The COPRI Governing Board initiated the Project Excellence Award in 2008 to provide a platform to highlight outstanding projects. This award is designed to acknowledge projects that exhibit exceptional design or construction in coastal, oceans, ports and harbors, or rivers related areas. The award-winning projects are recognized for their design excellence and innovation.
The Project Excellence Award acknowledges significant accomplishments in the following areas: concepts in design or construction; application of new or existing analytical techniques or technology; adaptive reuse of existing features or infrastructure; and innovative methods that minimize environmental impacts.
The 2025 COPRI Project Excellence Award was awarded to BAE Systems Jacksonville Ship Repair – Shiplift Dry-Docking Complex
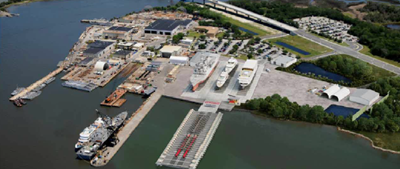
The BAE Systems Jacksonville Ship Repair project employed innovative design methods to overcome specific site challenges. The design team constructed a new bulkhead using steel sheet piling and a deadman anchor wall for stabilization and erosion protection, extending it about 150 feet east to fit the shiplift structure and dredged side slopes. Additionally, a precast stay-in-place form system was incorporated for the structural pier deck to enhance stability and construction efficiency.
To ensure project success, the design team performed extensive geotechnical investigations, including soil borings and electrical resistivity surveys, to understand the site's geological conditions and guide construction methods. A test pile program was also implemented to determine pile lengths and ensure structural integrity, utilizing the Pile Driving Analyzer (PDA) and CAPWAP analyses for capacity recommendations. The construction employed innovative techniques, including a two-step dredging process that involved a cutterhead dredge for pre-treatment and a mechanical dredge for loading limestone into scows. Additionally, the transfer bridge was built using precast-prestressed concrete and steel pipe piles, with a detailed 3D model created to address geological challenges and high dynamic loads from Self Propelled Modular Transporters (SPMTs).
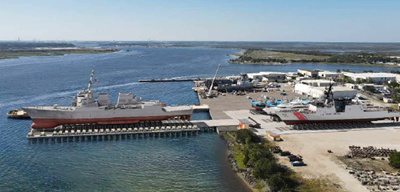
The BAEJSR project employed various techniques to reduce environmental impacts, including new bulkhead construction and enhanced waste containment measures to prevent water contamination. A SedCon system was used to decrease future maintenance dredging of the shiplift basin, while an industrial stormwater treatment system was established to manage stormwater runoff and wastewater, ensuring compliance with water quality standards before discharging into the St. Johns River. The design team also integrated the new bulkhead with existing structures, showcasing adaptive reuse of infrastructure, which required careful planning and coordination to maintain structural integrity and operational efficiency.
Throughout the construction of the BAEJSR project, comprehensive survey checks were performed to monitor tolerances for the shiplift platform and piers, ensuring adherence to design specifications and operational precision. Monitoring methods included spot checks, surveys, and flexible pile design to accommodate variable geological conditions. The project was engineered with the shiplift platform designed to support differential loads within a 3/4-inch tolerance. It also incorporated provisions for high dynamic loads and various pile types to address geological challenges. A granular load transfer platform (LTP) and a deep pile foundation with rigid inclusion elements were used to reinforce low shear strength soils and minimize foundation settlements.
The BAEJSR project resulted in several environmental enhancements, including significant increase in dry-docking maintenance space, reduction in maintenance and dredging days, and lower environmental impacts through improved waste containment and pollution reduction measures. The project's design and construction methods minimized potential water contamination and reduced the overall environmental footprint of the shipyard operations.
Image sources are BAE Systems.