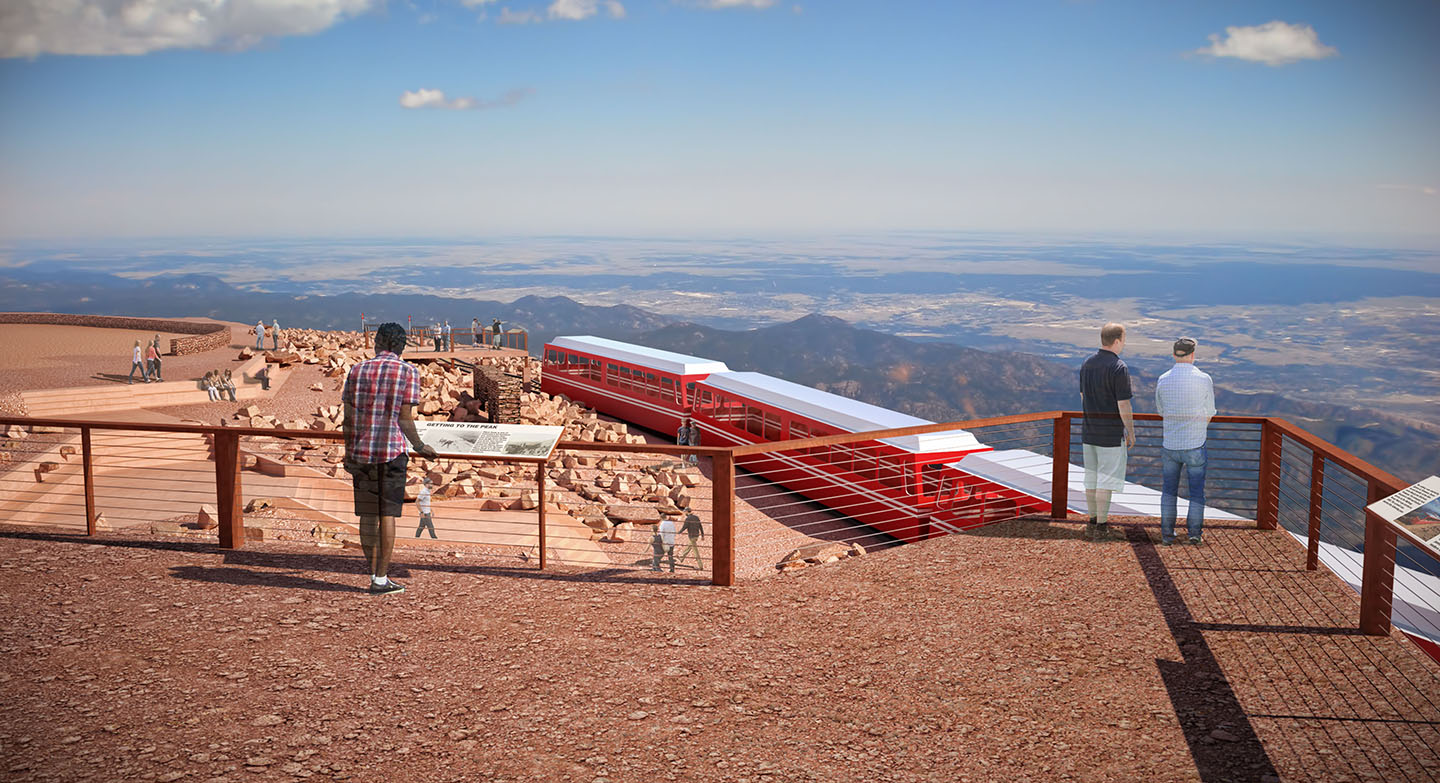
The building’s exterior includes upper and lower terraces. Outside the pavilion, raised pathways guide visitors to and from such features as a summit elevation marker, the end of the line for the Broadmoor Manitou and Pikes Peak Cog Railway, and an overlook that juts out approximately 30 ft beyond the north side of the mountain. The complex also includes a communications facility for Colorado Springs Utilities and the U.S. Army’s High Altitude Research Laboratory, both of which previously had been separate buildings located at the summit.
‘An iconic experience’
The new visitor center was designed by GWWO Architects in collaboration with RTA Architects, the architect of record for the project. In developing the vision for the project, the design team sought to create a facility that would emphasize the grandeur of the natural setting itself. “The intent was to design a building that really becomes one with the peak,” says Alan Reed, FAIA, LEED AP, the president and design principal for GWWO. “Seen from below, the building and entry pavilion seem very diminutive on the peak, but when you walk in, these views just explode,” Reed says.
“We wanted to create an iconic experience, not an iconic building,” says Stuart Coppedge, FAIA, LEED AP, the principal in charge for RTA. “You can’t out-mountain the mountain. It’s all about the total experience, not some architectural monument.”
Ensuring accessibility for all visitors to the rugged site was a priority for the project owner, the city of Colorado Springs, Coppedge says. The pavilion itself includes two elevators, while the precast-concrete walkway system links the building to the various outdoor features at the site. “This will be one of the most accessible public facilities in the country,” he notes.
Geotechnical challenges
The design and construction team had to contend with numerous challenges associated with the high-altitude site, says William Hoffmann Jr., P.E., M.ASCE, a senior engineering consultant for CTL Thompson Inc., which served as the geotechnical engineer of record and provided third-party testing of materials. For example, geotechnical conditions entailed an active layer of permafrost in the upper 6 ft of soil. As a result, this soil layer is susceptible to seasonal freezing and thawing, Hoffmann says. Immediately beneath this active permafrost, a 2 to 3 ft thick layer of ice extends down to the bedrock, which maintains a year-round temperature of 27 F or lower.
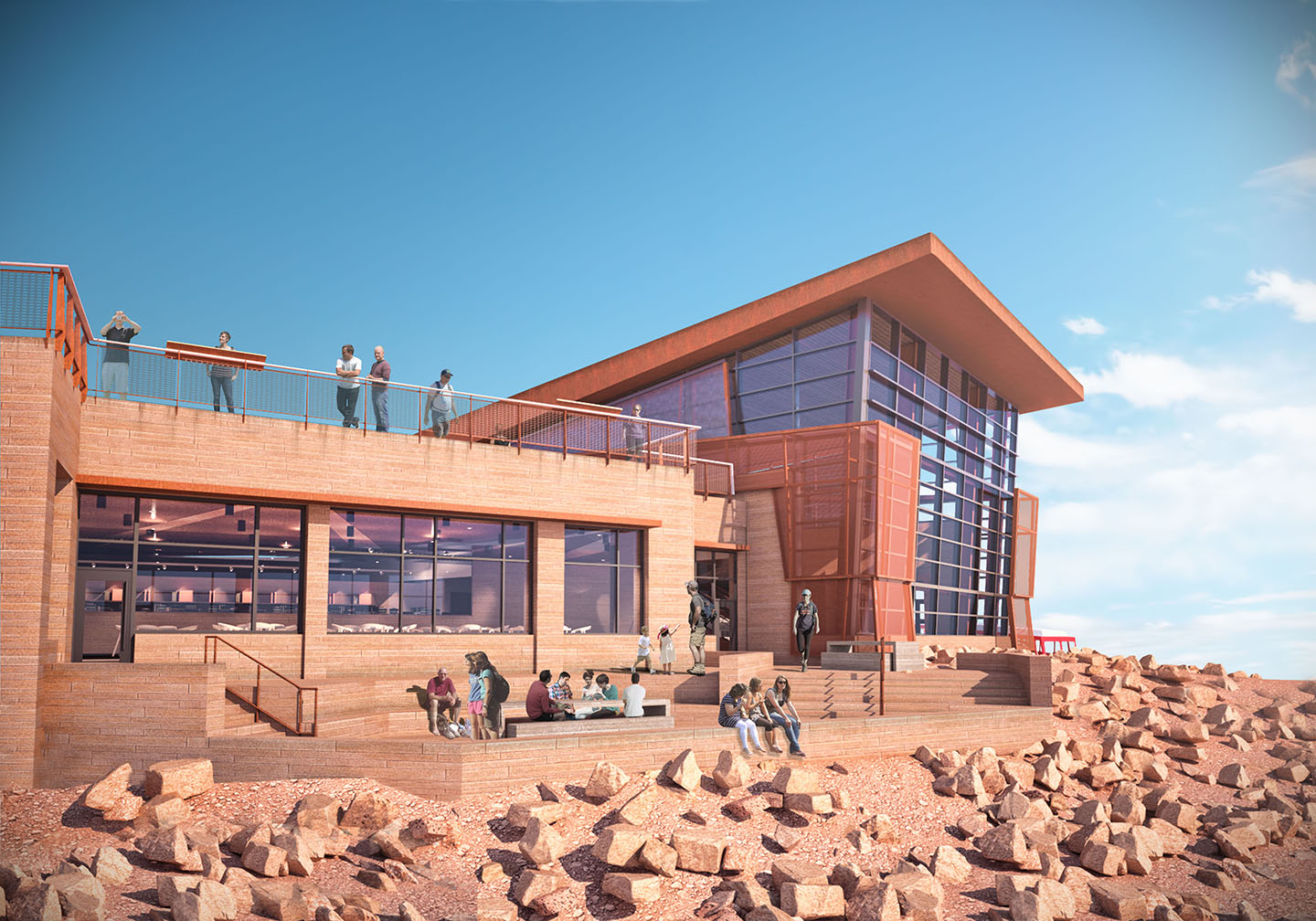
As it happens, the foundation of the original Summit House had been seated on the ground with insufficient insulation, offering an example of how not to proceed, Hoffmann says. When it was heated in the summer, the building would melt the underlying ice layer. During the winter, the closed building was not heated, allowing the ice layer to “heave back up,” Hoffmann says. Essentially, the Summit House “was tearing itself apart, all the way from 1963 when it was originally built,” he notes.
Because of this, adjustable posts had been installed to support the original floor. These were reviewed and adjusted every season to accommodate the subgrade’s continual movement.
To avoid a similar problem in the new building, the design team realized that the spread footings that had been selected as the foundation for the new visitor center “had to penetrate that ice layer and get into the bedrock,” Hoffmann says. Simplifying matters somewhat, the design called for the north edge of the visitor center to be recessed into the mountainside, resulting in a building foundation that is two stories below-grade in this location. In this way, the contractor — the GE Johnson Construction Co. — was able to excavate through the ice layer on that side of the building. On the south side, by contrast, “we had to deepen the foundations to make sure they got through the ice layer and into the bedrock,” Hoffmann says.
The remote location of the project affected the extent to which concrete was placed on-site during construction. Simply hauling concrete to the summit was a challenge because the roadway’s steep grades along the route to the top precluded the use of standard-sized concrete trucks, Hoffmann says. “We had to half-load a smaller concrete mixer” to transport concrete to the project site, he notes.
Altitude adjustments
Further complicating matters were the effects of the altitude on the concrete itself. Concrete that was to be placed on-site was made in Colorado Springs, which has an elevation of about 6,000 ft. However, “the properties of concrete change when you get it up to 14,000 ft,” Hoffmann says. “Air bubbles in concrete made at 6,000 ft expand incredibly” at the summit because of the lower air pressure there, he notes. “There was quite a dance going on with concrete placement,” as the effects of the 90-plus-minute drive from the plant and the elevation change were managed with concrete additives, he says.
Because of the complications related to the high elevation, “we tried to fabricate as much of the building as possible down at Colorado Springs or along the Front Range,” says Steve Horner, P.E., a principal for HCDA Engineering Inc., the structural engineer of record for the project. Ultimately, 424 pieces of precast concrete were made by the precast-concrete manufacturer Stresscon at its Colorado Springs facility and hauled to the site.
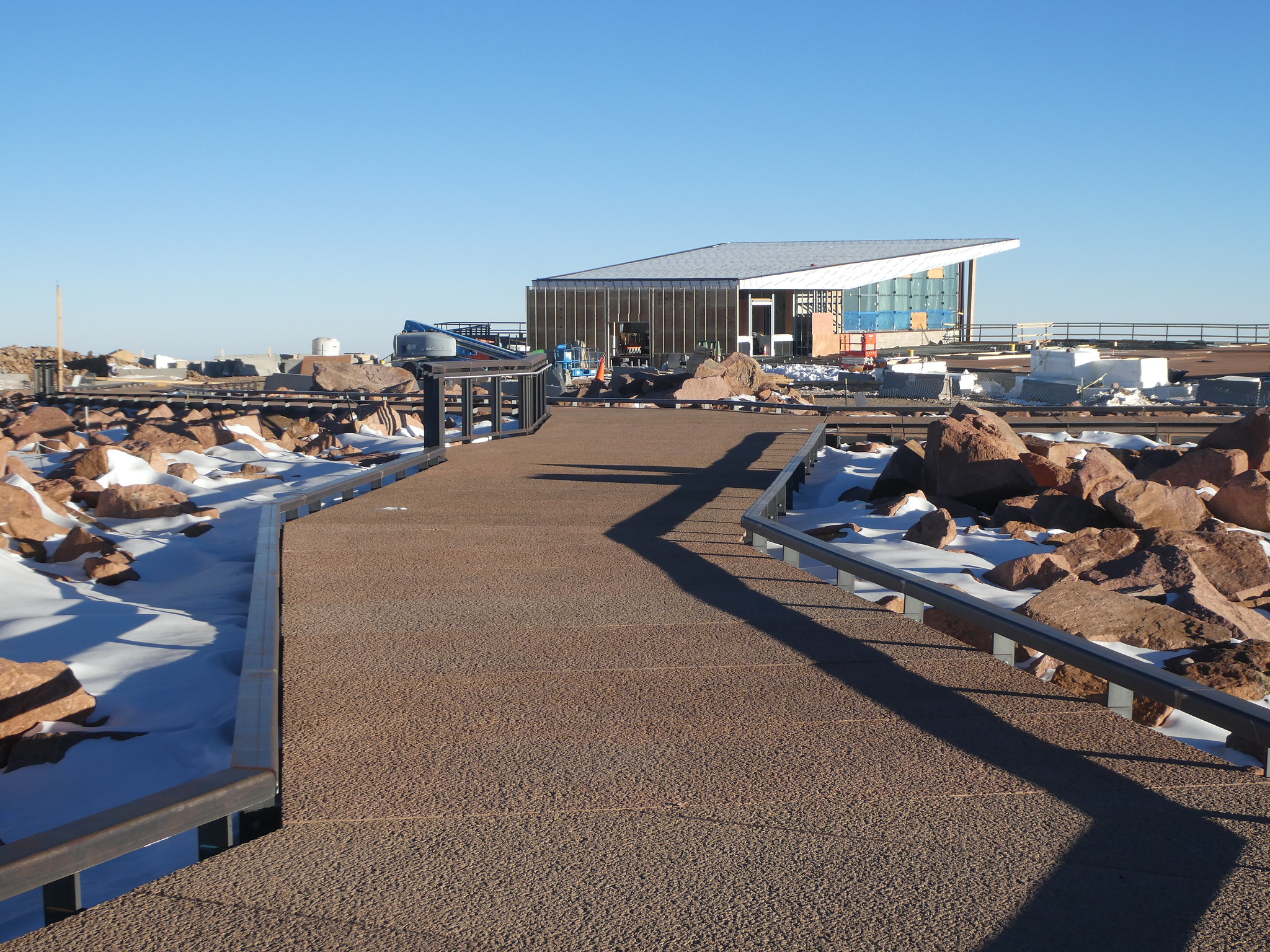
Extreme weather conditions at the high-altitude site affected the project design in other ways. For example, the summit complex was designed with a snow design load of 125 lb/sq ft, while the ultimate wind design load was a 3-second gust at 270 mph, Horner says. As a comparison, for a similar building category along the Front Range of Colorado in cities such as Pueblo, Colorado Springs, Denver, and Fort Collins, the common snow design loads are 30 lb/sq ft with wind design speeds of approximately 140 mph.
In addition to the loads of the gusts themselves, the strong winds at the summit routinely pick up gravel and other debris, creating a “scouring effect” on the visitor center, Coppedge says. For this reason, “we designed a shutter system that comes down over the windows,” he notes. The system was needed to protect the windows from “flying debris hitting the building,” Coppedge says.
Beyond silver
From the outset, the project was designed to achieve silver certification as part of the U.S. Green Building Council’s Leadership in Energy and Environmental Design program. However, during project development, BranchPattern — the project’s mechanical and electrical engineer — suggested that the design team also pursue certification as part of the Living Building Challenge standard developed by the International Living Future Institute, Coppedge says. “We realized that (with) all the things we were doing (to promote sustainability on the project), we were almost reaching many of the Living Building Challenge criteria,” he says.
Looking to align the built and natural environments to the greatest degree possible, the aspirational LBC standard comprises the seven performance categories of place, water, energy, health and happiness, materials, equity, and beauty, according to the website of the International Living Future Institute. Among other things, attaining the LBC certification meant designing a project that generated as much energy as it consumed, produced net-zero waste, and reduced water use considerably.
To this end, the visitor center includes a radiant floor heating system that circulates heat from the lobby floor — where the direct solar gain is significant — to colder areas of the building. “We’re sharing heat into the right zones of the building,” Coppedge says. Meanwhile, recessing the building into the mountain and heavily insulating it help maintain a stable internal temperature. As for energy generation, the harsh environment precluded the use of solar panels at the summit. However, the project will include the installation of photovoltaic panels elsewhere in the state that will feed into the grid. The location of that array is still being determined. However, once that portion of the project is complete, “that electricity that we’re generating … will let us be net electricity positive,” Coppedge says. “When it’s all finished, we’ll generate more electricity than we’re using.”
The visitor center is equipped with vacuum toilets that require minimal amounts of water to send waste to an on-site wastewater treatment system. In turn, the system will treat the water to a nonpotable level for reuse on-site in toilet flushing. “Much of the water then is essentially recycled and reused on the summit,” Coppedge says. “That reduces the amount of water we’re using, and it reduces the amount of energy that it takes to haul that water up and down the summit.”
Achieving the LBC certification also accords with the long-term goals of the project owner. “We wanted the place that we are building today to be sustainable and healthy for our families who visit today, tomorrow, and 50 years from now,” says Beatrice Reinhardt, a senior office specialist for Pikes Peak-America’s Mountain, the entity of the city of Colorado Springs that operates the visitor center. “LBC was a way to meet the challenge.”