By David Jen
Recent travelers on east London’s Leaway footpath may have seen a bridge with iconic, vertical square hoops roll over onto its side and then upside down as they waited to cross the ex-industrial Cody Dock. The inversion, however, need not have caused any worry, as the bridge — the first of its kind — rolls to raise the height of its deck for boats underneath.
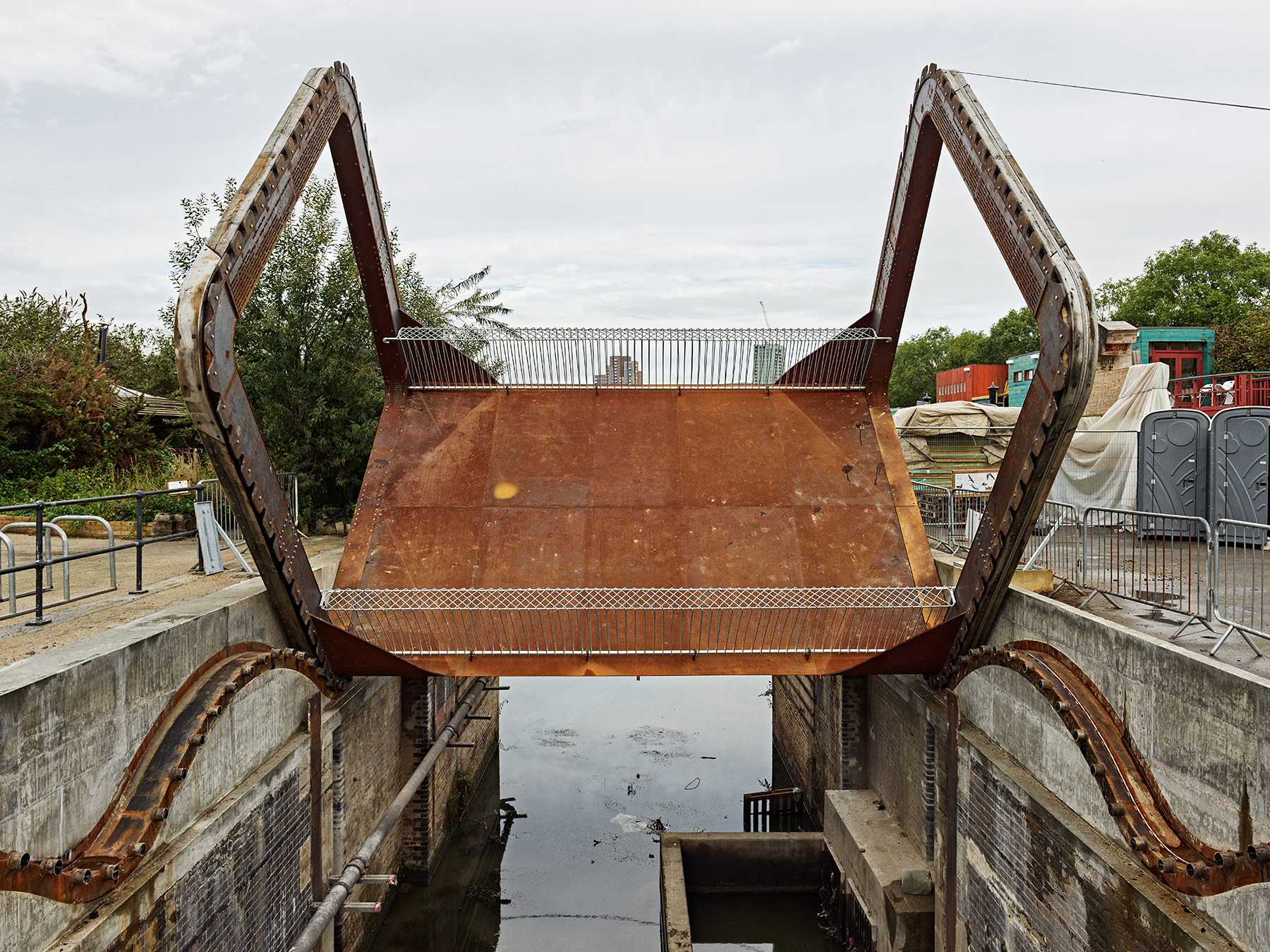
The installation of the Cody Dock Rolling Bridge in August concluded an eight-year design journey involving a playful idea, strict tolerances, and some tricky math.
“It's kind of one of those mad ideas that’s actually come to fruition,” says David Knight, CEng, MICE, MIStructE, the design director of London-based Cake Industries.
The bridge rotates using the two vertical square hoops, which are geared along their outer edges. These enable the entire bridge, made from weathering steel, to ride along a curved track with peaks and valleys built into the dock abutments. And because the bridge deck joins the hoops along one side, the roll lifts the deck by the height of the hoops — about 5.5 m — when inverted.
“There's a real charm to the square rolling because you just really don't expect that to happen,” says project architect Thomas Randall-Page, who partnered with structural engineers at Price & Myers, mechanical engineers at Eadon Consulting, and fabricators at Cake Industries for the project.
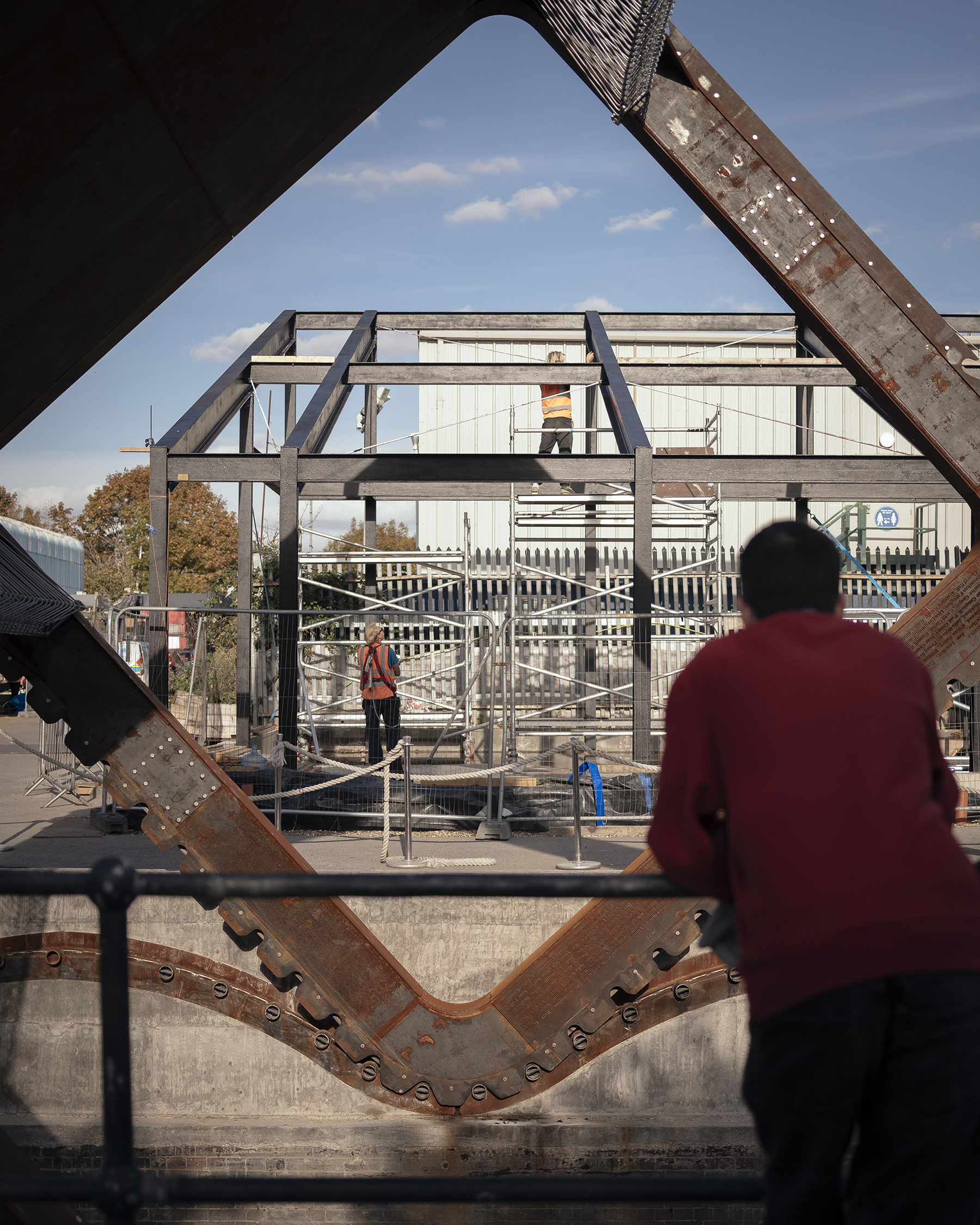
The square shape, in addition to the element of surprise, offers practical benefits over a simpler, circular rack-and-pinion design.
“A square … doesn't actually have to travel as far (as a circle would),” explains Knight. “And if you want to constrain the site, that meant you could just squeeze it in and you are efficiently using that space for people to walk.”
The idea for the novel design originated from a weeklong trip taken by Randall-Page in 2014, during which he helped a friend move a boat through a series of canals.
“I spent a lot of time on the roof of the boat sketching and then periodically jumping off and helping her go through locks,” says Randall-Page. “And it got me thinking a lot about Victorian infrastructure and how it's kind of super low tech in one sense, but it's also really smart in that there's not a lot of energy. They didn't have the ability to plug in, like we do now to power sources, so they had to be much smarter with the physics of things.”
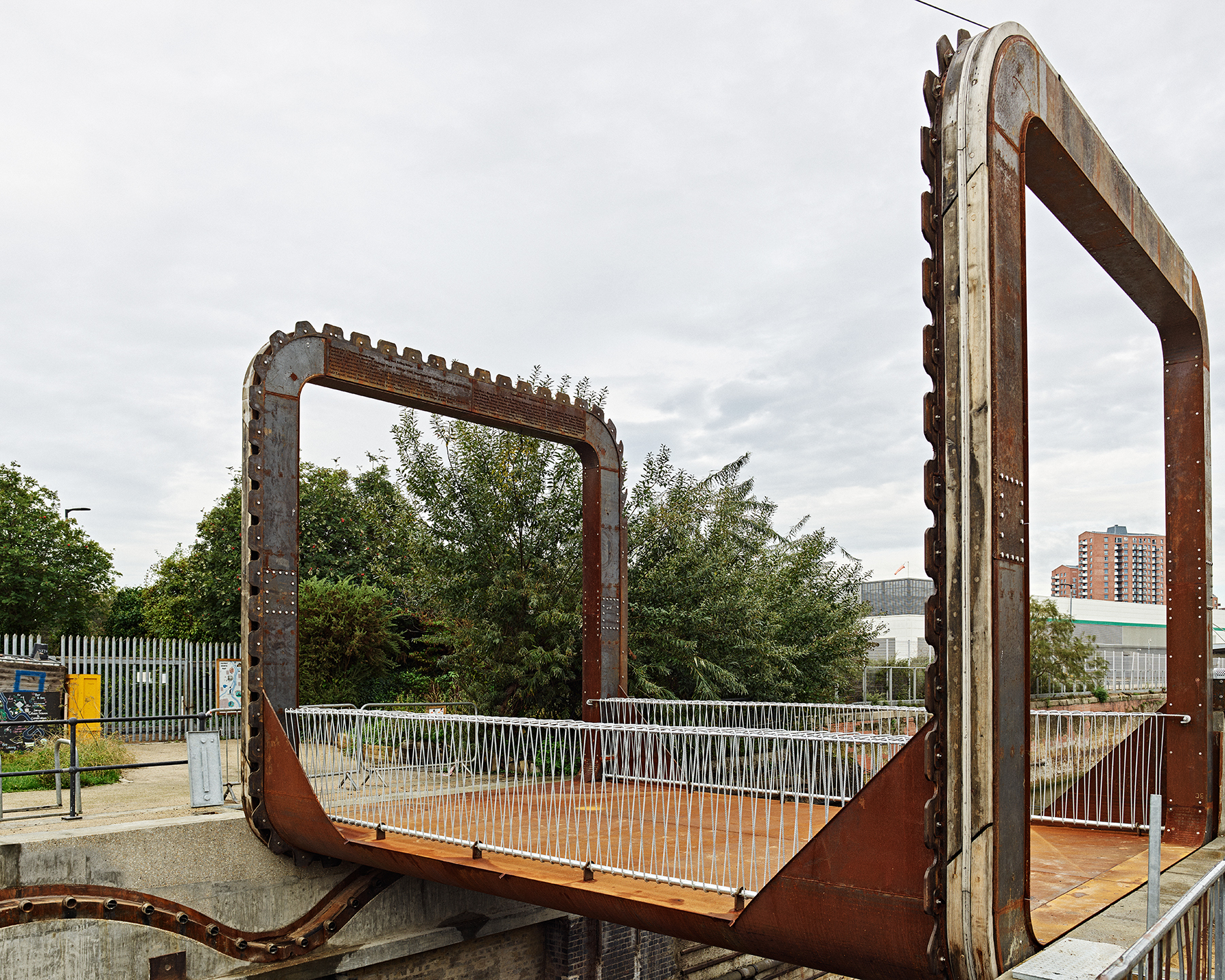
The hand-powered Cody Dock bridge relies on a counterweight consisting of scrap concrete and rebar within the top hoop segments to align its center of mass with its rolling axis. Human-powered hand winches alone move the 13 metric ton bridge through its roll.
“The cable is just to overcome inertia — to get it just to move — and to overcome wind forces which, in the end, ended up being a big factor,” says Randall-Page.
To design the bridge’s tracks so that the rolling axis could remain level throughout its inversion, the design team built off work by Stan Wagon, Ph.D., professor emeritus of experimental mathematics at Macalester College. A 1992 article for Mathematics Magazine co-authored by Wagon, titled “Roads and Wheels,” explored theoretical non-circular bicycle wheels and the road shapes they could ride on. For square wheels, the article described a road of truncated, inverted catenaries.
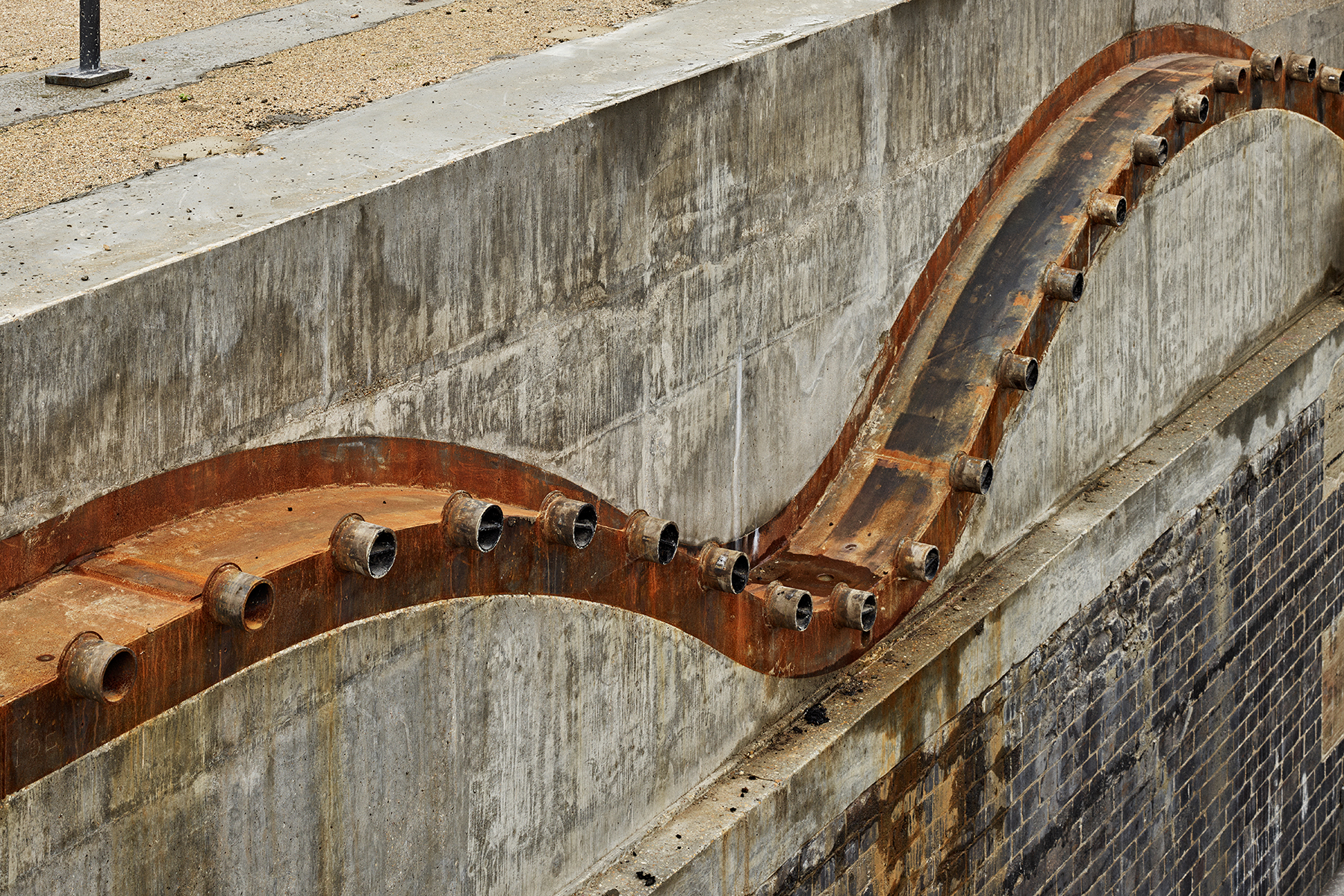
Wagon’s thought experiments, however, assumed sufficient traction between the wheels and the road when, in reality, real-world slippage necessitated the large teeth seen on the Cody Dock bridge.
“Friction was one of the big unknowns,” says project engineer Robert Nilsson, an associate at Price & Myers.
With a track originally envisioned with a serrated profile, the team later decided to isolate the bridge’s rolling surfaces from its guiding surfaces and used an oak sacrificial rolling surface with guiding pins along the tracks. The oak surface is straightforward to replace and expected to last 15-20 years.
The hoops’ rounded corners, while part of Randall-Page's original sketches, also helped avoid a real-world situation where the square corners would have scraped the track when they rolled through its valleys.
In the final design, catenary functions generate the peaks of the tracks, while elliptic integrals generate the valleys, says Nilsson.
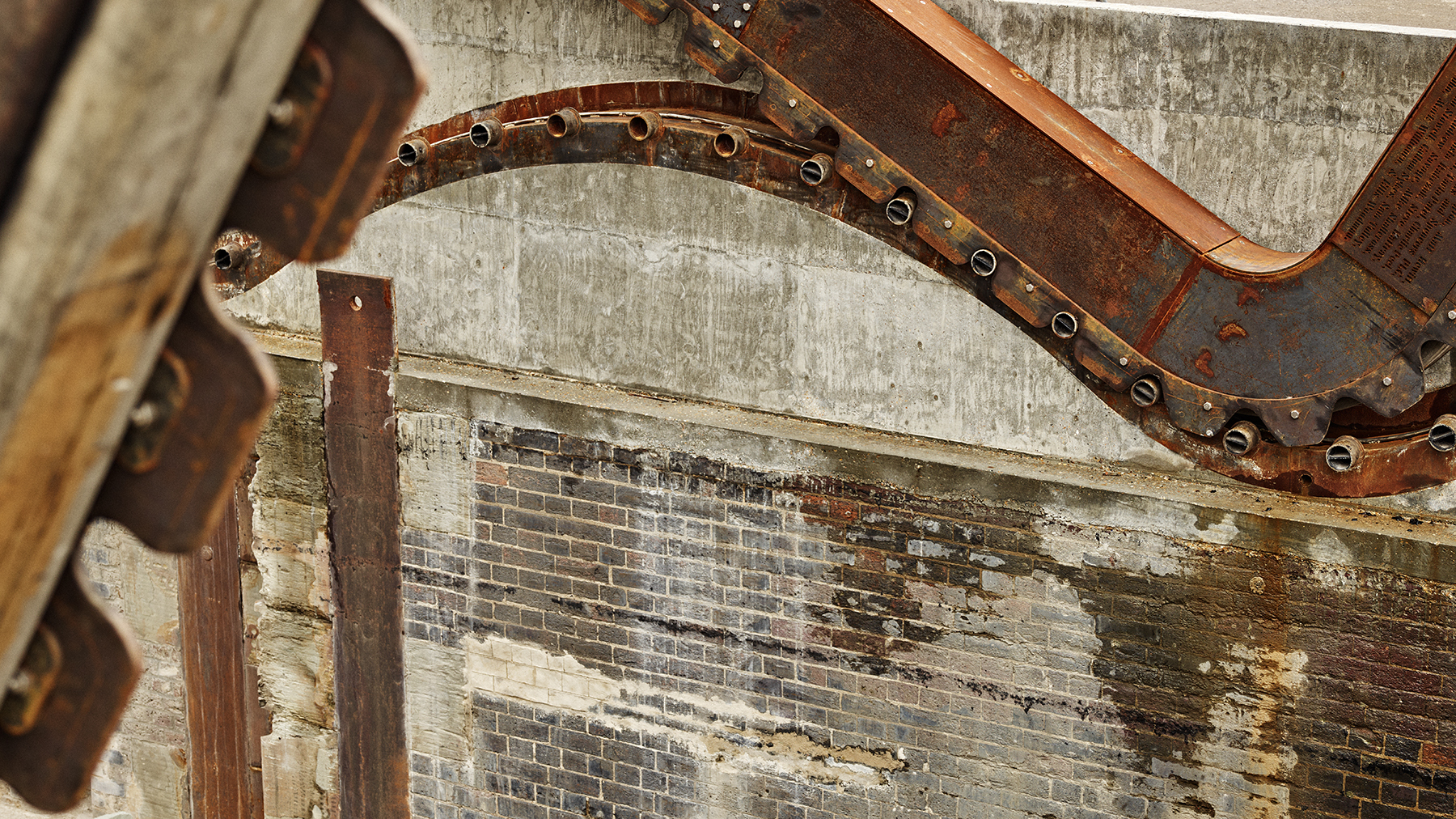
Fabrication challenges, meanwhile, stemmed largely from the large bridge’s tight tolerances.
“Normal civil engineering tolerances are about an inch for concrete, if you’re lucky, and probably 2 inches, whereas we were looking at translating into a quarter of an inch or smaller,” says Knight. Cake enlisted furniture makers for the accuracy they brought to the build.
The team developed the bridge for the Gasworks Dock Partnership, a London-based charity focused on “developing a community-based arts and creative industries quarter on the banks of the River Lea,” according to the Cody Dock website.
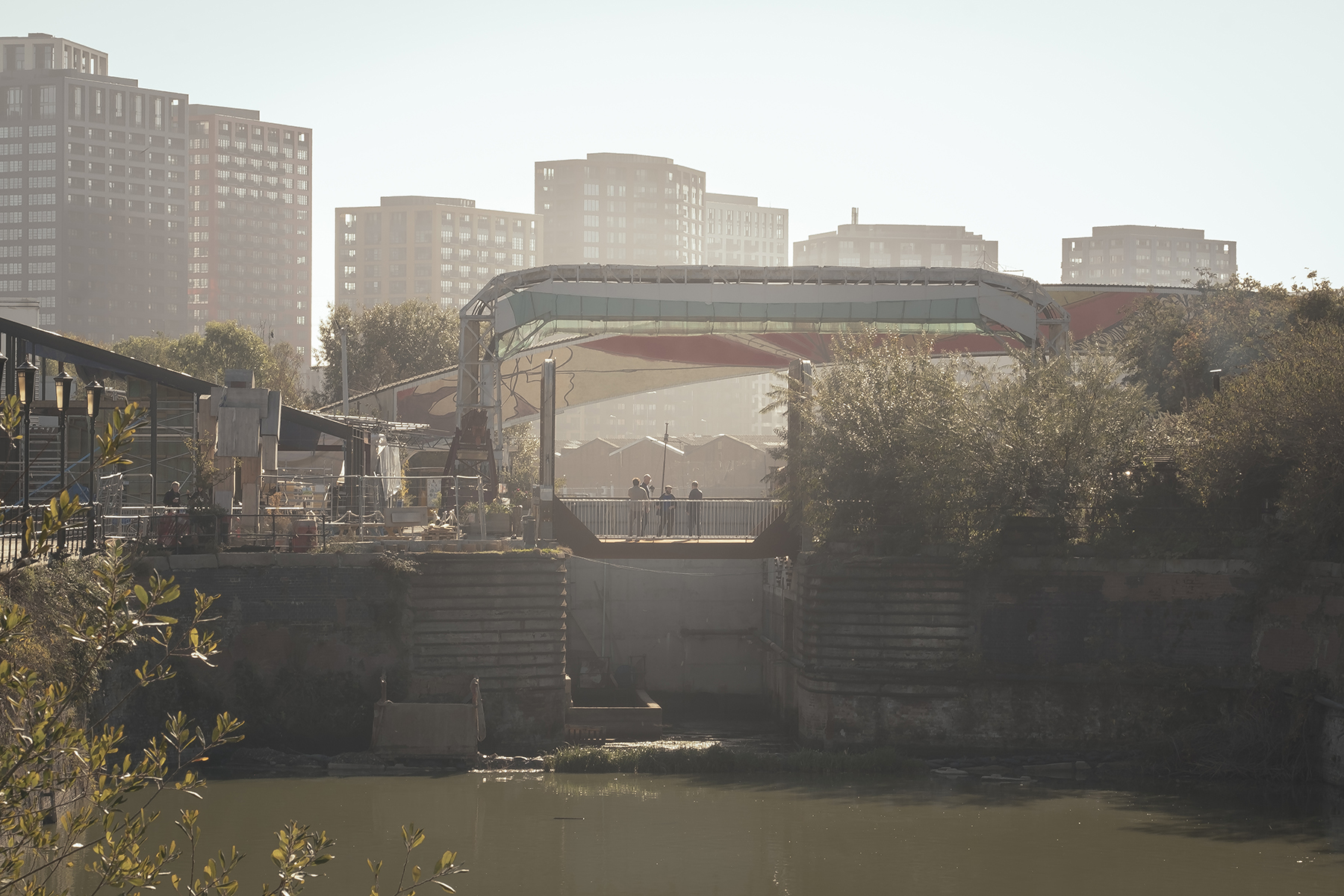
Project funding came from the National Lottery Heritage Fund, which distributes lottery ticket proceeds to projects that “sustain and transform the (United Kingdom’s) heritage,” according to the fund’s website.
While the dock currently remains dammed and dry for surrounding work, Randall-Page expects it to reflood and allow boat traffic in the next 12 months.
And when asked what might limit the size of the rolling design in future implementations, he replies, “Bravery, I think.”
This article is published by Civil Engineering Online. It appeared in the July/August 2023 print issue of Civil Engineering magazine as "Bridge, Inverted."