By Celeste C.B. Bennett
As the world gears up to meet net-zero carbon emissions goals in the next few decades, companies around the globe are thinking creatively and intentionally about the part they will play. For Utah-based Eco Material Technologies, the addition of fly ash that has been recovered from landfills will help create more sustainable concrete.
The U.S. Army Corps of Engineers began using fly ash mixtures in concrete in the late 1950s. The material is a byproduct left over when pulverized coal is burnt in coal-fired power plants. Fly ash, which is often sent to landfills, can be used as a 20% replacement for portland cement.
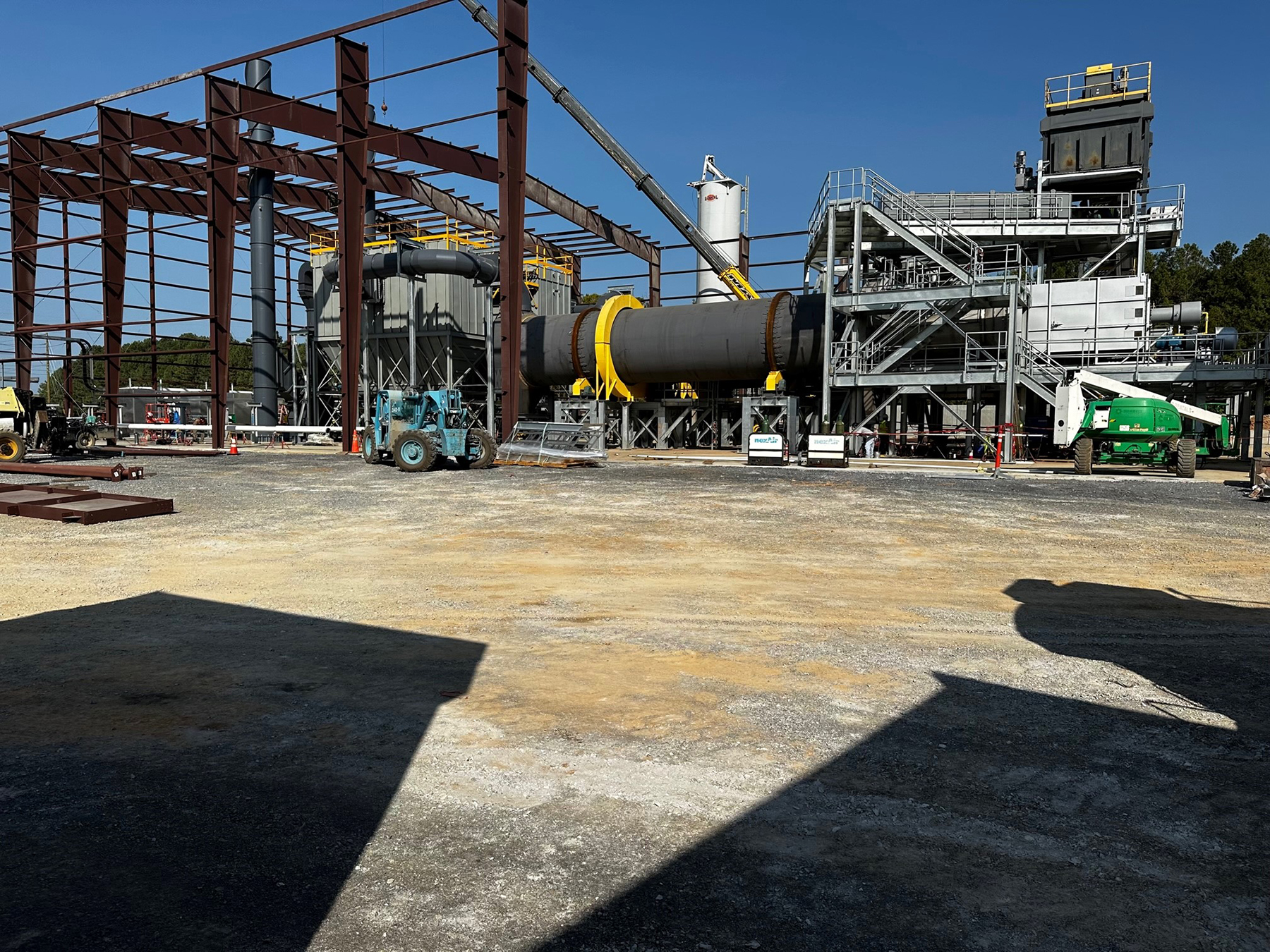
Rob McNally, the executive vice president and chief growth officer of Eco Material, says rather than collecting fly ash from the coal plants as it is created as a byproduct, his company has developed technology to harvest discarded fly ash from landfills and process it for use in concrete.
Why fly ash?
“When you replace cement with fly ash, let's say 20% by weight, you're reducing your overall emissions in concrete by more than 20% by weight. So that's (one reason) why its use is beneficial,” says Sriramya Duddukuri Nair, Ph.D., E.I.T., A.M.ASCE, an assistant professor in the civil and environmental engineering department at Cornell University.
“It varies, depending on which plant you're at, but with portland cement production, 1 ton of cement is associated with around 0.9 tons of CO2 that's emitted during production … and if it's fly ash, the value is around 0.03 tons of CO2,” Nair says.
While the beneficiation and transportation of landfilled fly ash can contribute to emissions, overall, using the material still results in much lower carbon emissions, according to Nair.
Fly ash-cement mixtures make concrete stronger in the long term, over and above mixtures that just use portland cement, says Nair. One reason is because switching cement for fly ash means less water needs to be used for the mix due to fly ash’s composition.
“Using less water to lower the water-to-cement ratios means that you can make your concrete more durable and stronger using fly ash. The overall long-term performance and compressive strength can be higher,” she says. A lower water-to-cement ratio also means the material is less permeable and will better withstand extreme conditions after it’s placed.
Reclaiming fly ash
Once the reclaimed fly ash has been transported from the landfill to the Eco Material facility, it is analyzed for durability and chemical composition, tested for regulatory and commercial requirements, and prepared for use in concrete through drying and grinding.
The company has its own fleet of trucks and more than 400 train cars to transport the prepared fly ash to concrete companies and construction projects across the country.
Eco Material has partnered with Georgia Power to source landfilled homogenous fly ash created by Plant Branch, the power company’s former coal-fired power plant that closed in 2015. McNally notes this kind of ash is more effective in concrete than other kinds because of its ability to prolong the life of concrete structures.
Fresh fly ash and landfilled fly ash perform equally well in cementitious mixtures, according to McNally.
As more coal-fired power plants are retired over the next few decades, McNally says the quantity of available “fresh” fly ash will decrease. However, the work his company is doing to prepare and provide landfilled fly ash will help ensure the material will continue to be available to contractors.
Teams at Plant Branch are expected to harvest and prepare 600,000 tons of landfilled fly ash annually over the next 15 years. According to McNally, the ash from this plant will be used in concrete that will be used to repair and construct bridges, roads, and buildings in Georgia and throughout the southeastern United States.
This article is published by Civil Engineering Online.