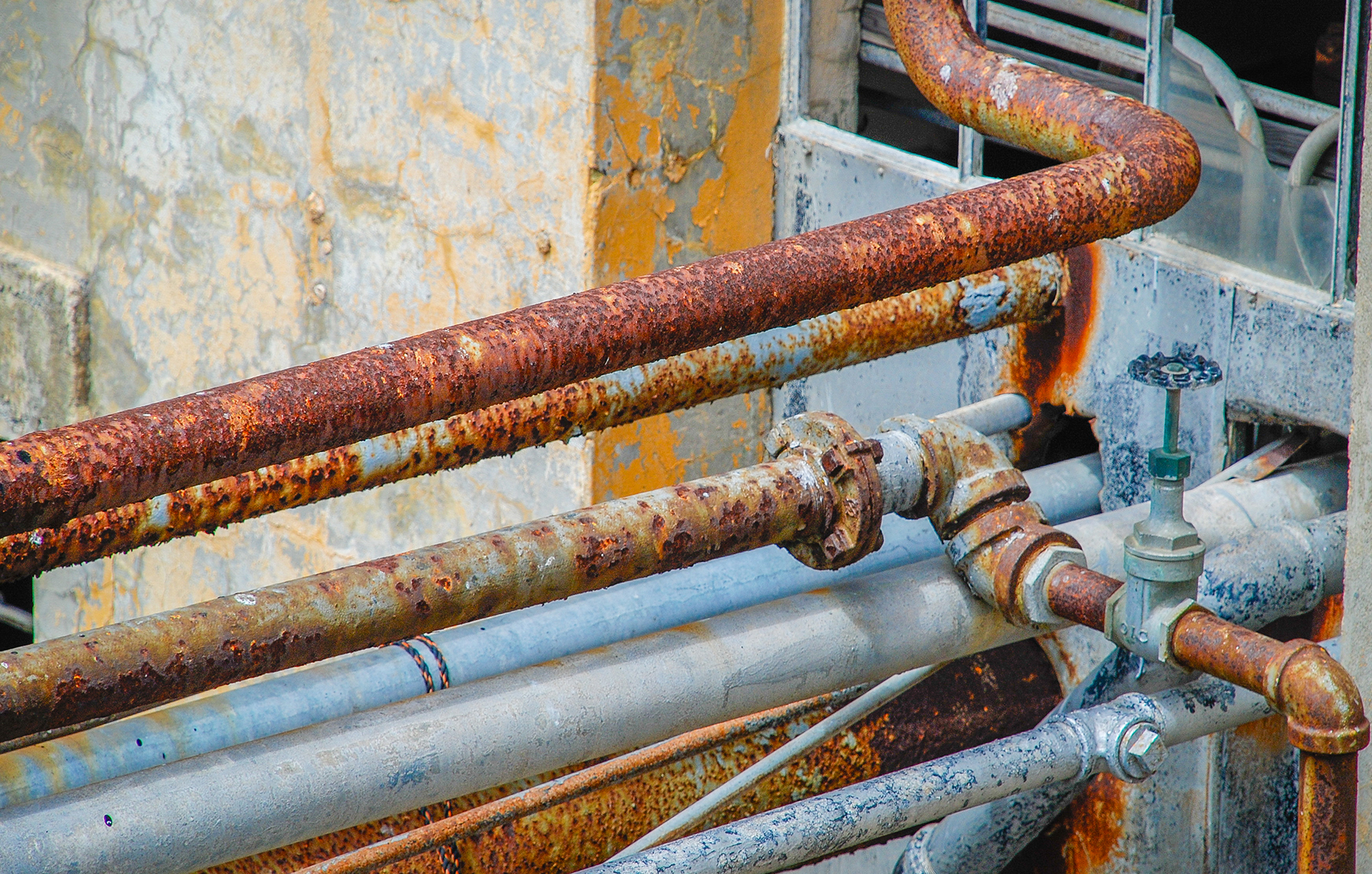
Many of the buildings and other infrastructure in the U.S. date to the 1950s and 1960s, when a post-World War II economic boom spurred the construction of then-modern facilities.
Today, this aging infrastructure presents hidden risks and significant challenges for insurance and legal professionals tasked with resolving claims related to physical failures that cause substantial losses. Forensic metallurgical failure analysis plays a critical role in unearthing the root causes of these problems, minimizing their financial impact, and mitigating future risks.
A big challenge
In major cities across the country, the heating, ventilation, and air-conditioning infrastructure in many office buildings, hotels, and other facilities are nearing or are past the end of their intended lives, with their original piping and other mechanical systems still in place. Often, the design and construction decisions made 60 or 70 years ago create problems that become complicated and expensive to solve, and they aren't always evident until a failure occurs.
Further reading:
- An unintended consequence of energy-efficient structures: Mold
- That sewer system ‘rotten egg’ smell is corrosive to pipes
- Can basalt fiber-reinforced polymer repair underwater steel corrosion?
For example, many postwar office buildings incorporated then-cutting-edge dual-temperature HVAC systems that used extensive networks of small-diameter piping around the perimeters of buildings. Degradation over time and building renovations have often resulted in flow and chemical water treatment variations.
Insulation deterioration can also cause corrosion attack on piping outer surfaces, as well as render the systems vulnerable to freeze-thaw events. When an HVAC piping failure occurs, it sets off several complex questions.
How do you identify the source of a behind-the-wall leak with high accuracy, extreme precision, and minimal disruption to tenants and other occupants?
If it is determined that the problem is endemic to the system, do you tear down walls and replace the original piping or abandon the original material and use more modern technology to install new HVAC systems in more accessible areas, like ceiling ductwork or wall-mounted units?
When an insurance claim is involved, how do you determine which party is liable for the failed component and subsequent damage?
Questions like these demand the expertise of highly skilled engineers in forensic metallurgical evaluation, including corrosion assessment and failure analysis.
The value of skilled evaluation
Forensic engineers are often called in to resolve situations like these on behalf of building owners or insurance companies, and they sometimes work with legal counsel. Engineers with experience in metallurgical evaluation can precisely identify the root cause of an infrastructure-related failure, determining whether it was a material flaw, an installation error, an environmental factor like freezing temperatures, or decades of service degradation. Then, they can recommend practical, cost-effective solutions that minimize expensive business interruption and avoid recurrences.
Forensic engineers are also tapped to proactively prevent mechanical and structural failures – either by assessing their conditions and recommending preventive measures or by advising building owners and project developers on which materials to avoid to reduce the risk of failure.
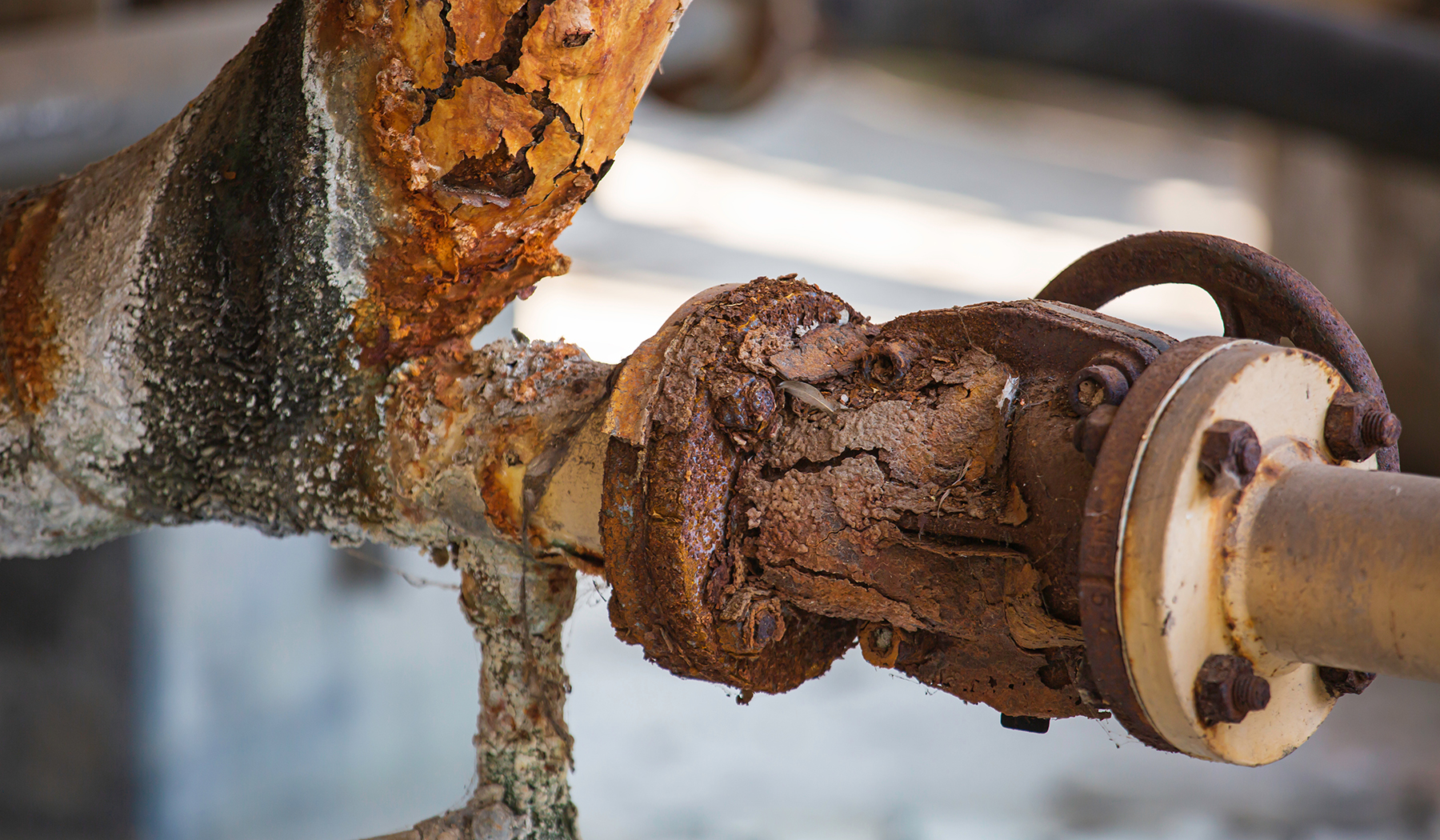
The economic value of a forensic metallurgical evaluation is typically significant. Consider a water leak in a luxury high-rise condominium in New York City, which caused extensive property damage to dozens of residences, including flooring, high-end appliances, and irreplaceable artwork. The damages totaled over $20 million, prompting a significant insurance claim. (Similar leaks in high-rise hotels have necessitated repairs that take dozens of rooms out of service for weeks, resulting in substantial lost revenue for the properties.)
The condominium developer’s insurer needed to identify the cause of the leak and determine whether the manufacturer or the installer was liable. The forensic metallurgical evaluation concluded that the leak occurred due to a brass valve that fractured at an internal threaded connection – a $7 component susceptible to stress corrosion cracking.
Other materials commonly used in prewar buildings are also subject to failure, often many years after installation.
Domestic water piping made of yellow brass is highly susceptible to dezincification – a situation where, over time, zinc leaches out of the brass alloy and leaves a porous copper pipe wall where water can weep through. This has been a common problem in buildings constructed in the early 20th century before pure copper alloy piping became the norm.
Since there is no apparent visible crack, it takes a skilled forensic engineer with metallurgical failure analysis experience to identify the problem and recommend how to solve it.
What the investigation involves
Following the evidence is the key to identifying and resolving a metallurgical problem in an aging building. While an initial hunch might suggest a cause, there is no substitute for detailed, objective analyses using the most advanced technology and led by a highly experienced forensic engineer. That’s the best way to obtain reliable, evidence-based findings that stand up to legal scrutiny.
While every project is unique, metallurgical failure analysis typically involves examining the affected component in a fully equipped lab. An experienced engineer will perform a microscopic examination to look for physical features indicative of the fracture mode or type of corrosion degradation, conduct chemical analyses of corrosion deposit materials, and perform other tasks, including compositional analysis and mechanical testing.
Consider an example in which the failure involves a section of piping. In such a case, the engineer would guide and assist the building owner or facilities manager on where and how to remove and transport the affected item to the lab.
Examining and testing physical components proves very telling because how a material degrades or fractures often effectively provides a fingerprint of its failure mode. The appearance of the fracture surface will be different based on the cause of the problem, such as whether it was bent/overloaded, installed incorrectly, sustained stress corrosion cracking, was exposed to extreme temperatures, or suffered a fatigue fracture caused by vibration.
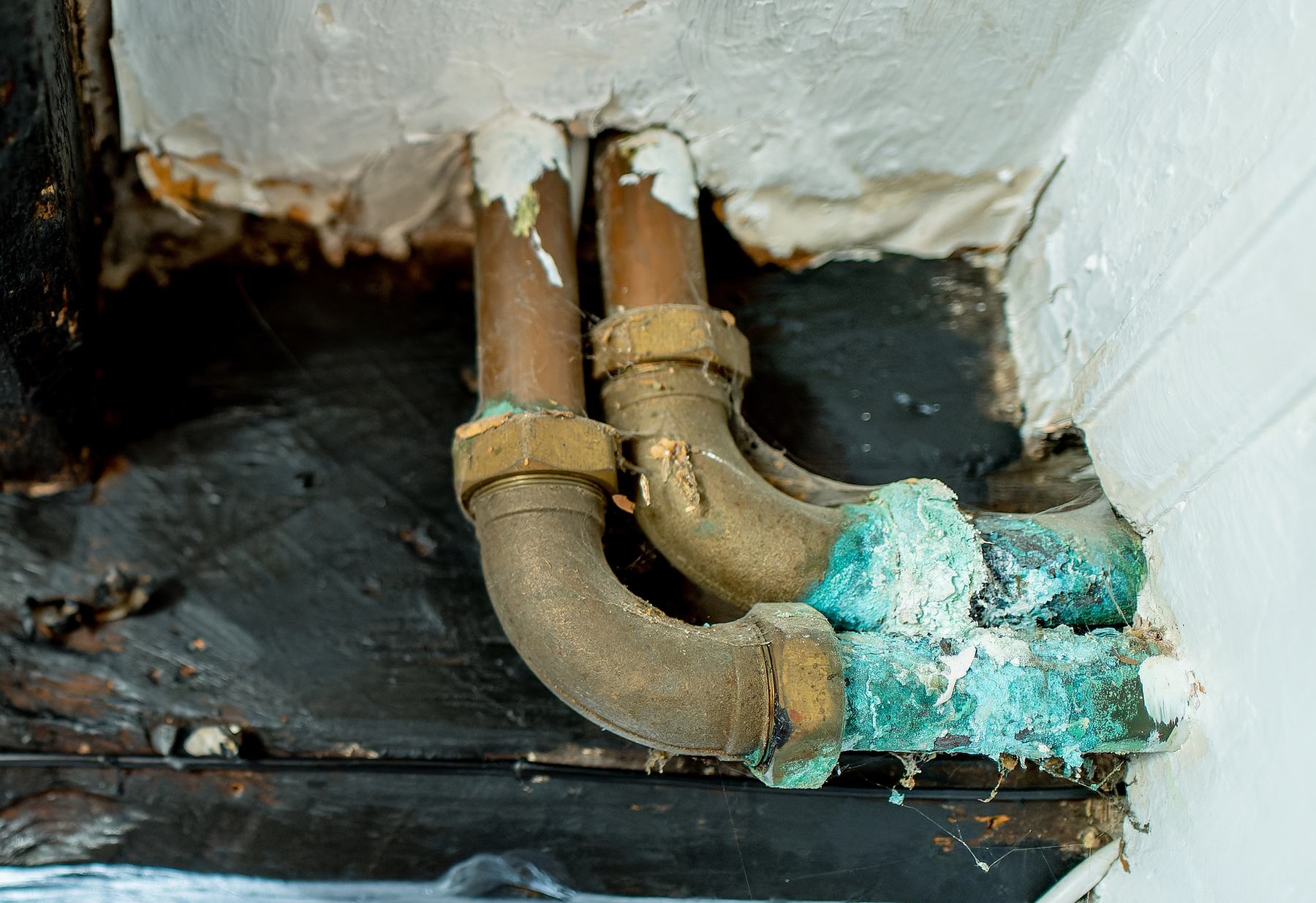
Advanced testing techniques also help engineers determine the alloy composition of the material, which is invaluable since some alloys are more susceptible than others to certain types of failure.
Once the metallurgical evaluation is complete, at the client's request, the forensic engineer prepares a detailed report documenting all observations and test findings, provides definitive conclusions on the cause of the failure, and offers recommendations for resolving the problem and avoiding a recurrence. In the case of an insurance claim, the report must provide sufficient evidence to help the carrier determine which party is at fault and facilitate a settlement, ideally avoiding the cost of a trial.
Forensic engineers are highly experienced at assessing damage and losses involving new construction projects and aging buildings, structures, and systems; identifying the root cause; and recommending practical solutions. Leading businesses, utilities, insurance companies, and law firms rely on those engineers’ expertise to help investigate what happened, why it occurred, and how best to resolve the situation.