By Jay Landers
In 2010, California’s Central Valley Regional Water Quality Control Board issued a new, much more stringent wastewater discharge permit to the Sacramento Regional County Sanitation District. Commonly known as Regional San, the entity owns and operates the Sacramento region’s wastewater conveyance system and treatment facility. To comply with the new requirements, Regional San embarked on a 12-year, $1.7 billion project to upgrade its secondary wastewater treatment plant to a tertiary system, which is now known as the EchoWater Resource Recovery Facility.
[Editor's note, March 2024: Since publication the district has changed its name to Sacramento Area Sewer District, now known as SacSewer instead of Regional San.]
Unique among projects of its size and scope, the recently completed effort was delivered on schedule and under budget and will enable Regional San to conduct one of the largest agricultural water recycling projects in the country beginning in late 2025.
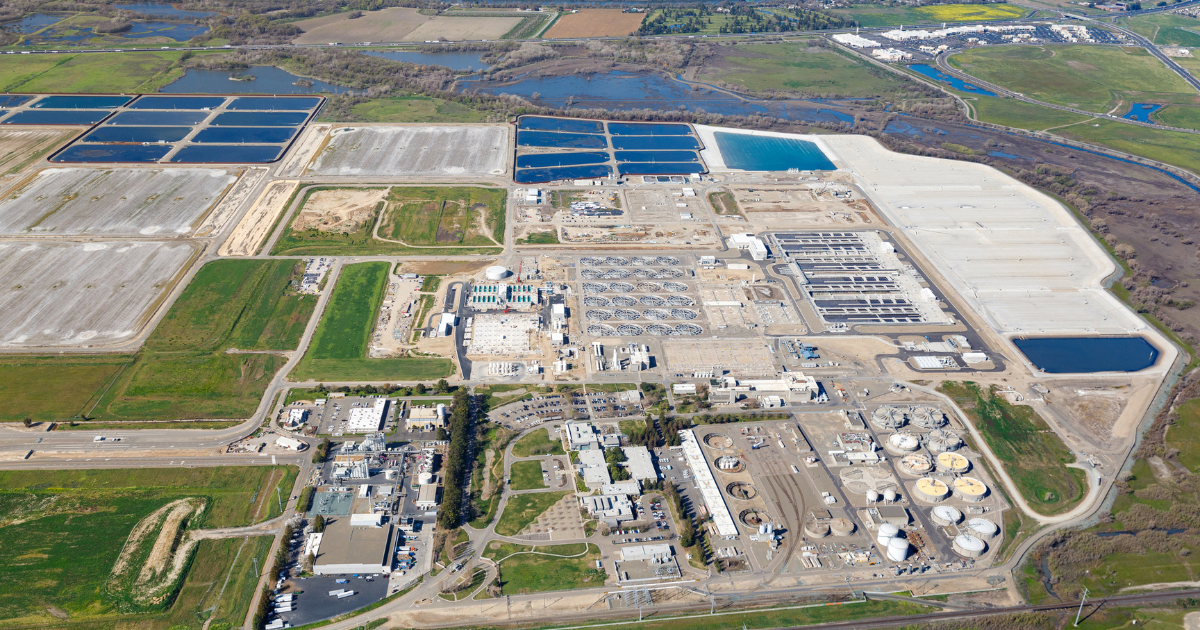
Major changes
Looking to improve the health of the Sacramento River and the delta formed by the Sacramento and San Joaquin rivers, the Central Valley Regional Water Quality Control Board made “major changes” to Regional San’s discharge permit in 2010, says Mike Crooks, the agency’s deputy director of operations.
For example, the permit required a much lower limit for the amount of ammonia in Regional San’s discharge and set a limit of 10 mg/L for nitrate-nitrogen. By mandating improved pathogen removal and destruction, the permit essentially required that Regional San add filtration to its treatment facility, which discharges to the Sacramento River. Discharge limits for biochemical oxygen demand and total suspended solids were reduced from 30 to 10 mg/L, and total coliform levels were limited to a most probable number of 2.2/100 mL.
“Basically, the permit required that we produce water that was equivalent to Title 22 regulations for drinking water and for unrestricted water recycling uses,” Crooks says. (Title 22 of the California Code of Regulations includes the state’s requirements for treating different sources of water.)
Pilot test
Given the multiple process changes that would be needed, Regional San quickly set up a pilot treatment facility to evaluate various advanced treatment technologies. For example, different configurations for controlling ammonia by means of nitrification and denitrification were tested “using our own wastewater coming into the plant,” Crooks says. “The treatment technologies had to be compatible with our incoming flow characteristics.”
In terms of testing filtration methods, Regional San evaluated “granular media using different types of media and different depths,” Crooks says. “We also looked at a couple different membrane technologies.” For disinfection, the pilot facility evaluated chlorine, ultraviolet light, and ozone.
“This pilot plant let us test all these different variables against our own water quality coming in,” Crooks says. “By doing that, we could select the processes that best addressed the treatment needs in a very cost-effective way. I'd say that that was the key for us getting started, to know what we had to build here in order to meet those new permit requirements.”
Based on its pilot test results, Regional San opted to employ biological nutrient removal as the secondary treatment process to remove ammonia. Comprising eight large concrete basins that operate in parallel, the BNR facility includes aerated and non-aerated zones to effect nitrification and denitrification. “That was our largest project for the whole program,” Crooks says.
All told, the BNR process removes 99% of ammonia and 89% of nitrogen from the wastewater stream, according to a May 15 news release from Regional San.
Size, cost reductions
For the filtration process, the EchoWater facility uses granular media filters containing sand and anthracite. Thanks to its pilot testing, Regional San was able “to prove to the state that we could design these facilities using different criteria compared to those that are prescribed by various state regulations,” Crooks says.
Although California’s regulations prescribed a filtration rate of 5 gal./minute per sq ft of media, “we were able to prove that we could meet the treatment goals at a higher rate of 7 ½ gal. per minute per sq ft, which meant a significantly smaller footprint that we had to construct for the filter facility,” Crooks says. “That meant rather large savings in terms of construction dollars.”
A similar finding occurred regarding the chlorine disinfection process. “The state has requirements with respect to how much time the water has to be in contact with the disinfectant,” Crooks says. “We were able to prove that we could do it with a shorter contact time. That meant a smaller footprint for our disinfection contact basin.”
These changes to the filtration and disinfection processes “substantially reduced the entire footprint of the tertiary facility,” says Scott Parker, P.E., a senior project manager and senior vice president for the engineering consulting firm Carollo Engineers, which designed several of the 22 individual projects that the EchoWater project comprised.
“We were able to fit it into a part of the plant that allowed for a very compact footprint,” Parker says. “It went along well with existing plant infrastructure in terms of flow conveyance and reserved a substantial swath of land that was going to be taken up by the proposed filters and chlorine tank contact tanks. We were able to preserve that for future plant expansion.”
Sidestream treatment
Among the more out-of-the-ordinary upgrades made as part of the EchoWater project was the addition of an approximately 4 mgd sidestream treatment facility designed to remove ammonia from return flows generated by solids handling processes.
Digested solids from the EchoWater facility are stored in stabilization basins and capped with water until such time as the solids are removed and applied to agricultural lands. When it rains, water levels rise in the basins, and the overflow is returned to the headworks of the treatment facility. “That water has a really high ammonia load,” Crooks says.
The sidestream nitrification treatment facility comprises three independently operating sequencing batch reactors that aerate the return flows to convert the ammonia in the wastewater into nitrite and then nitrate. The effluent from the sidestream treatment process is then pumped upstream into Regional San’s conveyance system, where the nitrate-rich water helps control odors by reducing hydrogen sulfide levels.
As a result of this approach, Regional San has been able to reduce the amount of sodium hypochlorite that it purchases for use in controlling odors in its collection system. In this way, the nitrification treatment facility “provides a cost savings in terms of chemical costs,” Crooks says. “If it hasn't already done so, it'll pay for itself in a very short amount of time.”
The sidestream treatment facility also “reduces the nutrient load on the BNR process,” Parker says. This factor also enabled Regional San to decrease the size and cost of the BNR system.
Emergency storage
The EchoWater facility is permitted to treat an average dry weather flow of 181 mgd, though it typically treats on the order of 135 mgd. During wet weather, the facility can treat up to 330 mgd. In the event that incoming flows exceed this volume, the excess is conveyed to emergency storage basins and held until treatment capacity is available.
Existing equalization basins were expanded and lined with concrete to provide 430 million gal. of storage for wet weather flows, Parker says. To obviate the need for operators to manually clean the basins after they have been drained, the basins are equipped with automatic drainage and washdown features, he notes.
Beneficial factors
Major construction on the EchoWater project was completed this spring, on time and $400 million less than the original upper estimate for the project. Crooks attributes this happy outcome to multiple factors. “We did well with respect to preparing the consultant services that we did,” he notes.
Program management services for the overall project were provided by a joint venture comprising infrastructure consulting firms Brown and Caldwell and HDR. Besides Carollo, AECOM also designed several of the project’s major features.
“We had early engagement with our board to establish delegated authorities that allowed us to be a little bit more nimble with respect to responding to changes,” Crooks says. “It gave our general manager a lot of authority to do things, where otherwise we would have had to go to the board every single time something came up. That was tremendously helpful.”
A “beneficial” economic climate at the start of the program also helped, Crooks says. With the project getting underway not long after the economic downturn of 2008-09, “contractors were looking to get to work,” he says. “A lot of good competitive bids came in. We got some really great prices on our construction contracts. That helped a lot with respect to our budget and remaining fiscally responsible.”
Approximately $1 billion in fixed, low-interest loans from the state of California also played a “tremendous” role in helping lower costs, Crooks says. “Our debt service on those loans will be significantly less than it would've been had we had to issue bonds to finance the program.”
Harvest Water
Approximately 3% to 5% of Regional San’s treated wastewater is recycled for use in such activities as plant washdowns and landscape irrigation. However, wastewater recycling is expected to increase in a big way in 2025 following the completion of Harvest Water, a 41 mi long distribution system designed to convey treated effluent from the EchoWater facility to agricultural and wildlife habitat lands in southern Sacramento County.
“The overall program goal is to deliver 50,000 acre ft of water annually to the area, not only for irrigation purposes but also during the wintertime for ecological benefits,” Parker says. A joint venture of Brown and Caldwell and Carollo is providing program management services on the project to Regional San.
Once Harvest Water is up and running, “there will be periods during a typical summer day where all water treated by the EchoWater facility will be recycled, meaning nothing will be discharged to the river,” Crooks says. “It's been estimated that we will recycle roughly one-third of the water that the plant processes during the year.”
This article is published by Civil Engineering Online.