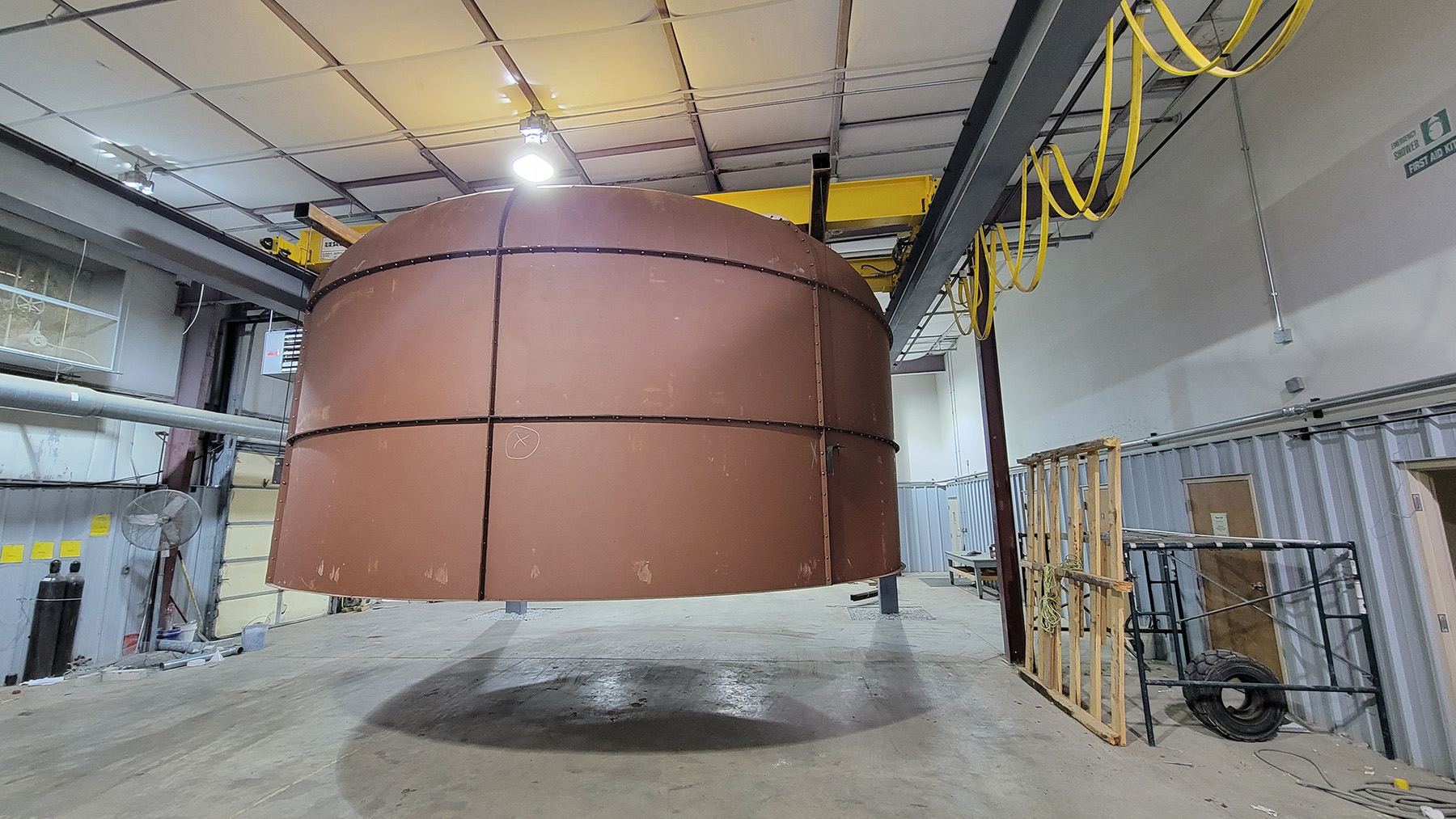
By Catherine A. Cardno, Ph.D.
The largest tornado simulator in the U.S. capable of simultaneously producing swirling and translating winds — that is, winds that swirl upward while moving along the horizontal plane — has opened in the Wind Hazard Mitigation Laboratory at the Missouri University of Science and Technology in Rolla. The first tests in the tornado simulator took place this fall.
The simulator will evaluate tornado-structure interactions to help researchers better understand how structures fail during tornadoes, which is a step in the process of improving tornado-resistant building codes, according to Guirong (Grace) Yan, Ph.D., M.ASCE, an associate professor in the civil, architectural, and environmental engineering department at Missouri S&T. Yan is also the director of WHAM and the university’s Center for Hazard Mitigation and Community Resilience.
The simulator is composed of an 84 in. diameter commercial fan that can produce a 139,000 cu ft/minute uplift wind flow rate. This fan is encased in a steel, bell-shaped structure measuring 17 ft in height with an exterior diameter of 20.2 ft. The simulator is hung from a steel bridge crane system that allows it to move 45 ft along a track at up to 8.2 ft/second as the fan is being operated, thus creating a swirling wind flow that translates.
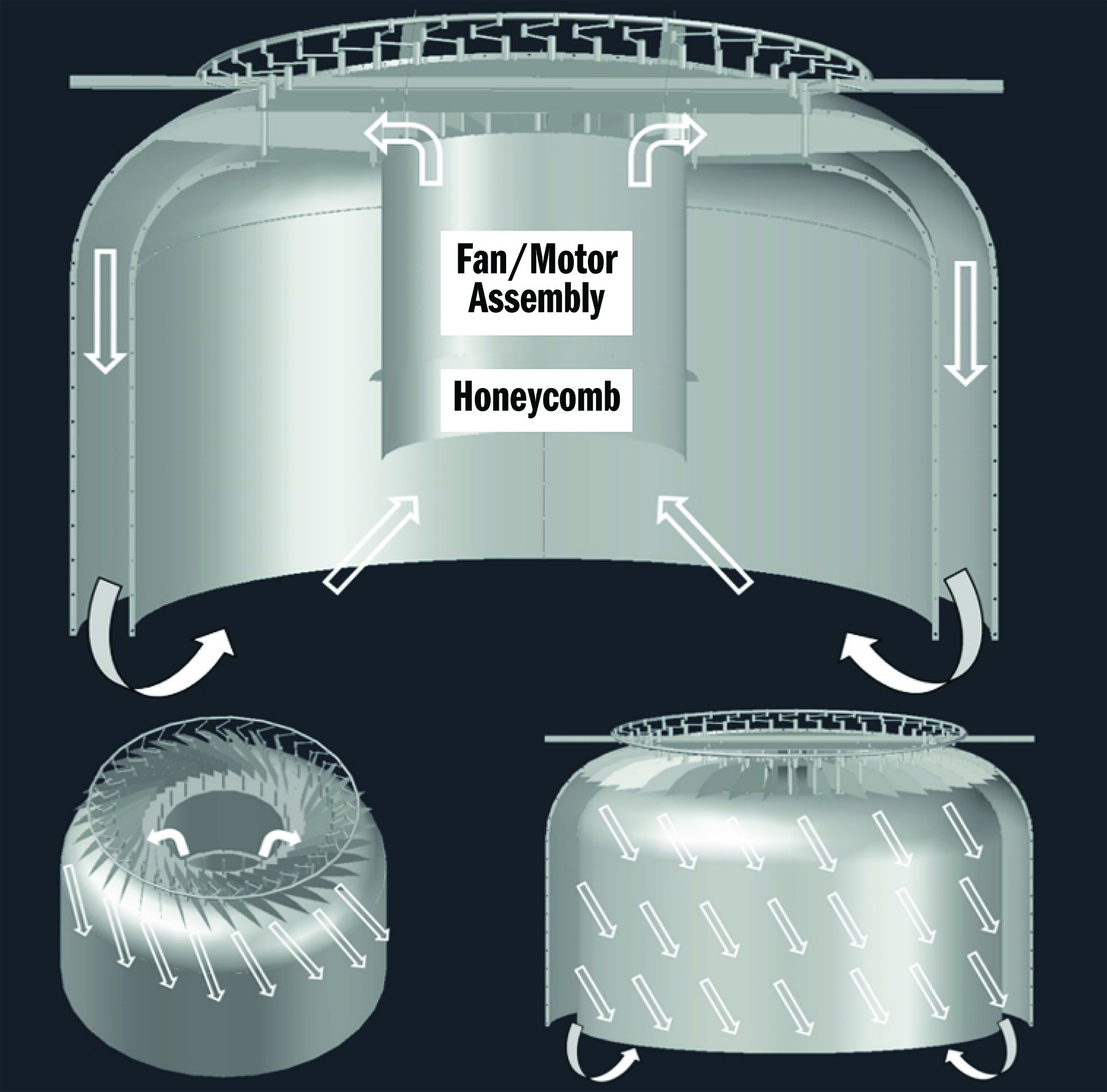
The simulator can reach uplift wind speeds of 20 m/second, which, when scaled, equates to a tornado rated a 4 on the Enhanced Fujita Scale, according to Yan. (EF-4 tornadoes can reach between 166 mph and 200 mph.)
The tornado simulator works by generating a vortex within its central chamber. With its 18.2 ft interior diameter, it can test large-scale models. This type of testing is differentiated from small-scale simulators, which can measure about 3 ft across, and full-scale testing, which would occur in real-world tornadoes, according to Ryan Norbo Honerkamp, Ph.D., EIT, A.M.ASCE, a structural engineer at KPFF Consulting Engineers in St. Louis. Honerkamp was the primary manager of WHAM prior to completing his doctoral work at the university.
As the central fan of the simulator spins, it creates an upward flow of air through two nested shells. The air passes through a central top hole in the inner shell, where it moves through turning vanes located between the inner and outer shells and is then directed down and into a gap between the shells. The angle of these vanes induces radial and tangential velocities in the air, Honerkamp explains. When it gets to the bottom of the gap between the shells, the swirling air is pulled toward the fan, inducing uplift. The central fan then recirculates the air through the simulator.
“As (the air) circulates, it generates a vortex right underneath the central fan, and this vortex extends from the ground plane up to the inlet for the fan,” Honerkamp explains. The structures and models, custom built for each specific test, are placed along a fabricated ground plane. Different topography models can be added to the ground plane to consider the influence of topography on wind effects, and the ground plane can be raised or lowered to create different heights.
The structures that are being assessed in the simulator are scaled-down models on a fixed base, with all the necessary sensors and pressure tap tubes built into that base, according to Honerkamp. “You don’t want wires or anything coming across your testing field, so you’ll have them come in from the bottom,” he says.
Because the air is recirculated, if a model is tested to failure and debris forms, it will remain within the simulator’s chamber.
The simulator’s dome shape is designed to reduce energy loss as the system operates while having the capability of changing the air-flow directions, according to Yan. The curved turning vanes are also designed to decrease the turbulence generated in the duct. “These unique features enable us to generate stable wind flow rotating around large-scale test models,” she explains.
Researchers, practitioners, and other stakeholders will be able to conduct tests using the simulator. Funding was provided by the university’s College of Engineering and Computing and the office of the vice chancellor for research and innovation as well as from the Sinquefield family in Missouri.
The simulator includes an unusual computer modeling component, according to Jeanne Cairns Sinquefield, Ph.D., who was a supercomputer software developer before her retirement. (She and her husband, Rex, are philanthropists.) Sinquefield and Steven Goldstein, an inventor based in Los Angeles, are currently designing an inexpensive, domed movable tornado shelter that fits five people and weighs 2,000 lb after being filled with water.
Prior to the fabrication of the S&T tornado simulator, Sinquefield had traveled to Texas Tech University to test her shelter’s design in its stationary large-scale simulator. The shelter has also been tested in the San Diego Wind Tunnel.
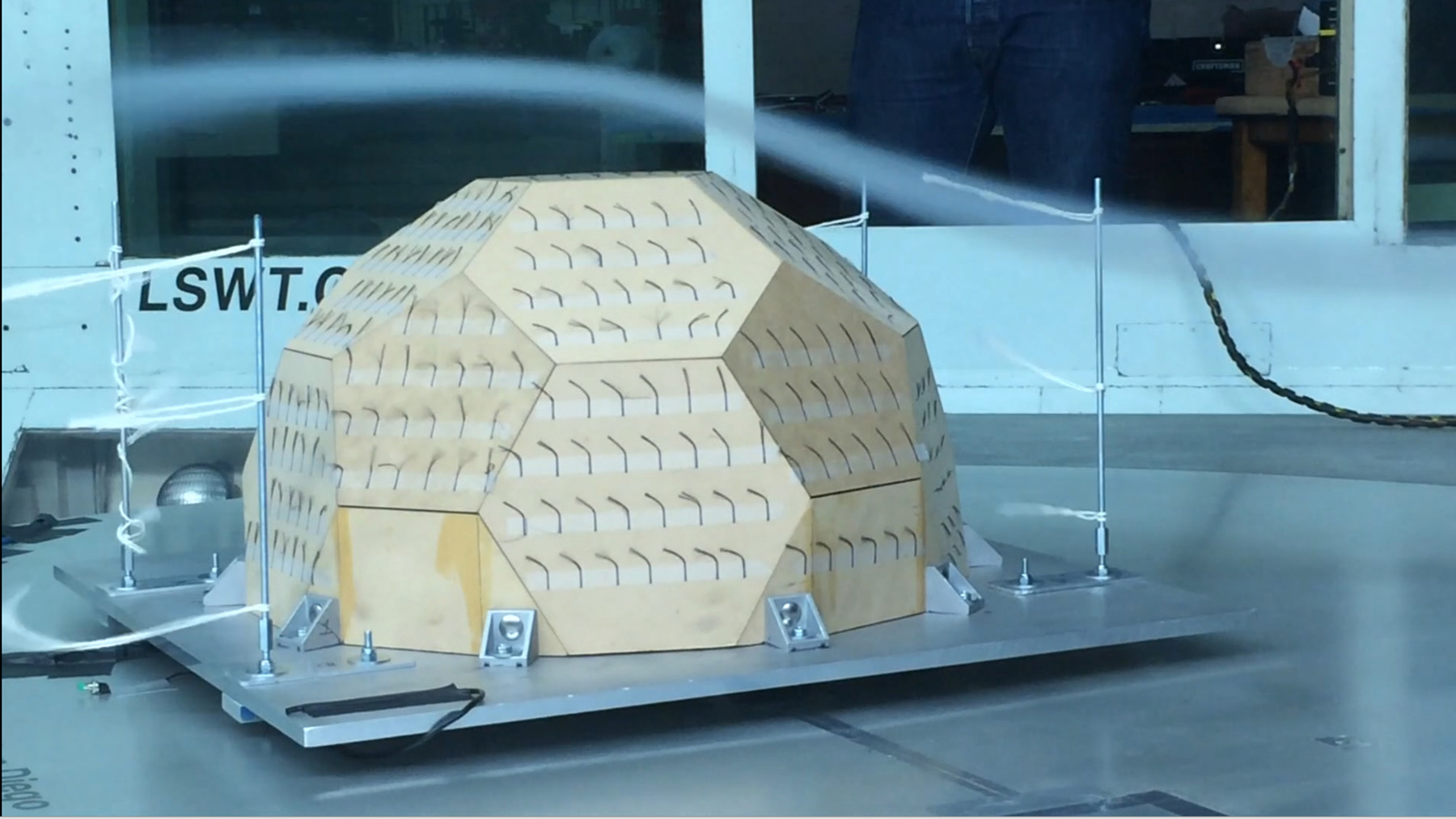
“It was very interesting how (Yan and her team) were looking at the problem in a slightly different way” than other universities, Sinquefield says. By adding the ability for the simulator to move, “the idea is to improve (testing of) what happens when a tornado actually occurs,” she says. The simulator can produce multivortex tornadoes and works in conjunction with a computational fluid dynamics model.
“These computer modeling simulations are rare for tornadoes, and very few people know how to run them,” Sinquefield says. “It’s very exciting that she’s improving that area (and how) you analyze the impact of (a tornado).”
Construction of the simulator was completed in April, and the ground plane design was completed in July.
Catherine A. Cardno, Ph.D., is the editor in chief of Civil Engineering Online.
This article first appeared in Civil Engineering Online as “Largest US translating tornado simulator opens” and in the November/December 2022 issue of Civil Engineering as “Testing Tornado Aerodynamics.”