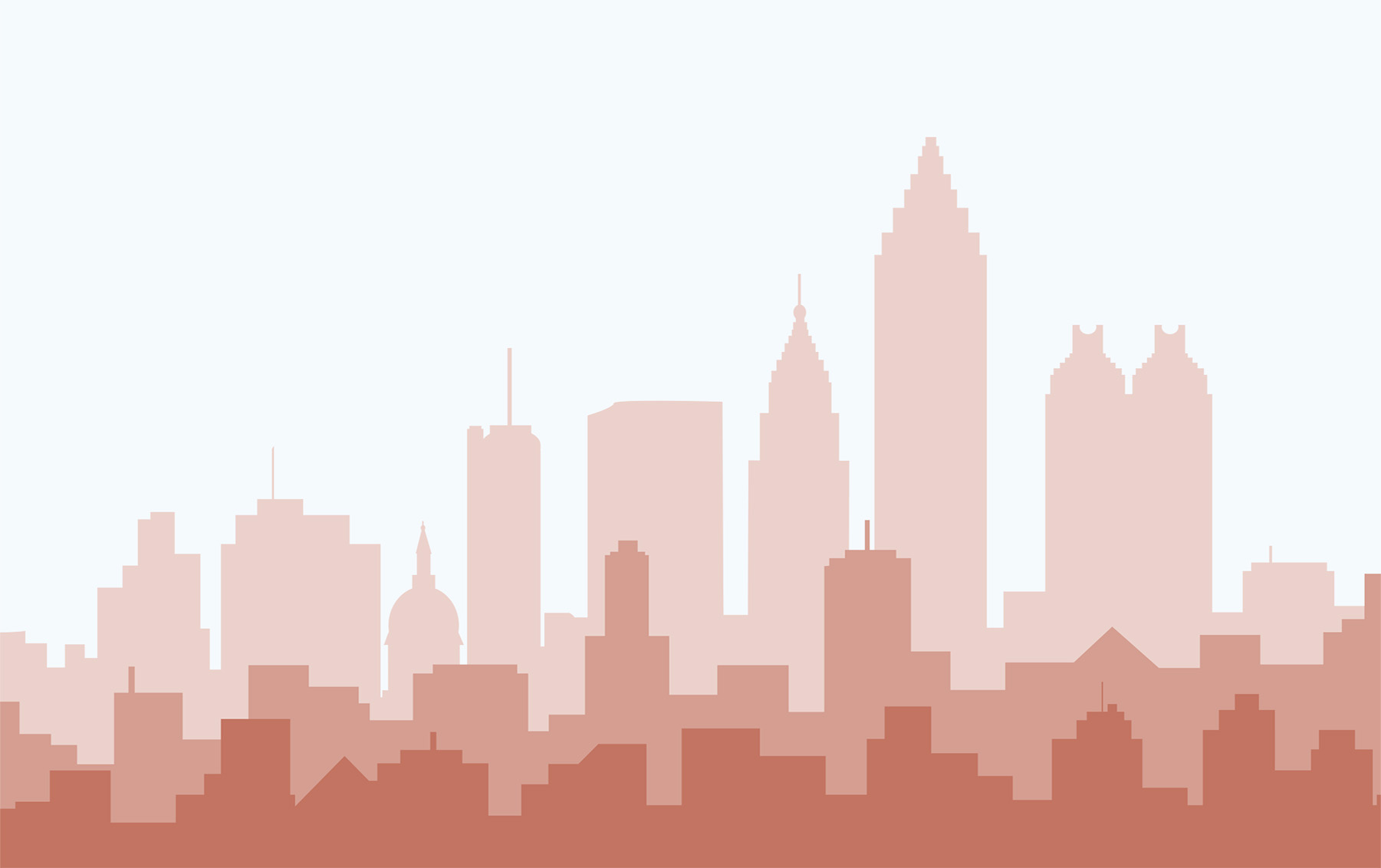
By Robert L. Reid
The entertainment industry in Georgia is growing fast. Assembly Atlanta, developed on a restored brownfield site, is adding another 1 million sq ft of soundstages and other film and TV production facilities.
Hollywood and Vine might need a reboot.
The legendary intersection of Hollywood Boulevard and Vine Street in Los Angeles, once considered the center of the movie business in Southern California, has increasingly had to share the entertainment spotlight with the growing film and television industry in the southern state of Georgia.
Call it Hollywood and Peachtree, after the ubiquitous name for untold roads and streets and other places within Georgia, whose nickname is the Peach State.
Thanks in part to film-friendly tax incentives, Georgia-based studios and locations have helped produce episodes and segments of hit TV shows and movies such as Stranger Things; The Walking Dead franchise; Marvel Cinematic Universe films, including the Black Panther and Guardians of the Galaxy franchises; and countless reality TV shows and other entertainment offerings. In fiscal year 2022, these productions brought more than $4.4 billion to the state from some 32 feature films, 36 independent films, 269 TV and episodic productions, 42 commercials, and 33 music videos, according to the Georgia Film Office, part of the Georgia Department of Economic Development.
Dramatic increase
The growth of Georgia’s film and TV industry has been almost as dramatic as the plotlines of the stories the state helps tell. From just 60,000 sq ft of purpose-built film and television studio soundstage space in 2008, Georgia now has 4 million sq ft of such production facilities, according to a report from the Creative Media Industries Institute at Georgia State University. Moreover, that soundstage capacity is poised to increase by approximately 250,000 sq ft as part of a project known as Assembly Atlanta, which will also add studio offices, production-related facilities, and mixed-use spaces, for a total development of more than 1 million sq ft.
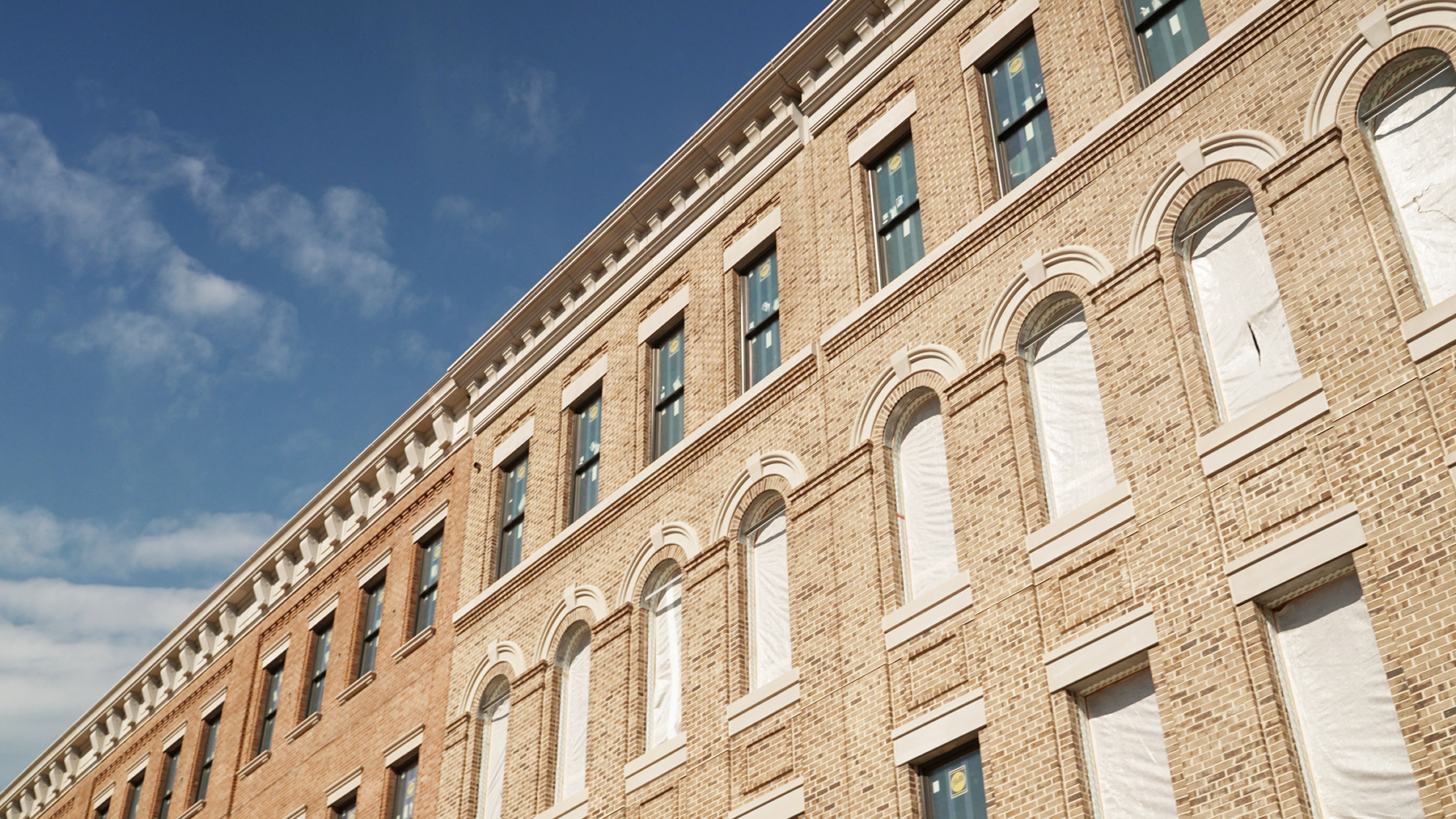
Set in Doraville, Georgia, within DeKalb County and about 15 mi northeast of Atlanta, the Assembly Atlanta project features a 135-acre mixed-use development that includes eight enclosed studio buildings that can accommodate 19 soundstages, warehouse and mill buildings for storage and set construction, two artificial ponds for stormwater control (one in the studio area and the other in a public event space), an amphitheater, a parking garage, and other facilities. The site is ideally located just off U.S. Interstate 285, which is known as the Perimeter and which carries traffic around Atlanta, and close to a commuter rail station for the Metropolitan Atlanta Rapid Transit Authority.
And, of course, Georgia being Georgia, the site is near a Peachtree Road, a New Peachtree Road, and a North Peachtree Road. DeKalb-Peachtree Airport, a municipal general aviation facility, is also close by and influenced the building heights at Assembly Atlanta.
At press time, the Assembly Studios portion of the project — part of the overall development’s first phase — was nearing completion, with the studio buildings themselves ready for occupancy. Other phase 1 work, including the public space pond and the amphitheater, is underway. A second phase will involve the construction of retail shops, restaurants, hotels, and other amenities in public spaces adjoining but separate from the studio complex. That second phase work will not begin until all phase 1 work is completed.
The Assembly Atlanta project is being constructed on a brownfield site that formerly housed an assembly plant for General Motors. After the GM plant closed in 2008, the buildings were demolished and the grounds environmentally remediated. By 2015, more than 1,660 tons of “impacted soil” had been excavated and replaced at the site, according to the Decide DeKalb Development Authority, the county’s economic development arm.
Over the years, various developers considered different options for the site, and some smaller projects were constructed on peripheral properties that had once been part of the original GM land. These were separate developments, not affiliated with Assembly Atlanta. But none of the larger plans made much headway until Gray Television — an Atlanta-based media conglomerate — purchased the bulk of the property in 2021. Gray and the Gipson Co., also based in Atlanta, are leading the Assembly Atlanta project. Gray plans to use some of the studio production facilities for its films and TV shows, while NBCUniversal Media — which includes Universal Studios, the NBC television network, and other entertainment companies — will lease and operate multiple production facilities at the site.
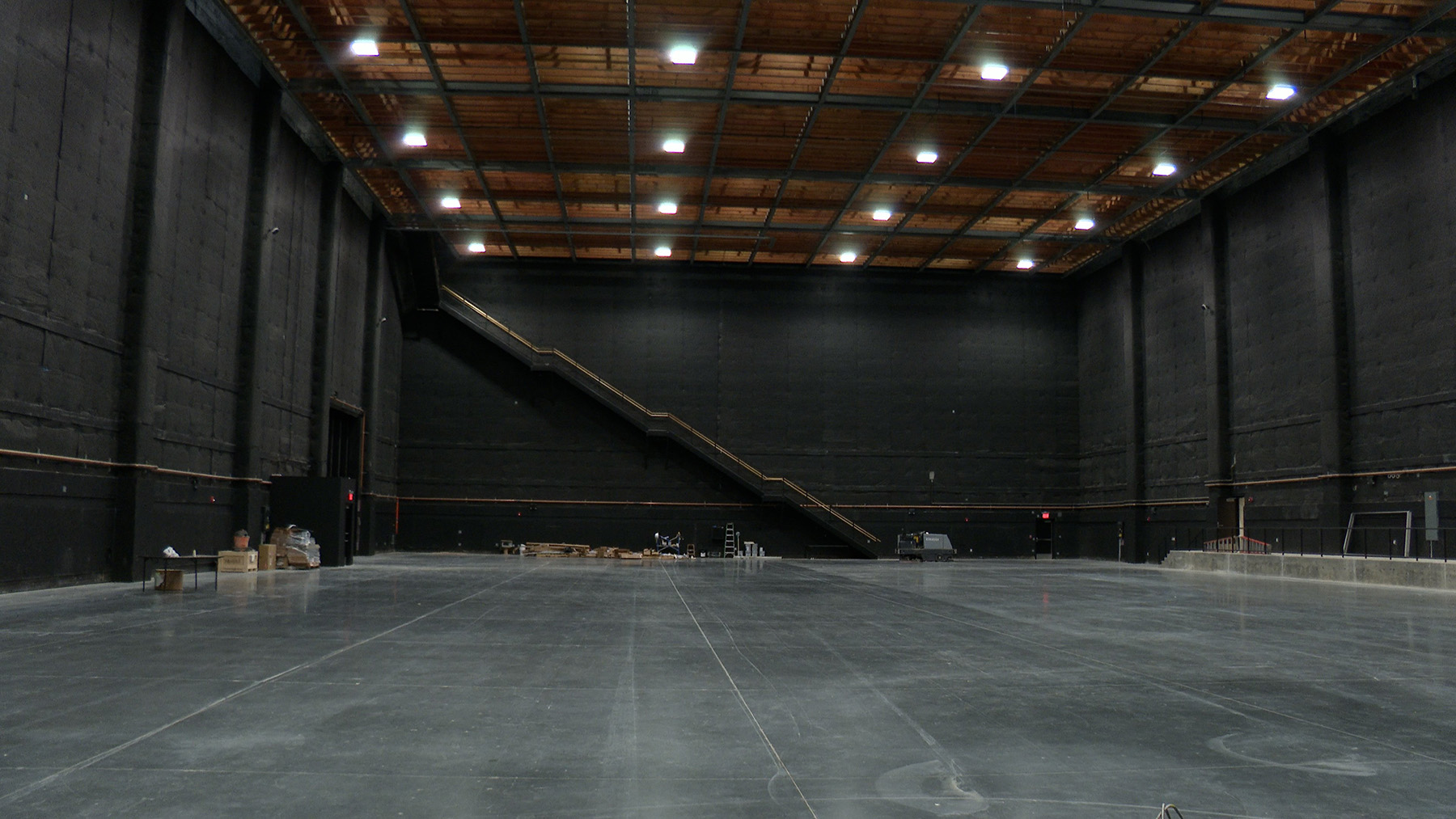
Smith Dalia Architects LLC led the project design team and PES Structural Engineers provided structural engineering services. Kimley-Horn was the civil engineer. UES conducted the environmental evaluation of the site, served as the geotechnical engineer, and provided concrete materials testing and special inspections during construction. HGOR was the landscape architect.
The project included two mechanical systems engineers — AHA Consulting Engineers and Westside Engineering — and two general contractors — Bailey Construction and Joe N. Guy Co. Inc.
Stormwater work
The Assembly Atlanta project features an approximately 43-acre triangular space in plan for the Assembly Studios complex, roughly in the northwest portion of the property, and an approximately 90-acre rectangular area for the public spaces to the southeast. A portion of an original road called Assembly Line Drive was reconstructed and extended to become Assembly Boulevard, which serves as a rough dividing line between the two parts of the project.
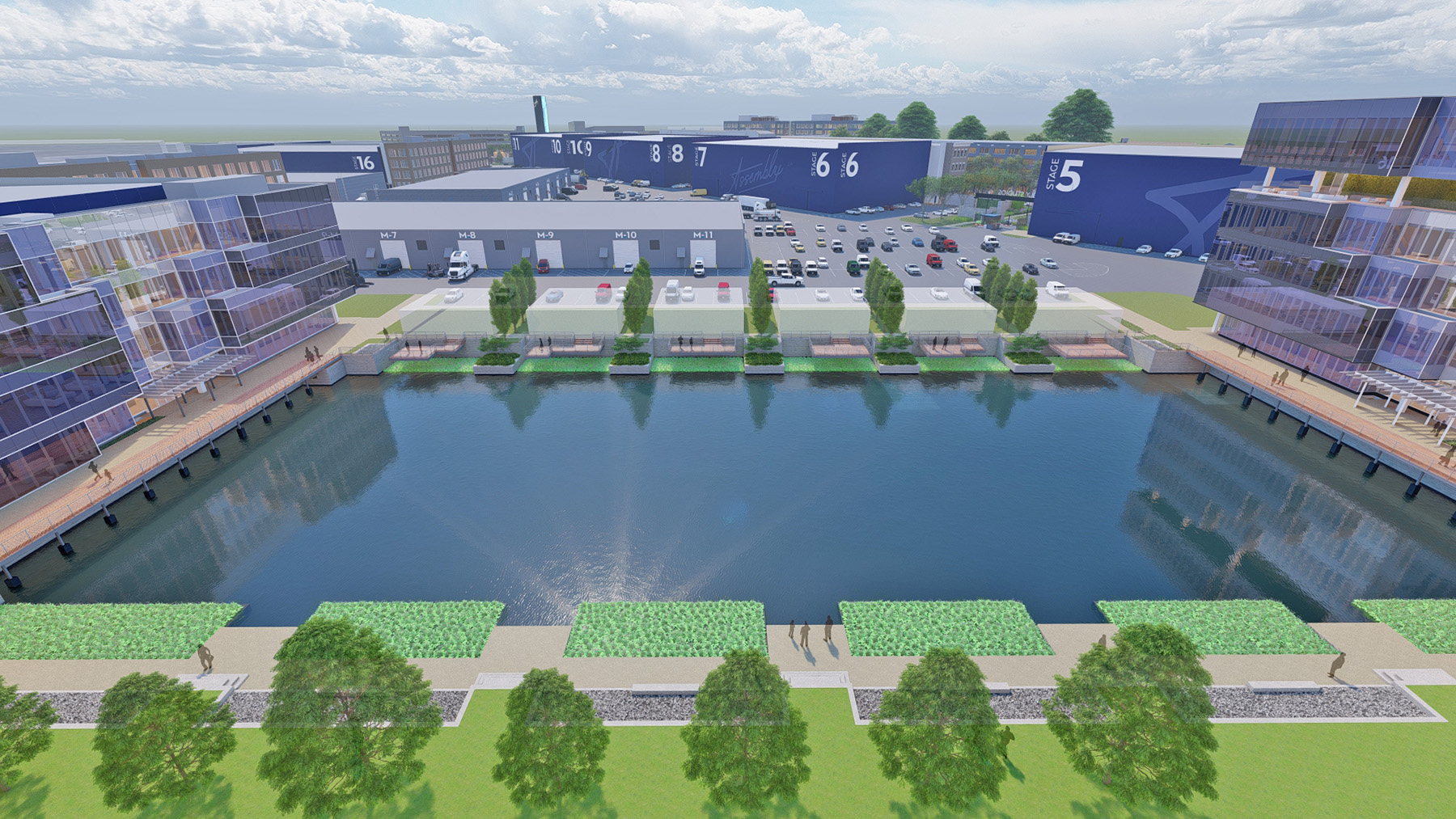
Kimley-Horn has worked at the site since the early 2000s, first with some of the previous developers and now with the Assembly Atlanta team, notes Blake Anthony, P.E., an engineer in the firm’s Alpharetta, Georgia, office. Initial efforts included rerouting some large storm sewers and coordinating the layout of other utilities for some of those smaller developments around Assembly Atlanta.
Because the overall site was fairly flat, a number of the original sewer lines had been buried deep underground to provide adequate space to slope for drainage, Anthony notes. Kimley-Horn had to carefully design the new lines for Assembly Atlanta’s two stormwater ponds so they did not conflict with any of the older systems that remained in place.
In addition to the two new ponds that Kimley-Horn helped design for the studio space and the public portion of Assembly Atlanta, the firm also built a retaining wall for one of the existing ponds to increase its volume from 267,000 cu ft to 698,000 cu ft, notes Reid Irwin, P.E., a senior project manager in Kimley-Horn’s Alpharetta office. The stormwater systems for the studio and the public spaces drain to a stream at the northern end of the site, Irwin adds.
The studio stormwater pond is rectangular in plan while the public stormwater pond will feature a more organic, oval shape. Both are designed to contain a certain level of water at all times, similar to a reflecting pool, but they are surrounded by concreted or landscaped spaces that will flood during heavy rainfalls. The studio pond can ultimately hold up to 828,000 cu ft of water during storms and the public side pond will have a capacity of 842,000 cu ft. Both feature concrete slabs that can support the weight of a vehicle driven across it, but only the studio pond — dubbed the “water stage” or “wet stage” — is intended to be used for filming movie and TV scenes involving water, says Irwin.
Kimley-Horn also modeled the project’s water pressure and flow needs for domestic consumption and firefighting services using the WaterCAD V8i software system from Bentley Systems Inc., of Exton, Pennsylvania. This led to the installation of pumps to create a network of pipes called a dedicated fire loop for the hydrants and sprinklers within the studios, Irwin notes. In addition, Kimley-Horn employees developed traffic and transportation studies for the project, examined a flood plain and wetlands habitat in the northwest portion of the site, and provided other services.
Soil solutions
The geotechnical conditions at the site were poorly documented, with potentially unsuitable soils for the planned structures, notes Scott Thomson, P.E., a vice president and principal engineer at Contour Engineering, a UES company. So the firm performed more than 100 soil test borings that determined variability, rather than unsuitability, was the issue, Thomson says. There were hard and soft zones, perhaps from the demolition of the original GM buildings, after which “someone may have just pushed soil into a hole,” he explains. “The soil might have been fine material, but they didn’t compact it.”
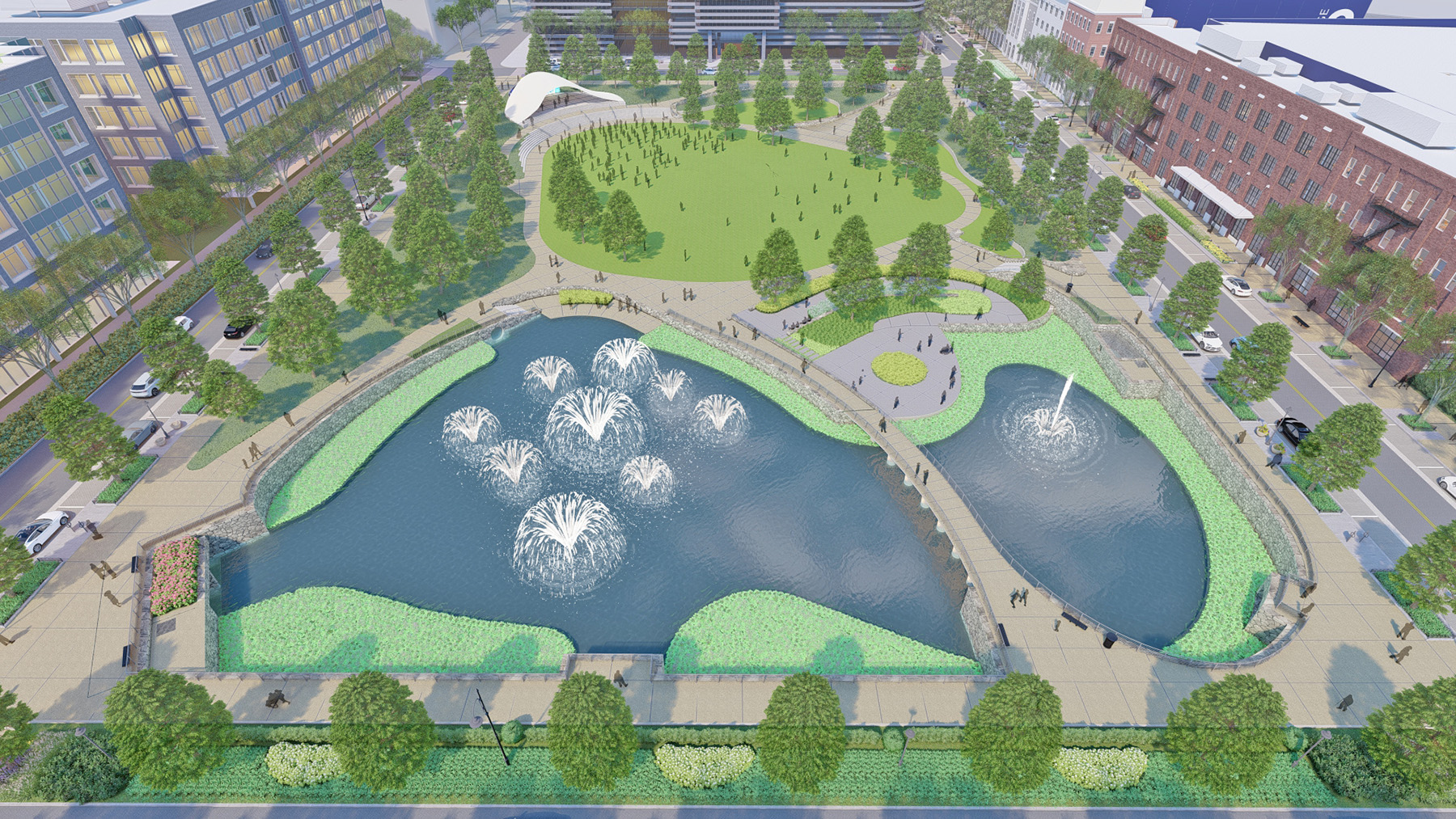
To prepare the site for the new studio structures, UES stabilized some of the soil with lime and directly beneath the eight studio buildings installed aggregate vibrated stone columns that densified the soil in all directions around the columns. The columns were installed to depths ranging from 10 ft to 25 ft in holes that measured 30 in. in diameter, adds Tyler Smith, P.E., a Contour project manager.
An extended period of rainy weather created areas of wet soil as well, Thomson adds. To keep the project on schedule, this wet soil was used as fill in two locations and then remediated with the stone columns. “Usually, you don’t create ‘bad’ fill to fix soil problems,” he adds, but in this case “we felt it would help the project timing.”
UES also conducted materials testing on the concrete mixes and the steel elements, especially for the large girders used in the studio buildings, Thomson says.
Supporting structures
The Assembly Atlanta studio buildings each measure approximately 300 ft long by either 120 ft or 150 ft deep. Six of the studios reach a maximum height of about 65 ft — to accommodate a 50 ft internal clearance to the underside of the roof structure needed for movie productions — while two have a maximum height of roughly 55 ft to provide the lower clearance required for making television shows, says Erik Swerdlow, P.E., S.E., a senior associate at PES. The studio buildings feature large, open spaces inside that, in some cases, can be subdivided by temporary walls to accommodate the filming of one or two movies or TV shows at the same time.
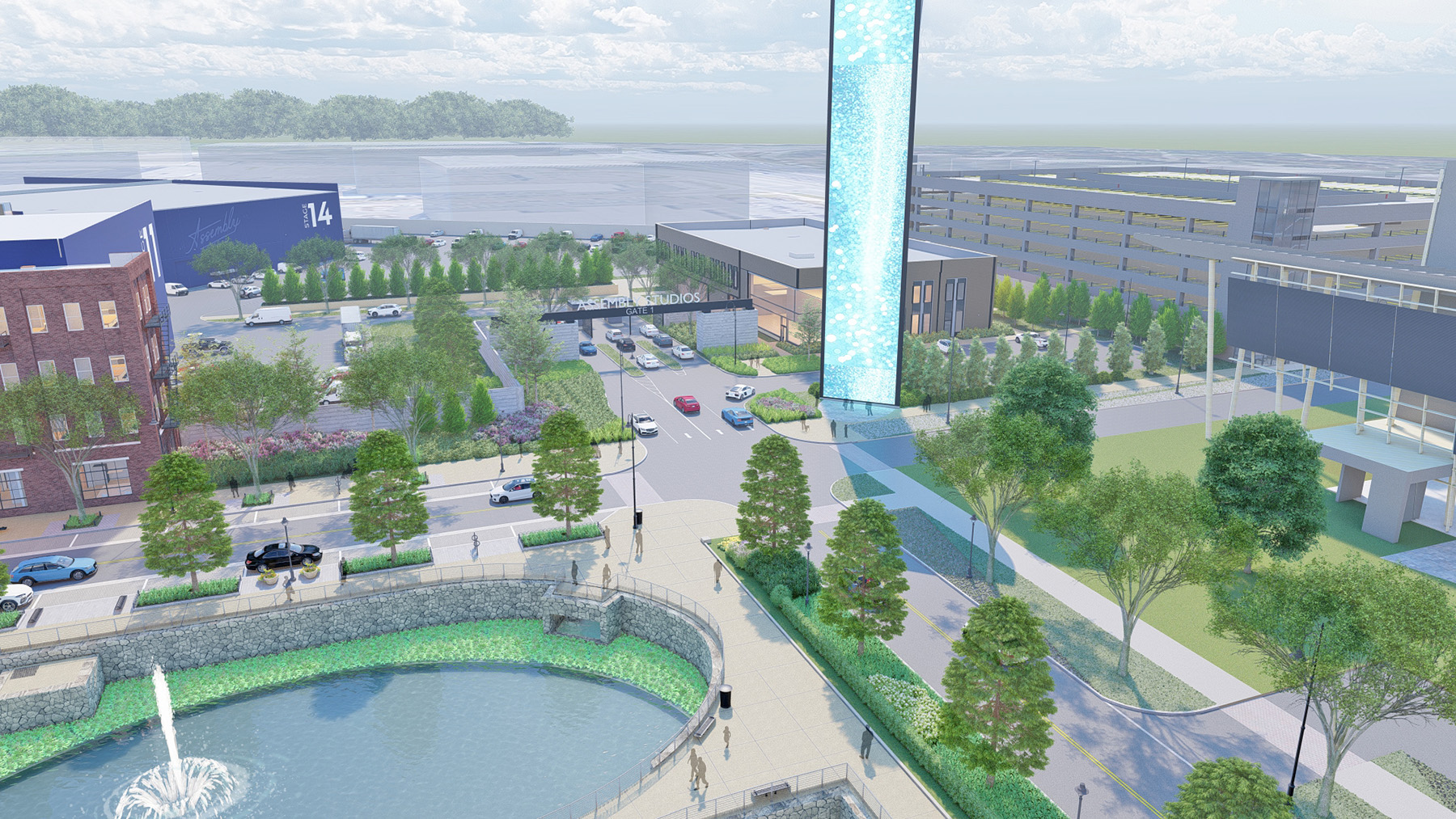
Framed in reinforced-concrete panels that measure roughly 40-60 ft tall — to accommodate roofs that slope for drainage — and 9-15 ft wide, the studio buildings were constructed using the tilt wall method. This means the panels, which weigh as much as 170,000 lb, are cast on-site and then raised and tilted into position by a crane. The panels were either cast directly on the foundation slab of the building they were used with and then lifted into position, or they were cast on a separate, temporary casting bed and then moved to where they were needed, Swerdlow says.
The roofs of the studio buildings feature steel trusses that measure 10-15 ft deep because of the roof slope. The trusses support a concrete roof deck — for better acoustics inside the studio spaces — and bear on the tilt walls. The trusses are aligned at 30 ft intervals, and the wall panels that support them feature additional framing in the form of a columnlike concrete pilaster, Swerdlow says.
All the concrete tilt walls measure 11.25 in. thick, which will help provide soundproofing. Although the proximity to train lines, highways, and DeKalb-Peachtree Airport made the site “a very attractive location” for movie and television studios because there were multiple modes of transportation for bringing in production crews and equipment, it also “meant a lot of different sounds — the rumble of trains, the traffic hum, the noise from being in the flight path for small aircraft,” Swerdlow says. So the acoustician — Sonics ESD — “came multiple times to take readings to help determine the correct sound protection for the buildings,” Swerdlow explains.
The wall panels will serve as the lateral- and gravity-load-supporting systems for the studio structures. The panels also support a network of fire-treated wooden joists that form catwalks and a floor area called the perm level to which lights, set rigging, and other equipment are attached. The system is framed in wood because “the rigging operators are working with live electrical wires, so we don’t want them to discharge on anything,” Swerdlow explains.
The studio buildings are fronted by four-story-tall office structures, approximately 45 ft deep, that are separated from the studio structures by movement joints, Swerdlow says. Framed in steel, these facilities will provide production offices for the films or television shows being made in the studio at any given time along with dressing rooms, editing rooms, and other support spaces.
Filmable facades
Six of the studio buildings feature what the design team calls filmable facades. This means the fronts of these office structures can serve as backlot spaces to film outdoor scenes. One resembles a series of attractive brownstone buildings in New York City, while another features a grittier section of Manhattan with exposed fire escapes. A third represents the French Quarter in New Orleans, and a fourth looks like a European streetscape. Two others, located elsewhere on the studio site, feature glazed exteriors.
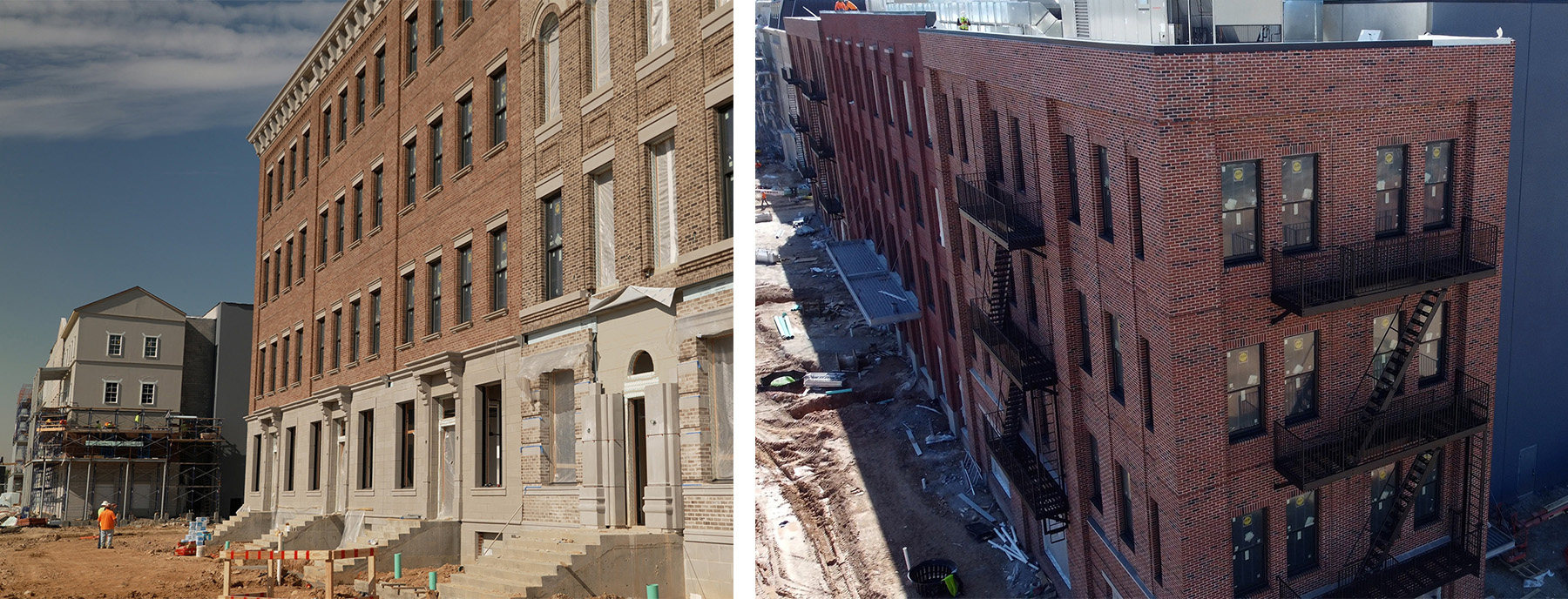
Although the filmable facades are purely set pieces, the aesthetic details posed some structural challenges, Swerdlow says. For example, the balconies on the New Orleans buildings had to be framed through the veneer of the facade and secured to the office structure to support the weight of the actors who might stand on them.
Most of the studio complex will be fenced off from the public spaces within Assembly Atlanta, but the four filmable facade buildings along the main thoroughfare that runs through the development will offer visitors a special amenity. While the street itself will be closed to traffic during filming, the public will be able to watch from nearby, Swerdlow says.
Other structures within the studio portion of the project include a two-story administration building with rehearsal space, a cafeteria, other amenities, and the mill buildings, which are framed in concrete masonry unit blocks and have steel roofs. The mill buildings feature large roll-up doors for moving set pieces in and out.
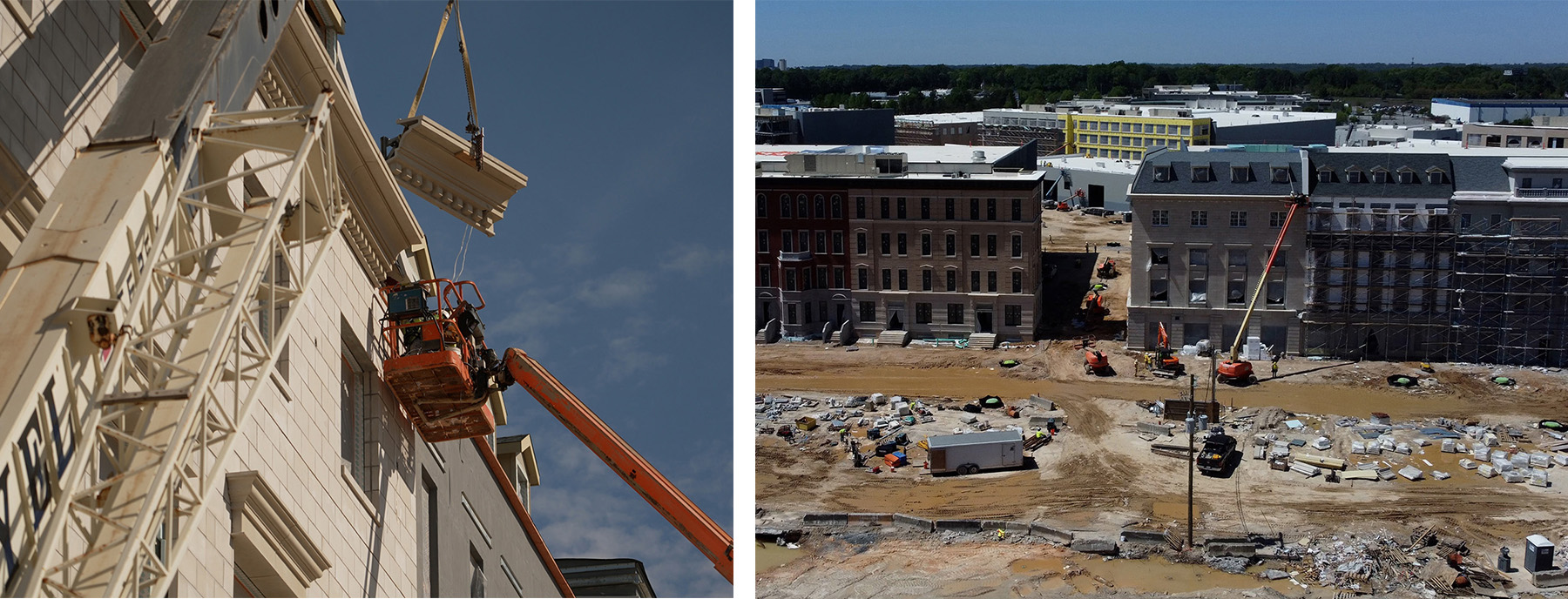
PES designed the deep foundations for a concrete-framed parking garage on the studio side of the project. Metromont designed the six-level parking structure, which features an especially tall ground level to accommodate large trucks. But PES designed the auger-cast piles that are more than 30 ft deep to support the heavy loads of the garage. The firm also designed the foundations to accommodate a centerpiece element dubbed the iconic tower: a 140 ft tall steel-framed structure near the parking garage that will support digital screens for advertisements and announcements. Triangular in plan, the tower features bolted braced frames and is supported on auger-cast piles more than 30 ft deep, Swerdlow says.
Playing a part
The Assembly Atlanta project followed a fast schedule, moving from groundbreaking to construction of the studio portion in just two years, Swerdlow notes. The design and construction teams met on a weekly basis during that period, with the number of participants in the daylong meetings — as well as the rooms in which the meetings were held — growing larger as the work progressed. It was a challenging project, but in the end it all paid off, he says.
“I drive by the site every day, watching it come to be and knowing I was a small part of the entertainment industry here in Georgia that’s been booming!” Swerdlow notes. “So I can’t wait to take my family to the movies and say, ‘I recognize that backdrop! That’s the New Orleans building or the New York building, and I helped design that!’”
Robert L. Reid is the senior editor and features manager of Civil Engineering.
Project credits
Clients: Gray Television and the Gipson Co., Atlanta (both)
Architect: Smith Dalia Architects LLC, Atlanta
Structural engineer: PES Structural Engineers, Atlanta
Civil engineer: Kimley-Horn, Raleigh, North Carolina
Geotechnical engineer, environmental evaluation, concrete materials testing, and special inspections: UES, Orlando, Florida
Landscape architect: HGOR, Atlanta
Mechanical, electrical, and plumbing engineers: AHA Consulting Engineers and Westside Engineering, Atlanta (both)
General contractors: Bailey Construction, Alpharetta, Georgia, and Joe N. Guy Co. Inc., Marietta, Georgia
Acoustician: Sonics ESD, Monterey, California
This article first appeared in the November/December 2023 print issue of Civil Engineering as “Hollywood and Peachtree.”